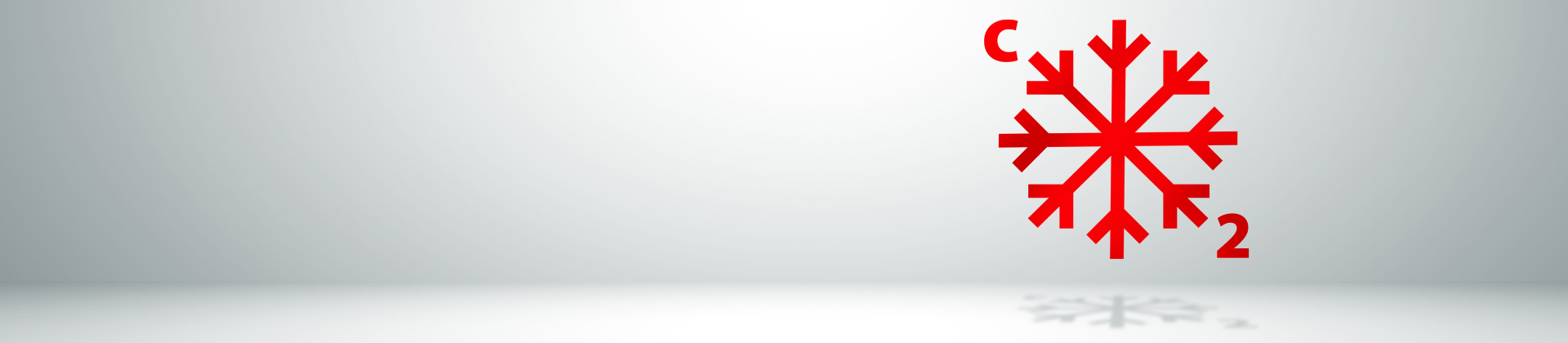
Forward Naturally
As we transition toward a more environmentally friendly future, your refrigerant choice becomes an important factor for your business and the planet. CO2 is a natural cooling agent that delivers sustainable and energy-efficient refrigeration in everything from warehouses to ice machines. Allowing businesses to move forward naturally.
General properties
CO2 has several unique thermo-physical properties making it an ideal refrigerant:
- Excellent heat transfer coefficient
- High energy content
- Relatively insensitive to pressure losses
- Very low viscosity of the liquid phase
In practical applications, CO2 systems deliver a very high-performance output. The main reasons are:
- Superior heat exchange.
- Smaller piping sizes
- Low pumping power as secondary fluid.
- Superior heat recovery
For all refrigerants, there is a decline in system efficiency with increasing condensing temperatures. High condensing temperatures are often seen as limiting factor for usage of CO2. However, the inherent thermo-physical properties of CO2 and the use of the expansion energy with ejectors can help to compensate for and offset this factor.
In addition, CO2 refrigeration systems possess heat recovery options that can help further future-proof your business. CO2 and its high energy content, which continues to scale at greater temperatures, can be reclaimed, increasing overall system efficiency.
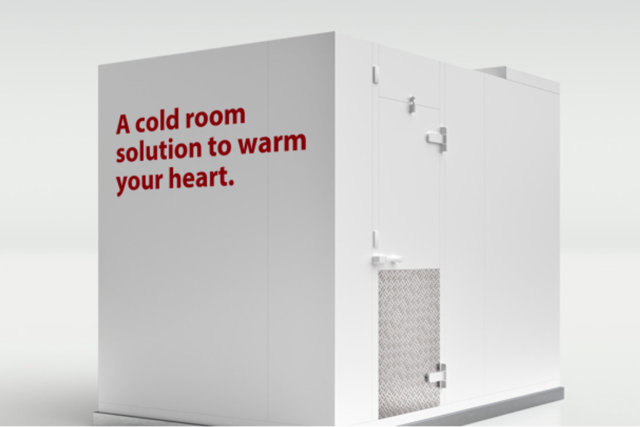
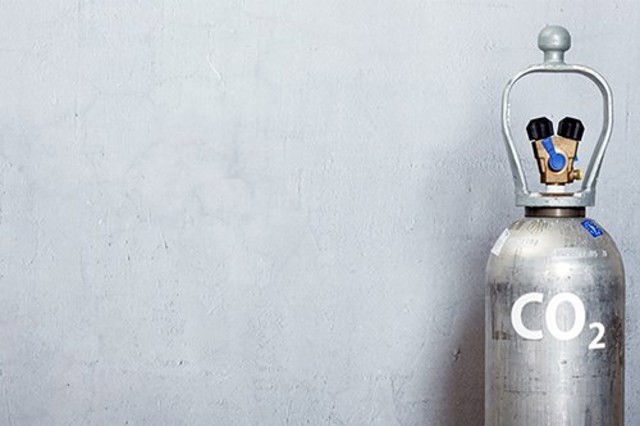
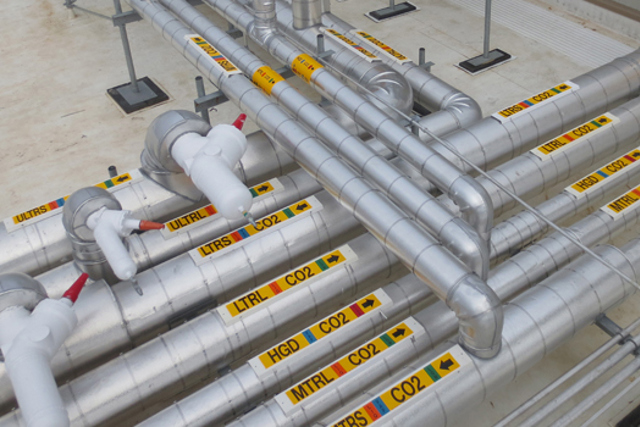

Mobile training unit for CO₂ applications
Danfoss presents the mobile training unit equipped with CO2 solutions and interactive learning modules for transport across the globe to support our worldwide community to address growing CO2 concerns.

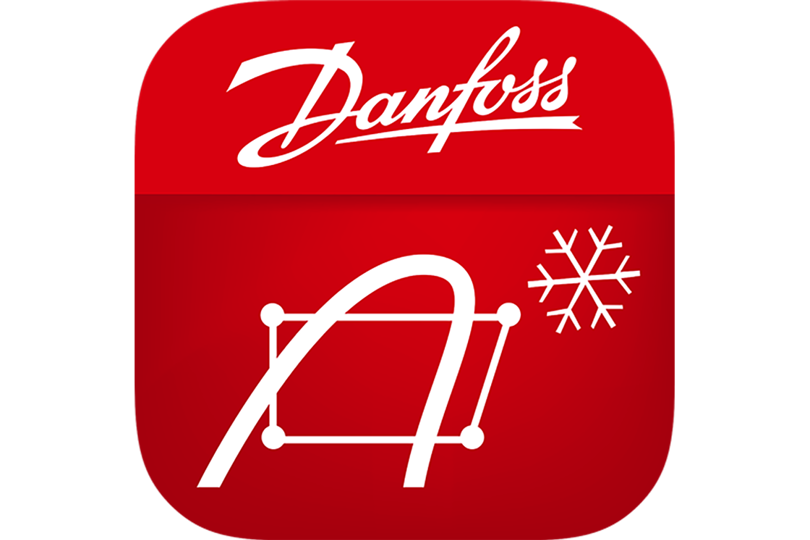
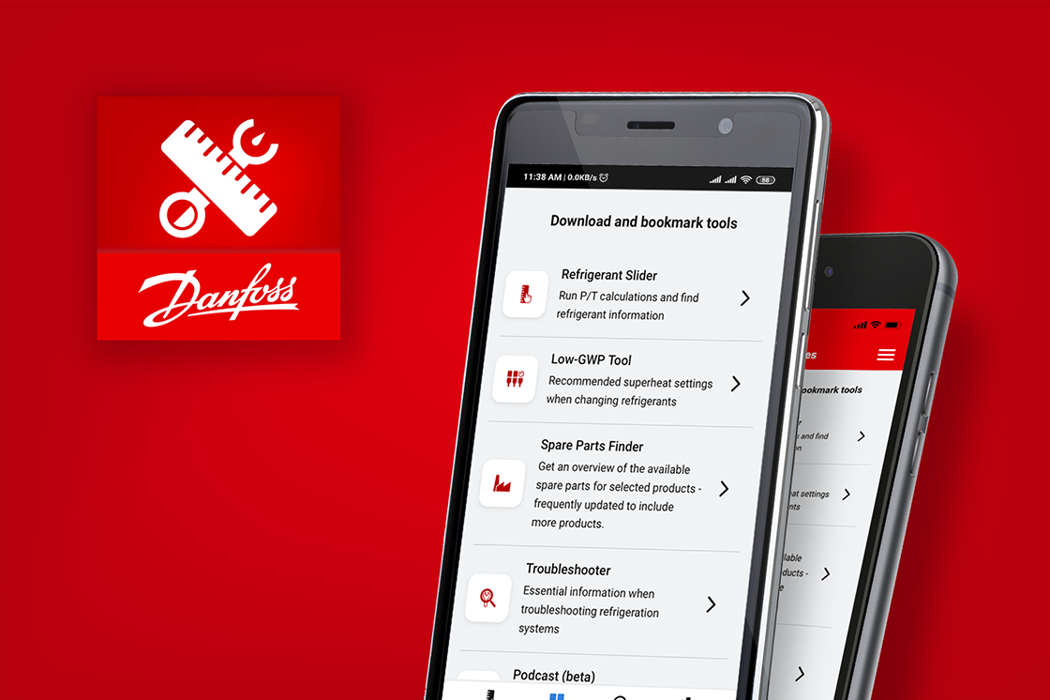