Motion control is traditionally synonymous with exact position, velocity, and acceleration control. Typically, such applications require complex servo solutions or an AC drive plus an additional motion control assembly and an encoder. With the Integrated Motion Controller (IMC) function, Danfoss offers an attractive alternative to servo motion control. Directly integrated into the VLT® AutomationDrive series, IMC very easily performs positioning and synchronization tasks with and without encoders. At the Bühler Group wafer machine factory in Leobendorf, Lower Austria, the technicians already appreciate these advantages - in particular, the resulting motor independence.
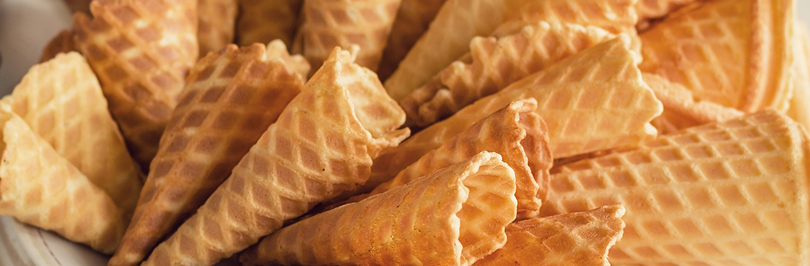
Discover how Bühler Group saved 30% in construction costs thanks to Integrated Motion Controller
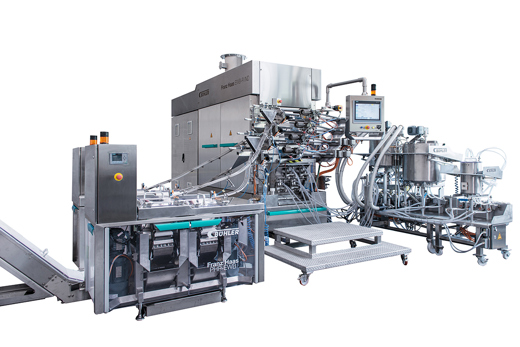
The world-renowned, domestic machine builder of production systems for wafers, biscuits and confectionery had already used VLT® drives from Danfoss under its former company name FHW Franz Haas Waffelmaschinen for many years - and remains true to this tradition even under the flag of the Bühler Group. Due to the increasing need to synchronize and position, the machine drives have recently been gradually converted to servo technology.
When Danfoss launched the Integrated Motion Control (IMC) functionality in 2017, Haas - as it was known at that time - asked whether the new control technology would also be a practical alternative to servo controls for its machines. Advantages were particularly expected from the associated free choice of motor, the technology independence and the simple system optimization through automatic motor adaptation
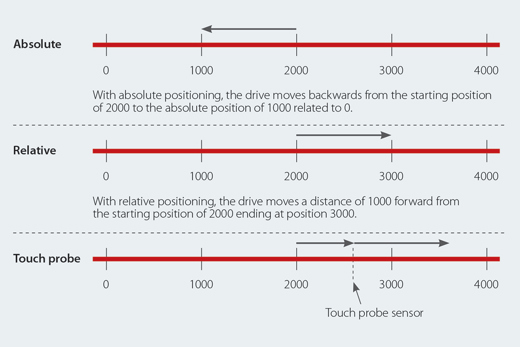
IMC offers three types of positioning
The IMC function can be used universally, since it can position absolutely, relatively and with sensor. In absolute position, the position reference refer to a defined machine zero point. This is determined at the start of the machine by the so-called homing run. If an optional feedback system with absolute position is used, this is not necessary because the zero point is set by the encoder. A typical application for this in Leobendorf is “downstream” of the cone oven with an absolute positioning of linear axes. The task here is to place paper in front of the continuously moving candy cones in order to be able to slide them into each other in the next step. The motors used are PM motors that are operated in open loop. The advantage of IMC: The rotary encoder can be eliminated, thus eliminating the costs for the encoder as well as for cabling, evaluation and work time for installation and commissioning. The use of the VLT® AutomationDrive (with IMC) itself also brings savings, because the purchase and installation costs of standard drives are significantly lower compared to a corresponding servo system.
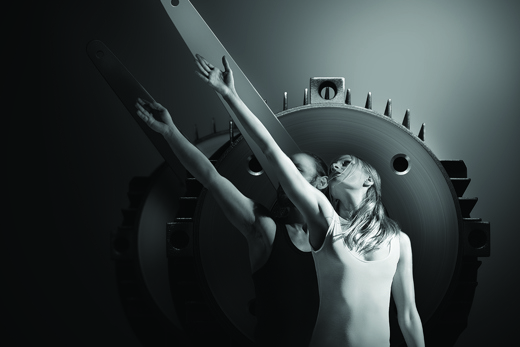
Synchronization made easy
Synchronization means creating an angle-synchronous synchronization of two or more axes. The gear ratio of the two axes to each other can be continuously adjusted. The reference signal for position and speed is either picked up by an external encoder, generated by a PLC as a pulse signal or specified via a virtual master signal. This virtual master signal is a pulse signal from which the direction of rotation, speed and position can be derived.
The reference for the master drive is either carried out in the traditional way via an analog signal or via a setpoint on the fieldbus. This master drive then converts the signal into a virtual master signal, which serves as a reference value for the follower drives as well as for the master itself.
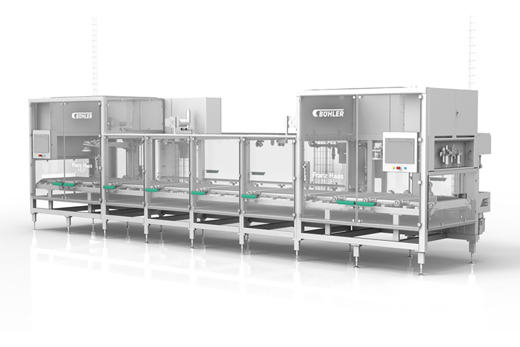
The Leobendorf wafer machine specialists use synchronization with a master signal, for example in the follower drives of the cone oven. In the subsequent processes, up to eight axes each move at an angle synchronous to one another. A pulse signal from the PLC is used as the master signal. Before starting the drives, all are moved to a reference position (homing). The PM motors used in open loop with gearbox achieve angle-synchronous synchronization despite different gearboxes and different motors, via exact adjustment of the gear ratio. This removes the need for the complete encoder system for the eight axes and the servo controllers. In addition, the ovens can be started up much faster and the engineering has been simplified
High reliability at lower cost
In addition to simple parameterization, IMC offers high reliability thanks to proven AC drive technology and easy troubleshooting in the event of a fault. Recommissioning can usually be done by the operator and requires no specially trained personnel. The Integrated Motion Controller reduces costs for OEMs and users through simple engineering with fewer components as well as reduced downtime.
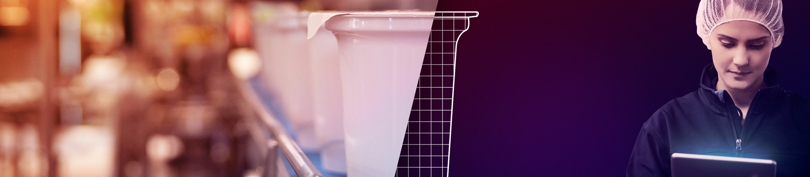
The best food plants are powered by Danfoss Drives
Related case stories
-
if (isSmallPicture) {
; } else if (isBigColumns) { } else { }iC7-Automation drives König’s automatic crate sorter at DGLKönig and Danfoss smoothly integrated iC7-Automation into DGL sorting machines for returned bottle crates. The highly efficient system sorts 3,600 crates hourly.
-
if (isSmallPicture) {
; } else if (isBigColumns) { } else { }Future-proof energy efficiency at AB InBev Hoegaarden® breweryChallenged by aging machinery and no time for downtime, AB InBev Hoegaarden® chose Danfoss iC7-Automation and VLT® OneGearDrive®—for high energy efficiency.
-
if (isSmallPicture) {
; } else if (isBigColumns) { } else { }Effortless control: Kohberg Bakery thrives with iC7-AutomationDENMARK: Kohberg Bakery upgraded its conveyor line for bread rolls to implement full control with built-in sensors and easy scalability for future adaptability.
-
if (isSmallPicture) {
; } else if (isBigColumns) { } else { }Refrigeration systems preserve apple quality using VSDs with integrated condition monitoring and DrivePro Remote Monitoring serviceITALY: At Rivoira Group, VLT® drives with built-in condition-based monitoring help preserve fruit perfectly by ensuring utterly reliable refrigeration.
-
if (isSmallPicture) {
; } else if (isBigColumns) { } else { }First mover controls beverage conveyor systems with iC7-AutomationBELGIUM: Legendre Conveyors has built up great trust in Danfoss over many years of conveyor design using VLT® drives. Now they progress to the new iC7 series.
-
if (isSmallPicture) {
; } else if (isBigColumns) { } else { }Carlsberg brewery drives down energy consumptionPOLAND: For more than a decade, Danfoss drives have reduced the power consumption at Carlsberg’s Okocim Brewery. The brewery uses less water and has lowered its emissions, too.
Related applications
-
if (isSmallPicture) {
; } else if (isBigColumns) { } else { }Drives and gear motors for conveyors in food and beverageEnsure maximum uptime and lowest possible cost of ownership with hygienic, variable-speed conveyor control. IPA-certified.
-
if (isSmallPicture) {
; } else if (isBigColumns) { } else { }Drives for compressors in food and beverageCompressor speed control provides constant pressure regulation as well as reducing your energy consumption, especially for part-load operation.
-
if (isSmallPicture) {
; } else if (isBigColumns) { } else { }Drives for fans in food and beverage applicationsVariable speed fan control reduces costs by trimming energy consumption, and improves comfort levels by avoiding noise-generating frequencies.
-
if (isSmallPicture) {
; } else if (isBigColumns) { } else { }Drives for positioning and synchronization in food and beverageReduce cost, complexity, and programming time in servo applications by using an AC drive for high-precision positioning and synchronization.
-
if (isSmallPicture) {
; } else if (isBigColumns) { } else { }Drives for pumps in food and beverage applicationsControl of pump speed can reduce energy consumption significantly, extend pump life, and dramatically reduce water consumption in your operations.