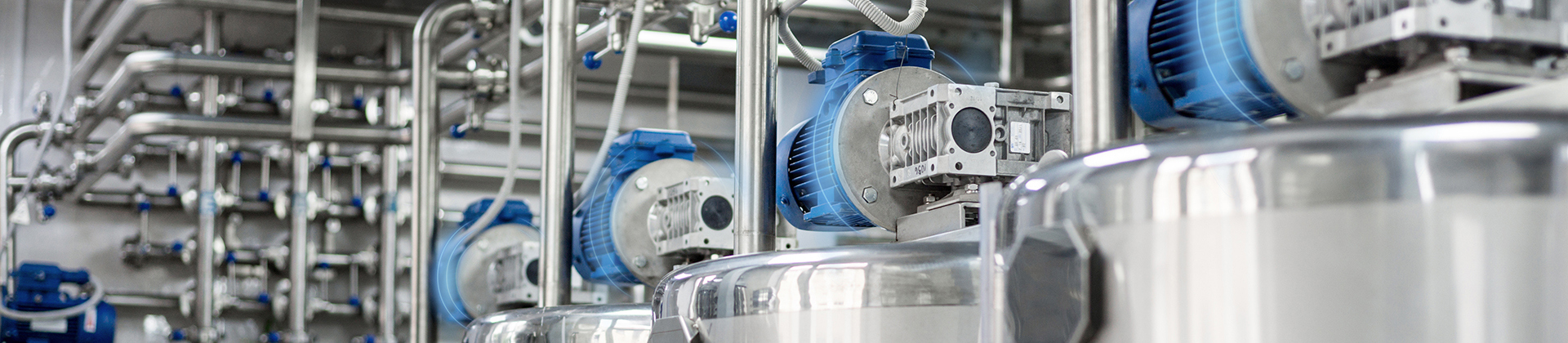
Integrated CBM in one comprehensive package
Condition-based monitoring (CBM) integrated into premium Danfoss drives has revolutionized the way these drives monitor electric motors for faults and potential failures. With breakthrough technology implemented at the drive level, CBM offers advanced features such as motor stator winding monitoring, vibration monitoring, wear-out monitoring of bearings, load envelope (torque) monitoring, and cavitation detection, all in one comprehensive package.
Improving performance via a motor monitoring system
The benefits of CBM for motors are significant. Monitoring performance using CBM provides a simple and cost-effective way to obtain machine data for smart maintenance decisions. With CBM, there is no need for specialized expertise, as existing user interfaces are supported. CBM can be used in a wide range of applications and motor ratings. It’s also reassuring to know that CBM operates independently of the cloud, using edge computing in the drive, ensuring data privacy and security.
Make the shift from scheduled maintenance to predictive maintenance
Enable your maintenance decisions based on application data. By enabling early warnings and notifications, CBM increases production uptime by allowing operators to take action on alerts, to perform necessary remedial actions before an unscheduled breakdown occurs. It helps identify damaged motor windings, increasing vibration levels, squealing bearings, and unusual torque values. CBM also allows for the transition from scheduled maintenance to predictive maintenance, increasing the efficiency and effectiveness of maintenance strategies. It is a cost-effective solution compared to external complex systems offered by third parties.
Example: The ability to prevent unexpected breakdowns is especially significant in an aseptic manufacturing environment. One pharmaceutical company conducted tests to prove that intelligent Danfoss drives with integrated condition-based monitoring provide reliable ventilation in an aseptic environment. The drives help to prevent downtime with real-time system monitoring and customizable instant alarms, which provide an early warning enabling operators to take preventive action.
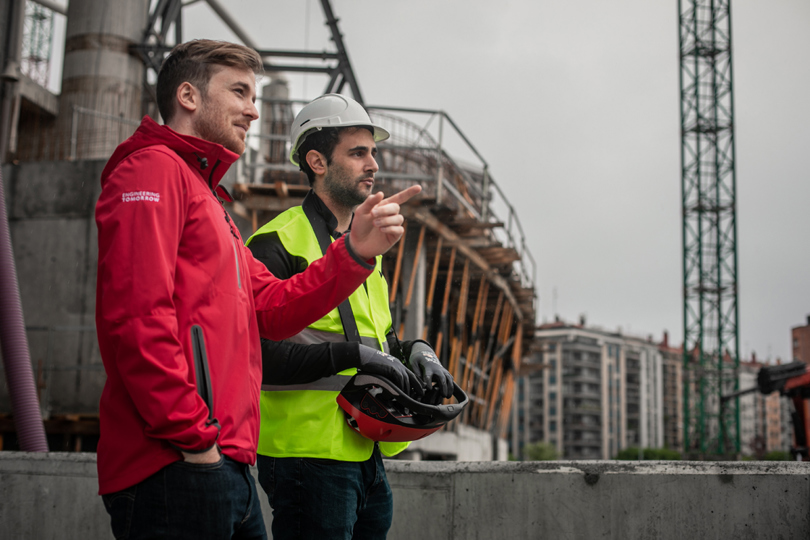
Motor condition monitoring for remote locations
CBM is especially suitable for remote locations or devices that are difficult to access. With permanent monitoring, potential faults can be detected and addressed before they result in motor failure and production downtime. By taking maintenance strategies to the next level with CBM, industries can increase their application uptime, reduce maintenance costs, and enhance overall operational efficiency.
Explore more opportunities with condition-based monitoring(CBM)
Highlighted products
Danfoss products using condition-based monitoring
-
if (isSmallPicture) {
; } else if (isBigColumns) { } else { }VLT® AQUA Drive FC 202VLT® AQUA Drive FC 202 controls all types of pumps and comes equipped with a cascade controller.
-
if (isSmallPicture) {
; } else if (isBigColumns) { } else { }VLT® HVAC Drive FC 102This tough and savvy FC102 drive enhances pump and fan applications in building management systems, and runs outdoors in most climates.
-
if (isSmallPicture) {
; } else if (isBigColumns) { } else { }VLT® Refrigeration Drive FC 103FC 103 is dedicated to controlling compressors, pumps and fans for significant energy savings in refrigeration plants.
-
if (isSmallPicture) {
; } else if (isBigColumns) { } else { }VLT® AutomationDrive FC 301 / FC 302The VLT® AutomationDrive FC 301 / FC 302 is designed for variable speed control of all asynchronous motors and permanent magnet motors. It comes in a standard version (FC 301) and an advanced high dynamic version (FC 302) with additional functionalities.
-
if (isSmallPicture) {
; } else if (isBigColumns) { } else { }VACON® NXP Air CooledDesigned for a broad range of demanding applications, focusing on higher power sizes and system drives.
-
if (isSmallPicture) {
; } else if (isBigColumns) { } else { }VACON® 100 XA drive for indoor and outdoor applications that withstands high pressure and vibration levels, water, heat and dirt.
-
if (isSmallPicture) {
; } else if (isBigColumns) { } else { }VACON® 100 INDUSTRIALDrive modules and enclosed drives that are easily integrated into all major control systems.
-
if (isSmallPicture) {
; } else if (isBigColumns) { } else { }VACON® 100 FLOWDedicated functionality that improves flow control and saves energy in industrial pump and fan applications.
-
if (isSmallPicture) {
; } else if (isBigColumns) { } else { }VACON® NXP System DriveConfigured and assembled to meet your needs whether you need to control one or several motors.
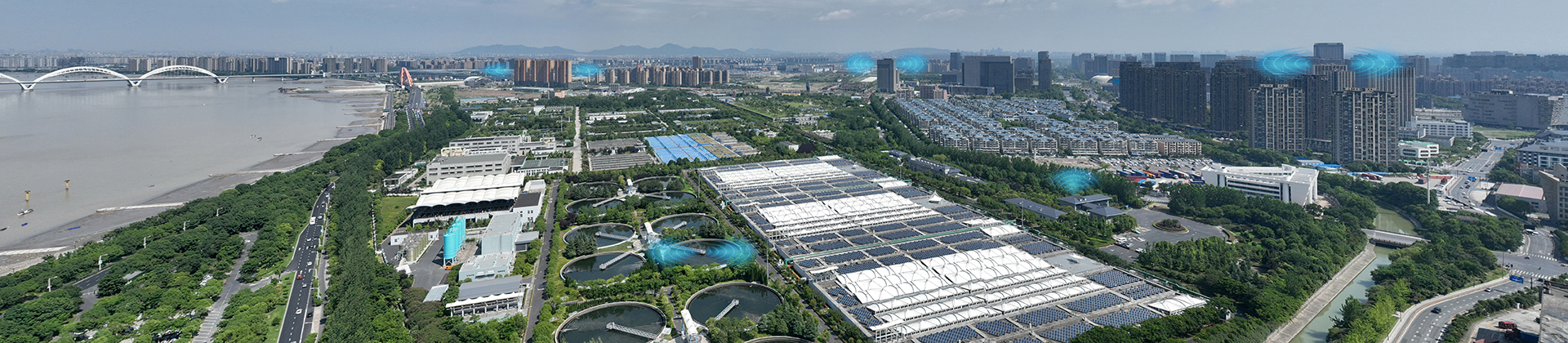
Danfoss first innovations
CBM has emerged from a history of Danfoss firsts in innovation. Danfoss drives differentiate from others in the market with intelligent functions embedded in the drive, to reduce the external components required.
Case stories
-
if (isSmallPicture) {
; } else if (isBigColumns) { } else { }How did this smart factory reach carbon-neutral?POLAND: The new Danfoss production hall in Grodzisk Mazowiecki has reached carbon-neutrality, thanks to full electrification, energy-saving solutions such as Danfoss drives, and energy from renewable sources.
-
if (isSmallPicture) {
; } else if (isBigColumns) { } else { }Refrigeration systems preserve apple quality using VSDs with integrated condition monitoring and DrivePro Remote Monitoring serviceITALY: At Rivoira Group, VLT® drives with built-in condition-based monitoring help preserve fruit perfectly by ensuring utterly reliable refrigeration.
-
if (isSmallPicture) {
; } else if (isBigColumns) { } else { }How does Beat the Storm deliver more fun for less CO2?DENMARK: Universe Science Park saves on both power bill and emissions for its wind tunnel attraction “Beat the Storm”, with the intelligent VLT® HVAC drive.
-
if (isSmallPicture) {
; } else if (isBigColumns) { } else { }Driving maximum uptime in aseptic pharmaceutical productionDENMARK: A leading global pharmaceutical company was determined to find an intelligent HVAC solution to prevent downtime with real-time system monitoring and customizable instant alarms. Plus, the solution needed to fit within the organization’s ambitious digitalization strategy. The solution: Danfoss VLT® HVAC Drive FC 102 with integrated condition-based monitoring.
-
if (isSmallPicture) {
; } else if (isBigColumns) { } else { }Brewing up real change at HEINEKENNETHERLANDS: HEINEKEN understands that to meet demand, its production line must always be up to the task – with all assets expected to deliver a consistently reliable and excellent performance. At Den Bosch brewery, the tough working environment posed several challenges. The solution was an upgrade using drives with integrated condition-based monitoring.