With the European beer market expected to grow 15.2% by 2025, HEINEKEN understands that to meet demand, its production line must always be up to the task – with all assets expected to deliver a consistently reliable and excellent performance. At Den Bosch brewery, the tough working environment posed several challenges: with every machine fault resulting in costly and lengthy periods of downtime due to operations taking place in wet and harsh conditions, and electrical motors being concealed and hard to reach in the event of an emergency. With this in mind, Danfoss Drives was tasked with helping HEINEKEN integrate condition-based monitoring into its procedures to
- Increase uptime
- Lower overheads
- Improve management of spare parts and stock
- Access new levels of machine data
- Boost application and system performance
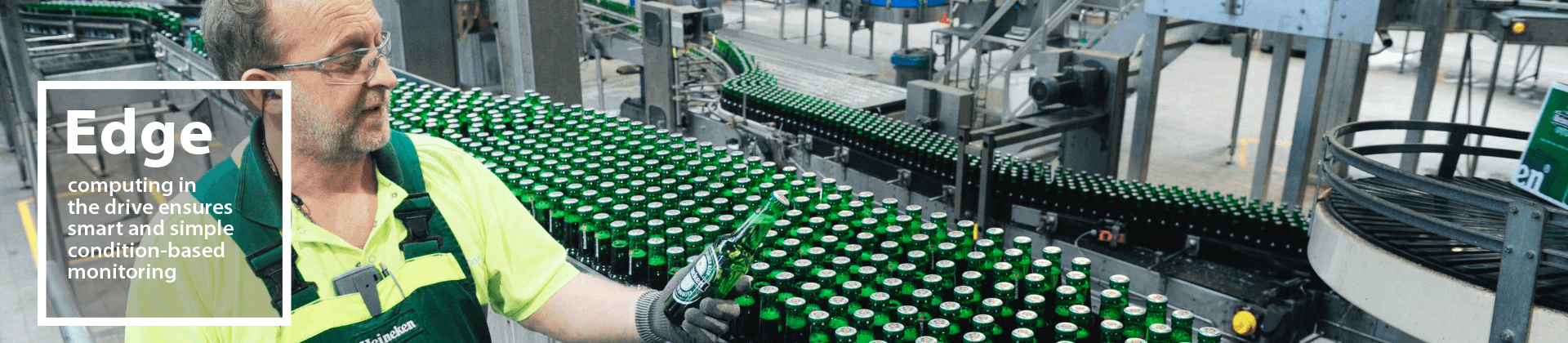
Helping Heineken digitalize operations
When brewer Heineken Netherlands Supply made the decision to upgrade the maintenance system at its Den Bosch brewery, it turned to Danfoss Drives. Download our case story and read up on the solutions we chose for our client, what processes we went through to optimize the brewery’s applications and production line, and how, in the end, Heineken was able to unleash the intelligence from within its systems
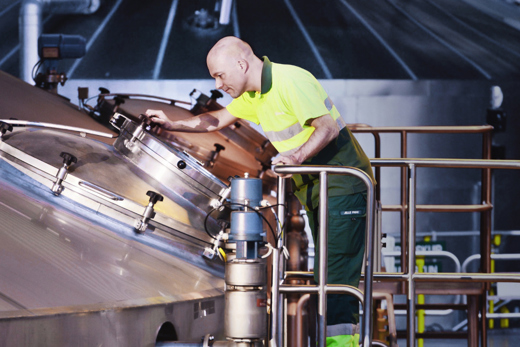
In August 2019 Danfoss Drives proposed HEINEKEN install VLT® drives with embedded intelligence, connectivity, and sensor capabilities. Condition-based monitoring signals were then integrated into the brewery’s maintenance system via edge computing. The brewery also received 4-20 mA vibration sensors from Hansford Sensors, and Danfoss provided additional support with project scoping, commissioning, and training, as well as holding workshops to determine the best solution for HEINEKEN’s needs. The VLT® drives also support pre-existing communication interfaces and software such as fieldbus, local control panels, and VLT® Motion Control Tool MCT 10, meaning HEINEKEN did not have to invest in a new parallel system as part of the upgrade.
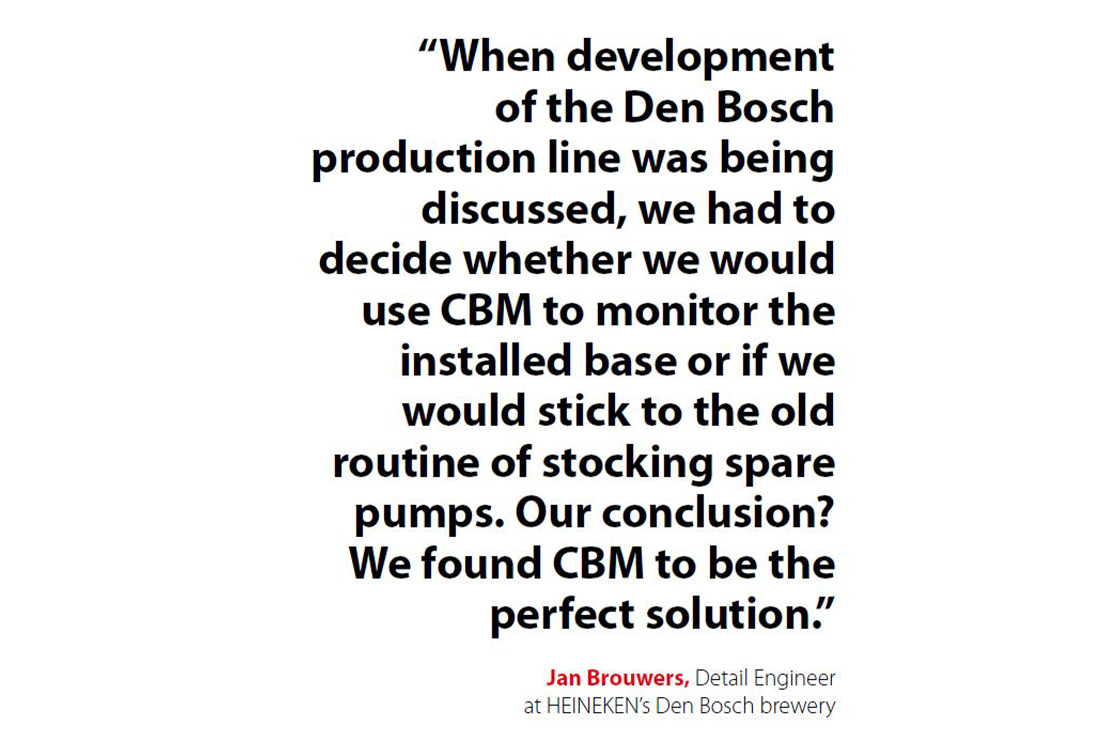
The VLT® Motion Control Tool MCT 10 plug-in proved to be a real game changer, enabling seamless commissioning with consistent parameter settings. And so, with the power to gather more critical application data in real time than ever before – and thanks to the efforts of Danfoss Drives – HEINEKEN was able to optimize its Den Bosch production line while solving all its pain points and building a total value proposition.
In addition, Danfoss Drives’ digital expertise enabled HEINEKEN to go and retrofit the rest of its drives in the rest of its facilities with condition-based monitoring functionality.
In conclusion, the Den Bosch upgrade shows that condition-based monitoring is no longer a premium product meant for a few critical assets, but an affordable solution available for all – thanks to Danfoss Drives’ innovative and forward-thinking approach.
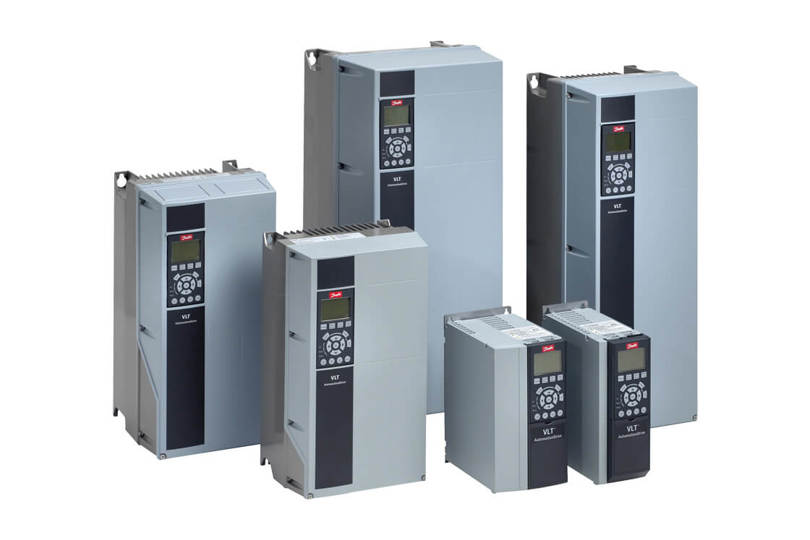
Discover VLT® AutomationDrive FC 302 with condition-based monitoring
More case stories
-
if (isSmallPicture) {
; } else if (isBigColumns) { } else { }iC7-Automation drives König’s automatic crate sorter at DGLKönig and Danfoss smoothly integrated iC7-Automation into DGL sorting machines for returned bottle crates. The highly efficient system sorts 3,600 crates hourly.
-
if (isSmallPicture) {
; } else if (isBigColumns) { } else { }Future-proof energy efficiency at AB InBev Hoegaarden® breweryChallenged by aging machinery and no time for downtime, AB InBev Hoegaarden® chose Danfoss iC7-Automation and VLT® OneGearDrive®—for high energy efficiency.
-
if (isSmallPicture) {
; } else if (isBigColumns) { } else { }Effortless control: Kohberg Bakery thrives with iC7-AutomationDENMARK: Kohberg Bakery upgraded its conveyor line for bread rolls to implement full control with built-in sensors and easy scalability for future adaptability.
-
if (isSmallPicture) {
; } else if (isBigColumns) { } else { }First mover controls beverage conveyor systems with iC7-AutomationBELGIUM: Legendre Conveyors has built up great trust in Danfoss over many years of conveyor design using VLT® drives. Now they progress to the new iC7 series.
-
if (isSmallPicture) {
; } else if (isBigColumns) { } else { }Maximizing uptime for high-volume bottle fillingNORTH MACEDONIA: To meet new standards for uptime, flexibility, and energy efficiency, Pivara Skopje’s RGB line needed modernization. The ideal VSDs? VLT® FlexConcept®.
-
if (isSmallPicture) {
; } else if (isBigColumns) { } else { }Brewing up real change at HEINEKENNETHERLANDS: HEINEKEN understands that to meet demand, its production line must always be up to the task – with all assets expected to deliver a consistently reliable and excellent performance. At Den Bosch brewery, the tough working environment posed several challenges. The solution was an upgrade using drives with integrated condition-based monitoring.
Meet us at drinktec 2025
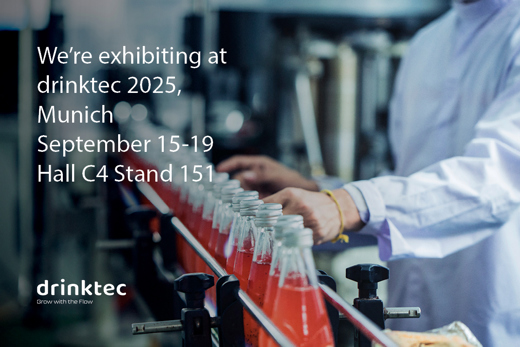
Shaping the future of beverage production – Together at drinktec 2025
After three years, the beverage industry is gathering again at drinktec in Munich. Visit us there and talk to our Danfoss experts about our latest solutions for increased productivity and sustainability in your plant. We look forward to seeing you at our booth C4.151 from September 15 to 19!