The beverage industry keeps our thirst quenched around the clock—but not without effort. Pivara Skopje is the Balkan region’s leading producer of Coca-Cola beverages, the world’s most famous soft drink portfolio. The Macedonian facility is owned by Heineken and Coca-Cola Hellenic Group, which are leading the industry with consistent investments in energy-efficiency projects across their production facilities.
To meet the new standards for uptime, flexibility, and energy efficiency—and to keep up with the consistent demand for Coca-Cola’s broad range of beverages—Pivara Skopje’s returnable glass bottle (RGB) production line needed modernization. The conveyor belt system was operating on outdated gearboxes and a nearly obsolete PLC solution—with inefficient bottle-filling that led to downtime and high maintenance costs.
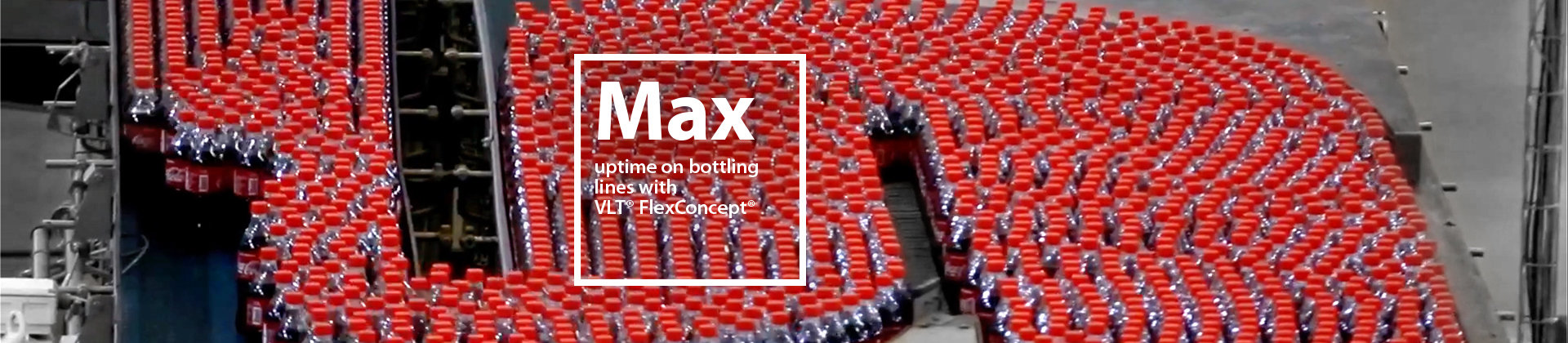
Discover more
Discover how Danfoss VLT® FlexConcept® - a seamlessly integrated, modern, and future-proof solution - helped the production line reliably increase the production speed for accurate bottle filling and accomodate flexibility with ease - all while improving energy efficiency on the bottling line.
The challenge
Pivara Skopje's conveyor line relied on motors started directly-on-line (DOL). That meant the conveyor belt speed couldn't be regulated — leading to bottles failing, filling mishaps, and, sometimes, production coming to a standstill. Combined with an outdated and nearly obsolete PLC automation system behind it, they faced expensive maintenance costs and continuously had difficulty sourcing spare parts.
Modernization was key to addressing the challenges on Pivara Skopje's conveyor line — especially when it came to increasing uptime and improving energy efficiency.
As the region's largest producer of Coca-Cola beverages, Pivara Skopje needed a future-proof solution that empowered their production line to accommodate multiple recipes, quantities, and speeds with agile precision — and support operational optimization.
"Certain bottles were very unstable and easily overturned. So, Pivara Skopje significantly slowed the line to prevent filling mistakes, but it only caused additional downtime," explained Darko Kovac, PLC & SCADA Programmer at INDAS and Nenad Mirosavljevic, Sales Engineer for Danfoss Drives.
The solution
At Pivara Skopje's Coca-Cola conveyor line, our long-standing partner INDAS implemented the innovative Danfoss VLT® FlexConcept® solution. The outdated mechanical variator gearboxes on all nine drives were replaced with Danfoss VLT® OneGearDrives® controlled by a VLT® AutomationDrive FC 302. Plus, the Danfoss drives and gear motor seamlessly integrated with the new PLC system thanks to an open system architecture compatible with solutions from any other controls vendor.
Engineered specifically to meet the demands of modern food and beverage production, the VLT® FlexConcept® is highly efficient, enables agility in production, and dramatically improves uptime.
A combination of the VLT® OneGearDrive® — delivered in a hygienic housing that complies with food safety guidelines — and the VLT® Automation Drive FC 302, the solution optimizes plant productivity while reducing energy costs thanks to simplified drive configuration and the need for fewer spare parts.
VLT® FlexConcept® - Features and benefits
The features and benefits of the VLT® FlexConcept® deliver the most energy-efficient and flexible solutions for high-volume production lines.
- Higher energy efficiency with matched design of the permanent (PM) motors and inverters
- Fewer variants simplify project planning, integration, commissioning, and maintenance
- Open system architecture means the solution is compatible with any PLC for seamless integration and simple retrofitting
- Unique hygienic design with a smooth, crevice-free surface can be cleaned quickly and easily, reducing associated costs
- Direct mounting onto the conveyor shaft is advantageous for retrofitting
The outcome
The Danfoss VLT® FlexConcept® empowers high-volume production lines to modernize their operations with ease and efficiency.
At Pivara Skopje, the implementation of the VLT® FlexConcept® has resulted in the highest level of flexibility and uptime for the production line. They gained faster and more reliable beverage production, instant energy savings, and an increased charging capacity — all while reducing downtime. Plus, with fewer drive variants, they have reduced inventory costs by 70%.
That means the Pivara Skopje production line can accommodate several recipes with different parameters while increasing energy savings, reducing inventory costs, streamlining maintenance procedures — all with a relatively short return on investment.
Products in this case story
-
if (isSmallPicture) {
; } else if (isBigColumns) { } else { }VLT® AutomationDrive FC 301 / FC 302The VLT® AutomationDrive FC 301 / FC 302 is designed for variable speed control of all asynchronous motors and permanent magnet motors. It comes in a standard version (FC 301) and an advanced high dynamic version (FC 302) with additional functionalities.
-
if (isSmallPicture) {
; } else if (isBigColumns) { } else { }VLT® OneGearDrive®A highly efficient combination of a permanent magnet motor and optimized bevel gearing.
Related applications
-
if (isSmallPicture) {
; } else if (isBigColumns) { } else { }Drives and gear motors for conveyors in food and beverageEnsure maximum uptime and lowest possible cost of ownership with hygienic, variable-speed conveyor control. IPA-certified.
Related case stories
-
if (isSmallPicture) {
; } else if (isBigColumns) { } else { }iC7-Automation drives König’s automatic crate sorter at DGLKönig and Danfoss smoothly integrated iC7-Automation into DGL sorting machines for returned bottle crates. The highly efficient system sorts 3,600 crates hourly.
-
if (isSmallPicture) {
; } else if (isBigColumns) { } else { }Future-proof energy efficiency at AB InBev Hoegaarden® breweryChallenged by aging machinery and no time for downtime, AB InBev Hoegaarden® chose Danfoss iC7-Automation and VLT® OneGearDrive®—for high energy efficiency.
-
if (isSmallPicture) {
; } else if (isBigColumns) { } else { }Effortless control: Kohberg Bakery thrives with iC7-AutomationDENMARK: Kohberg Bakery upgraded its conveyor line for bread rolls to implement full control with built-in sensors and easy scalability for future adaptability.
-
if (isSmallPicture) {
; } else if (isBigColumns) { } else { }First mover controls beverage conveyor systems with iC7-AutomationBELGIUM: Legendre Conveyors has built up great trust in Danfoss over many years of conveyor design using VLT® drives. Now they progress to the new iC7 series.
-
if (isSmallPicture) {
; } else if (isBigColumns) { } else { }Maximizing uptime for high-volume bottle fillingNORTH MACEDONIA: To meet new standards for uptime, flexibility, and energy efficiency, Pivara Skopje’s RGB line needed modernization. The ideal VSDs? VLT® FlexConcept®.
-
if (isSmallPicture) {
; } else if (isBigColumns) { } else { }Brewing up real change at HEINEKENNETHERLANDS: HEINEKEN understands that to meet demand, its production line must always be up to the task – with all assets expected to deliver a consistently reliable and excellent performance. At Den Bosch brewery, the tough working environment posed several challenges. The solution was an upgrade using drives with integrated condition-based monitoring.