SCOTLAND: In the suburbs of Edinburgh, an innovative system for the treatment of non-recyclable urban waste helps to reduce the city’s environmental footprint. In line with the zero waste objectives of the Scottish government, it contributes to eliminating landfill whilst generatiing electricity and heat. Equipped with high-efficiency VACON® NXP drives, the process generates heat enough to supply 25,000 households.
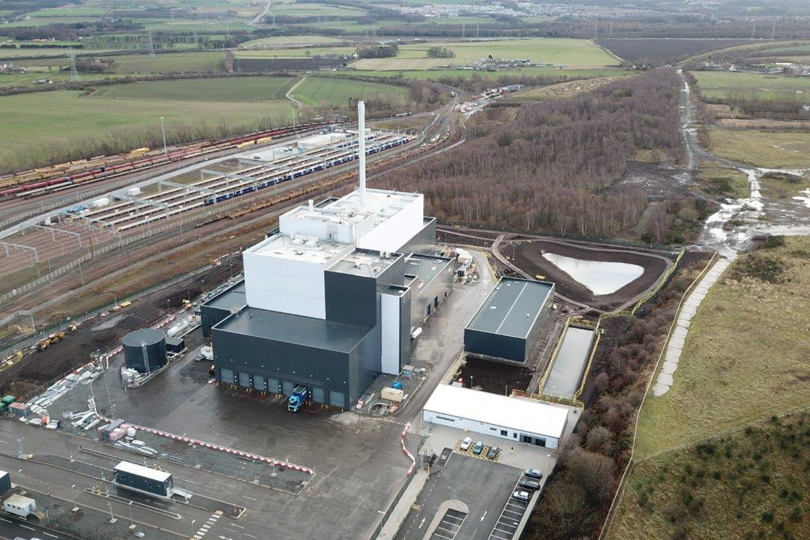
Sustainable energy from waste
Learn how Edinburgh is reducing its carbon footprint
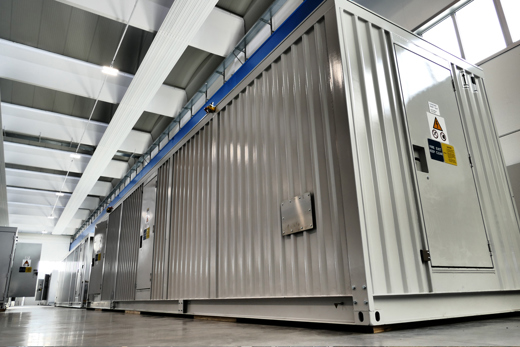
Competence that improves energy efficiency
The Millerhill Zero Waste Parc plant is an energy-for-waste (EfW) facility designed and built by Hitachi Zosen Inova (HZI) on behalf of FCC Environment, the company responsible for managing environmental services in the municipality of Edinburgh.
The EfW facility has a capacity of 155,000 tons per year of non-recyclable municipal solid waste, which after separation of metal residues, is sent for energy recovery. The sophisticated XeroSorp gas treatment process patented by HZI makes it possible to optimize plant performance and reduce the emission of residual particles into the atmosphere to a minimum.
The electrical and electromechanical systems supporting the waste treatment process ensure high energy efficiency of the 20 MW plant, and guarantee the reliability and durability which are essential for this kind of project, planned to operate continuously for decades. Casagrande Elettrocostruzioni Spa was responsible for the design, construction and commissioning of electrical panels for the Edinburgh plant.
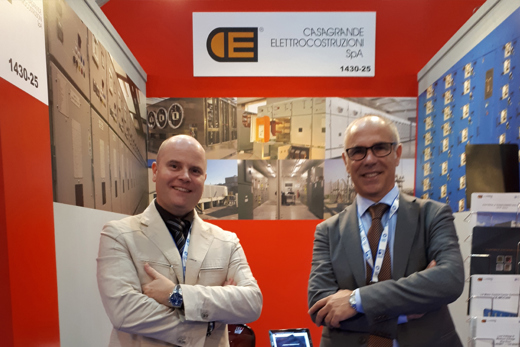
Sergio Boccagni, Project Manager at Casagrande Elettrocostruzioni:
“Together with Hitachi Zosen Inova, we defined a methodology for the design and construction of electrical Switchboards which are integrated into E-house containers at the factory. We met the demanding schedule imposed by the client, and also synchronized perfectly with site development needs, minimizing the time required for installation, commissioning and start up of electrical systems. Casagrande Elettrocostruzion assumed full technical and operational responsibility for the construction of electrical panels. Its appraoch allowed the customer to successfully start the plant on schedule and ensured excellent energy efficient performance as defined in the project.”
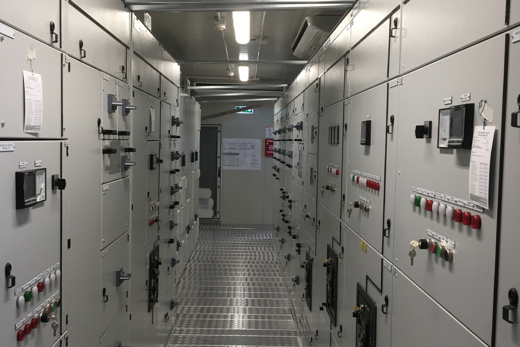
Non-stop drives
The electrical panels which supply power to the combustion process are integrated into seven containers known as E-houses. Sized 15 m x 3 m x 3.5 m, they are placed inside a metallic bearing structure inserted in a thermally insulated building located adjacent to the process plants. The seven containers contain the entire electrical infrastructure necessary for the EfW facility, from the medium-voltage connection to the distribution of all medium and low-voltage users.
The most powerful control system is linked to the emission treatment subsystem of the incinerator. Heavy loads in this system absorb about one-third of the installed electrical power.
Mr. Boccagni explains: “We chose Danfoss VACON® NXP drives because they allow us to achieve maximum performance in demanding applications. High energy efficiency must always be combined with exceptional reliability. From this point of view the Danfoss VACON® product range is a guarantee.”
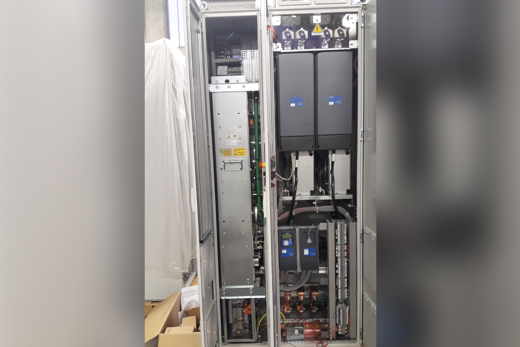
Good people make the difference
Casagrande Elettrocostruzioni collaborated with Danfoss Drives Italy to customize the high-power drves to meet the specific needs of the customer. For example, special panels for high-power drives were designed with a circuit breaker instead of a service switch with fuse, and using halogen-free cables instead of PVC cables. Mechanical details were adapted to ensure optimal installation of equipment in the container. Furthermore, the command and control parameters to be sent to supervisory systems were chosen and optimized for simple and effective integration with the SCADA plant. Many activities required specialized skills, where the ability and willingness of people made the difference.
Working in synergy
Mr. Boccagni explains: “In this project, product quality was prerequisite for selecting the most suitable supplier. Therefore, our criterion of choice was basically to rely on a company that knew how to support us from the technical point of view and with flexibility. Our need was to work in synergy to create a “tailor made” solution that would fulfil the customer’s requirements. We found the optimal partner in Danfoss Drives Italy.”
