SERBIA: With intensifying urbanization, producing concrete blocks for construction is a vigorous growth industry. VLT® AutomationDrive FC 302 with Integrated Motion Controller enables Metalika to build concrete handling machines that operate flexibly and fast, with high precision.
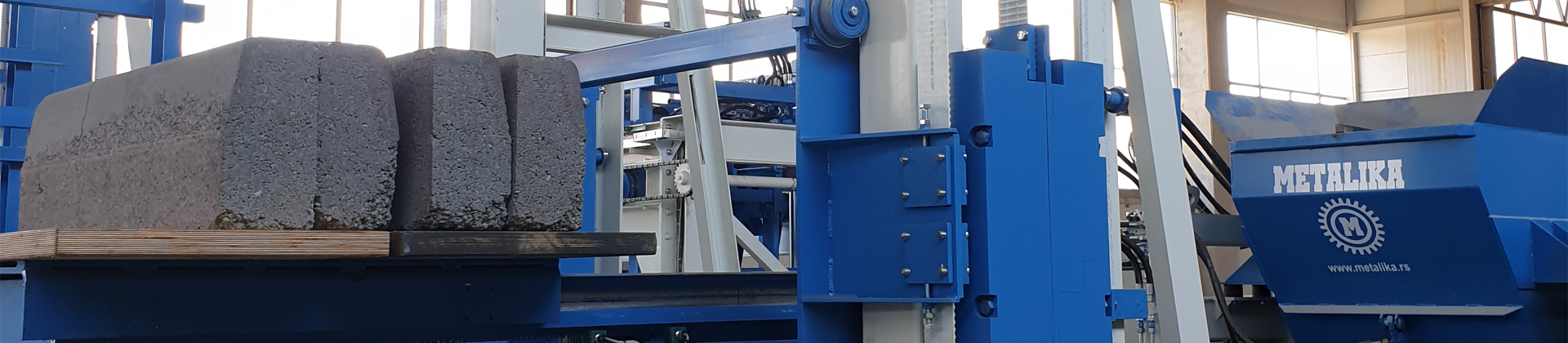
Flexibility and precision in positioning concrete blocks
VLT® AutomationDrive with IMC delivers flexible positioning with 0.5 mm precision
As manufacturer of concrete making machines and automated robotic lines, Metalika is constantly innovating to make its machines more competitive in the dynamic market. The Metalika concrete making machines take care of the entire process of mixing concrete, casting and curing concrete blocks, and packaging of the concrete blocks on pallets, ready for transport.
In the past, a concrete making machine delivered fixed dimensions of concrete blocks. Casting blocks of more than one size required more than one machine. However, with its newest automated concrete machine, Metalika aimed for more flexibility. Metalika needed a solution enabling them to build a machine with flexibility to produce a range of different dimensions of concrete blocks, and palletize them in different ways for transport.
From experience, Metalika knew they needed close control with a positioning function to achieve this flexibility. In the past, they had already attempted introducing a positioning function with various manufacturers of drives, but could not achieve appropriate precision. In addition, these early proposals involved inconvenient complex PLC programming as well as requiring external positioning sensors.
VLT® AutomationDrive FC 302 with Integrated Motion Controller (IMC) as a solution for exactly this need. IMC delivers the precision required and offers a parameter handling functionality which is free of complex programming. IMC is simpler to use than the earlier proposed systems, and even better for project costing, it does not require external sensors for positioning. The resultant performance vastly exceeded Metalika’s expectations. Using FC 302 drives with IMC, Danfoss achieved 0.5 mm precision in positioning concrete blocks. The specification for the machine was ±1-2 mm precision.
Stationary automated concrete making machine
Where does IMC optimize the automated concrete machine?
Seven FC 302 units rated 3 kW – 5.5 kW are installed per concrete machine, four of them equipped with IMC software. An induction motor with encoder is used, both directly connected to the drives. A homing sensor communicates the machine zero position. The whole process is executed via Modbus TCP fieldbus communication, which facilitates easy wiring of the system.
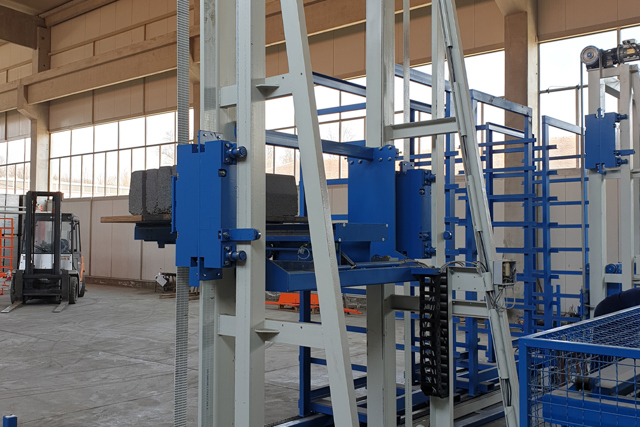
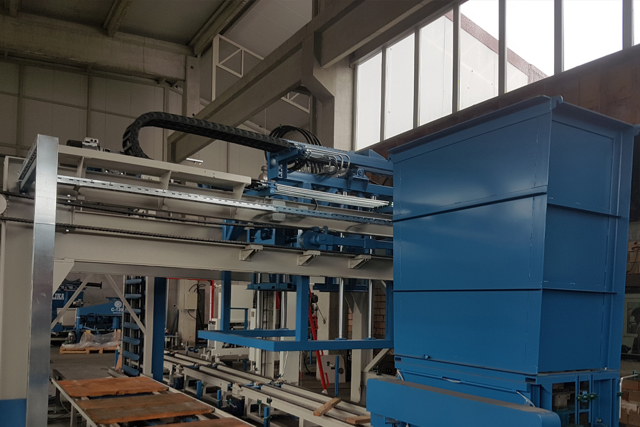
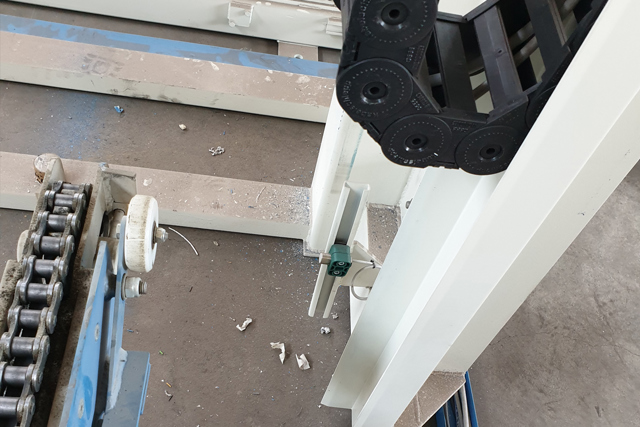
High-precision positioning and synchronization with reduced costs and system complexity
To optimize performance, many applications across all industry sectors have a need for precise positioning and synchronization. These applications include rotary tables, packaging machines, labelling machines, conveyors, extruders and palletizers. In the past, positioning and synchronization operations have been performed using servo drives. However, servo equipment is expensive; it is difficult to commission and requires additional cabling. And, as servo drives do not work with open loop control systems, there is a high failure rate. Many applications do not require the high dynamic performance offered by a servo drive. An alternative was to use an AC drive. But, until recently, an additional internal or external module or an encoder on the motor was required.
Sensorless alternative to servo control
An innovative alternative to servo control is the Integrated Motion Controller (IMC) functionality that enables an AC drive to perform high-precision positioning and synchronization operations without the need for additional modules or hardware. IMC is configurable in the software of the VLT® AutomationDrive FC 302, and offers many advantages. It works with all conventional motor technologies, with closed loop or open loop control, and offers sensorless homing with torque detection. Drives are adapted to the applications through simple parameterization. This means that no special knowledge of servo technology or programming languages is required. As no encoder or additional cables are needed, engineering, installation and commissioning time and costs can be reduced.
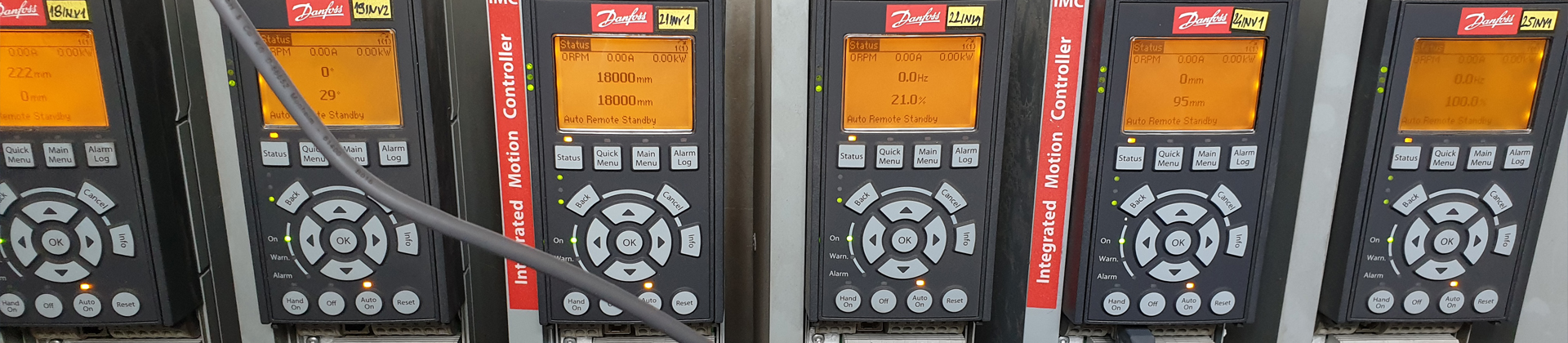
Discover VLT® AutomationDrive with Integrated Motion Controller
IMC delivers the precision required and offers a parameter handling functionality which is free of complex programming.
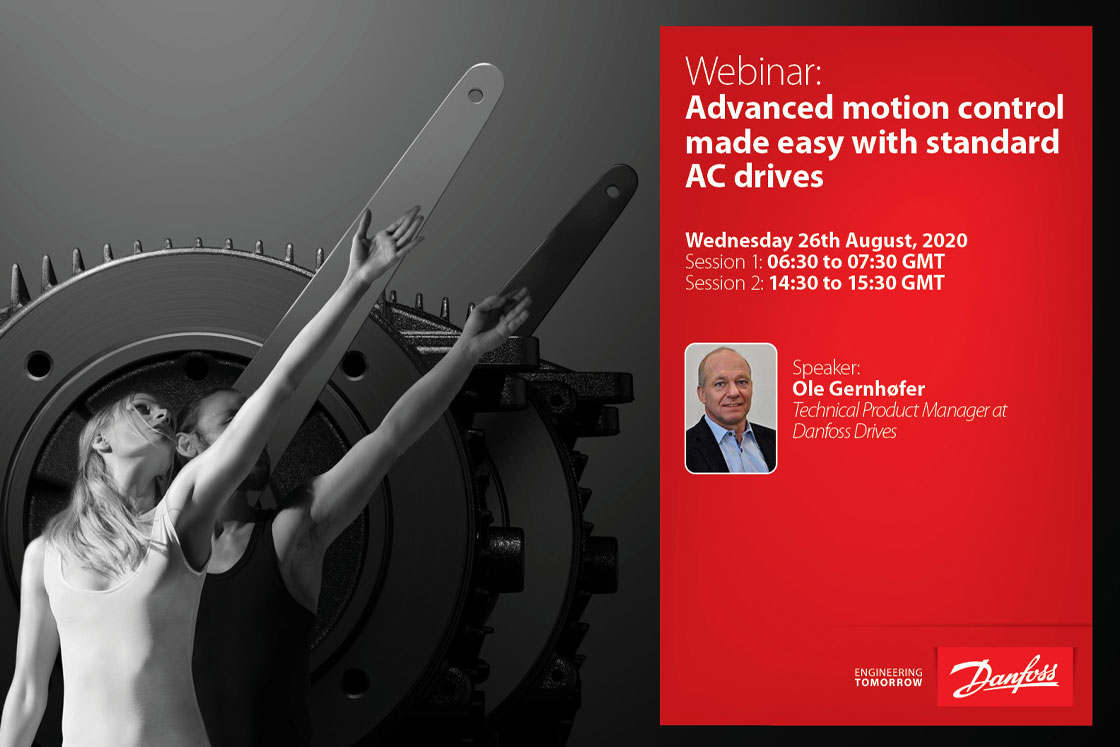