About inverter technology for AC, heating and ventilation
A quantum leap in energy efficiency
The HVAC market is rapidly changing. AC inverter drive technology is the most energy efficient technology and is currently revolutionizing the way air conditioning systems are being designed and built to meet climate control needs around the world. The first to embrace variable-speed technology gains a competitive advantage.
Market needs: Avoid system oversizing, reduce electricity bill and inrush current, increased comfort and process are some key drivers for variable capacity.
Modulating technologies: There are several ways to modulate the cooling capacity in refrigeration or air conditioning and heating systems.
Working principle: Inverter compressors operate at different speeds generating a modulated refrigerant mass oil flow and cooling output.
Video "Inverter Compressors for HVAC"
Benefits: Better power supply quality, system diagnostics, humidity control, energy savings, accurate temperature control, less noise, process safety, greater comfort
Challenges: Compressor and drive selection, designer skills makes the system overall reliability and efficiency.
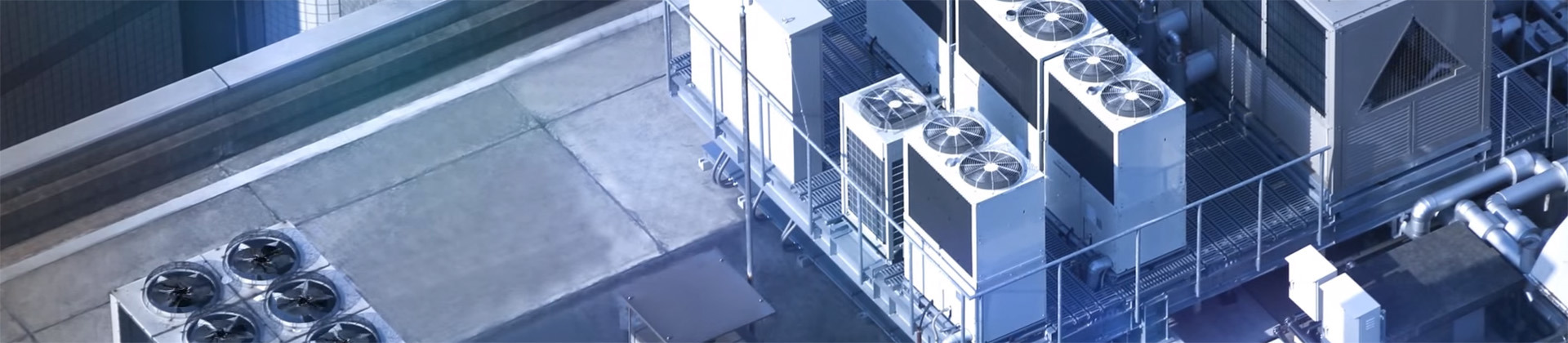
Danfoss variable speed technology
By using the Danfoss inverter compressor solutions, significant energy savings can be achieved compared to traditional on-off compressors or mechanically-modulated technologies.
Highlighted products
-
if (isSmallPicture) {
; } else if (isBigColumns) { } else { }Reciprocating inverter - VTZDanfoss reciprocating inverter compressors avoid oversized and short cycling systems. The compressor automatically adapts to the current load. By combining an efficient Danfoss Maneurop® reciprocating compressor with a Danfoss Drive, the company provides an innovative and intelligent package that utilizes variable-speed technology to ensure superior efficiency across the entire operating range for precision cooling.
-
if (isSmallPicture) {
; } else if (isBigColumns) { } else { }Inverter scrolls - VZHDanfoss inverter scroll compressor VZH offers effectiveness and reliability. Over 30% energy savings is possible in rooftops, chillers, close controls etc.
-
if (isSmallPicture) {
; } else if (isBigColumns) { } else { }Turbocor® - TGSDanfoss Turbocor model TGS oil free compressors are available in 5 different models ranging from 40 tons to 150 / 140 kW to 540 kW utilizing ultra-low GWP R1234ze or R515B.
-
if (isSmallPicture) {
; } else if (isBigColumns) { } else { }Turbocor® - TTSDanfoss Turbocor®model TTS oil free compressors are available in four different models ranging from 60 tons to 200 tons / 200 to 700 kW utilizing R134a or low GWP R513A.
-
if (isSmallPicture) {
; } else if (isBigColumns) { } else { }Turbocor®Danfoss is the leading manufacturer of oil-free compressors and is the pioneer of the Danfoss Turbocor® compressor - the world’s first oil-free magnetic bearing compressor for the HVAC industry.
Related applications
-
if (isSmallPicture) {
; } else if (isBigColumns) { } else { }Air handling units with inverterAir handling units with integrated cooling are used in commercial applications for air conditioning in many different kinds of buildings, from small office buildings, fitness centers and medical institutions to skyscrapers.
-
if (isSmallPicture) {
; } else if (isBigColumns) { } else { }Close controls with inverterPackaged unit for electronic cabinet cooling. Close control air conditioners are used in the cooling of electronics such as IT and electronic equipment used in data centers, in telecommunications and in manufacturing industries.
-
if (isSmallPicture) {
; } else if (isBigColumns) { } else { }Modular chillersCore component of the HVAC system, a chiller cools the water or brine used to cool and dehumidify air in buildings or industrial processes. It's a factory-assembled unit that cools the water or brine using an evaporator, and has an internal or a remote condenser with appropriate controls.
-
if (isSmallPicture) {
; } else if (isBigColumns) { } else { }Packaged unitCooling of IT equipment in data centres is an increasing challenge for operators and design engineers. Power management is the major challenge, with energy consumption and heat loads increasing in step with the server density. Meeting these challenges is essential for ensuring the safety and availability of the data.
-
if (isSmallPicture) {
; } else if (isBigColumns) { } else { }Process coolingIn many industrial processes the machinery or processes generate heat which requires cooling, to protect the equipment and/or to ensure that the product being manufactured is of the required quality. The process cooling unit is used to cool, to extract humidity or regulate the temperature of the manufacturing process.
-
if (isSmallPicture) {
; } else if (isBigColumns) { } else { }Variable refrigerant flow with inverterVariable Refrigerant Volume or Variable Refrigerant Flow (depending on the manufacturer) has been established since the early 1990s. The basic idea is that a large outdoor unit (or several manifolded outdoor units) serves multiple indoor units.
Learning
Online training and e-lesson about inverter technology
Welcome to the Danfoss online training portal! Through this service, Danfoss strengthens its support to all HVAC-R professionals and students. Sign-up today for a great opportunity to maximize your performances and profits!
What’s in it for me?
- Learn about the existing technology from the leader in variable speed / inverter compressors.
- We offer free e-lessons, online courses and face-to-face seminars illustrated with technical explanations, videos and in field experiences.
Just follow these quick steps to start:
- Register on Danfoss learning Platform.
- Attend the e-lessons by clicking on below links
Case stories
-
if (isSmallPicture) {
; } else if (isBigColumns) { } else { }Denmark's new climate-friendly hospitality giant depends on Turbocor® oil-free chillerThe new Alsik hotel in Southern Denmark sets a higher standard in energy-efficiency and is built to reach 76% CO₂-neutrality. A main contributor is the 900-kW chillers by Clint (a company of G.I. Industrial Holding) which features award-winning Danfoss Turbocor oil-free compressors.
-
if (isSmallPicture) {
; } else if (isBigColumns) { } else { }Oil-free compressors maintain consistent performance over timeDanfoss conducted a study to see how long term operation affected performance on Danfoss Turbocor® compressors. The results showed that oil-free, magnetic bearing compressors maintained consistent performance even after 10+ years of operation.
-
if (isSmallPicture) {
; } else if (isBigColumns) { } else { }Wind powerWind turbine producing water cooled by an energy efficient refrigeration system featuring inverter scroll compressor
-
if (isSmallPicture) {
; } else if (isBigColumns) { } else { }Shopping mallsInverter technology is improving one of the world's largest home DYI stores and helping gain Brazil’s first sustainability certificate with an innovative air conditioning installation.
-
if (isSmallPicture) {
; } else if (isBigColumns) { } else { }Satellite launch towersThe satellite launch tower is a vital facility. Reliable energy efficient inverter HVAC unit in this critical application was secured with Danfoss solution.
-
if (isSmallPicture) {
; } else if (isBigColumns) { } else { }Process chillersVariable speed with Danfoss Turbocor Oil free centrifugal compressor guarantees reliable process cooling and efficient comfort cooling in factory
News
-
if (isSmallPicture) {
; } else if (isBigColumns) { } else { }Danfoss and RefPower collaborate to offer customers energy-efficient screw compressorsWednesday, June 29, 2022Danfoss Commercial Compressors has entered into a strategic collaboration with Italian based, RefPower Srl, to introduce and sell new screw compressors to the European market.
-
if (isSmallPicture) {
; } else if (isBigColumns) { } else { }Coolselector®2: We did complex. You do awesome.Wednesday, March 20, 2019Coolselector®2 is essential software for engineers, consultants, and system designers who work in the refrigeration and air conditioning industry. Using Coolselector®2, you can easily optimize energy consumption and increase efficiency in your HVACR system — simply run calculations based on your operating conditions and then choose the best component setup for your design.
-
if (isSmallPicture) {
; } else if (isBigColumns) { } else { }New 8.5 TR and 11 TR variable speed compressors with IDVWednesday, October 10, 2018New efficiency opportunities for Chiller/Rooftop units and Computer Room Air-Conditioners
Danfoss has added new 8.5 TR and 11 TR (*) variable speed compressors with IDV(**) to its popular VZH range, giving commercial cooling manufacturers the market’s most complete choice of variable speed scrolls with qualified drives for HVAC systems.
Contact us
For further information, please contact us.