The global injection molding market is ever-expanding and increasingly competitive – producing everything from fast cycle, high volume items such as bottle preforms, to high precision items such as mobile phone components.
The injection molding market has long focused on improving energy efficiency and productivity through incremental changes, resulting in a move away from traditional hydraulics to hybrid systems combining hydraulic pumps with variable speed drive systems.
With the ever-increasing focus on energy usage, manufacturers have been focused on developing equipment that will reduce the energy demand per piece and improve production uptime and reliability.
Direct electric drives are the best choice for small, highspeed injection molding machines, but as machine size increases it is prohibitively difficult and expensive to utilize this technology. The shift to electronically controlled swash plate pumps has significantly reduced the energy consumption of hydraulic injection molding machines – and while this technology is mature, the internal leakage, mechanical inefficiencies, and lack of controllability of these pumps provide an opportunity for improvement.
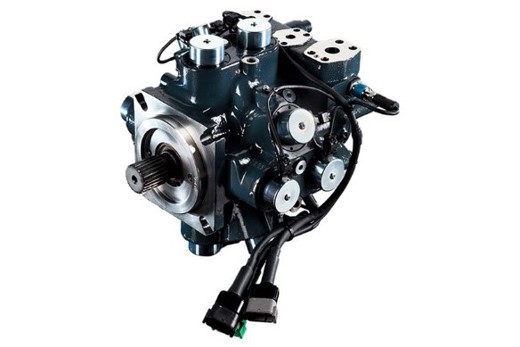
Now a new category of digital pumps is set to transform the industrial hydraulics market.
The DDP096 is the first in a series of Digital Displacement® pumps being brought to the market by Danfoss Power Solutions.
Digital Displacement is a unique technology. It utilizes a radial piston mechanism with high mechanical efficiency and ultra-fast microprocessor controlled mechatronic valves to enable or disable cylinders every pump revolution. Digital Displacement provides the exact flow needed at the exact instant.
When combined with traditional fixed speed induction motors, Digital Displacement delivers better performance When combined with traditional fixed speed induction motors, Digital Displacement delivers better performance and efficiency than variable speed motor drives – and therefore eliminates the need for variable speed drives.
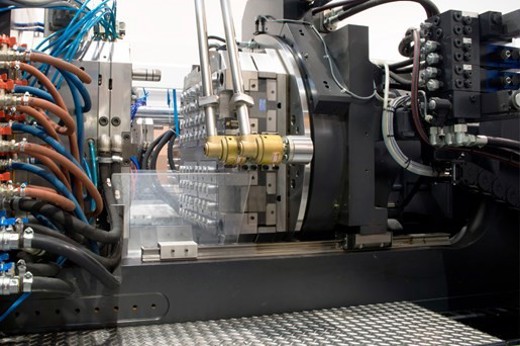
In larger injection molding machines, Digital Displacement provides the required power density, fast response and high efficiencies over a wide operating range, rivaling and exceeding electric machines.
The fast duty cycles of the latest generation of energy efficient injection molding machines requires pumps with fast response times and high dynamic range, a feature which is easily accomplished by Digital Displacement.
And with pressurized idle losses around 90 percent lower than conventional hydraulic axial piston pumps, significant reductions in standby energy use can be achieved. In situations such as mold clamp hold or while the machine is in standby, the savings quickly add up.
Intelligent control
A Digital Displacement pump can have multiple independently controllable outlets, offering the ability to have two or more outlets working in totally independent control modes.
When placed at the heart of a hydraulic machine, a single Digital Displacement pump can provide flow to up to four independent hydraulic functions, or circuits, working at totally different pressures and flows – replacing either multiple motors and pumps, or tandem arrangements, with a single intelligently-controlled pump.
Optimizing the hydraulic circuit around multiple independent systems reduces throttling losses in valves by providing the exact pressure and flow for the function, rather than bleeding off excess hydraulic energy across a metering valve. By doing this, significant energy savings can be realized in addition to the already improved pump efficiency.
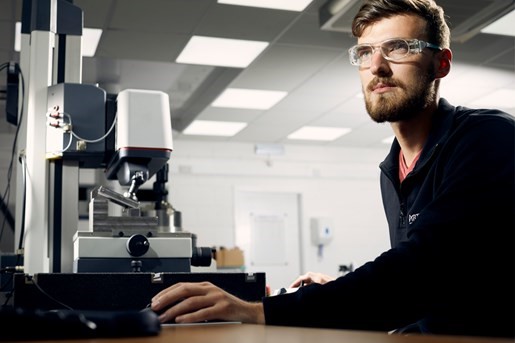
For fast cycle machines, consistent repeatability often limits the cycle time, however, the ultra-fast response of the Digital Displacement pump provides a consistent and reliable hydraulic source enabling faster cycle times. Faster cycle times means higher throughput, better utilization of machine capital and higher profit.
Digital Displacement pumps are configured via software – and this offers the potential to rapidly setup machines for new product lines without the need for hardware intervention.
In addition, Digital Displacement pumps operate over a wide pressure range. The pump’s response is not dependent on pressure and the pressure setpoint can be dynamically adjusted as an input to the digital pump controller.
The Digital Displacement pump’s reduction in energy loss through improved pump and hydraulic circuit efficiency not only results in electricity savings, reduction in electric motor and wiring size, it also reduces cooling needs. Reducing cooling system capacity results in lower energy consumption, reduced capital expenditure and improved profitability.
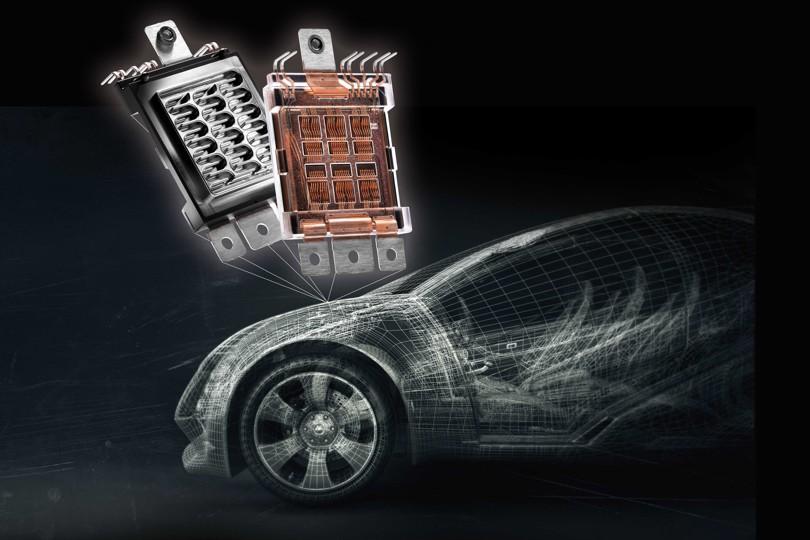
This is where the electrification starts
To power up the fast-growing fleet of electric vehicles Danfoss developed a cutting-edge power module technology platform for traction application - the DCM™1000.