Maximizing the potential of Si and SiC power modules
To power up the fast-growing fleet of HEVs, PHEVs and BEVs, Danfoss has developed a power module technology platform, DCM™1000, for traction applications.
With silicon (Si) and silicon carbide (SiC) being the main cost-drivers in power modules, our DCM™1000 platform aims at reducing the semiconductor surface enabled by combining our winning patented technologies.
Your DCM™1000 benefits
Customizable to your exact needs
Combining of winning technologies for higher performance
Maximizing the potential of Si and SiC
Scalable across voltage classes
FAQs about the DCM™1000
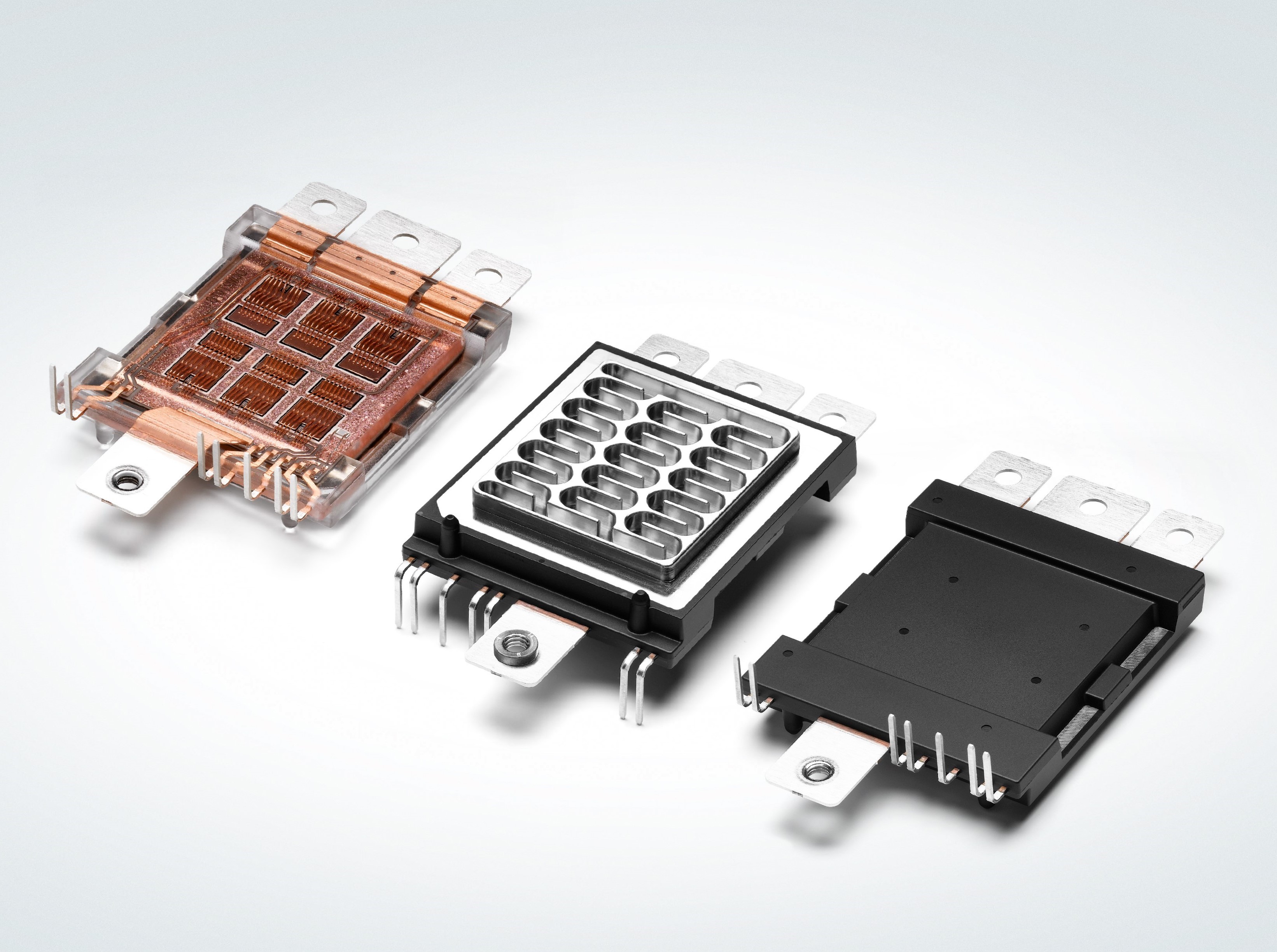
SiC and IGBT power modules
Danfoss engineers custom SiC and IGBT power modules to help you meet stringent reliability, design and cost targets.