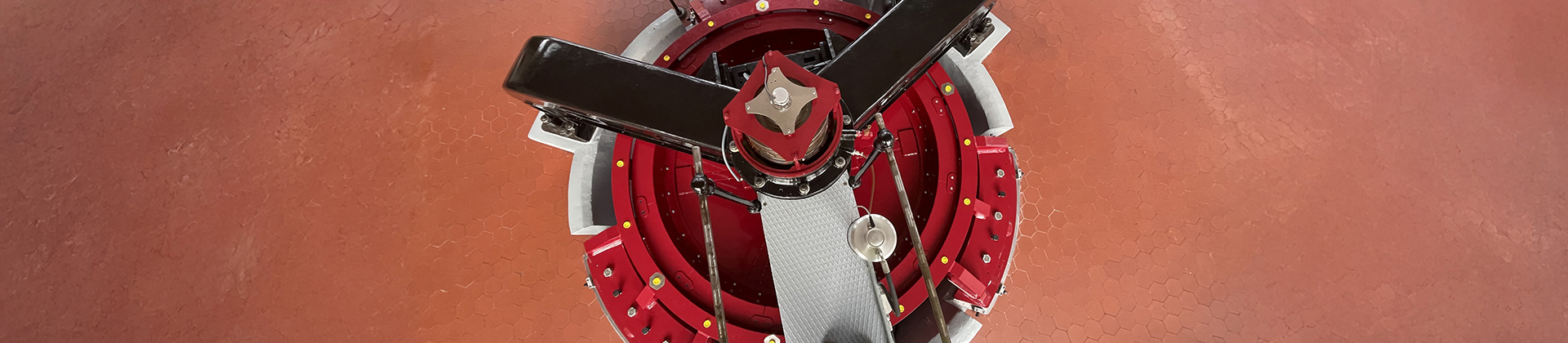
How can variable speed control optimize hydroelectric power generation?
CZECHIA: In the Albrechtice and Orlicí municipality in Czechia, a small hydropower plant (SHP) has been supplying electricity to surrounding towns since before World War II. However, the plant was originally designed to produce energy at maximum efficiency for only about three months a year. When the 80-year-old gears began to fail, Danfoss proposed a retrofit solution that eliminated the need for gears and introduced variable speed drives to increase the plant’s efficiency with minimal adjustment to the existing installation. The new gearless solution includes a VACON® NXC low harmonic drive, a VACON® NXP Common DC Bus, and DrivePro® services. As a result, the plant now produces approximately 10% more energy than the previous setup.
Discover how SHP Albrechtice improved the efficiency of their operations with a retrofit solution and DrivePro® services.
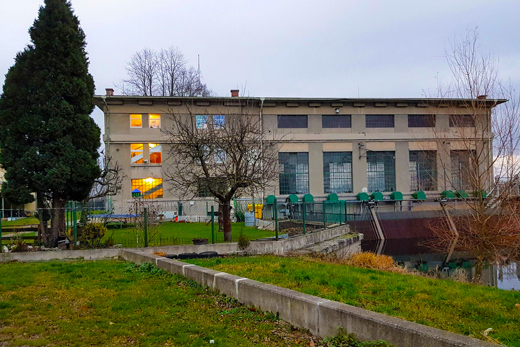
The challenge: Ensuring year-round efficiency despite changing demands
High efficiency, performance, and longevity are key for any hydropower plant to operate reliably while reducing maintenance costs. However, with one 150 kW and two 250 kW Francis turbines with MV synchronous generators synchronized to the grid and running at a fixed speed, the 80 year-old SHP Albrechtice installation was designed to operate at optimal efficiency only during the three months of the year when water levels were most consistent.
When SHP Albrechtice saw the gears in the old generators begin to fail, they reached out to Danfoss and Q-ELEKTRIK for a new solution. Danfoss identified an opportunity to improve efficiency in the old installation by retrofitting the system with drives and a synchronous generator with permanent magnets, rather than simply replacing the worn gears with new ones.
The old gears had been working well for 80 years, but technology has obviously advanced quite a bit since then. We saw a chance to enhance efficiency by introducing variable speed drives. However, we wanted to avoid making the project more extensive than necessary, so we proposed a retrofit solution instead of a full replacement
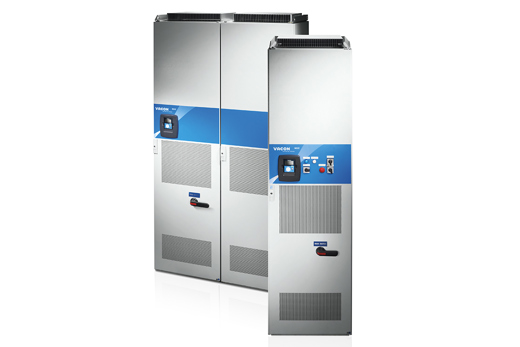
The solution: Adapting to the changing flow with variable speed drives
The system proposed by Danfoss included a 250 kW TES VSETIN GSP1120S60 synchronous generator with permanent magnets, a 250 kW Danfoss VACON® NXC Low Harmonic drive with regenerative capabilities, and a brake chopper unit from the VACON® NXP Common DC Bus products.
One of the standout features was the robust design of the compact VACON® NXC drive, which adjusts the frequency and voltage of the power supplied to the motor/generator. This allows the turbine to run at variable speeds, adapting to changes in water flow and maintaining optimal performance under different conditions — always generating maximum power at any given time.
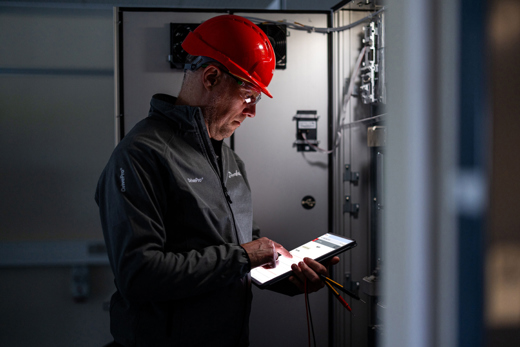
The drive, which includes an integrated filter for harmonic mitigation, was custom configured with an Active Front-end (AFE) inverter equipped with a voltage measurement board to support grid code compliance.
In addition to the two types of drives, SHP Albrechtice selected two DrivePro® lifecycle services to ensure a smooth implementation and minimize unplanned downtime. With DrivePro® Start-up, professional drive experts helped guarantee optimal performance from day one, reducing both installation and commissioning time and costs. DrivePro® Preventive Maintenance offers a tailored maintenance program, helping the plant enhance efficiency while mitigating the effects of wear and tear.
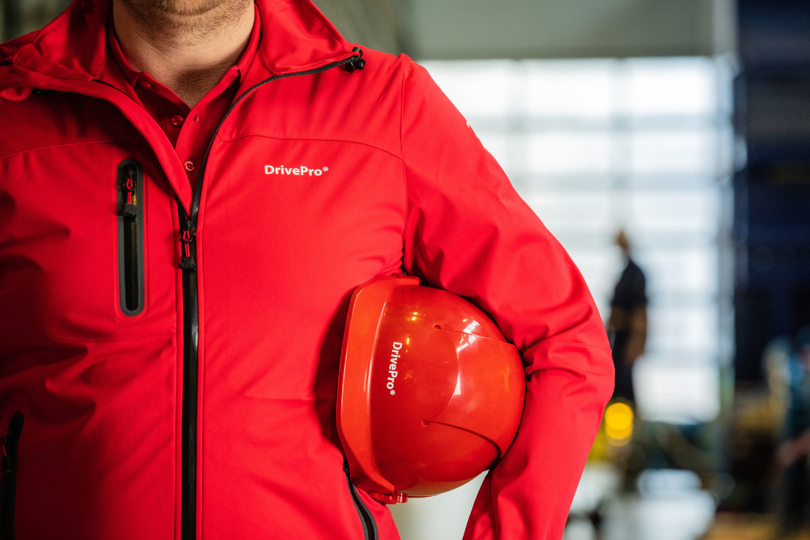
Benefits of VACON® NXC and VACON® NXP drives with DrivePro® services:
- The VACON® NXC enclosed drive performs reliably in harsh operating conditions
- VACON® NXC offers lower maintenance costs due to its robust, type-tested design
- Reduced energy costs with VACON® NXP as regenerative front end feeds excess braking energy back into the network
- The active front-end unit in VACON® NXP improves drive line-up tolerance to voltage dips/sags and minimized harmonic distortion
- DrivePro® services cover the full lifecycle of a Danfoss drive, maximizing performance, uptime, and lifespan with expert assistance and a predictable maintenance budget
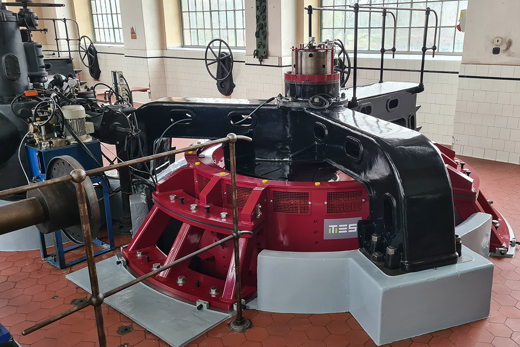
The outcome: Producing 10% more energy in the first year
After one year of operation, SHP Albrechtice’s expectations for a more efficient setup had already been met.
“With the ability to adjust the speed of the system based on real-time demand, we produced 10% more energy in the first year of running the new setup,” says Mr. Jiří Čáp, Owner, SHP Albrechtice.
In addition, the system, along with the two service agreements, has helped the plant reduce maintenance costs and minimize stoppages.
“Overall, our experience with Danfoss has been very positive, marked by a proactive approach, dedicated people, and clear communication,“ says Mr. Jiří Čáp.
Preparations began in 2021, with commissioning taking place at the end of 2022. The first DrivePro® Preventive Maintenance visit is scheduled, and an upgrade of the plant’s next generator is planned for 2025.
Related products
-
if (isSmallPicture) {
; } else if (isBigColumns) { } else { }DrivePro® Start-upTake the complexity out of commissioning with DrivePro® Start-up’s full range of health checks and adjustments. Our DrivePro® experts inspect and test your AC drive and motor performance to ensure the best configuration of your AC drives.
-
if (isSmallPicture) {
; } else if (isBigColumns) { } else { }DrivePro® Preventive MaintenanceTake the guesswork out of your maintenance plan. With a structured maintenance program tailored to your needs, you can boost operational efficiency and reduce the effects of wear and tear.
-
if (isSmallPicture) {
; } else if (isBigColumns) { } else { }VACON® NXCAn enclosed drive designed for demanding applications that includes options for Active Front Ends and low harmonic solutions.
-
if (isSmallPicture) {
; } else if (isBigColumns) { } else { }VACON® NXP Common DC BusEnables system integrators, machine builders and OEMs to design and build efficient industrial drives systems. Active Front-end (NXA), Non-regenerative Front-end (NXN), Brake Chopper (NXB) and Inverter (NXI) configurations are available.
More case stories
-
if (isSmallPicture) {
; } else if (isBigColumns) { } else { }Unlocking efficiency with a drive retrofit at a Czech hydropower plantCZECHIA: When 80-year-old gears were replaced by variable speed control at the Albrechtice hydropower plant, power production increased by 10%.
-
if (isSmallPicture) {
; } else if (isBigColumns) { } else { }Revolutionizing green hydrogen production with Danfoss DrivesDENMARK: The Everfuel HySynergy facility produces green hydrogen with the help of iC7-Hybrid power converters for efficient, cost-effective electrolysis.
-
if (isSmallPicture) {
; } else if (isBigColumns) { } else { }Danfoss powers high-capacity SmartGrid energy storageNETHERLANDS: Retaining 80% capacity after 8000 cycles, SmartGrid smart battery containers promise 21 years of daily discharge and recharge without performance concerns.
-
if (isSmallPicture) {
; } else if (isBigColumns) { } else { }Speedy AC drive retrofit for Linz StromAUSTRIA: A Linz Strom power plant needed to replace three ageing AC drives. DrivePro® Life Cycle Services played an essential role in meeting project requirements.
-
if (isSmallPicture) {
; } else if (isBigColumns) { } else { }Generating energy from green waste to fuel a cityAUSTRALIA: Jeffries Group supports the city of Adelaide by using the biochar byproduct of green waste to generate renewable energy, driven by VACON power conversion. There's enough power to run their entire green waste operation and feed surplus energy back into Adelaide’s power grid — with zero emissions.
-
if (isSmallPicture) {
; } else if (isBigColumns) { } else { }Unique heat recovery for geothermal power using VACON® drivesAUSTRALIA: A geothermal power station recovers energy during the bore water cooling process then uses it to generate power for the local community, with the help of VACON® drives.