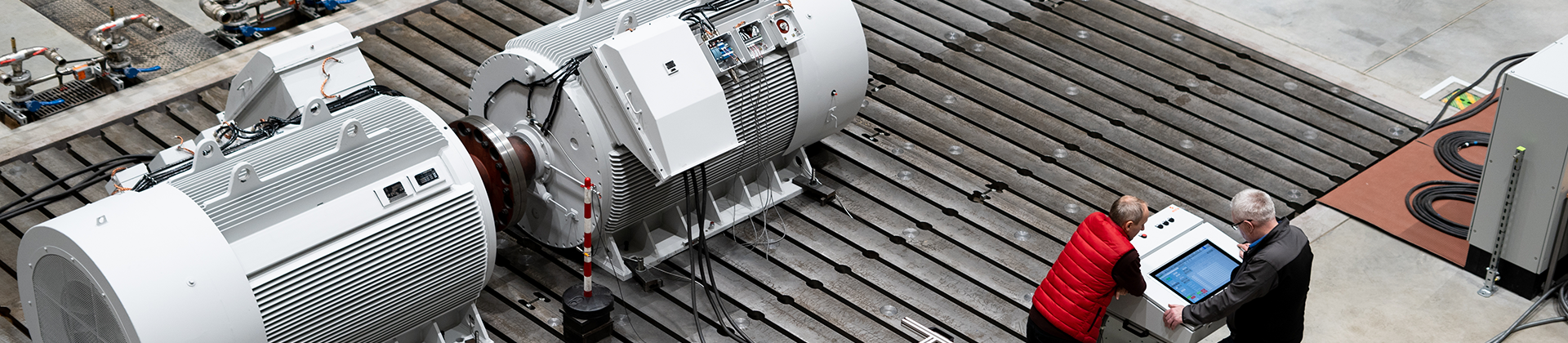
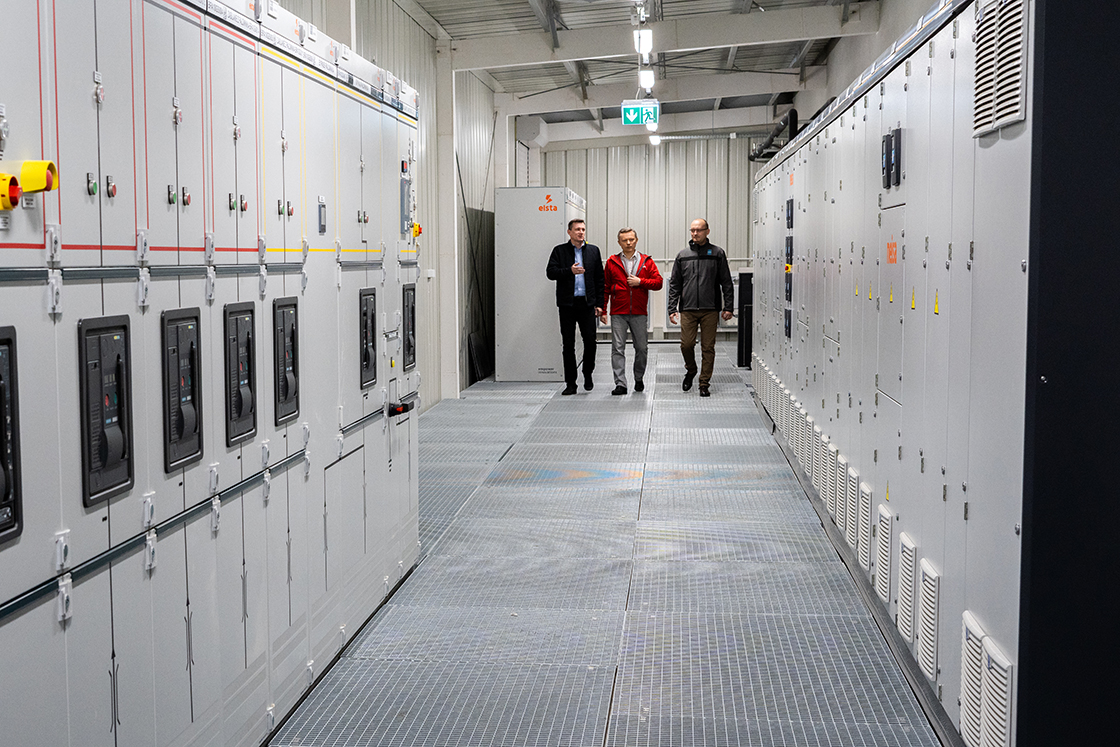
POLAND: EMIT (EMIT Electric Machines Manufacturing Company) has established a Research & Development Center which enables testing the parameters of motors with a diverse range of power outputs, dimensions, cooling systems and rated voltages. It is the most modern facility of its kind in Poland, and one of the most modern ones in Europe. By conducting comprehensive motor tests, EMIT can refine its manufacturing processes. EMIT also makes the Center available to partners, customers and research establishments who want to validate motor performance.
Thanks to an innovative approach, the systems at the Center consume minimum electric power. A recovery system ensures circulation of electricity throughout the premises, so only the amount of power required for covering losses is drawn from the mains. The heart of the Research & Development Center is a commercial drive system based on VACON® NXP drives.
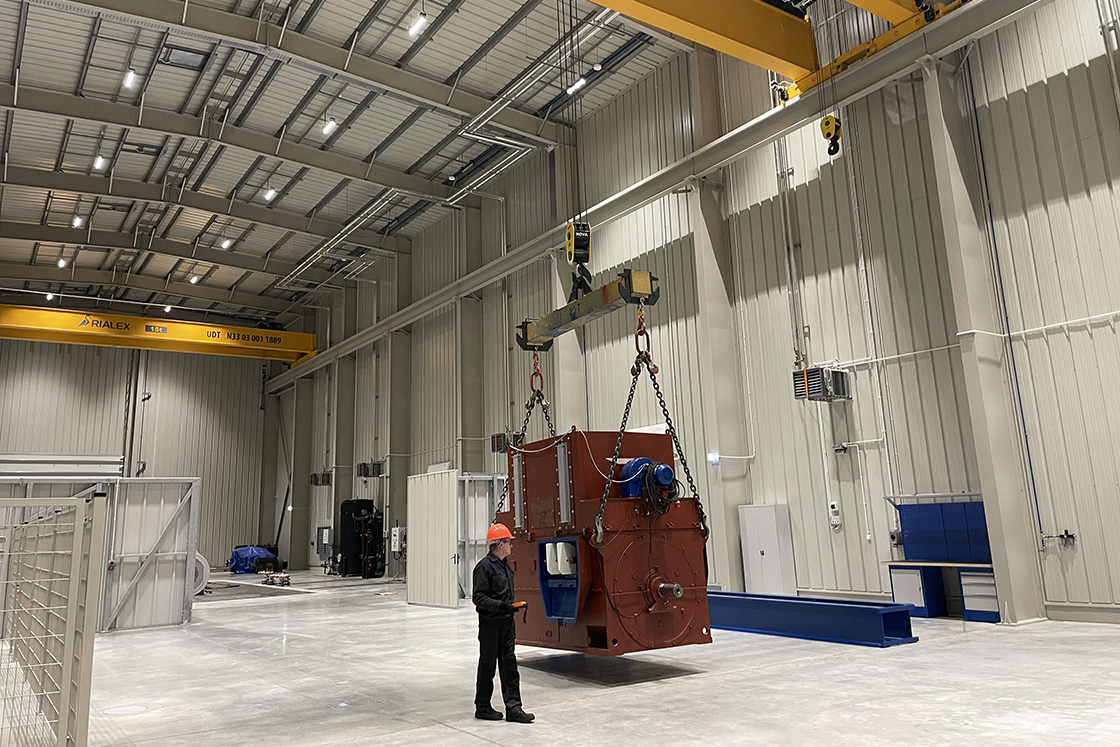
The challenge: Power and voltage limitations when testing
One of the aims in designing the Research & Development Center was to supplement the previously used motor testing methods based on the Ward-Leonard system. The power and voltage limitations inherent in the old system impacted the ability to conduct tests and the results obtained, since using substitute methods was necessary.
A requirement for the modern facility was its suitability for testing electric motors with diverse power outputs and rated voltages, even up to 15 kV, and with varying loads. This made it possible to conduct tests for as many industries as possible. According to the concept, the new center would be capable of verifying conformity of parameters to the existing standards, and also verifying performance exceeding current norms.
The matter of power consumption was also important. The designers opted to install drives in a circulating power system (on the DC voltage bus level), featuring power return to the mains. According to the planned solution, the motor would drive a generator, which would generate energy that would be sent to a drive, and then back to the tested machine. Thus, the power consumption costs of the Center aimed to be only 85% of a conventional system without energy recovery and circulation capability.

The solution: 15 MW regenerative drive system
A test slab with a surface area of 72 square meters accommodates testing of motors up to 60 tons in weight. The machines are handled with the use of modern overhead cranes.
The main component of the Center is a commercial drive system based on the VACON® NXP drive. The motor-generator power supply system comprises a total of 10 power inverters connected with a common DC bus. Direct engine and generator drives consist of 4 modules each, whereas the remaining 2 modules form a bidirectional rectifier system operating in the active front-end (AFE) system. As a result, excess energy is returned to the mains, and the level of harmonics is very low.
The power output of each drive system is 6 MW. The total power output of all the power modules is 15 MW. The system is liquid-cooled, and the entire length of the system cabinets, together with the cooling system exchangers, is 14 meters. The combined power output of the system is equivalent to the needs of a small town of 3000 households.

The outcome: Efficient, versatile, and reproducible tests
With its 15 MW capacity, the completed Research & Development Center can perform precise and reproducible tests of electric motor strength and efficiency. A manufacturer can draw relevant conclusions from the completed tests, and optimize its products in terms of strength, operating performance, and energy efficiency. That gives them the knowledge needed to reduce failure rate and ensure longer lifetime of equipment.
By using VACON® NXP drives from Danfoss, the research center has achieved high energy efficiency, and at the same time retains full potential for effective testing of electric motors. As a result, the EMIT company owns one of the most modern testing facilities in Europe. It now has the edge over its competitors because it can introduce innovations more efficiently while upholding the principles of sustainable development.
Thanks to its flexibility and wide range of compatibilities, the Center operated by EMIT provides new testing opportunities which were previously unavailable. These new testing capabilities benefit organizations from the industrial, power engineering, and chemical sectors. The Center also caters for equipment manufacturers who can now design, test, and develop a wide range of electric motor types with precision and ease.
Related case stories
-
if (isSmallPicture) {
; } else if (isBigColumns) { } else { }VACON® drives electrify passenger ferries in Oslo FjordNORWAY: Electrification of the Nesodden ferries has reduced CO2 emission in the port of Oslo. VACON® drives and power converters play a key role onboard.
-
if (isSmallPicture) {
; } else if (isBigColumns) { } else { }How did EMIT optimize its motor testing center?With regenerative drives and a focus on universal compatibility, this R&D facility excels in efficiency and versatility in motor testing.
-
if (isSmallPicture) {
; } else if (isBigColumns) { } else { }STX ocean research vessel meets 2025 efficiency targets, todayLeading Korean shipbuilders enhance their vessel performance with assistance from Danfoss for optimized operation, increased efficiency, improved quality, and greater customer satisfaction. Danfoss delivers innovative marine solutions introducing new standards for energy efficiency, expanding opportunities for the shipbuilding industry.
-
if (isSmallPicture) {
; } else if (isBigColumns) { } else { }Controlling a 3000t slew crane on Chinese offshore pipe-laying vesselAn innovative 3000-tonne derrick pipe-laying barge built by Shanghai Zhenhua Heavy Industry Co., Ltd.* uses the world’s most advanced pipe-laying technology. The vessel’s 3000-tonne, 360° slew crane is driven by VACON® AC drives.
-
if (isSmallPicture) {
; } else if (isBigColumns) { } else { }Massive grabber crane in control at Tata Steel IJmuidenLiquid-cooled VACON® active front-end drives control Tata Steel grabber crane, and the reliability of these AC drives is vital.
-
if (isSmallPicture) {
; } else if (isBigColumns) { } else { }38% fuel savings and emission reductions for CMAL ferriesCMAL ferries use 38% less fuel than conventional vessels and emissions are reduced by a similar amount.