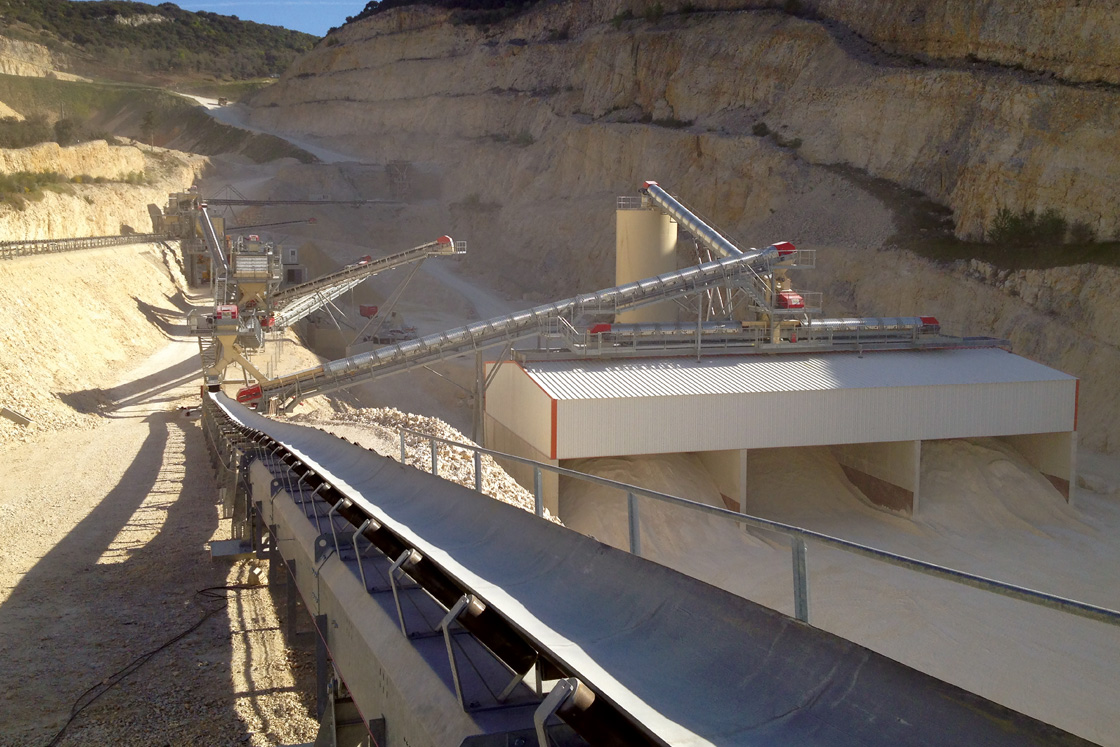
Fearless of the difficult applications, dust and bad weather, the VLT® AutomationDrive FC 302 was chosen to ensure efficient production of 800,000 tons of hard limestone at the Roussas quarry.
With an annual cement production capacity of 60 million tons and 42 cement plants across four continents, Italcementi Group is a leading global supplier of construction materials. The group is a major player in the French building-material market; in the cement business through Ciments Calsia, in the ready-mix concrete sector through Unibéton and in aggregates production and supply with GSM.
Italcementi has a strong focus on innovation and sustainable construction materials. They saw many synergies with Danfoss and decided to invest in 31 VLT® AutomationDrives to control the speed of industrial applications such as conveyors belts, water pumps, agitators and crushers in the GSM Aggregates limestone quarry in Roussas, France.
The three main goals of the investment were to:
- reduce energy consumption
- optimize productivity
- reduce the risk of malfunction by removing the need for long cables
Optimized performance in all conditions
Quarries are notorious for being harsh environments, with dust, noise, extreme temperature variations and vibration frequent occupational hazards. The VLT® AutomationDrive’s broad range of enclosure sizes and protection ratings from IP20 to IP66 made it easy to install the drives outdoors, directly on the frame of the applications, which ensured reliable operation in the quarry’s harsh conditions.
Previous drives used at the site had a relatively low power range and, being placed in protective cabinets, meant that significant costs associated with their cooling were incurred.
The VLT® AutomationDrive’s control algorithm, its over-torque of 160%, wide power range up to 1.4 MW and versatility made it suitable for the wide range of applications on site. And, the fact that its RFI filter and harmonic chokes are integrated in the IP66 housing, ensured protection of the electronics and increased efficiency. In addition, because the drives are cooled by ambient air, they no longer encounter overheating problems, which will enable tangible energy savings.
The configuration of the installation meant that the drives could be installed in the immediate vicinity of the motors which simplified infrastructure management and development costs.
The size of control cabinets could be reduced and high-performance fieldbus options installed in the VLT® AutomationDrive enabled connection to EtherNet/IP-based networks, which simplified cabling.
Accurate performance analysis
The VLT® AutomationDrive contains many integrated sensors that can extremely accurately monitor daily site activities. Frequent and relevant performance records can be generated that indicate where energy savings at all levels can be made.
The qualities of the VLT® AutomationDrive allowed Italcementi to rethink the automation of their facilities, particularly with regard to the water pumps that are spread across all their sites. They can now be fully controlled by the drives.