Traditional Machines
A problem common to many off-highway and material handling machines
An R&D project is combining the super-fast characteristics of Digital Displacement® pumps with a Danfoss PLUS+1® controller to improve control and reduce ‘bounciness’ and oscillations in off-highway and material handling machines.
Very small movements in a joystick can translate to large movements and ‘bounciness’ in a bucket or boom. This can be tiring for the operator, it introduces risk and wastes time and energy over the course of a work-cycle, resulting in less productivity at the end of the day.
These oscillations can be reduced in the hands of a skilled operator, but as we move to increased automation and improved operator experience, a technical solution offering better control can be found.
To date, the main solution has been to throttle flow via proportional valves – which results in energy losses and poor system efficiency.
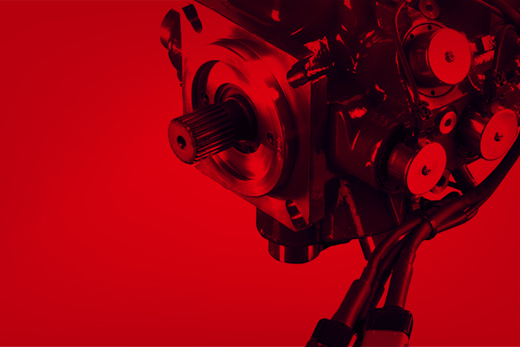
Digital Displacement® Hydraulics
R&D team in Edinburgh in innovative project
Now Danfoss Power Solutions is moving ahead with an innovative project which combines the super-fast characteristics of Digital Displacement® pumps with a Danfoss PLUS+1® controller.
The company’s R&D team in Edinburgh has constructed a motion control rig, with a 96cc Digital Displacement pump motor being used to raise and lower a boom actuated by a hydraulic cylinder – identical to the cylinder found in a standard 20-tonne excavator. In this set up the Digital Displacement pump is coupled directly to the cylinder, with no valves in between. In a typical scenario, a step up in flow from the pump would cause a pressure oscillations and thus unstable movement of the boom.
To combat this, the R&D team modified the pump command to be out of phase with the pressure oscillations, thereby radically reducing their amplitude.
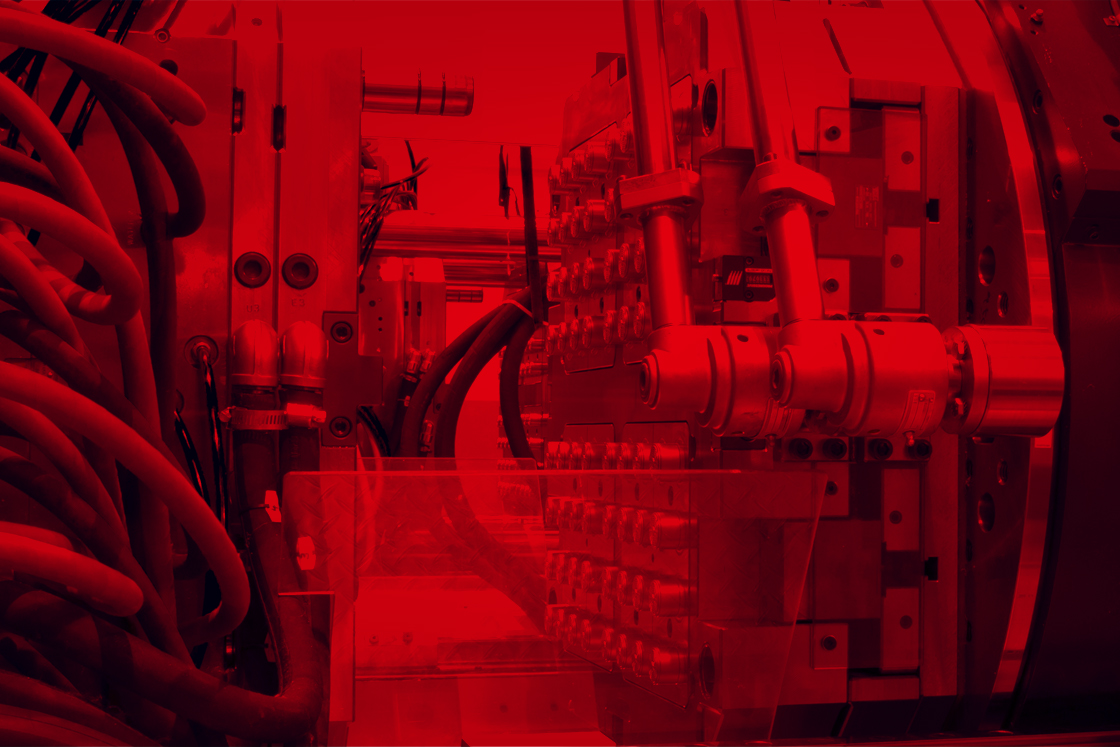
Radically Improved
Very low hysteresis and fast response time
This solution, which purely uses the displacement of the pump, is only possible because of the very low hysteresis and fast response time of a Digital Displacement pump, which can go from zero to full flow or vice versa in half a shaft revolution.
To test this the Edinburgh team created a simulation model and developed code in Simulink. They then used a ‘Simulink to Plus+1 tool chain’ which has been developed by Digital Displacement engineers in Ames, Iowa, to enable the code to be uploaded directly to Danfoss’s ruggedized PLUS+1® controller.
This newly programmed controller was then used to command the pump on the test rig in Edinburgh, with the pressure signal from the hydraulic cylinder fed back to the controller
The Results
Smoother, more responsive operator control
The results have been extremely positive. The modified commands reduced the amplitude of the oscillations by 81 percent (RMS velocity) on the test rig and offered smoother, more responsive operator control.
Building on these results the team is now modelling more complex scenarios with multiple actuators including booms and arms operating over a wide range of frequencies.
It is hoped the resulting outputs and test rig results will pave the way to making active damping a readily adoptable commercial product in the years ahead.