Industrial motor drives
Motor drives are the backbone of modern global industry. They are well hidden, but nevertheless they play a key role in industries helping to make the world, and our way of living, more sustainable. Today, the most common usage of drives is for the control of fans, pumps and compressors. These applications account for about 75 percent of all drives operating globally.
Motor drives go by various names such as AC drives, adjustable speed drives, adjustable frequency drives, variable frequency drives, variable speed drives, frequency converters, inverters and power converters. By varying the frequency and voltage of the power supply to an electrical motor, drives can control its speed making it possible to enhance process control, reduce energy usage and generate energy efficiently or optimize the operation of various applications relying on electric motors.
Drives also have the capacity to control ramp-up and ramp-down of a motor during start or stop respectively. This decreases mechanical stress on motor control applications and improves ride quality in, for example, elevators.
Motor drives can also be utilized to convert energy from natural and renewable resources like the sun, wind or tides, and transmit it to the electrical network or use it for local consumption. In hybrid technologies, motor drives are used to combine conventional energy sources and energy storages to create total energy management solutions.
IGBT power modules - the heart of the motor drive
The three major variable frequency designs used in drives are pulse-width modulation (PWM), current source inverter and voltage source inverter. The PWM technique is the most common. It requires switching the motor drive’s inverter power devices – transistors or insulated-gate bipolar transistors (IGBTs) – on and off many times, to generate the proper root-mean-square (RMS) voltage levels. Controlling and varying the width of the pulses is how PWM varies the output frequency and voltage.
In other words, an IGBT power module functions as an electronic switch where packaged power semiconductors are switching to reach a perfect sinus curve to match the application specifications. That makes the choice of power semiconductors and the design of the power module a core discipline in controlling speed and reaching the highest possible energy efficiency of the individual drive.
Downloads
Type | Name | Language | Valid for | Updated | Download | File type |
---|
Related products
Coming soon...
Coming soon...
Related solutions
-
if (isSmallPicture) {
; } else if (isBigColumns) { } else { }Industrial power electronicsHow do customized power modules from Danfoss optimize power management, increase quality and strengthen productivity in power conversion systems? World leader in power electronics.
Contact us
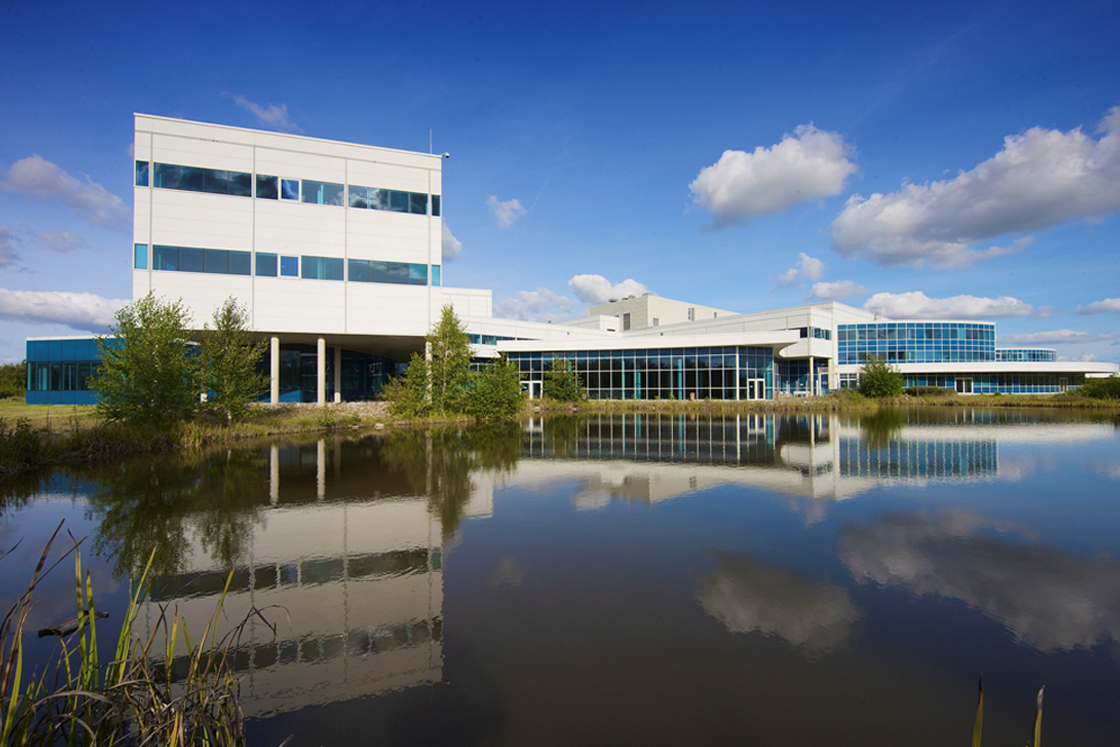
Danfoss Silicon Power is a globally active manufacturer of customized IGBT power modules, MOSFET power modules, SiC modules and power stacks. We promise that each product is individually designed to meet your exact requirements.
Learn more about how Danfoss Silicon Power works to optimize electrification, together with automotive, renewables and industrial manufacturers.