Achieving energy efficient operation while preventing liquid from damaging your compressors is a key consideration when designing refrigeration systems. The ideal requirement is to achieve the optimal balance between protecting your compressors and getting maximum refrigeration capacity from your evaporator. Danfoss has pioneered two control algorithms that help you achieve this balance.
The Minimum Stable Superheat (MSS) algorithm has been an important part of the Danfoss ADAP-KOOL® offering for years and is still the ideal choice for adaptive evaporator control for dry expansion. Now Danfoss introduces the next generation: Adaptive Liquid Control (ALC).
Wide safety margins can decrease system performance
Many retail refrigeration systems are designed to run with high fixed superheat as a safety measure to avoid damage to the compressors. This is an understandable precaution, as refrigeration system failure is costly, leading to downtime and customer inconvenience. However, setting too wide a safety margin for superheating results in poor system performance and high energy consumption. The evaporators are not utilized fully, and this results in less efficient refrigeration and increased energy consumption. Adaptive evaporator control, by contrast, optimizes system performance and energy consumption. Danfoss offers two different adaptive control algorithms, but before we look at them in detail, let us briefly recap what happens in the evaporator.
What happens in the evaporator?
Liquid refrigerant is injected into evaporators where it evaporates, absorbing heat from the environment in the process. Initially, most of the refrigerant is still in its liquid state, but as the evaporation progresses, the gas (vapor) to liquid ratio increases. The gas takes up more room than the liquid, increasing the velocity of the refrigerant, and the remaining drops of liquid are whirled around in the gas. If the rate of refrigerant injected is adequately controlled, all liquid has evaporated before reaching the end of the evaporator, leaving superheated gas only.
To better understand the different control strategies, let us have a look inside the evaporator. If we imagine the evaporator being a long pipe with refrigerant being injected from the left (see figure 1), the refrigerant starts boiling at the very beginning. If there is still refrigerant present in liquid form (until the dry-out point), the superheat can be measured to zero. In the part of the evaporator where there is a mixture of liquid drops and refrigerant gas (referred to as the mist flow area), the temperature of the gas is very unstable. As soon as all liquid drops have evaporated, and only gas exists, the temperature signal becomes stable again, and the temperature of the gas increases. By measuring the difference between the refrigerant temperature at the inlet of the evaporator (typically the evaporating pressure converted to temperature) and the temperature measured at the outlet of the evaporator, it is possible to control the amount of injected refrigerant. This temperature difference is normally expressed as superheat.
Since the temperature signal of the refrigerant gas in the mist flow area is very unstable and difficult to control, injection is commonly controlled by setting a fixed (stable) superheat reference high enough to ensure that only refrigerant gas is leaving the evaporator, thereby protecting the compressor against liquid slugging.
Fixed superheat control
Conventionally, superheat has been controlled by setting a fixed reference of typically 6 to 12 Kelvin. In real-world applications, the superheat setting depends on the type of evaporator as well as the load and running conditions, meaning that a higher superheat reference is needed at high load conditions compared to partial load conditions. To protect the compressors, a high fixed superheat reference is set for worst case conditions, with the result that evaporator efficiency is poor in partial load conditions.
Minimum Stable Superheat control
The temperature at the borderline between the unstable and stable superheat signal is called Minimum Stable Signal or Minimum Stable Superheat (MSS). This is the point at which all refrigerant has changed into the gas phase, and it is the point where the best trade-off between optimal efficiency and robust operation is obtained. From this point onwards, there is no longer any risk of damage to the compressors, as the refrigerant is in its gas phase. To optimize refrigeration system performance, refrigerant injection must be carefully controlled so that the evaporator is filled as much as possible without any risk of liquid returning to the compressors. Optimum superheat contributes to the best possible performance
for the system and the highest possible evaporator capacity. Controlling the injection valve to keep the optimum superheat is, therefore, a crucial consideration in designing, installing, and operating refrigeration systems. If operating conditions were always the same, defining the optimum superheat would not be a major challenge. In the real world, however, different types of evaporators, operating conditions, and load variations result in changes to the optimum superheat. This means that you cannot rely on a fixed superheat setting, as you will either operate with poor evaporator utilization or risk damaging your compressors due to liquid slugging. To ensure optimal operation and safeguard your system, an adaptive control method should be used.
The Minimum Stable Superheat algorithm: a proven technology invented by Danfoss
The Minimum Stable Superheat (MSS) algorithm is part of the ADAP-KOOL® offering from Danfoss and was introduced in 1987. Optimized to handle refrigerant injection, it is still the most effective method for adaptive evaporator control for dry expansion. The MSS algorithm controls the injection valve in all load conditions, enabling the system to operate at a low superheat down to 3 Kelvin and continuously adapts to condition changes. With MSS, the utilization of the evaporator surface is maximized while ensuring that no liquid exits the evaporator. The MSS algorithm in combination with suction pressure optimization delivers maximum system efficiency. When the refrigeration system is started, the MSS algorithm reduces the superheat from a reference setpoint until it measures instability in the signal by controlling the refrigerant injection (see fig. 2). The superheat reference is then gradually increased until the signal becomes stable again, and then periodically reduced again until instability reappears. This procedure is carried out continuously, and control parameters are adjusted according to actual load conditions and evaporator dynamic. MSS provides several benefits. Regardless of load, changes in ambient temperature during day/night, the use of night curtains, or seasonal differences, MSS always ensures minimum energy consumption and stable case temperatures, often resulting in energy savings of 10% or more when compared to non-adaptive control methods such as fixed superheat set-point or systems with mechanical thermostatic expansion valves. MSS ensures that all liquid has evaporated before reaching the end of the evaporator. This allows the system to optimize the suction pressure to the highest possible level while keeping even a fully loaded supermarket display case at the desired temperature. In summary, significant energy savings can be realized through the use of adaptive superheat control of evaporators. Across the world, thousands of retailers use the MSS algorithm in their refrigeration
systems, benefitting from energy savings and optimum food safety.
How to obtain the highest evaporator efficiency
The highest efficiency of an evaporator is realized when the dry-out point can be constantly controlled to be located correctly at the end of the evaporator, ensuring annular flow in the main part of the evaporator. Unfortunately, this is impossible in dry expansion systems since droplets of refrigerant will leave the evaporator, ending up at the compressor and resulting in high risk of compressor damage. If the system is designed so that the compressors are not exposed to liquid, e.g. using a suction accumulator and pump work to bring excessive refrigerant back to the receiver, the best strategy is to control the dry-out point of the refrigerant as close to the end of the evaporator as possible. If the liquid is just flooded through the evaporator, ending up in the suction accumulator, this would not increase the capacity of the evaporator. On the contrary, it would just cause extra energy to be used to circulate a larger amount of liquid. Also, a bigger accumulator would be needed to protect the compressors against liquid slugging.
Adaptive Liquid Control (ALC): controlling superheat as close to zero as possible Despite its age, the MSS algorithm is still exceptional in terms of precision, stability, reliability, and efficiency. Danfoss, however, has now developed its adaptive evaporator control offering even further, introducing the Adaptive Liquid Control (ALC) algorithm that allows even better evaporator utilization with highly precise liquid control. With the ALC algorithm, you can take refrigeration system performance to the next level.
What is superheat in refrigeration?
In refrigeration, superheat (SH) is the temperature difference between a refrigerant gas above the saturation temperature (boiling point) and its saturation temperature. For every Kelvin the superheat can be decreased, there is an equal potential to increase the evaporating temperature. For every Kelvin the evaporating temperature is increased, 2-3% energy can be saved in a refrigeration system.
Higher suction pressure reduces compressor energy consumption
One of the cornerstones of the MSS algorithm is that it safeguards the compressors by ensuring that no liquid exits the evaporator. This is the optimal solution when using dry expansion evaporators. For systems with a suction accumulator, however, where it is not a requirement that no droplets leave the evaporator, it is possible to further enhance the utilization of the evaporator, reduce superheat and achieve optimal energy efficiency. The ALC algorithm typically used in transcritical CO2 systems with Liquid Ejectors injects greater amounts of refrigerant into the evaporator, fully utilizing the entire surface. Increasing the amount of refrigerant increases the evaporation temperature, bringing the superheat very close to zero. As stated above, every degree Kelvin of increase in evaporation temperature makes it possible to save 2-3% energy in a refrigeration system. With ALC, the refrigerant leaving the evaporator has not been superheated.
The suction pressure is, therefore, higher, reducing the load on the compressors. With an increase in evaporation temperature of up to 5 Kelvin compared to adaptive MSS systems, and even more when compared to non-adaptive solutions, significant energy savings can be achieved. The trade-off is that the refrigerant leaving the evaporator is part liquid. The Danfoss ALC algorithm, however, is capable of controlling the evaporation process very precisely, keeping the amount of liquid low. This means that the suction accumulator installed to collect these droplets of liquid can be small, lowering the first cost and saving installation space. By adding a Danfoss Liquid Ejector, you can drain away the liquid from the suction accumulator without consuming additional energy. For more information on the Danfoss ejector offering, see our article The Danfoss ejector range for CO2 refrigeration: design, applications, and benefits, or visit multiejector.danfoss.com
Four different control strategies for refrigerant injection in evaporators
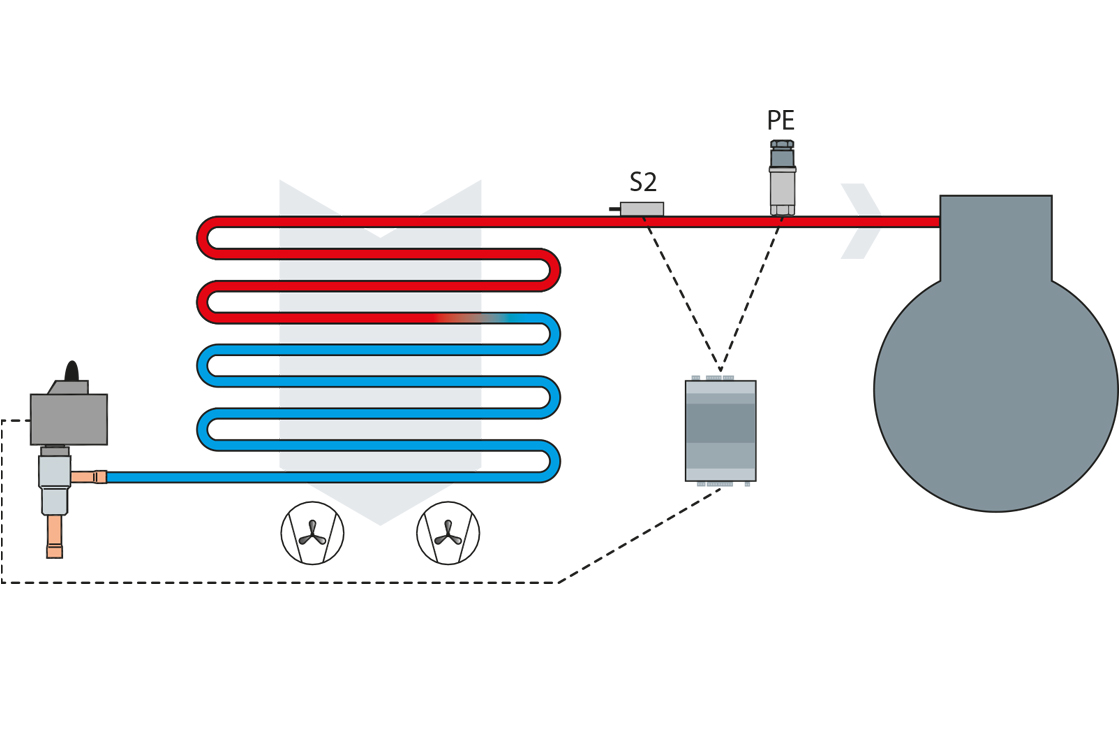
1. Fixed superheat control
To ensure robust control without harming the compressors, a high superheat setting for the worst case
conditions are required, compromising full utilization of evaporator capacity.
Fixed superheat control in dry expansion systems. Typically seen in competitor systems and systems
with thermostatic expansion valves. Increased energy consumption compared to MSS.
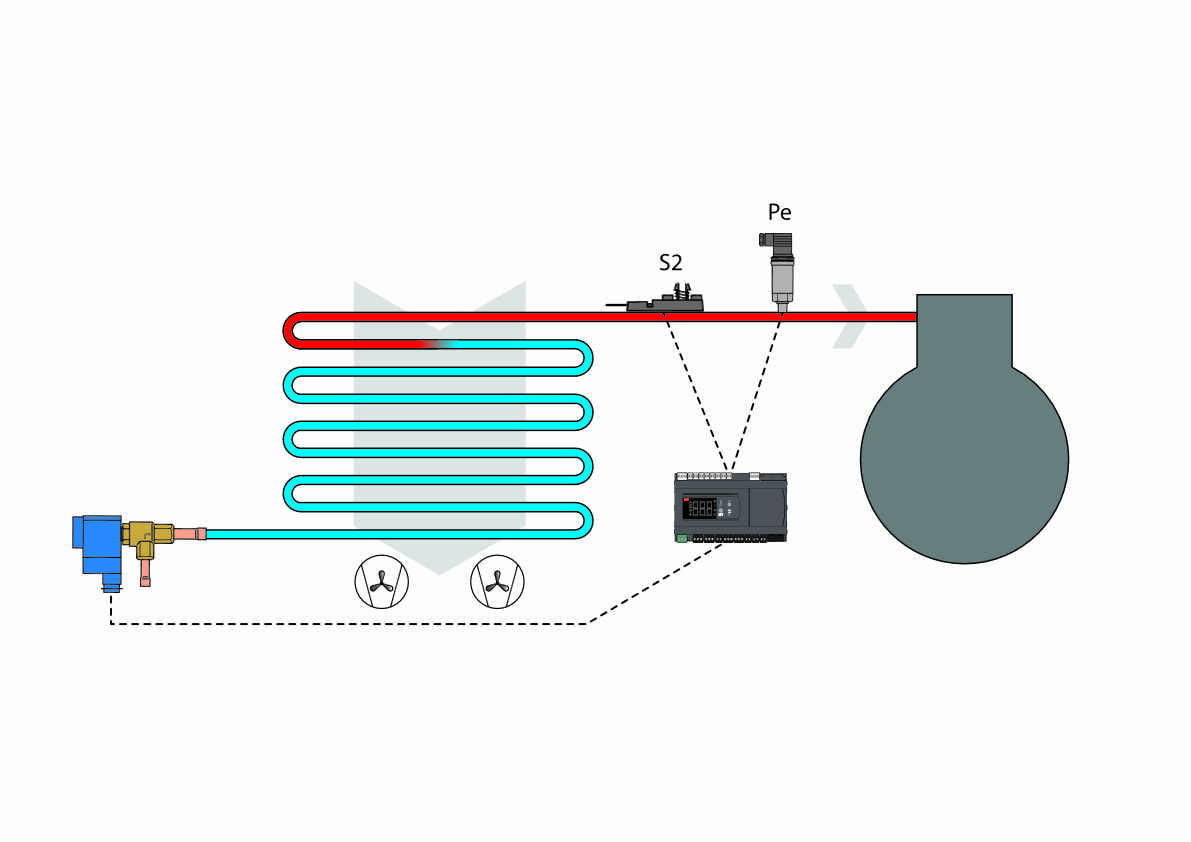
2. Danfoss adaptive MSS control
With MSS, utilization of the evaporator surface is maximized while ensuring that no liquid exits the evaporator. The MSS algorithm in combination with suction pressure optimization delivers maximum system efficiency in systems with dry expansion. Proven Danfoss MSS control driving more than 1.5 million AKV valves since introduction. Provides up to 10% energy saving compared to fixed superheat control.
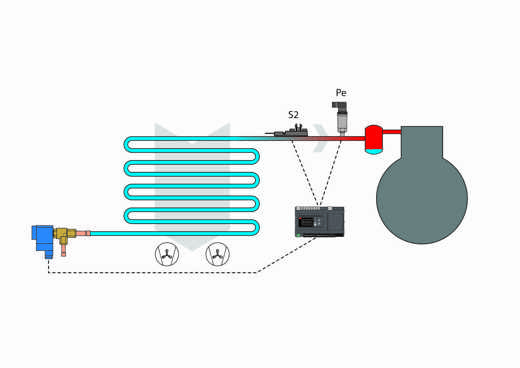
3. Danfoss Adaptive Liquid Control (ALC)
The ALC algorithm typically used in transcritical CO2 systems with a suction accumulator and Liquid Ejectors injects greater amounts of refrigerant in the evaporator, fully utilizing the entire surface. Increasing the amount of the refrigerant increases the evaporation temperature, bringing the superheat very close to zero. The new Danfoss ALC algorithm provides the highest
utilization of evaporator capacity, enabling up to 5 Kelvin higher suction pressure compared to MS control and even twice as much compared to systems with fixed superheat.

4. Flooded evaporator control
Flooded evaporator control is seen in competitor systems where the fixed superheat setting is set close to zero. When superheat is measured to zero, there is no control over the flow rate. A proper mechanism is therefore required to switch between flooding and dry expansion. In competitor systems with flooded evaporator control, a bigger suction accumulator is required to contain the excess liquid and to protect the compressors while no additional capacity increase is seen in the evaporators.
ALC: the best control strategy for CO2 systems with the suction accumulator and ejectors By controlling the superheat close to zero and fully utilizing the evaporator, you get optimum evaporation effect from the refrigerant. This allows you to minimize the amount of liquid circulated in the system. This Danfoss solution for managing liquid in transcritical CO2 refrigeration applications is only possible thanks to enhanced versions of case controls, pack controls, and system managers, together with the Liquid Ejector. This solution is called CO2 Adaptive Liquid Management (CALM) and it represents a major step forward in refrigerant management. The brain of the adaptive system is the self-learning controller. For more information on Danfoss AK-PC and AK-CC controllers used in transcritical CO2 systems, please see our article Intelligent and adaptive control in transcritical CO2 refrigeration.
Conclusion
Over the decades, data from thousands of installations have proved the superiority of adaptive superheat control. There are several ways of achieving optimal superheat in CO2 refrigeration systems – the evaporator control strategy you select depends on a number of factors. Danfoss offers a choice of adaptive, intelligent and proven control methods that deliver operational savings and high system reliability. The proven MSS algorithm is the best choice for adaptive evaporator control for dry expansion where liquid in the suction line is not desired. The new ALC algorithm is the best choice for systems with a suction accumulator and a Liquid Ejector, giving you the option of utilizing the evaporator optimally. No matter which solution you select, there are significant energy savings to be realized compared to fixed superheat systems. For more information, please contact your local Danfoss sales office, or visit smartstore.danfoss.com