The brewery viewed the revamp of its 27-year-old industrial refrigeration system as an opportunity to simplify operations, improve safety, and reduce CO₂ emissions. However, they faced a challenge. Their existing facility remained essential for daily operations, so shutting down for weeks or months was not an option.
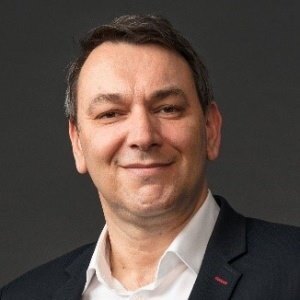
Old technology comes with risk, we cannot afford. We trust Danfoss to provide the innovative, high-quality solutions our clients require.
The challenge: retrofitting and operating at the same time
Under these conditions, the brewery turned to the design expertise of their trusted, local contractor, Frigotehnica Industrial, part of VINCI Energies. Firstly, the brewery was particularly concerned about the operational safety of their existing system. Secondly, cumbersome ammonia control station valves required frequent servicing. Finally, the pipe network, originally built in 1997 and partially extended in 2007, further complicated maintenance efforts.
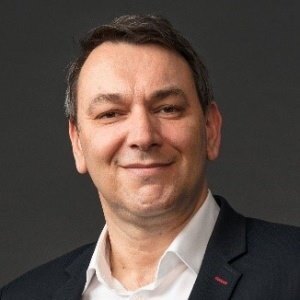
"If you need to move quickly and cannot afford mistakes or delays, ICF valve stations are essential. We are seeing simpler installations, fewer errors, and lower maintenance costs. Clients appreciate the reduced space requirements and the operational savings from carbon capture."
The solution: ICF valve stations
To address the unique project situation, Frigotehnica's design experts proposed a straightforward and efficient solution— new Danfoss ICF valve stations. To address these needs, Frigotehnica installed the latest technology from Danfoss — ICF valve stations — known for enabling fast installations and operational simplicity. With this extensive upgrade, the client was able to leverage the latest technologies, extend its cooling capacity, and improve its CO₂ footprint.
The outcome: a trusted solution and implementation
The brewery's innovative and eco-friendly application has been well-received by employees. The redesigned system includes a 120 ICF valve station and reduces soldering sections from eight to two. Additionally, there are 73% fewer welding points, down from 1,164 to 308. Installation was carried out in cold conditions while the unit remained operational, causing minimal disruption to daily activities. Only one major stoppage of the refrigeration plant was necessary, allowing the brewery's to maintain normal business operations. The result was 30% less downtime for the brewery retrofit.
Related products
-
if (isSmallPicture) {
; } else if (isBigColumns) { } else { }ICF Flexline™ stainless steel valve stationThe ICF SS valve station offer savings in time, space and money compared to control solutions using conventional components.
-
if (isSmallPicture) {
; } else if (isBigColumns) { } else { }ICF Flexline™ valve stationUnmatched freedom is the keyword of ICF Flexline™ valve stations. As part of the Flexline™ platform, these valve stations are based on a unique modular concept.