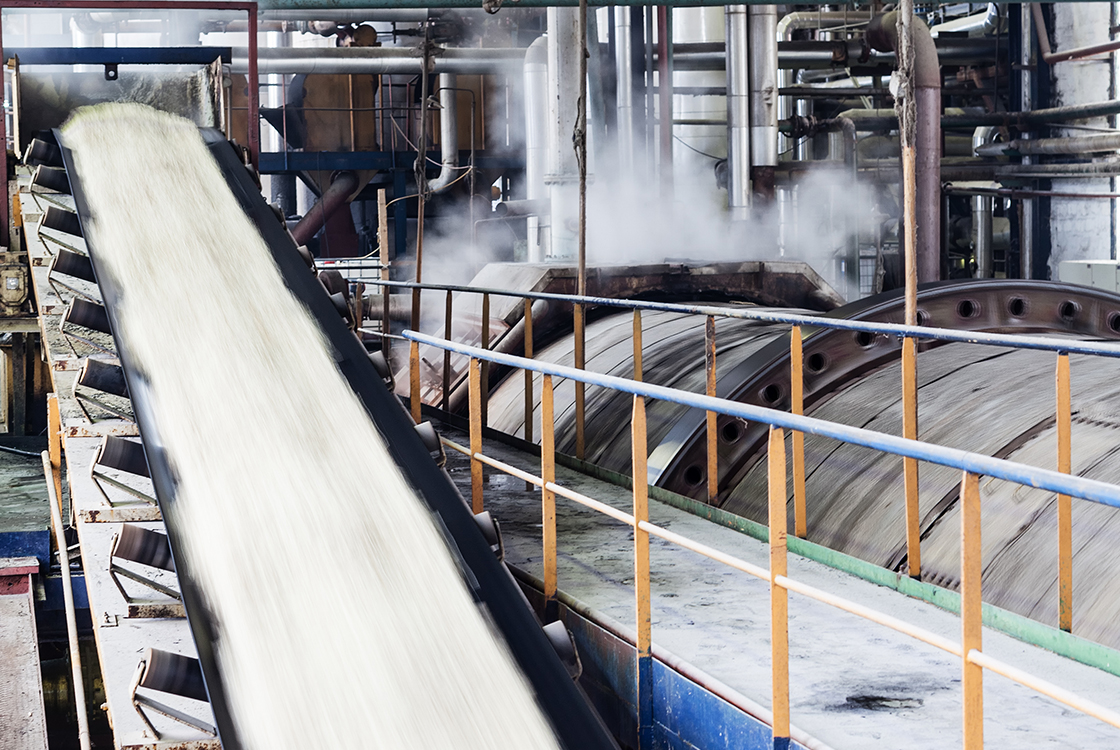
Because sugar cane must be processed within a day of harvest, high throughput is essential. Efficiency and productivity are key factors in sugar production centrifuges.
The centrifuges used in the production of sugar are designed for processing massecuite, a mixture of sugar crystals and molasses, which is produced by the crystallization phase of sugar refining. The centrifugal spins the massecuite in a perforated basket at speeds of up to 1200 rpm.
A feeding system delivers the massecuite to the basket. The charging speed can be varied to suit the properties of different massecuites.
When the massecuite valve has closed, the basket accelerates to its spinning speed. Then the spinning phase is followed by braking, at the end of which the closing hood opens and the discharging cycle begins.
The discharged sugar exits through the product outlet of the housing, which can be equipped with an automatic cleaning facility, and is led to downstream conveyors.
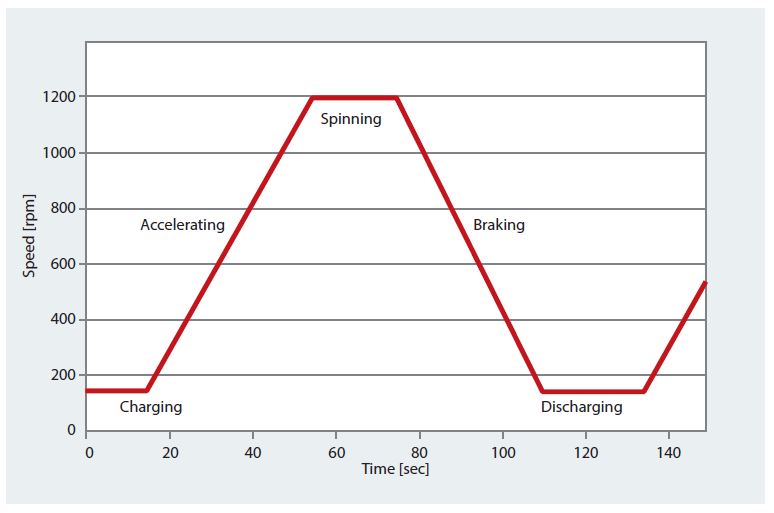
Energy usage in centrifuges
Typical centrifuges can process 20 to 28 loads per hour. In order to keep this cycle time the drive system must be able to maintain reliable constant torque control during acceleration and spinning.
Energy savings are realized when the braking energy from the spinning centrifuge, which turns the motor into a generator, is recovered and transferred via the drive to an adjacent centrifuge or back to the grid. This way 70-90 % of the consumed energy per cycle can be recovered during the braking of the centrifuges.
Centrifuges in sugar refining are commonly driven by AC motors rated between 90 and 630 kW and often with high torque motors to save time and improve productivity.
A loaded centrifuge typically presents a moment of inertia of around 2500 kgm2, thus a rotational kinetic energy of 19,700 kJ is needed to decelerate in 35 sec.
Applications like this require a frequency converter with a high starting torque and a constant torque flux controller to allow the fast acceleration of the centrifuges and to reduce cycle times while ensuring a uniform process and robustness against load shifts due to material changing in the basket.