SPAIN: Through innovation and planning, Volkswagen aims to continuously reduce energy consumption and the associated CO2 emissions at its factory sites. One good example is in air conditioning. The demands placed on the air conditioning of buildings increase steadily. Axial fans can make a significant contribution to combining technical requirements with sustainable building design.
Therefore in 2018, two production sites in two separate countries installed air handling units with new technology and highly efficient axial fans controlled by VLT® HVAC Drive FC 102 : Porsche in Stuttgart/Zuffenhausen, Germany and Volkswagen Navarra in Pamplona, Spain. The upgrade at Volkswagen Navarra resulted in impressive 20% energy savings in AHU operation.
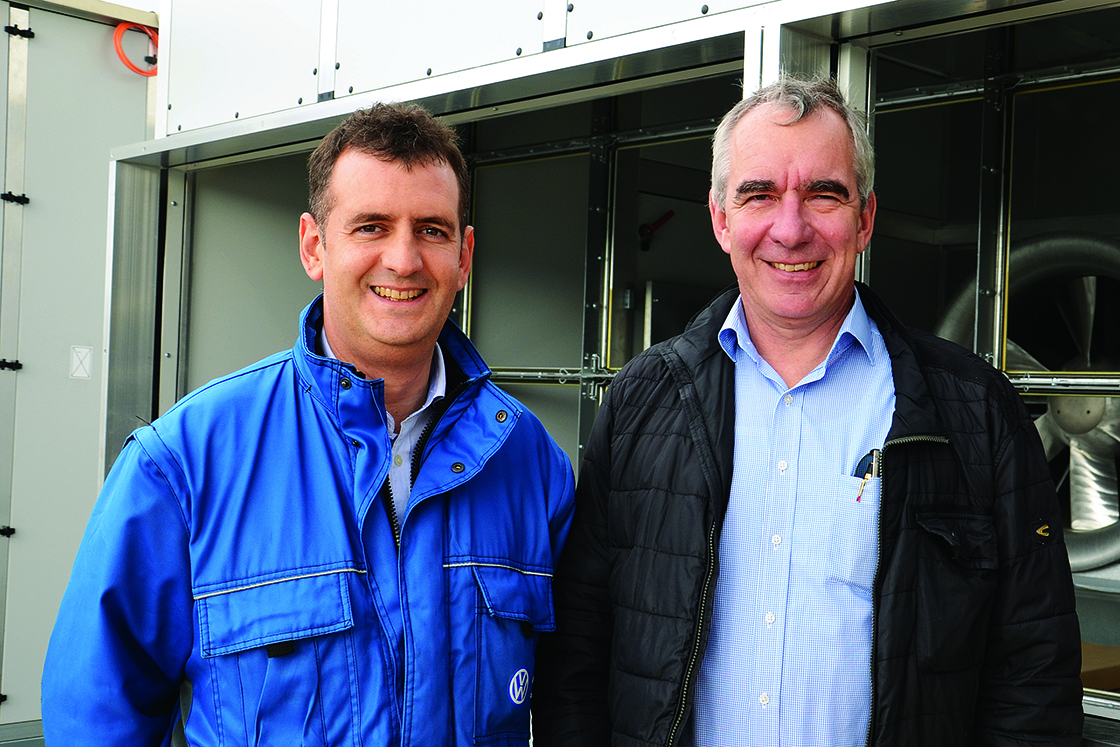
Discover how Volkswagen achieved 20% energy savings in AHU operation
The new trend-setting AHU technology installed at Volkswagen fully met all expectations of Asier Matorell, Factory Planning Manager, Volkswagen Navarra (left) and Axel Rossmannek, Head of Supply Planning, Volkswagen Wolfsburg.
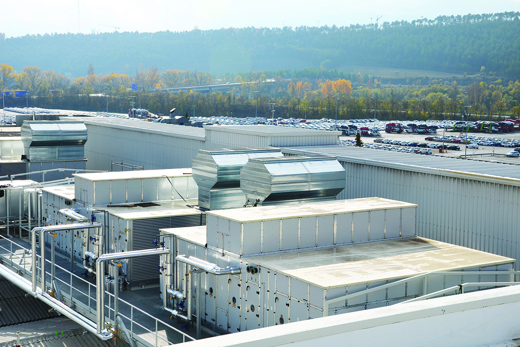
Pioneering sustainable ventilation technology
The ventilation had to be completely renewed for one of the largest production buildings at the factory. Higher air volumes were needed and the space available for the installation of the equipment was insufficient. Therefore, a new installation location for the AHUs had to be found on the roof. The large 80,000 m³/h units were placed on a steel platform on the connection between two buildings. In addition to saving energy, the criteria unit size, weight saving and noise reduction were therefore also key requirements.
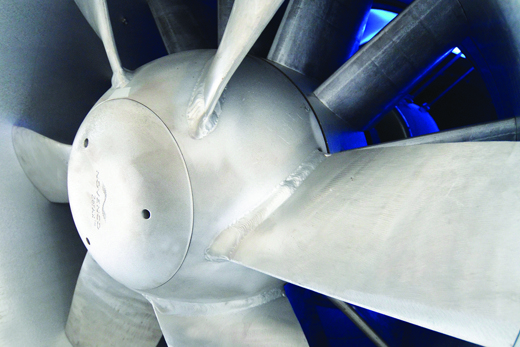
Intelligent interaction
The high demands could only be met with the new generation of air handling units, optimally utilizing the highly efficient axial fans from NOVENCO, with VLT® HVAC Drive FC 102. Performance exceeded all expectations. The ZerAx® axial fans currently represent the world’s leading fan technology with fan efficiencies of up to 92%. NOVENCO, however, went one step further by optimizing the ZerAx® even more for use in the air handling units. Here the Danfoss EC+ Concept was an essential contributor to the energy savings.
The key phrase here is intelligent interaction of the system components. This interaction is embodied in the term EC+ and is developed in cooperation between Danfoss and NOVENCO. Only the optimal interaction of the system components fan - motor - electronics – diffuser, makes the full potential of a highly efficient fan realizable.

What is the Danfoss EC+ Concept?
When building an HVAC system, to get the highest performance and system efficiency, the individual components – motor, drive and fan – need to be flexible and broadly compatible with each other. For instance, if you specify a high-efficiency motor that is only compatible with lower efficiency fans, the overall system efficiency would suffer and would not reflect the high performance – and investment – in the individual components.
Danfoss Drives’ EC+ concept allows ventilation system designers to combine a VLT® HVAC Drive with the most efficient fan and permanent magnet motor.
Advantages of the EC+ concept:
- Free choice of motor technology: PM, asynchronous or synchronous reluctance with the same AC drive
- Device installation and operation remain unchanged
- Manufacturer independence in the choice of all components
- Superior system efficiency thanks to a combination of individual components with optimum efficiency
- Retrofitting of existing systems is possible
- Wide range of rated powers for standard, PM and synchronous reluctance motors
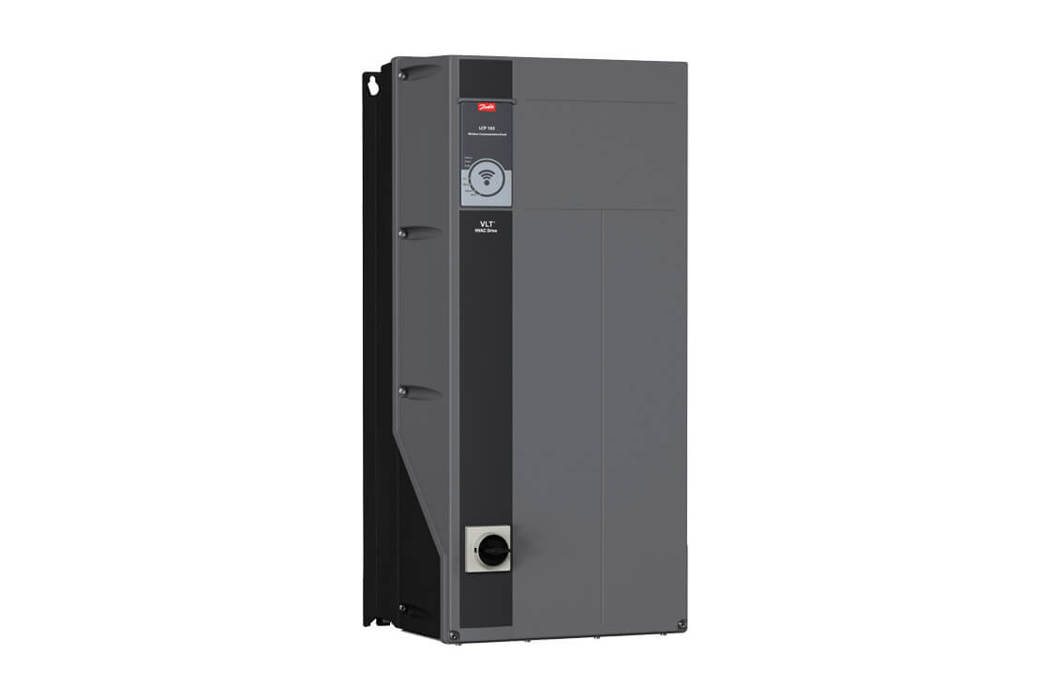
Products
-
if (isSmallPicture) {
; } else if (isBigColumns) { } else { }VLT® Refrigeration Drive FC 103FC103 is dedicated to controlling compressors, pumps and fans for significant energy savings in refrigeration plants.
-
if (isSmallPicture) {
; } else if (isBigColumns) { } else { }VACON® 100 FLOWDedicated functionality that improves flow control and saves energy in industrial pump and fan applications.
-
if (isSmallPicture) {
; } else if (isBigColumns) { } else { }DrivePro® Service ContractDrivePro® Service Contract begins where the warranty leaves off. Service Contract coverage periods of 1 to 4 years are available for many Danfoss Drives products nearing the end of the standard warranty or extended warranty.
-
if (isSmallPicture) {
; } else if (isBigColumns) { } else { }DrivePro® ExchangeMaintain uptime with a fast alternative to repair when there is no time to waste. If an AC drive fails, the DrivePro® Exchange service can quickly exchange any drive to ensure as little production delay as possible.
-
if (isSmallPicture) {
; } else if (isBigColumns) { } else { }DrivePro® RetrofitThe DrivePro® Retrofit service offers an onsite audit to plan for the replacement of your AC drive well in advance. Be prepared for the end of your AC drive’s life cycle and ensure minimal unexpected downtime.
Read more about Danfoss HVAC solutions
-
if (isSmallPicture) {
; } else if (isBigColumns) { } else { }Condition monitoring of HVAC/R systemsIn air flow and indoor air quality-related applications, condition monitoring functionality improves system uptime and competitiveness by preventing issues before they occur.
-
if (isSmallPicture) {
; } else if (isBigColumns) { } else { }Drives for fansGet more out of your air handling units, using fan control that gives you easy air filter monitoring and built-in fire safety features.
-
if (isSmallPicture) {
; } else if (isBigColumns) { } else { }Drives for fans in commercial buildingsWith user-friendly interfaces, distributed intelligence and reduced power consumption, Danfoss AC drives optimize the performance of fans.
More AHU case studies
-
if (isSmallPicture) {
; } else if (isBigColumns) { } else { }How did this smart factory reach carbon-neutral?POLAND: The new Danfoss production hall in Grodzisk Mazowiecki has reached carbon-neutrality, thanks to full electrification, energy-saving solutions such as Danfoss drives, and energy from renewable sources.
-
if (isSmallPicture) {
; } else if (isBigColumns) { } else { }Drives secure fresh air inside South America’s tallest buildingA huge number of Danfoss drives secure comfortable temperatures and cut down energy use inside Chile’s famous Costanera Center.
-
if (isSmallPicture) {
; } else if (isBigColumns) { } else { }The Verdict: Courthouse retrofit provides comfort, efficiency for occupants as well as a path to decarbonizationWhen it began ‘raining’ in the Towson Court House a leaky roof was assumed to be the culprit, according to project leaders at the Maryland Department of General Services (DGS), the state’s property manager. For Courtney League, DGS’ Chief of the Facilities Engineering Division, and Harry Hughes, Project Manager for Design, Construction and Energy, the truth turned out to be much stranger.
-
if (isSmallPicture) {
; } else if (isBigColumns) { } else { }EC+ Concept drives optimal air conditioning at Volkswagen’s Navarra factoryHighly efficient axial fans controlled by VLT® HVAC Drive FC 102 at Volkswagen Navarra, Spain, delivered 20% energy savings in AHU operation.
-
if (isSmallPicture) {
; } else if (isBigColumns) { } else { }Healthcare Data Center Takes Control of Uptime and Energy with Danfoss VLT® DrivesThe data center industry has standards to define the level of uptime required for a given class of application and the infrastructure needed to maintain that level. The standard being applied to medical data centers — known as the Uptime Institute’s Tier III standard — calls for 99.982 percent uptime, which translates to no more than 1.6 hours of downtime per year. This standard requires an uninterruptible power supply (UPS) system that can handle a power outage of at least 72 hours, and Danfoss was selected to help meet this standard.