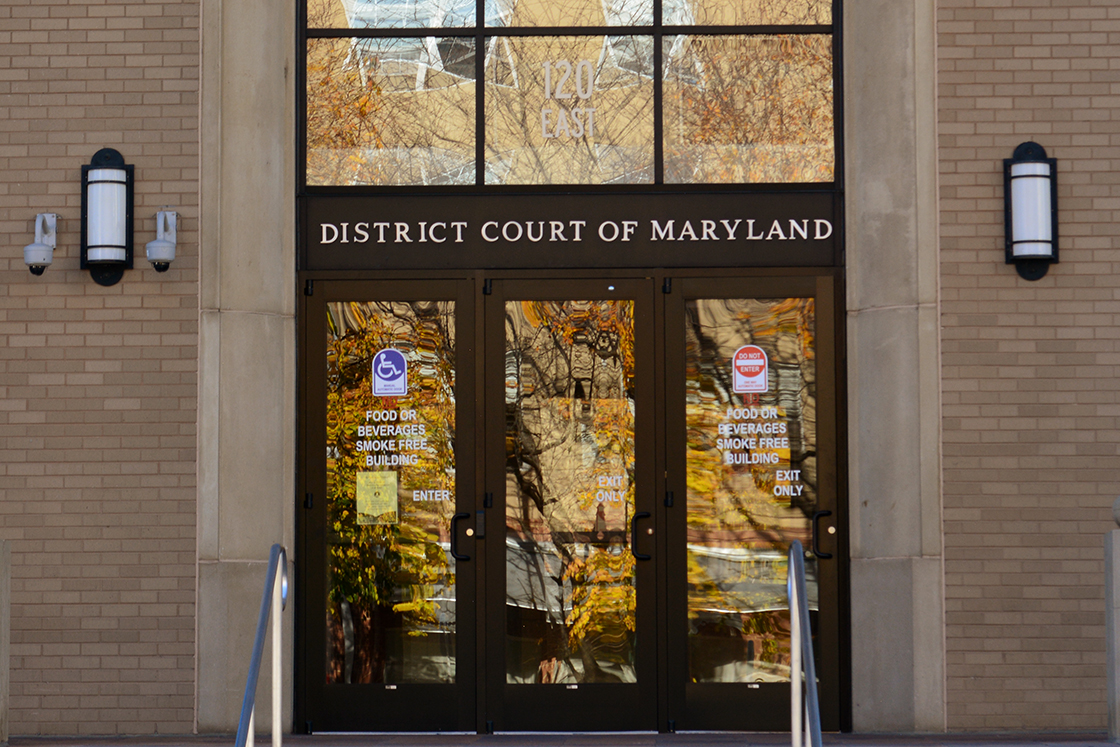
When it began ‘raining’ in the Towson Court House a leaky roof was assumed to be the culprit, according to project leaders at the Maryland Department of General Services (DGS), the state’s property manager. For Courtney League, DGS’ Chief of the Facilities Engineering Division, and Harry Hughes, Project Manager for Design, Construction and Energy, the truth turned out to be much stranger.
“There was such negative air pressure in the building from the HVAC system that outside water was literally being sucked in through the perimeter walls and joints,” said League. “Ceiling tiles were visibly billowing and warping even though the roof itself was fine.” All of this hinted at the ongoing internal climate battle the building team faced. With outside air constantly flowing into the building, it became impossible to maintain temperatures at comfortable levels; residents consistently complained about pockets of hot and cold air, as well as humidity and dampness throughout the building.
At first, DGS took a traditional approach to fixing the building, focusing on individual pieces of equipment like chillers, pumps and air handlers. DGS’ maintenance team replaced air handling units, many of which were several decades old. When that didn’t solve the comfort issues, the DGS engineering team invited Jae Chon, Director of Strategic Markets at Chesapeake Systems, a Maryland-based HVAC consultant and equipment distributor, to evaluate the building system. Chon soon discovered it wasn’t a few pieces of old and faulty equipment; the entire HVAC system was completely unbalanced - dampers blowing into empty ceiling spaces, vital equipment plated up, control switches inexplicably disconnected, tarps hidden in crawl spaces to redirect water and more. Each “fix” to a seemingly isolated part of the system was, in fact, impacting the entire building. Chon, League and Hughes determined that simply replacing the existing equipment would not heal this sick building. A more holistic approach was necessary, one in which each piece of equipment was viewed as a node in a larger, synergistic system.
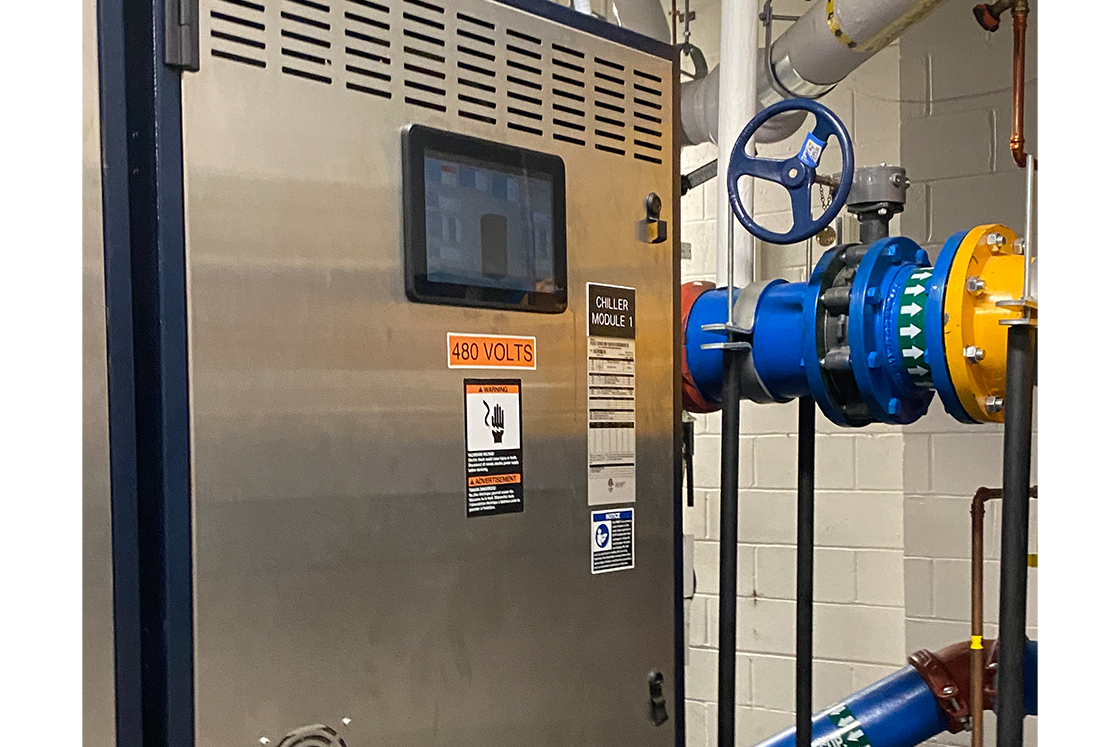
The Synchronized Hydronic Loop
The challenges DGS faced were a perfect match for the concept Danfoss and its partners were developing called the Synchronized Hydronic Loop, which considers how all of the seemingly isolated parts of a hydronic HVAC system work together synergistically.
A building’s hydronic HVAC system is comprised of chillers, boilers, pumps, variable frequency drives (VFDs), air handling units (AHUs) and valves that create a loop through which water is circulated to control the building’s temperature and its occupants’ comfort. In this loop, each component is a node that has an effect not just on the one next to it but on every other one, regardless of how far they are from each other. In fact, the nodes furthest from each other may impact each other the most. Variable speed pumps, for example, can surrender much of their part-load efficiency if the wrong balancing valves are installed at the terminal units. Too often systems are designed and components specified as though this loop is made of discrete nodes.
A system composed of synergistic components, on the other hand, enhances the efficiency of the entire loop. Pressure independent control valves (PICVs) installed at the AHUs tightly control the water temperature entering and exiting the unit’s coils, allowing the chiller’s variable speed compressors to work as efficiently as possible. VFDs on the pumps supply only as much water as is demanded to take advantage of part load conditions to save energy.
Investing in a synchronized hydronic loop made of synergistic components ultimately offers solutions to three common problems associated with conventional hydronic HVAC systems:
- Maintaining Occupant Comfort
- Achieving Design Efficiency in All Load Conditions
- Degradation of Efficiency Over Time
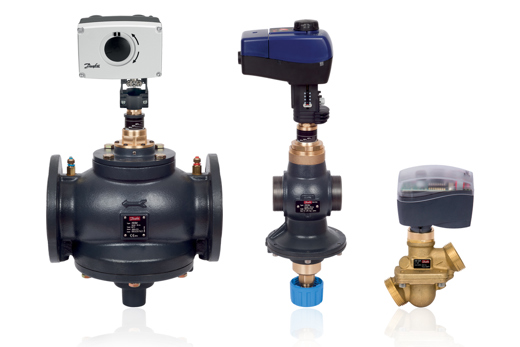
Out with the Old, In with the New
Drastic situations call for drastic measures: DGS ultimately made the decision to totally vacate the Towson Courthouse, relocating all of its occupants and operations to an alternate site. With the building vacant, DGS’ engineering team began the process of removing old equipment and planning for a new, holistic and state-of-the-art HVAC system that would achieve the dual goals of optimizing comfort for building residents and visitors; and, as mandated by the state of Maryland, increasing energy efficiency by at least 15%.
DGS turned to Jae Chon, Danfoss and their partners at Armstrong Fluid Technology and WaterFurnace for the equipment and expertise necessary to install a Synchronized Hydronic Loop in the Towson Courthouse. The system selected included the following pieces of equipment:
- (3) WaterFurnace 80-ton modular chillers, each with two Danfoss high-efficiency scroll compressors.
- (52) Danfoss pressure-independent control valves of various sizes.
- (4) Danfoss HVAC variable frequency drives installed on fan motors.
- (6) Armstrong Design Envelope Pumps with factory-mounted Danfoss VFDs.
The variable speed technology on the chillers, pumps and fan motors act in concert, automatically speeding up or slowing down to adapt to the comfort needs of the building while optimizing overall system performance and efficiency. The WaterFurnace modular chillers’ heat recovery capabilities added two other important benefits to the project:
- Simultaneous heating and cooling – The chillers have the ability to recover heat off the compressors producing hot water with up to a combined efficiency of 8 COP. Chiller modules that are not simultaneously producing chilled and hot water operate at lower condensing temperatures to increase cooling efficiencies even further. The chillers heat recovery capabilities can simultaneously provide heating and cooling to different parts of the building and increasing occupant comfort.
- Carbon reduction and electrification – While the chiller is producing chilled water, the system has the ability to recover as little or as much heat to dynamically meet the buildings comfort needs. This allows for the building to reduce natural gas consumption and carbon emissions by only running boilers during the peak heating months.
“We strategically selected the most innovative equipment we could possibly get to meet or exceed the twin goals of optimizing temperature control for building comfort and maximizing energy efficiency,” said Chon.
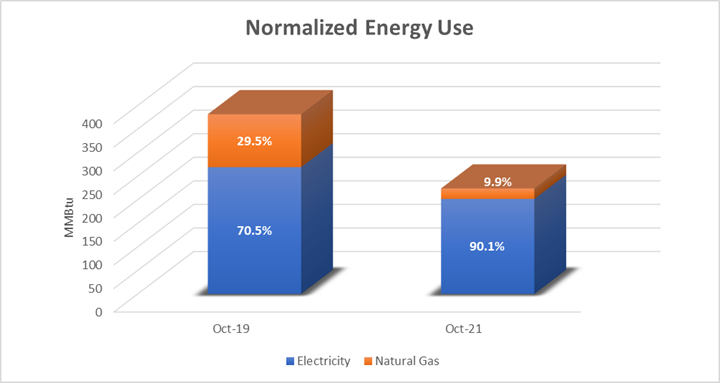
Positive Early Returns For Occupants and the Climate
Although final quarterly numbers aren’t in as of this writing, DGS is already receiving extremely positive returns in terms of energy usage, utility savings and comfort. According to data from the Maryland State Energy Database, through the first six months of operations the Towson District Courthouse is experiencing an average total monthly energy savings of 23% relative to its 2019 usage from the same months, a decrease entirely attributable to its new HVAC system since no other upgrades were made. That energy reduction equates to more than $2,000 in monthly utility bill savings. And, with the building now fully occupied, residents noticed the positive differences immediately—especially the district judge who was the senior official at the location.
“She sought me out immediately to say how comfortable the building was now, better than she ever experienced or expected,” said Hughes. “We heard great things from many of the people who had been working there for years, how they had never seen the building so comfortable. Everyone was very appreciative.”
Special compliments, DGS noted, related the new system’s heat recovery capabilities, which allow it to heat some rooms while cooling others simultaneously, optimizing comfort in every area of the large and diverse structure. Not only does this heat recovery feature contribute to enhanced occupant comfort, it offers significant climate benefits, as well. The building used 59% less natural gas in October and November of 2021 than it did in the same two months in 2019 and natural gas went from nearly 47% of total energy use to less than 32%. Decreasing natural gas’ share of overall energy use also had an outsized impact on that total: While monthly average energy use over the building’s first six months decreased by 23% versus 2019, total energy use was reduced by a staggering 55% in November 2021, the first month with significant heating needs. Those data are evidence of heat recovery’s potential to substantially decarbonize and reduce overall emissions even if a building does not convert to 100% electric operations.
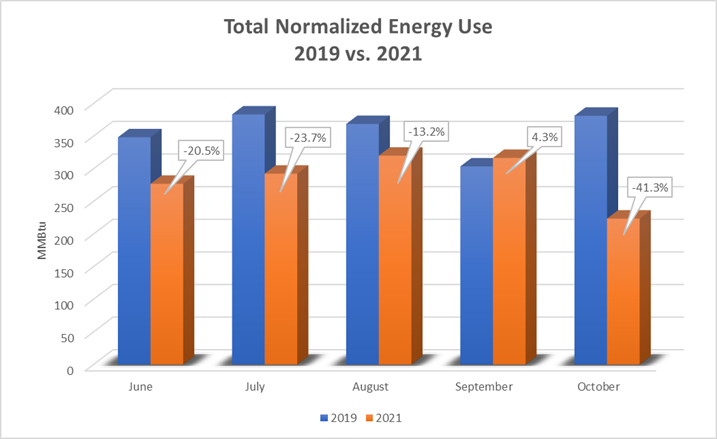
“The smoothest project in my 40- year career”
With such substantial changes made to building infrastructure, DGS assumed that there would be refinements needed over time, even as they allowed people to move back into their building as soon as possible, and informed them as such in order to manage expectations.
Nevertheless, there were tweaks to be made, and DGS gives the Chesapeake and Danfoss teams high marks for responsiveness, both during and after the main implementation process.
The highest marks, however, DGS reserves for the team’s efforts in the main project, which, although complicated by COVID-related delays, they rate as “exemplary.”
A.L. Merton, the prime contractor on this project, “went above and beyond to make every aspect of this job, down to the most insignificant details, like replacement of dirty ceiling tiles, work for our occupants’ satisfaction,” according to Hughes. “This was a total team effort between our contractors, vendors, Jae and our DGS support team. I’ve been involved in a lot of projects in my 40-year career, and I think that this was the smoothest and best coordinated I’ve ever seen to get the best possible results.”
“When faced with an issue of this magnitude, there is probably no better way to approach it then stepping back and looking at the problem as a whole, not just replacing a piece of equipment, but thinking through how to make the building most comfortable and most efficient for all stakeholders,” said Hughes. “That just makes a lot of sense.”