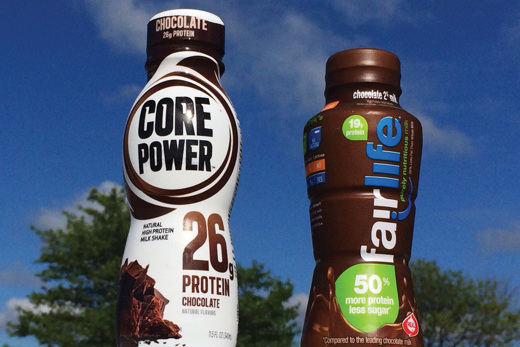
Fairlife has built a new dairy production facility in Coopersville, Michigan. The new site will begin production of a milk protein drink called Fairlife and Core Power.
Danfoss NAM has supplied a VLT® FlexConcept® solution for three packaging lines at the Coopersville facility. Each line uses approximately 60 pieces of the VLT® OneGearDrive® and the VLT® Decentral Drive FCD 302 respectively.
Everyone is a winner
To secure these packaging lines, Danfoss NAM utilized a Danfoss Food & Beverage PUSH / PULL strategy, providing savings to both the equipment builder Descon Conveyor Systems, and the end user Fairlife.
Savings in installation process
Jeff Philpott, Descon Conveyor Systems: “The VLT® Decentral Drive FCD 302 has saved Descon time and money, for we can utilize the I/O connection of the FCD 302 and reduce analogue I/O block. Node connectivity is very expensive. Any additional Ethernet switches and I/O blocks add so much more cost, more wiring and more time to install.”
“The additional digital and analogue I/O provided by Decentral Drives FCD 302 offers Descon and our customers the ability to add field sensors without adding major cost. Alternative suppliers did not support this feature”, explains Jeff Philpott, and elaborates on the cost savings achieved: “Descon is confident that we can deliver major savings for Fairlife in time, labour, and installation costs. With the FCD 302 decentral solution, costs are minimized for local electrical contractors.”
Streamlined hygienic design
Fairlife Maintenance Manager Robert Cunningham was highly impressed with the clean, hygienic design of the VLT® FlexConcept® solution: “The VLT® OneGearDrive® has no fan or bleeder valve, which is ideal for our dairy plant.”
Danfoss VLT® FlexConcept® offers a second advantage for Fairlife: the very limited number of spare parts required for the plant. Descon Conveyor Systems only required three VLT® OneGearDrive® variants and two Decentral Drives FCD 302 variants for all three bottling lines.
Many thanks for the excellent local support given to Descon Conveyor Systems by our sales partner Davis Controls. Davis was instrumental in securing this project order.