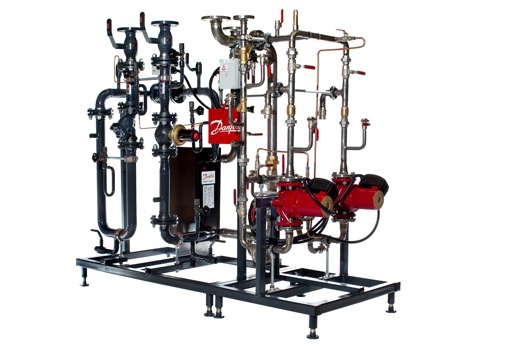
Quality and reliability are built-in to our custom engineered solutions...
At Danfoss, we develop, design & produce all major components for our custom energy transfer stations in-house. Our wide experience in designing and installing district energy systems spans over 80 years ensuring your solution will meet all applicable technical, user, safety, efficiency and installation requirements.
Avoid the hassle of building on-site solutions, while eliminating any additional consulting engineer investments to focus on what matters; optimized heat transfer & superior system control, performance, & efficiency.
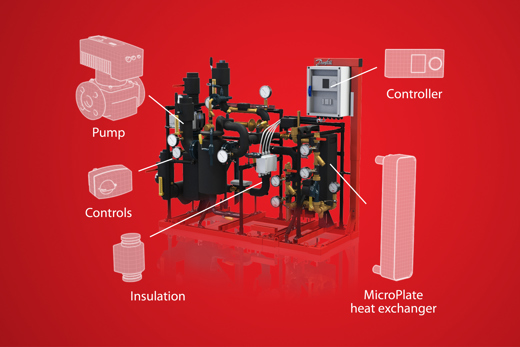
A complete solution delivered by one trusted and local supplier
Danfoss is bringing extensive energy transfer station expertise to the local North American market, by supplying USA factory designed and installed units, enabling us to uniquely ensure system uptime and performance, while also easily facilitating code compliance, efficiency optimization, startup and commissioning support assistance.
Danfoss utilizes a robust requirement collection process to tailor-fit the perfect solution for your situation. Pressure, differential pressure, temperature & flow are integrated & automatically controlled in all stations, allowing building occupants to always be comfortable.
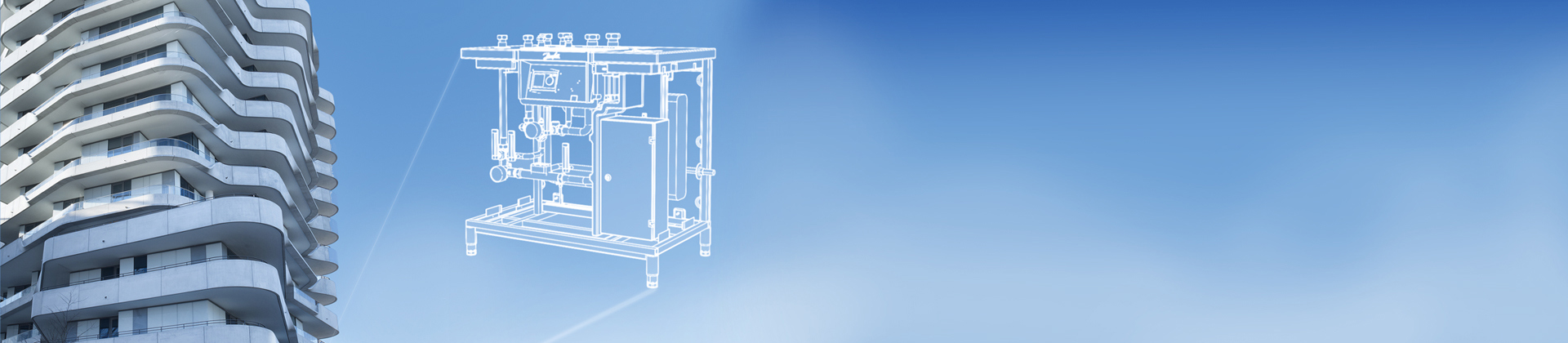
Submit an inquiry
Contact us today to learn more or complete the inquiry form to be connected to a Danfoss district energy expert.
Products
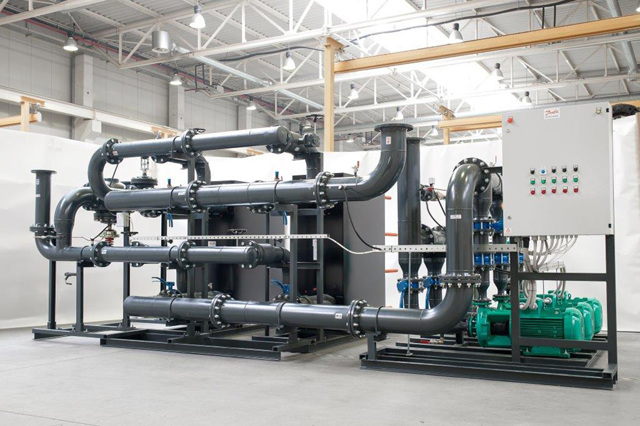
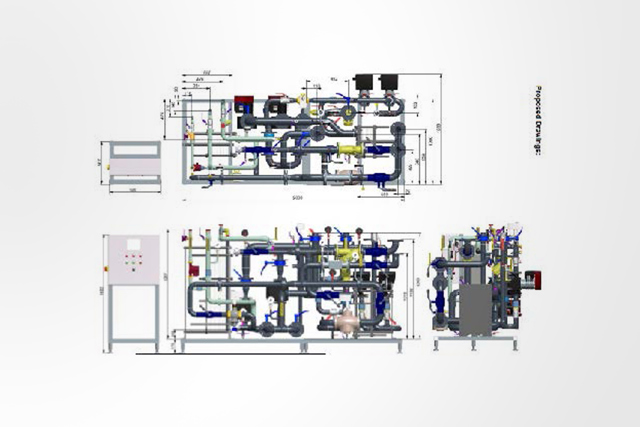
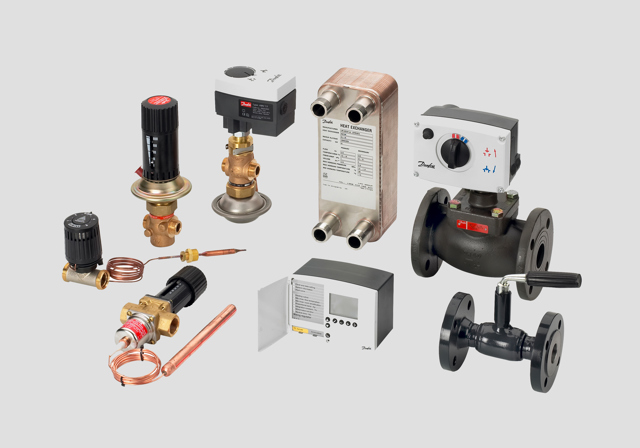
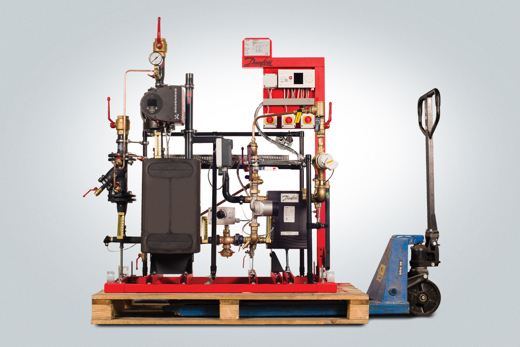
Designed for transport
Our custom-built energy transfer stations feature a compact size and weight, and are engineered to easily transport through halls and stairways as needed, with minimum hassle.
Available both pre-assembled or split in easy to assemble modules if required due to space and height restrictions.
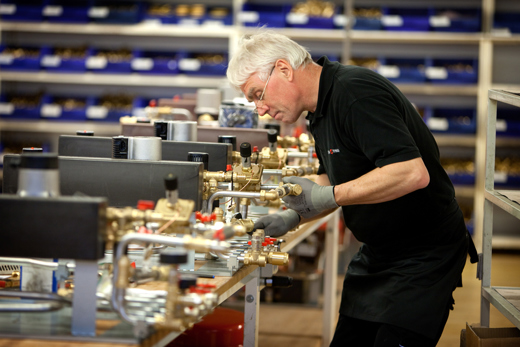
Industrialized production
Forget about waiting for on-site fabrication contractors. Danfoss takes pride in our professionally managed factory and production staff that offer improved quality through our rigorious control processes.
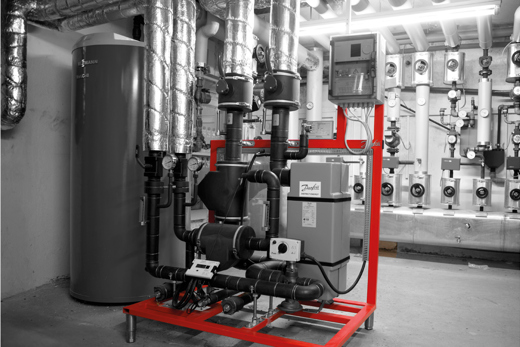
Configured for performance
Custom energy transfer stations arrive ready to run with factory configured controls. Each unit is pre-tested for function and performance and Danfoss maintains documentation on this before delivery.
In addition we maintain spare parts inventory to get you products fast, should they be needed. Our 3D drawings are archived for easy fabrication of replacement pipe network that may be needed over the lifetime of the equipment. This means often no welding is needed onsite.
Our products are also backed by the Danfoss warranty, which is typically 24 months from the service date, or 36 months from the delivery date.
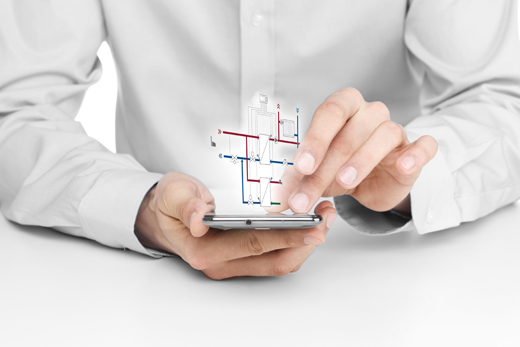
Installation, commissioning, and service support
Danfoss offers a comprehensive service support program to ensure that your new station is properly installed and commissioned. This covers all aspects of commissioning, maintenance, technical support, spares, warranties, and more.
Please contact Danfoss to inquire.
Features and benefits
Reduced engineering cost & risk: rather than hiring a consultant to design a unique system, a pre-engineered, factory-built ETS can be sized to meet the building’s load & other criteria while benefiting from standardized, proven controls solutions.
Improved production quality: Fabrication quality is better ensured in a professionally managed factory environment. Pressure and leak detection are carried out in a controlled environment following a prescribed process. Building equipment onsite introduces issues of space, lighting, and welding access that can compromise high quality work. The opportunity to pressure and leak test offsite is lost.
Less time onsite: producing an ETS onsite requires up to months of work inside the building & includes services from pipe fitters, electricians, & controls contractors. Producing the unit offsite enables scheduling delivery to coincide with construction project schedules. Construction managers appreciate the ability to minimize activity on already crowded job sites. Installation time is dramatically reduced to a little as one day. Activity onsite is limited to a single electric power connection plus connection to building & district pipe networks.
Documented, reproducible, and maintainable installations: Factory built ETS are supported by archived engineering design and fabrication documentation, including complete bill of materials that facilitate long term maintenance needs. “As built” drawings and documentation are unlikely to accompany the completed work of contractors attempting fabrication of a solution onsite. This can lead to long-term maintenance headaches.
Plug-and-play operability: Factory fitted, configured, & tested controls are integral on factory-built ETS. They can be configured for the operating conditions at the installation site prior to delivery. As a result, the ETS can be ready to heat or cool its served building upon first start. When a solution is “stick-built” onsite, the controls contractor’s work is just beginning after the pipe fabrication is complete.
Support: Engineering support & specification service as well as start-up & commissioning assistance provided by a Danfoss expert.
Typical applications:
- domestic hot water systems
- and/or other water-based (hydronic) heating systems
Typical installations:
- Commercial buildings such as universities and hospitals
- Residential buildings including multifamily buildings
- Government and industrial buildings and facilities
How it works
Case studies
-
if (isSmallPicture) {
; } else if (isBigColumns) { } else { }Danfoss Energy Transfer Stations Help Sheridan College’s District Energy System Make the GradeCreating a sustainable energy system to heat, cool and power an entire college campus is no easy feat. In 2013, when Sheridan College launched its Energy and Climate Master Plan, with the goal of lowering campus energy and greenhouse gas emissions by half, they realized that they would need to transform their heating and cooling system. They looked to the Trias Energetica model, first developed in 1979, as a guide to developing a sustainable energy system, integrating heating and cooling functions and recovering energy that might otherwise be wasted.
News
View related podcasts
Join our Envisioneering Exchange host, John Sheff, Danfoss’ director of public and industry affairs in North America, as he addresses the changing landscape through informative, valuable dialogue with thought leaders and experts-in-their-fields.
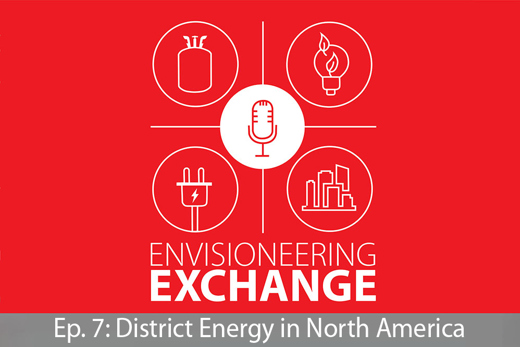
Episode 7 - District energy in North America
What is district energy? What is its potential for buildings, building networks/campuses, and cities in North America looking to improve efficiency, reduce greenhouse gas emissions, lower operating costs, and ensure resiliency? How is today’s technology affecting market development? Tune in to this episode for a conversation on district energy (including heating and cooling) with Jeff Flannery, Danfoss’ business development manager in North America.
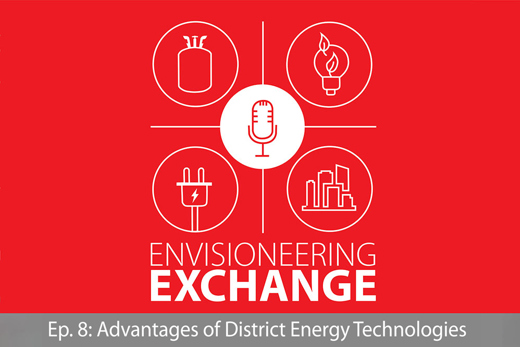
Episode 8 - Advantages of district energy technology
This episode takes the discussion on district energy in Episode 7 even further — examining how technology like pre-engineered, factory-built energy transfer stations are being used today to reduce engineering costs and risks and enable “plug-and-play” operability in district energy networks in North America. Jeff Flannery, business development manager for district energy in North America, joins us to discuss a recent project at Sheridan College in Ontario, Canada.