
Maximize conveyor uptime
Conveyor applications need to perform reliably to ensure maximized uptime and the lowest cost of ownership. Danfoss solutions provide optimized motor control and, for example, improve quality and product consistency, minimize waste and optimize whole filling and packaging area. They are often regarded as the preferred brand within many of these industry sub-segments.
Highly sensitive products, such as still bottled water and alcohol-free beer or new materials for packaging and bottles, raise the hygiene requirements in production plants. In addition to the Machinery Directive and national standards, the European Hygienic Engineering & Design Group (EHEDG) regulations are becoming increasingly important for plant design and drive engineering. Danfoss is unique in offering EHEDG and IPA certified solutions and products for use in hygiene-critical sub-systems.
The VLT® FlexConcept® is currently the only solution on the market that provides EHEDG-certified components specifically intended for use in hygiene-critical sub systems. The motors are also certified by the Fraunhofer Institute IPA for direct use in cleanrooms and aseptic production plants.
The system simplifies project planning, installation, commissioning and maintenance, especially for conveyor systems. System variants might be reduced by up to 70% so users benefit from maximum flexibility with a minimum number of modules, including motors and drives which offer a unified operating concept and standardized functionality regardless of whether the system is implemented with a centralized or decentralized structure, in dry, wet or aseptic areas.
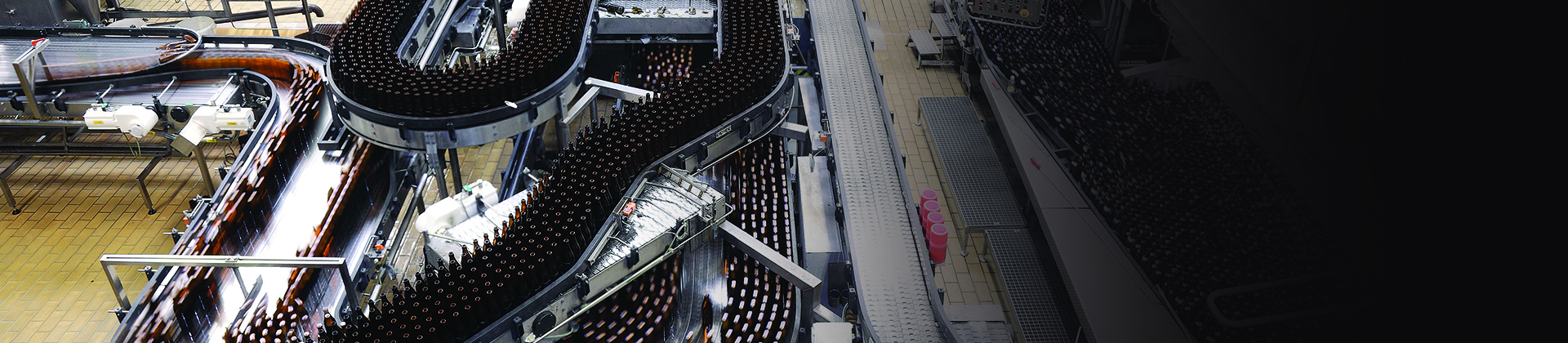
Discover how to maximize uptime with the VLT® FlexConcept® system
VLT® FlexConcept® combines modern motor technology with the most advanced inverter drives in a flexible unified drive system offering high efficiency, robust reliability and variant reduction.
Products
-
if (isSmallPicture) {
; } else if (isBigColumns) { } else { }VLT® Midi Drive FC 280FC280 provides precise and efficient motor control for machine builders in the food and beverage, material handling and processing industries.
-
if (isSmallPicture) {
; } else if (isBigColumns) { } else { }VLT® AutomationDrive FC 301 / FC 302The VLT® AutomationDrive FC301 / FC302 is designed for variable speed control of all asynchronous motors and permanent magnet motors. It comes in a standard version (FC301) and an advanced high dynamic version (FC302) with additional functionalities.
-
if (isSmallPicture) {
; } else if (isBigColumns) { } else { }VLT® OneGearDrive®A highly efficient combination of a permanent magnet motor and optimized bevel gearing.
-
if (isSmallPicture) {
; } else if (isBigColumns) { } else { }VLT® Decentral Drive FCD 302Thanks to its rugged design, the FCD302 drive can be mounted close to motors in demanding applications.
Case studies
-
if (isSmallPicture) {
; } else if (isBigColumns) { } else { }Future-proof energy efficiency at AB InBev Hoegaarden® breweryChallenged by aging machinery and no time for downtime, AB InBev Hoegaarden® chose Danfoss iC7-Automation and VLT® OneGearDrive®—for high energy efficiency.
-
if (isSmallPicture) {
; } else if (isBigColumns) { } else { }First mover controls beverage conveyor systems with iC7-AutomationBELGIUM: Legendre Conveyors has built up great trust in Danfoss over many years of conveyor design using VLT® drives. Now they progress to the new iC7 series.
-
if (isSmallPicture) {
; } else if (isBigColumns) { } else { }Cantine Riunite saves 30% energyIncorporating the VLT® FlexConcept® into a bottling-line expansion project helps save energy and minimize maintenance costs.
-
if (isSmallPicture) {
; } else if (isBigColumns) { } else { }Ready-made sauces the sustainable wayITALY: The home of pasta is also the seat of sustainable sauces. From Barilla’s Rubbiano plant, in the heart of the Parma food district, over 150 million jars of ready-made pasta sauce leave every year for tables all over the world. A plant expansion completed in 2019 uses more than 400 gear motors and decentralized drives from Danfoss to reduce complexity, optimize space, and minimize carbon footprint.
-
if (isSmallPicture) {
; } else if (isBigColumns) { } else { }Danish Crown super slaughterhouse saves 37k USD annually on motor replacementThe 1,000 VLT® drives installed throughout the plant control everything from simple conveyor belts to more advanced applications.
-
if (isSmallPicture) {
; } else if (isBigColumns) { } else { }Bottling is more competitive when it is sensorlessTo achieve higher productivity and energy efficiency on two new bottling lines, Tavina chose the Danfoss VLT® FlexConcept drive system.