It’s a challenging time to work on a supermarket’s technical team. Competitive pressure has brought an even greater need to reduce running costs—and often to do it with a reduced headcount.
Many new kinds of store facility technologies promise to help. Big data, automation, and the Internet of Things (IoT) all have the potential to save food retailers time, money, and energy, while preventing food waste.
This article will share five ways major food retailers around the world—and their refrigeration contractors—are realizing real-world benefits, right now. And they’re doing it by connecting their in-store systems to the internet.
Most stores protect food safety and the customer experience by using alarm functions to alert a technician if something is not working or a sensor reading is outside a set parameter. These can cover everything from the temperature rising because a cooler door was left open to a broken light or fan.
Some alarms are genuinely urgent and could lead to lost stock or sales. Others can wait to be batched as part of a technician’s task list, making servicing more efficient. But a large store can have dozens of alarm events a day; just interpreting all the error codes can be a full-time job.
When your refrigeration system controller is online, you can outsource this triage task—saving time and money and giving you 24/7 coverage all year round.
For example, Danfoss Enterprise Services’ (DES) international teams handle 2.8 million alarm events every month. There’s an online dashboard, so it’s easy to see, triage, and prioritize system alarms, all at once, at both a store and chain level.
This saves technician time and makes maintenance more efficient. And a centralized monitoring center like DES can learn from worldwide alarm data to help interpret every alarm quickly, understand where risk lies, and improve diagnostic problem solving.
For a food retailer, triaging system alarms in this way can help you to batch and plan your maintenance, saving technical workload without compromising food safety, shopper experience, or system reliability.
But it’s possible to go further and intervene remotely to solve refrigeration issues, without a technician visiting the store at all.
A connected system manager, like the Danfoss AK-SM800, lets a monitoring service do more than simply notify technicians of alarms. They can diagnose the problem, and often fix it remotely—for example, by updating refrigeration setpoints and alarm thresholds, or by triggering a defrost—without setting foot in the store.
At DES, we have seen that this approach typically results in a 15-30% reduction in unnecessary service truck rolls.
Centrally monitoring your alarms means service technicians can immediately prioritize emergencies when they come through. But that’s only one way a connected system can help retailers avoid food waste.
Accurate sensors in the refrigeration case can track and measure cooling performance to a high degree of accuracy.
This—and the fact setpoints can be adjusted remotely—means supermarkets can move away from the wasteful practice of including a wide margin of error around refrigeration temperature settings without risking food safety. More accurate temperature control makes cooling safer and often more efficient.
And because the system manager is connected online, the temperatures are all logged automatically at regular intervals. This means you have detailed evidence that every item of food has been kept in optimum conditions throughout. You can satisfy HACCP without requiring staff to manually record temperatures up to four times a day per cabinet.
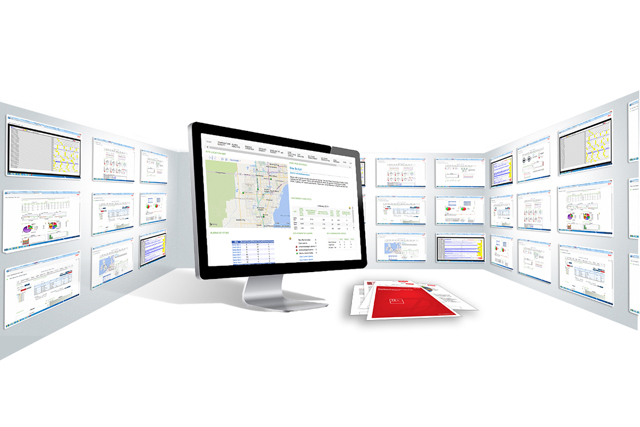
For years, supermarkets have looked closely at sales data trends to optimize the performance of individual stores—even individual displays. But fewer retailers realize it’s possible to do exactly the same thing with in-store technical systems to reduce operating costs. It’s enabled by a connected system manager.
First, an in-store system manager like the AK-SM800 collates energy usage and performance data from all connected systems—refrigeration, air conditioning, lighting, and more. Then it uploads it to the cloud, where the DES dashboard makes it easy to create an accurate baseline for each store—normalized to account for variables like size and ambient temperature, so the comparisons are fair.
This is powerful information. You can use it to make targeted and informed cost savings—identifying common trends among poorly-performing stores and making incremental improvements across the entire estate.
The data can point to potential compressor pack and defrost cycle optimizations, proactive ways to manage refrigerant setpoints, and refinements to a store’s HVAC and lighting schedules.
If you’re busy, you can ask DES to perform this analysis for you. We can make proactive suggestions to cut energy costs based on actual data and benchmarked against industry norms.
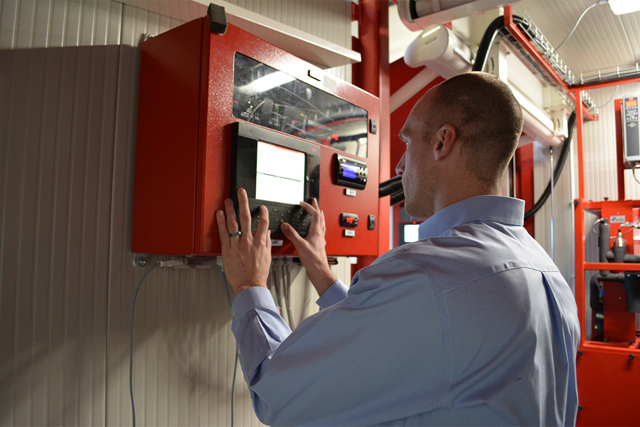
A growing number of supermarkets are engaging in energy arbitrage—adapting their energy consumption to respond to discounted off-peak energy or moments of peak demand.
For example, utility companies will often offer bonuses to companies who help them balance supply and demand in the grid. And supermarkets are ideally placed to benefit.
A simple change, like temporarily reducing sales floor lighting or allowing air conditioning temperature to drift slightly, can produce energy tariff savings with minimal impact on the shopping experience.
But in most stores, refrigeration uses more energy than anything else—and holds the greatest savings potential. Harnessing this without risking food safety is possible but takes significant food refrigeration experience.
This trend is so important that we’ve written a separate article about it. But it’s also worth knowing that a connected system manager makes the process much easier—the energy saving measures can be triggered remotely, using careful scrutiny to ensure temperatures stay in line. And DES can collect the evidence to claim the benefit from the energy provider.
These measures are all possible now, with today’s technology. At DES we’re managing them for tens of thousands of food retailers worldwide.
But the future is even more exciting. As more supermarket systems are connected, more retailers can all benefit from the resulting data.
For example, supermarkets understandably err on the side of caution when it comes to the preventative maintenance of their food refrigeration units. The cost of an unscheduled breakdown—food waste, emergency callouts, and lost sales opportunities—is often extremely high.
But this extra safety measure also means planned refrigeration downtime and servicing costs are higher than they need to be. If they had a clearer idea of which units were likely to break down, when, and under what conditions, they could save money accordingly.
By analyzing performance data, it’s possible to get an accurate prediction of the risk that an asset will fail. Then, retailers can focus their maintenance spend and catch small problems before they become expensive emergencies.
But to form an accurate prediction, you need a lot of data; more than any store—or even any chain—could gather alone. And that’s where the millions of alarms processed by a service like DES could help. We have a huge, international pool of anonymized store data telling us exactly how each model performs in different environments.
We’re using analytics to see if that data can tell us whether a unit will break down. If it can, we’ll be able to help retailers and maintenance contractors focus tight maintenance budgets where it reduces their risk the most.
To balance these current and potential benefits, it’s important to have a system that delivers savings today but is also ready for the future. For example, at Danfoss, our philosophy is to use open protocols, so customers can decide for themselves what happens to their data and how it’s used. It makes collaboration and updates easy.
And that means there’s no reason to wait for future developments—retailers can start saving money, protecting their margins, and saving time right now.
-
if (isSmallPicture) {
; } else if (isBigColumns) { } else { }Smart StoreThe Smart Store solution enhances food safety and brings down the energy bill by integrated and smart control of refrigeration, HVAC, lighting and other applications.