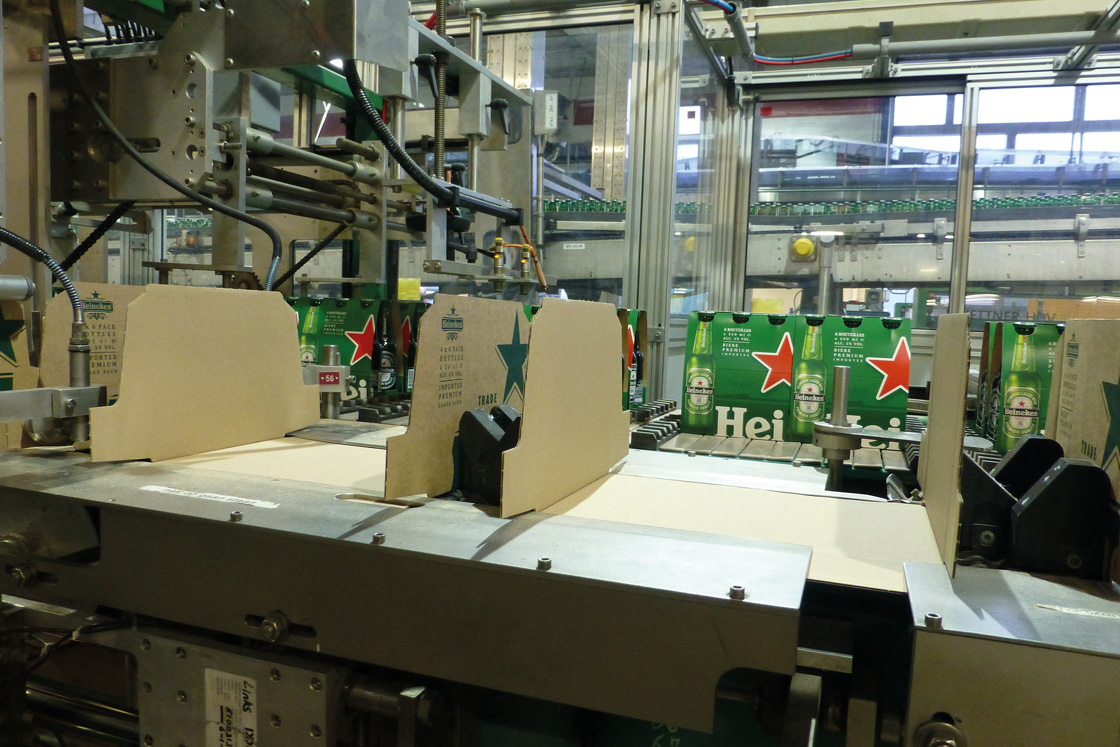
Six bottles of beer in a cardboard box, with a handle on top. It’s just that easy! This makes sense, as consumers often choose a six-pack. But Heineken in ‘s-Hertogenbosch, Netherlands, also likes this form of packaging. With the new six-pack production line, this brewery packages 44,000 bottles of beer into packs of six within one hour.
The view from the gallery above the packaging hall is impressive. Tens of meters of conveyor belts are moving bottles of beer of different brands towards the robots and stackers. Once they arrive, the bottles disappear in no time flat into all kinds of packaging, including plenty of six-packs. A handful of operators move between the lines and intervene here and there; only when something seems to be going wrong. The quietude of all the process is just overwhelming. The packaging seems to simply calmly go on.
Teamwork solves synchronization challenge
However, the six-pack line has some special technology behind it. Over the last nine months, a Danfoss-supported Heineken team has worked on a new drive and control system for this packaging line.
Jan Brouwers, Detail engineer at Heineken s´-Hertogen-bosch says: “The biggest challenge was the synchronization of all the drives. All the different motors with their different power ratings varying from 1.1 to 2.2 kW and having different transmissions, all of them had to be in the correct position at exactly the same time. For this reason, we used the MCO 350, an extra module for the VLT® drives supplied by Danfoss. The programming of the motor control was performed mainly via the PLC. But we could introduce the synchronization with the MCO 350 itself. This module is a card added to the VLT® drive, that can be addressed via an interface. When we got that far, we started with one drive at a time; then we would add another drive at a time, until we had the six drives. Since that moment on, this line has been running without any problems. We don’t have to keep watching it any more. The greatest benefit for Heineken is our improved reliability of supply. In the past, the unscheduled shutdowns used to throw a wrench in the works. Now, that’s all gone. Thanks to this project, Heineken awarded us ‘Team of the Month’. Of course, such a recognition is always welcome. But now, we have all moved on to new projects. We still have so many challenges that we will definitely not be bored”.
VLT® drives standard since 1968
Why did Heineken opt for the installation of Danfoss VLT® drives? Jan Brouwers explains: “Heineken has been working with Danfoss drives since 1968.
Of course, this started well before our time, but our companies have had a consistent relationship since then. At some point, Heineken decided to start using Danfoss VLT® drives as standard. That was a matter of cost savings on the one hand, and quality, support and delivery reliability on the other hand. Over time, all the hundreds of older drives have been replaced with new ones from Danfoss. And that’s what happened here, on this packaging line that creates the six-packs, too.” 44,000 bottles per hour The project for the new packaging line really demanded a major effort. What did it take to achieve this? Jan Brouwers: “Any changes to existing equipment here have to fit in with ongoing production. This means that you can’t just work on a machine whenever you want. And then, of course, this line has technical challenges, too. This line contains eight motors, all controlled by VLT® AutomationDrive FC 302 drives. These motors provide the propulsion for the conveyor belt and the Traypacker; the core component of this line. The Traypacker folds the cardboard and manipulates the bottles to create a six-pack. Then the Traypacker places four six-packs together on a tray, puts a top on them and glues the box shut. This box contains 24 bottles, same as a crate. Our line can now pack 36 trays per minute or around 44,000 bottles per hour.”
Contact person for more information:
Michael Kannekens, Application Engineer and Kees Bolier, Sales Engineer, Danfoss B.V. Netherlands