
Water presents a significant risk to mining operations, potentially causing equipment damage and environmental contamination. A robust pumping system is required to control the flow of water and remove it from the work site. A large copper mine in Arizona had reached a critical stage where they needed to replace their 250-horsepower (HP) dewatering pump and increase pumping capacity.
With plans for future growth, the owners wanted to ensure that the new pumping system would be able to accommodate their needs long into the future. On a dry day, 600-700 gallons of water need to be pumped out of the bottom of the mine each minute. If it rains, that amount could be as much as 6,000 gallons. The mine needed a reliable and flexible pumping system that would work well in the Arizona heat and sun.
The Low Voltage Solution
Jim Briggs, an engineer and CEO of Rockridge Controls, a consulting firm in Prescott, AZ, was helping the mine develop its new pumping system. Having built pump controls for several years using Danfoss VLT® AutomationDrive and VLT® AQUA drives, he was familiar with their versatility. “The drives are easy to program and reliable and work well in a variety of pumping capacities,” he said. He contacted IEC Supply, a Preferred Partner Distributor in Arizona for Danfoss, looking for a medium voltage drive for the new pump’s 900 HP motor. IEC Supply has been a Danfoss partner for more than a decade, supplying Danfoss VLT® drives to Arizona mines.
Unfortunately, at the time, “Danfoss did not have a cost-effective medium voltage solution, but we didn’t want to lose the opportunity,” said Lise Houston, regional sales manager at Danfoss. “We looked at low voltage alternatives and came up with a solution using a low voltage drive and transformers.”
The solution, employing the Danfoss VLT® AQUA Drive FC 202, and hi-lo transformers to connect the drive to the power supply and pump motor, proved to be an attractive option. The drive setup consisted of 2 parallel power modules of 450 HP each, on a common bus, to match the 900 HP pump. The cost was substantially lower than the expense of a medium voltage drive; Briggs estimates that the solution saved the mine about 50% of total costs.
With crews working at different areas of the mine on any given day, the dewatering pump, which sits at the bottom of the mine, needs to be moved along with the workers. To allow for mobility, Briggs built a trailer to house the drive and transformers, connecting them to the pump and main power line through cables. To ensure the drive is powering the pump motor at the correct voltage, one transformer sits between the power supply and the drive, lowering the voltage to allow the drive to operate.
The FC 202 variable frequency drive (VFD), with its capability to output anywhere from 0 to 480 V, enables the motor to operate over a wide speed range depending on how fast water needs to be pumped. An output transformer between the drive and the pump motor ‘steps up’ that VFD output voltage to supply the higher voltage motor. Changes in the VFD output voltage based on pumping demand is detected by the motor, which then adjusts its speed accordingly.
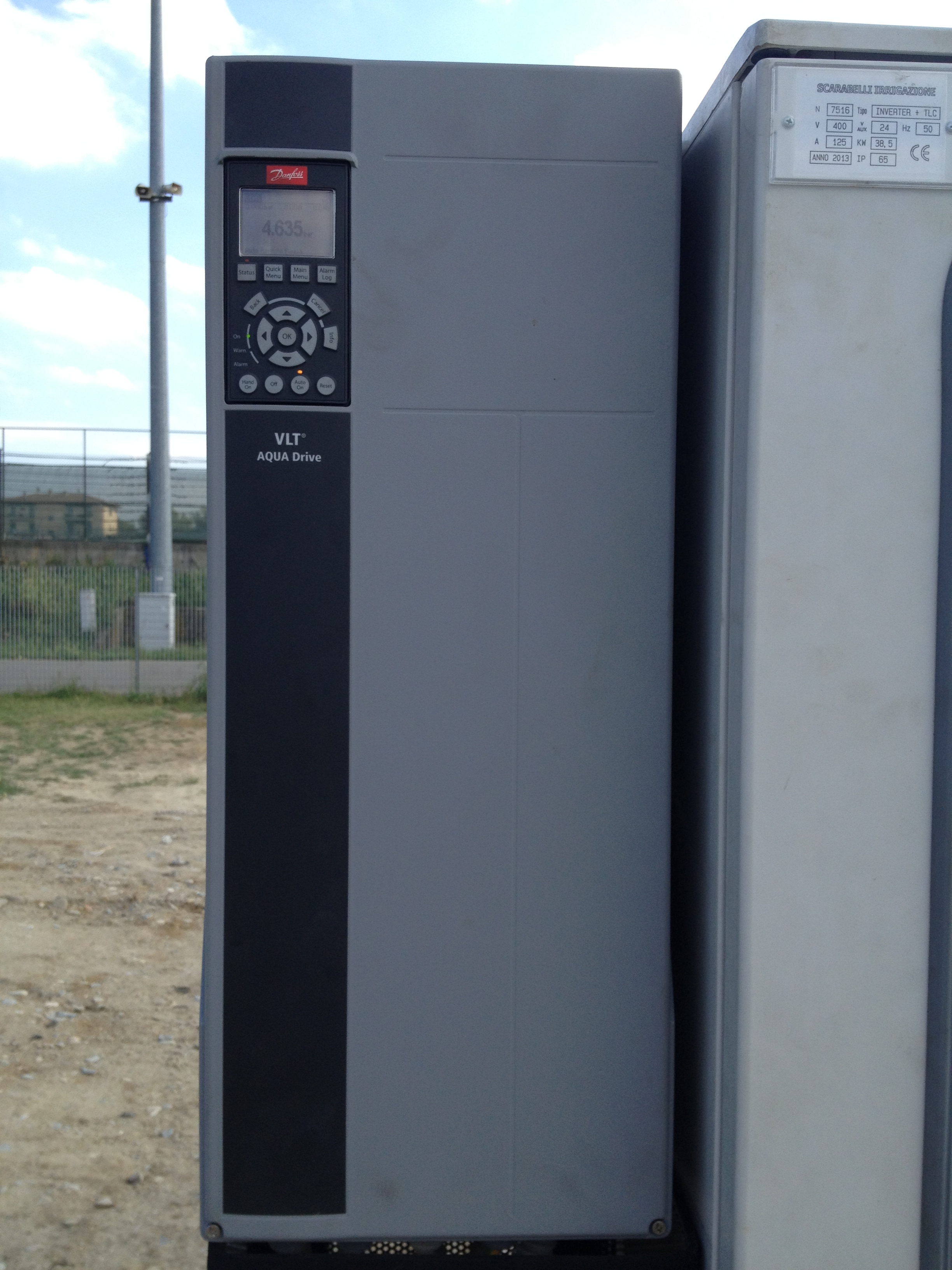
Performing Under Pressure
Another benefit offered by the AQUA drive is its back-channel cooling feature, which removes heat through the back channel, or enclosure panels, to the outside. This prevents the drive from overheating, reduces faults related to high temperatures and prolongs product life. With up to 90% of heat losses exhausted outside the trailer enclosure, the drive is very effective in a hot environment. Briggs noted, “It’s extremely hot down there and the drive has managed to handle the heat well.”
The trailer was delivered to the mine in May 2021 and installation was completed that September. Briggs noted that it was the first parallel drive system that he programmed and Danfoss technical support was “very helpful” in guiding him through the process. With the pump running daily, the low voltage drive system has proved to be up to the task. “The mine is large and deep and the pump needs to move a lot of water, especially if it rains,” Briggs said. “The customer has been happy. The drive has worked really well and the customer saved a lot of money.”
Learn More
-
if (isSmallPicture) {
; } else if (isBigColumns) { } else { }VLT® AQUA Drive FC 202Maximum energy efficiency for both water /wastewater and Industrial pump/fan applications