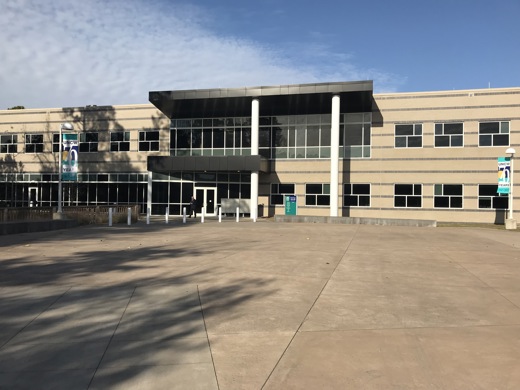
Located close to various waterways, the University of North Carolina Wilmington (UNCW) takes marine science seriously. Its new MARBIONC Building — a 69,000-square-foot interdisciplinary research facility for marine biotechnology — provides labs for lease to commercial enterprises that require reliable, energy-efficient 24/7/365 cooling. Faced with high humidity and mid-Atlantic climate variations, the building required a chiller plant that could take advantage of a wide range of operating conditions and still run reliably.
"Our climate extremes are 97.5°F dry bulb and 88.3°F wet bulb temperatures," said Steve Sharpe, energy manager for UNCW. "These conditions are taxing HVAC systems. The MARBIONC Building uses nearly 100 percent outside air. So, when you have high wet bulb temperatures, you must ring the moisture out of the outside air being supplied inside. Outdoors, the high humidity hampers evaporation, making it tough for cooling towers to reject heat.”
To optimize the chiller plant, Sharpe worked with John Blakeney, branch manager of Thermal Resource Sales, Wilmington, who suggested the best option would be an all variable-speed chiller plant given the variability of ambient conditions and the load.
Based on ASHRAE recommendations at that time, the most efficient type of plant would be a single, primary-flow, fully variable-volume chiller plant. In this design, variable-speed pumps circulate chilled water to cooling coils in air handlers that provide space cooling.
Along with variable-speed pumps, variable-speed chillers are employed because they can track the variable thermal load very closely, saving energy for the remaining 8,610 hours operating below peak load.
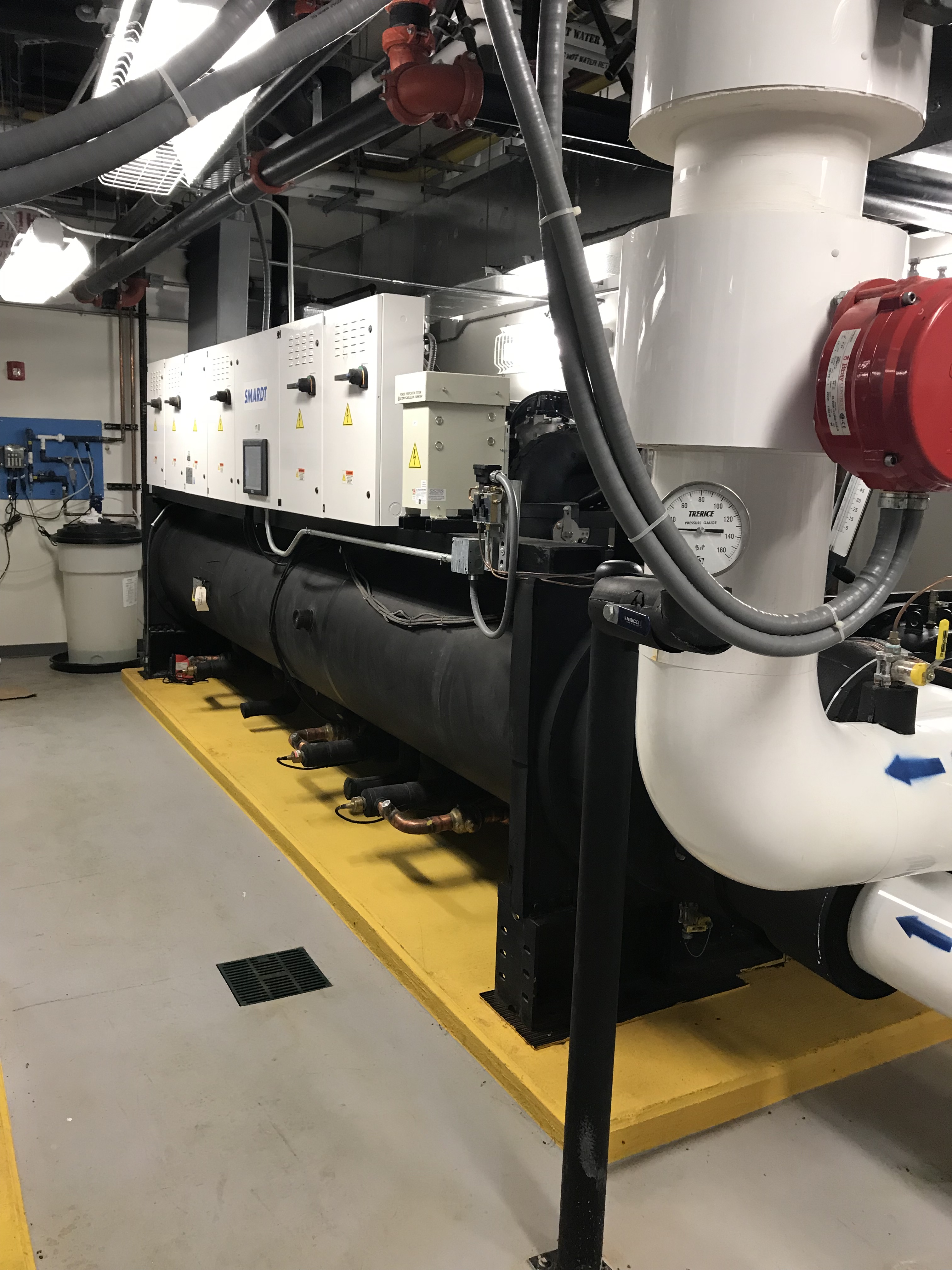
Magnetic-bearing chillers boost efficiency
To take maximum advantage of all the hours below full load, Sharpe selected two 750-ton Smardt WA240 water-cooled variable-speed chillers. Each chiller uses five Danfoss Turbocor® TT400 oil-free magnetic-bearing centrifugal compressors, individually rated at 150 tons nominal.
“Unlike positive-displacement reciprocating and screw compressors that use brute force to create lift, centrifugal compressors use impellers to create lift similar to a jet engine,” said Sharpe. “As system conditions change, the compressor must be able to adapt to these changes rapidly. Through constant system monitoring, the Danfoss Turbocor® compressor modulates refrigerant flow and impeller speed to counteract conditions that could create surge (stall) or choke. Danfoss also mandates a stop/check valve be installed to prevent reverse gas flow that could cause an internal mechanical issue.”
Additionally, Danfoss Turbocor® TT400 compressors do not have oil circulation problems because they use magnetic bearings that require no lubrication. The rotor shaft levitates in a magnetic field without the friction produced by physical contact bearings. Furthermore, there is no oil to foul evaporator tubes.
Sharpe also notes the Smardt chiller has outstanding stability across a very wide operating range. "Danfoss Turbocor® TT400 compressors have a very large operating envelope where the stall and surge lines are very far apart. That means a single compressor can turn down capacity to handle very low loads and flow.”
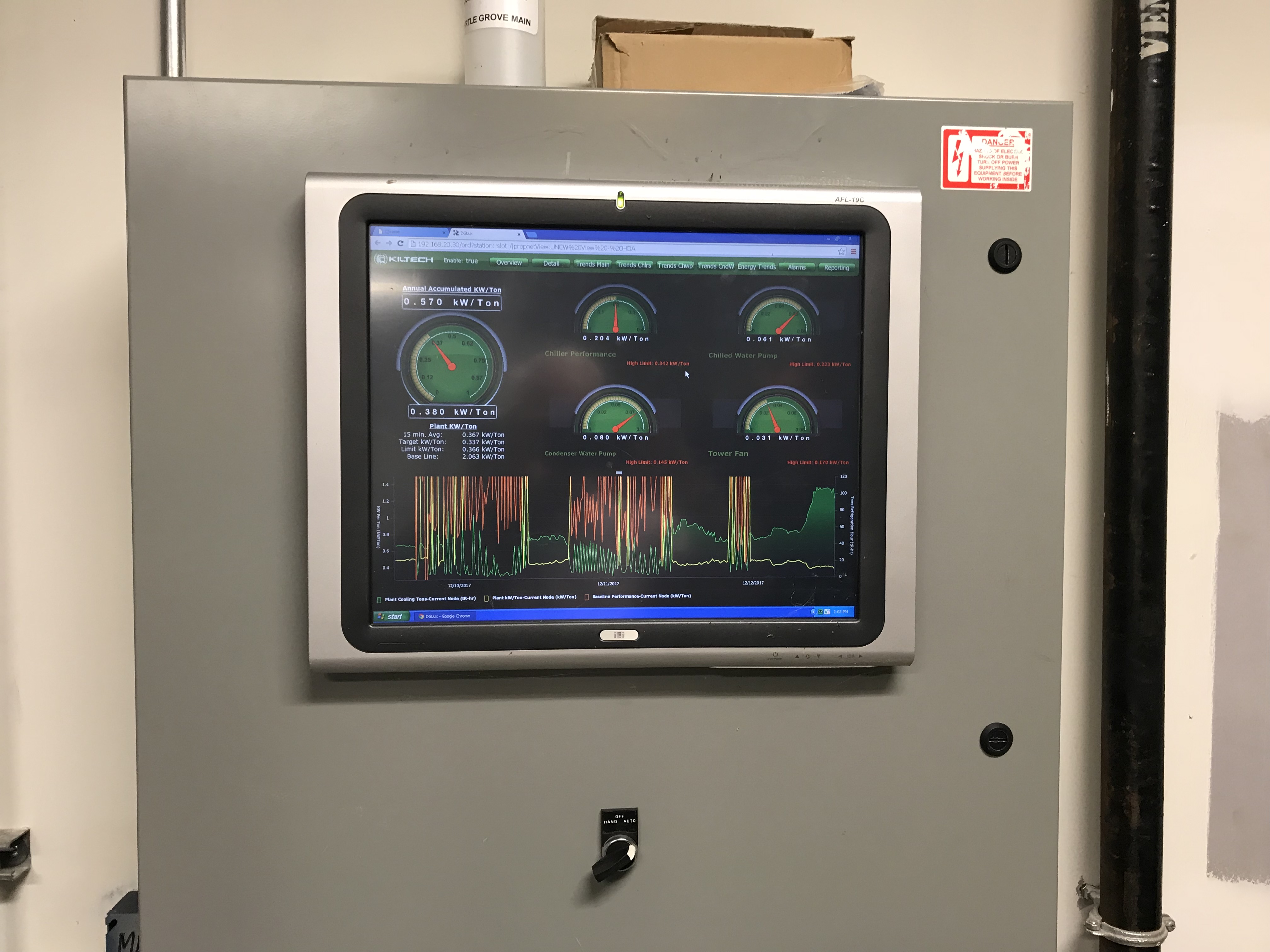
Variable frequency drives propel savings
Along with employing a true variable-speed, variable-flow chiller, another tactic that boosts system efficiency is minimizing the energy used by the cooling tower. "You save energy whenever you can reduce cooling-tower fan speed and flow down to the point that ambient conditions make it possible to reach your minimum condenser water temperature," says Matt Squires, Wilmington branch manager of Engineered Control Solutions. Squires worked with TRS in specifying and installing the controls and the Danfoss VLT® HVAC Drive FC 102 that modulates the cooling tower fans.
"This installation uses a Tower Tech forced-updraft, counter-flow cooling tower, which is very compatible with Smardt chillers," said Squires. "With a maximum capacity of 2,000 GPM, this cooling tower works well with variable heat load applications. In this case, we applied one 100-horsepower Danfoss VLT® HVAC Drive to operate ten 10-horsepower direct-drive fan motors. This configuration makes the most of the heat exchanger surface area. It delivers some of the best efficiencies you can get."
Results that add up
The Central Plant Energy Control System (CPECS) report from August 2016 to 2017 shows the plant ran 6,687 hours using 1,123,373 kWh for an average annual plant efficiency of 0.576 kW/ton. A baseline ASHRAE Standard 90.1 plant modeled on those same hours would have had an efficiency of 1.034 kW/ton, consuming an extra 929,529 kWh and costing an additional $67,855.
"The difference really shows up on our coolest days," Sharpe emphasized. "That's when we need as little as 38 tons of cooling capacity. This 750-ton Smardt chiller with its multiple compressors easily turns down to this load. Few chiller plants use compressors that can turn down capacity that low, and if they try, their compressors can run into big problems.”
"We were able to run that plant condition at an efficiency of 0.66 kW/ton. Do that with a baseline plant, and it would consume up 6.3 kW/ton. At more ideal part-load conditions, the Smardt plant operated at 0.396 kW/ton — the plant with an average system IPLV of 0.62 kW/ton. It can handle CHWST ranging from 51.4°F and 45.5°F, and chiller downtime is zero."
"It's smarter to use chillers that can handle temperature reset and not work as hard. If you have a plant that can unload efficiently, run at those part-load conditions, and take advantage of cooler outside conditions, the savings cascade hour by hour, day by day. We're saving a lot of money, with a payback well under five years, with less maintenance and 100 percent uptime — all while shrinking our facility's carbon footprint."
Related products
-
if (isSmallPicture) {
; } else if (isBigColumns) { } else { }Turbocor® - TTSDanfoss Turbocor® model TTS oil-free compressors are available in four different models ranging from 60 tons to 200 tons / 200 to 700 kW utilizing R134a or low GWP R513A.
-
if (isSmallPicture) {
; } else if (isBigColumns) { } else { }VLT® HVAC Drive FC 102This tough and savvy FC102 drive enhances pump and fan applications in building management systems, and runs outdoors in most climates.