Rising energy costs and global awareness of sustainability move the world towards improved energy efficiency. This is also true for the commercial refrigeration industry, where price competition and customer requirements for food storage and safety accelerate the demand for energy efficiency.
So how do you achieve the desired energy efficiency, operational accuracy and food safety requirements for Glass Door Merchandisers (GDM)? In this article we will explore some of the advantages provided by electronic thermostats & controllers, when compared to traditional electromechanical thermostats in order to support you in your choice of a temperature control device.
The traditional thermostats have been used for decades to control the on/off cycle of the compressor, ensuring that the temperature of the GDM is maintained at the pre-set value at all times. The electromechanical thermostat, Danfoss 077B series, has proven to be a simple and low-cost solution that allows the most basic functionality, i.e. control of the compressor, but with fewer options for achieving energy savings and other benefits that modern, electronic thermostats and controllers can provide.
Thermostat noun | ther·mo·stat | \’thәr-mә-,stat\ |
This thermostat, while cost effective and reliable, typically controls only the operation of the compressor and the potential energy savings offered by combined control of compressor, evaporator fan, and defrost heater cannot be fully realized. To address these issues, an electronic thermostat can be installed in place of the traditional electromechanical thermostat.
First of all, the electronic thermostat, offered by Danfoss as ETC 1H range of controllers, lowers the energy consumption by optimizing the operation of fan, defrost heater and condenser (optional) along with compressor. The electronic thermostat also offers high accuracy of temperature control due to close differential and narrow tolerances which remain stable over time. Sensors to control the cabinet temperature, the evaporator defrost and the condenser temperature may be added to enhance performance. Furthermore, the electronic thermostat typically has a built-in timer for defrost and other functionalities like initial pull-down and alarm delay. In addition to providing energy savings, the ETC 1H range of electronic thermostats provides voltage protection and zero cross-over relay technology that increases the life of the controller.
Electronic thermostats are similar in shape and size to conventional thermostats making them easy to apply in existing designs. To fulfill the wish for an external display of temperature on the GDM - a wish that has become more or less standard today - the electronic thermostat may be connected to an external display; a feasible solution, but requiring extra work on the assembly lines.
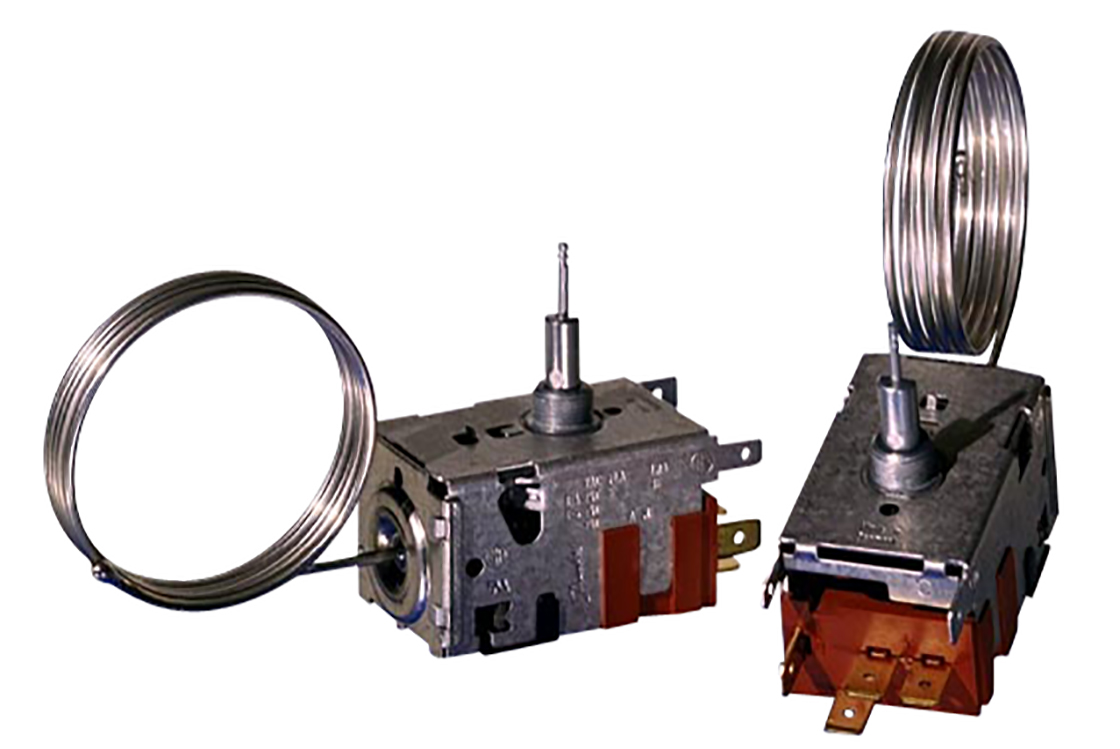
A more recent demand from an increasing number of customers is data collection in connection with the use of GDMs, e.g. the number of door openings, drinks chosen, fluctuations in temperature levels, fan and compressor cycles day/night. This demand requires an advanced electronic controller.
Let’s take a closer look at some of the advantages offered by the advanced electronic controllers described through the features of Danfoss ERC Electronic Controllers series.
Energy savings of up to 33%
The beverage industry has set ambitious sustainability targets, where energy savings play an important role. Electronic controllers promise to deliver substantial energy savings through automatic and integrated control of the compressor, fan, defrost heater and lighting. The electronic controller can be programmed to meet the exact requirements of your application depending on location, patterns of use, ambient temperatures and other factors impacting the energy consumption. In this way the energy efficiency of each GDM installation can be optimized by self-adjusting if changes occur in operating conditions, location, etc.
In a recent test performed at the Danfoss facility in Baltimore, the energy consumption of the GDM was compared using an electromechanical thermostat and an electronic controller. The test resulted in energy savings of 33 % in favor of the electronic controller.
Approved for flammable refrigerants
Thanks to the design of the electronic controllers, where all components are assembled into a confined cabinet, the controllers have been approved for flammable refrigerants, notably propane, which is fast becoming a favorite of the beverage industry. The use of natural refrigerants in GDMs is becoming more and more widespread as a result of the sustainability efforts of the leading beverage companies.
Telemetry noun | te·lem·e·try | \tә-’le-mә-trē\ Highly automated communications process by which data is collected remotely and transmitted to receiving equipment for monitoring and analysis. The word is derived from Greek, ‘tele’ (remote) and ‘metron’ (measure). The term usually refers to wireless data transfer, often by GSM, computer networks or SMS. |
Connectivity – prepared for the future
The advanced electronic controllers open new opportunities for remote monitoring in order to predict and optimize maintenance and avoid break-downs. The constant, automatic data collection enables analysis of GDM operation in real time and for regular follow-up. The electronic controller allows monitoring and control of all vital components to ensure constant, optimum performance, reduced down-time, substantial energy savings and long service life.
Coupled with future, advanced telemetry solutions, the advanced electronic controllers offer GDM operators online access to business critical data that can be used for a large number of efficiency measures, to predict maintenance, optimize performance, manage stock and follow-up on campaigns, promotions, etc.
Not only about temperature
When choosing a temperature control device it is important not only to consider the first cost of the component but the
additional features that can bring potential energy savings and reduction of carbon footprint. There is a clear shift in
the market towards more advanced controllers which do not only control the temperature of an appliance, but they
can manage most of the energy consuming components. At the same time, they can provide important data that can
be translated into performance, maintenance and even marketing information.
*The test was performed with the Danfoss ERC 112D controller compared to a conventional thermostat at the Danfoss facility in Baltimore, USA in an environmental chamber certified in accordance with ISO 17025. The test was performed under the following conditions:
- Door openings: 6 seconds, 6 times per hour for 8 consecutive hours
- Ambient temperature: 75°F
- Humidity: 45% RH
- Set point: 38.3°F
- Equipment Specifications:
- Compressor:
- Refrigeration Capacity: 998 kcal/hr (3960 BTU/hr)
- Voltage: 115
- Frequency: 60Hz
- Current: 8.5 Amps
- Refrigerant: R-134a
- Capillary Tube: 0.054
- Refrigerant Charge: 283g (10oz)
- Compressor:
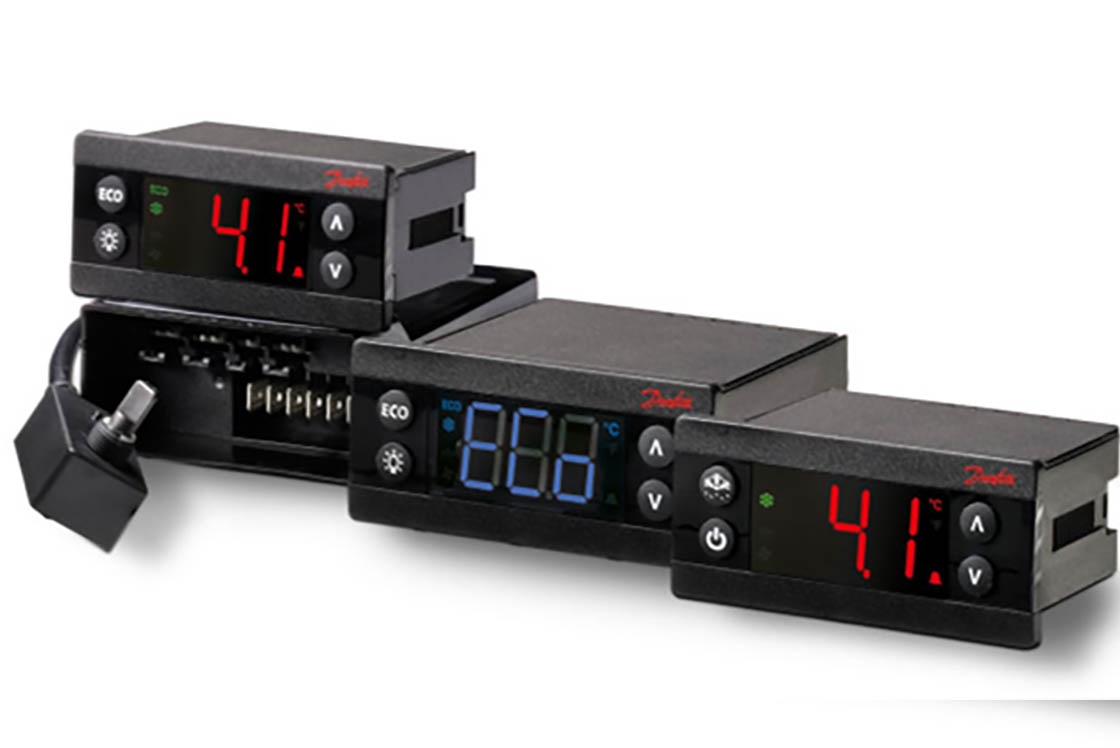