The mining industry is increasingly turning to commercial vehicle electrification solutions for the machinery used during operations because of the performance and safety benefits they offer. As well as reducing diesel emissions, introducing electric machines improves the underground environment for workers, increases production rates and saves companies significant money on machine overhead, fleet maintenance and total cost of ownership.
Growing numbers of international equipment manufacturers are showing their commitment to changing the underground mining sector for the better. One such company is Australian manufacturer Safescape, which has designed and developed innovative products for the mining industry since 2010.
In collaboration with its electrification partner 3ME Technology and Danfoss Editron, Safescape launched the Bortana EV in 2019 to meet high demand from Australian hard rock miners. Designed to handle the aggressive operating environment of underground mines, the Bortana EV is powered by a fully-electric Danfoss Editron drivetrain system.
Overcoming longstanding challenges
For decades, the vehicles used in underground mining operations in Australia have faced issues relating to corrosion, durability and the emissions they generate. Recognizing the need for a better solution, Safescape and 3ME Technology developed the Bortana EV specifically for the harsh environments of Australian mining sites.
The Bortana EV significantly reduces the mining industry’s energy usage and vehicle emissions. The vehicle tackles mining health and safety concerns head-on by producing zero emissions, reducing heat and lowering maintenance costs – all while carrying a 2.2-ton payload to handle the rigorous environment and tough underground mining duty cycles.
A compact, power-dense and highly efficient drivetrain system
Danfoss Editron first started working with 3ME Technology in 2015 as a strategic partner on electric drive technology for multiple market sectors. The two companies overcame several challenges unique to the electric vehicle industry while developing the Bortana EV. The vehicle’s entire body is galvanized to be robust enough for underground mining environments and strong enough for heavy loads. The undercarriage of the vehicle is fully sealed to protect from corrosion, extending the life of the vehicle substantially over that of current vehicles currently being used. All of the vehicle’s electronics and systems, including Danfoss Editron’s fully-electric drivetrain, were carefully selected to meet the rigorous drive cycles expected of the mining industry. They also surpass the evolving range and reliability standards demanded by mining operators. The Bortana EV was cleared for deployment underground in just three days, an unusually quick turnaround for a new battery-electric vehicle in the mining industry.
Danfoss Editron’s electric propulsion system installed in the Bortana EV comprises a 160kW motor using synchronous reluctance assisted permanent magnet technology and IP67 converter system. It has been paired with the company’s purpose built Bladevolt® battery system.
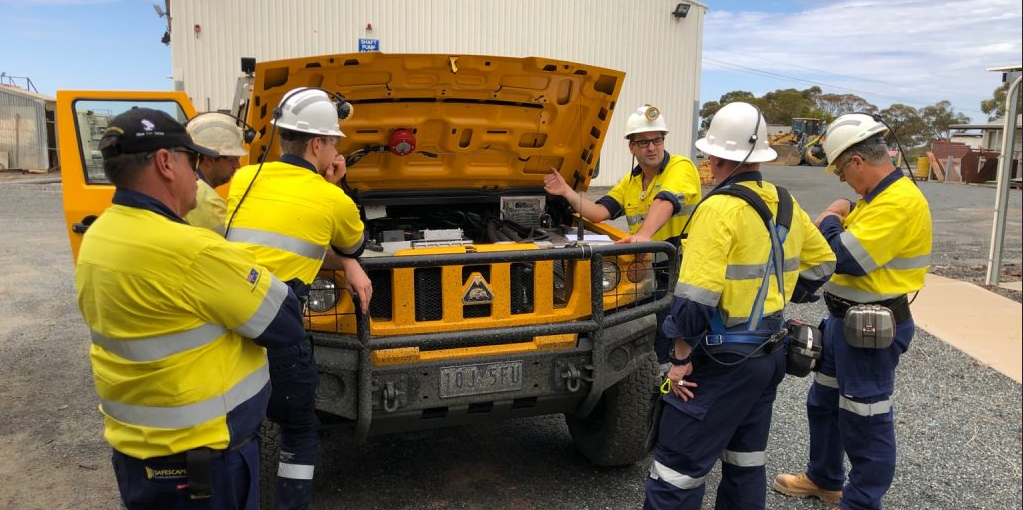
PASSING TESTS AND GETTING READY FOR COMMERCIALIZATION
Following a positive demonstration at the 2019 Austmine conference, the prototype of the Bortana EV successfully passed site trials at three hard rock mines across Australia. In a staged approach leading to full-scale production, 10 beta phase vehicles deployed across various mining applications will deliver the data required to inform fleet replacement strategies for mining companies globally. The company is already seeing major mining operators place orders to secure supplies of the Bortana EV, helping ensure they hit respective decarbonization targets.
Danfoss Editron’s VP of Editron Kimmo Rauma commented:
“Keeping safety and emissions in mind, significantly reducing the use of diesel in underground mining vehicles is a major market shift for the better. We’re looking to further this longstanding working relationship with 3ME Technology to support other OEMs as they bring electric machines and vehicles to the market quickly.”
3ME Technology’s Chief Growth Officer Steve Lawn added:
“We’re very appreciative of the relationship we have with Danfoss Editron. The company is an excellent partner and has been incredibly supportive during the system design, integration, and prototype phases. We’re looking forward to working with Danfoss Editron to support other OEM businesses to execute their electrification strategies.”
SPECIFICATIONS
Project | 3ME Technology Bortana Electric Vehicle |
Customer | 3ME Technology and Safescape |
Location | Australia |
Scope | Transforming the mining industry to electric |
Solution | Fully-electric drivetrain systems |
Technical specificities |
|
Benefits |
|