Energy efficiency in seawater reverse osmosis
Depending on local electricity costs and plant design, energy expenses can represent up to 86% of an SWRO plant’s total costs of ownership (TCO). In this article we take a look at where energy costs matter most, who should be most concerned about energy costs, what actually drives energy costs – and how you can reduce energy costs to improve an SWRO plant’s TCO.
The locations of many SWRO plants share some common characteristics. They are remote, often on islands or in coastal areas not served by major transportation links. They are not connected to large utility grids, and depend on locally produced electricity that is typically provided by generators powered by diesel fuel shipped in by sea.
If the description above applies to your SWRO plant’s location, then you probably already know that electricity costs more for your plant than it would for a similar facility that is served by better infrastructure. But did you know that it can easily cost 400% more?
According to data collected from our customers, SWRO operators in areas such as the Caribbean pay approximately USD 0.40 per kWh. Compare this to an “average” mainland price of USD 0.10 per kWh, and it is clear that energy costs matter more in some places than others.
Even on the mainland, however, energy prices vary widely depending a wide range of factors. Italians pay USD 0.21 per kWh; Spaniards pay USD 0.14. US prices averaged closer to USD 0.11 per kWh.
Given the great variety in production methods, raw materials costs, regulations, subsidies and taxation, it is difficult to agree on any kind of “average” energy cost that is applicable worldwide. Over time, nonetheless, energy prices move in one direction only – up – and reducing an SWRO’s plant’s energy consumption is a growing priority. Or is it? Even in 2014, we still see new SWRO plants that come online without energy recovery devices.
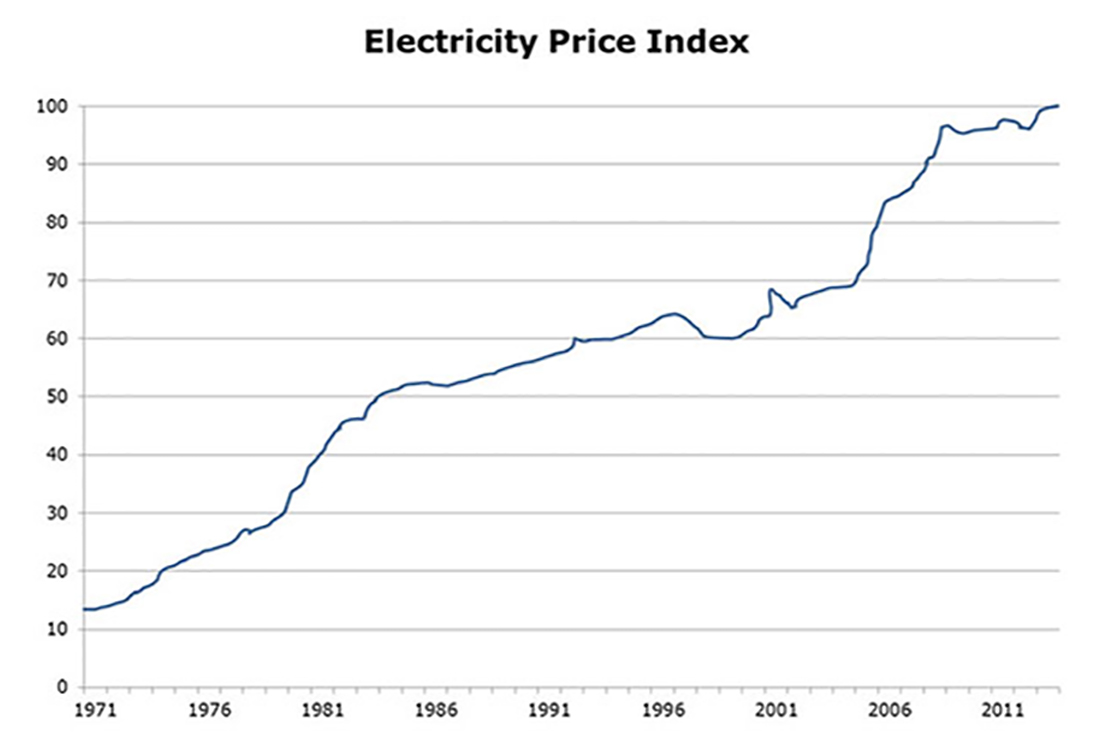
Despite the fact that energy plays such an important role in SWRO plant TCO – and any talk of CO2 reductions notwithstanding – energy conservation is a priority more for some than for others. Why? It depends on who pays for what.
Tenders are won or lost for a number of reasons. And as we all know, price is the number one reason.
If a tender for an SWRO plant is based solely on capital costs, energy efficiency may never even come into the picture. As long as an OEM bids the best initial price, the deal can be won with little or no consideration of lifetime energy costs. While this was almost always the case 10-15 years ago, even in remote areas where energy costs were then relatively high, we now see this tendency primarily in markets where energy costs are relatively low.
Tenders based on TCO, on the other hand, are different. According to our experience, all BOO and most BOOT projects in places like the Caribbean include careful consideration of energy costs over the plant’s lifetime. Of course, end users who pay for their water are also concerned about costs.
High-pressure pumps account for the single largest share of an SWRO plant’s energy bills. As a rule of thumb, a full two-thirds of a plant’s electricity costs are driven by pressurizing feed water.
Water pre- and post-treatment account for one-third of plant electricity costs.
A number of other factors also affect energy consumption, though to a lesser degree. These include equipment age and maintenance as well as filtration and membrane technology.
While plant designers and operators can do a number of things to improve overall energy efficiency, paying attention to the largest cost driver – pressurizing feed water – gives the largest payback.
Adding an energy recovery device (ERD) to a system is the single most effective fix, and most modern plants are designed around an ERD solution. Today, two ERD options are most commonly used: turbochargers and isobaric pressure exchangers. A turbocharger ERD typically saves about 40% compared to a system without ERD, while an isobaric ERD saves as much as 60% compared to a system without ERD. In other words, specifying an ERD is almost always a good idea; in locations where energy is relatively expensive, specifying an isobaric rather than a turbocharger ERD is an even better idea, since this can save an additional 30%.
New membrane designs that reduce feed pressure are also entering the scene, and are expected to save between 5-10% in energy costs.
Another major opportunity to reduce the costs of pressurizing feed water has to do with high-pressure pump technology.
Until a few years ago, SWRO plants of all sizes commonly relied on centrifugal high-pressure pumps. Recent developments in axial piston pumps, however, make this technology increasingly attractive for more and more mid-size plants with capacity up to 30,000 m3/day or more.As the graph above shows, axial piston pumps operate at 90% efficiency, whereas centrifugal pumps are always less than 80% efficient – and increasingly less so at lower flow rates.
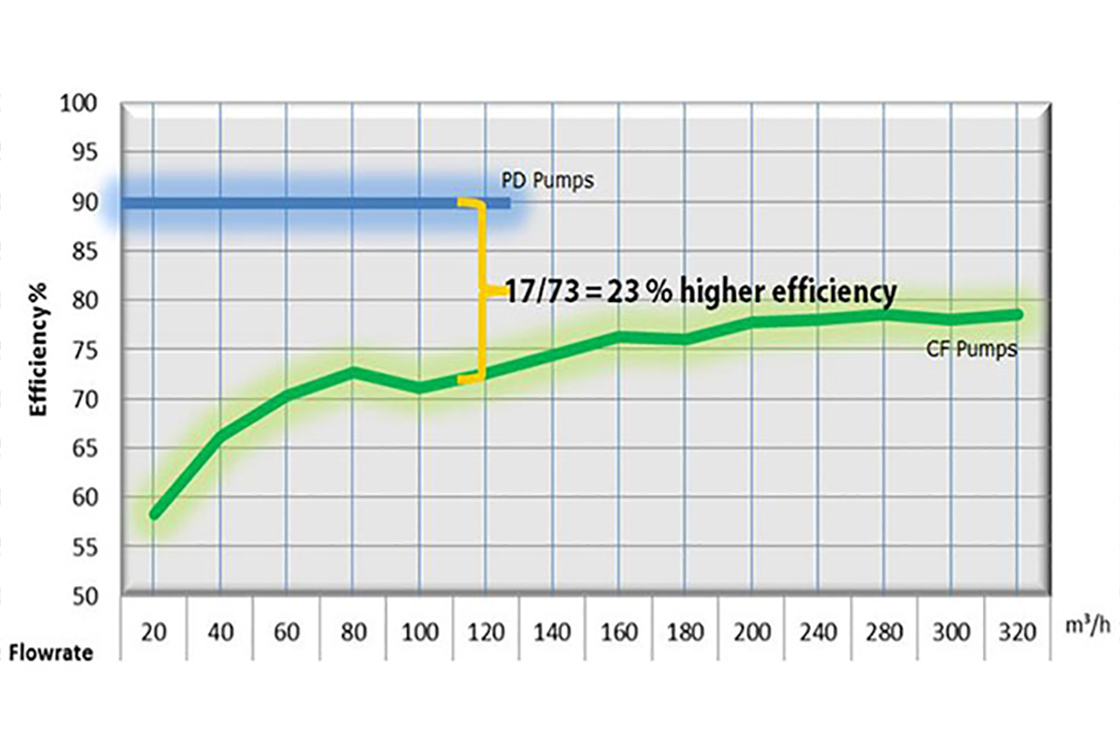
While a pump efficiency difference of 12-30% might not sound that significant to some OEM builders, BOO and end users will have a different opinion – especially when they factor in local electricity costs and plant output.
As the table below shows, a plant producing 120 m3/hour in a territory with relatively low energy costs (USD 0.10/kWh) can save USD 40,000 per year by switching to an axial piston high-pressure pump. If the same plant relies on a diesel generator for its energy supply – and pays USD 0.40/kWh – annual saving jump to USD 168,000. We’ll let you multiply these annual savings by 10 to get an idea of what improved high-pressure pump efficiency means over the course of an SWRO plant’s average lifetime.
40 m3/hour | 80m3/hour | 120m3/hour | 160m3/hour | 200m3/hour | |
Annual saving(0.1 $/kWh) | $23,500 | $30,200 | $40,000 | $47,700 | $49,800 |
Annual saving(0.4$/kWh) | $94,300 | $120,700 | $168,000 | $191,000 | $199,400 |
With savings like this, it’s no wonder that some BOOs are designing their plants as multiple-train configurations based on axial piston high-pressure pumps: in addition to significant energy savings, they get the additional benefits of system redundancy and increased uptime.
A number of factors make it is impossible to make a “one size fits all” generalization about energy’s share of a plant’s total operating costs.
Nonetheless, some simple calculations indicate that electricity is the largest variable cost, by far, and can account for as much as three-fourths or more of a plant’s total costs over a ten-year period.
As can be seen in the table below, energy’s share of total cost per m3 of produced water primarily depends on two factors: local energy costs and whether or not an ERD is used.
The table above relies on data from the Global Water Institute’s DesalData base, which places average energy costs at USD 0.06/kWh (well below 2013 rates as indicated above), while average prices in the Caribbean are closer to USD 0.40/kWh.
Using these price levels, and keeping everything else equal, we can see that electricity costs account for at least 31% of total costs per m3 (in a plant that pays USD 0.06 per kWh – and uses an ERD) and as much as 86% (in a plant that pays USD 0.40 per kWh – and does not use an ERD).
Related products
-
if (isSmallPicture) {
; } else if (isBigColumns) { } else { }High-pressure pumps for reverse osmosis applicationsHigh-pressure pumps for landbased, off-shore and marine reverse osmosis applications