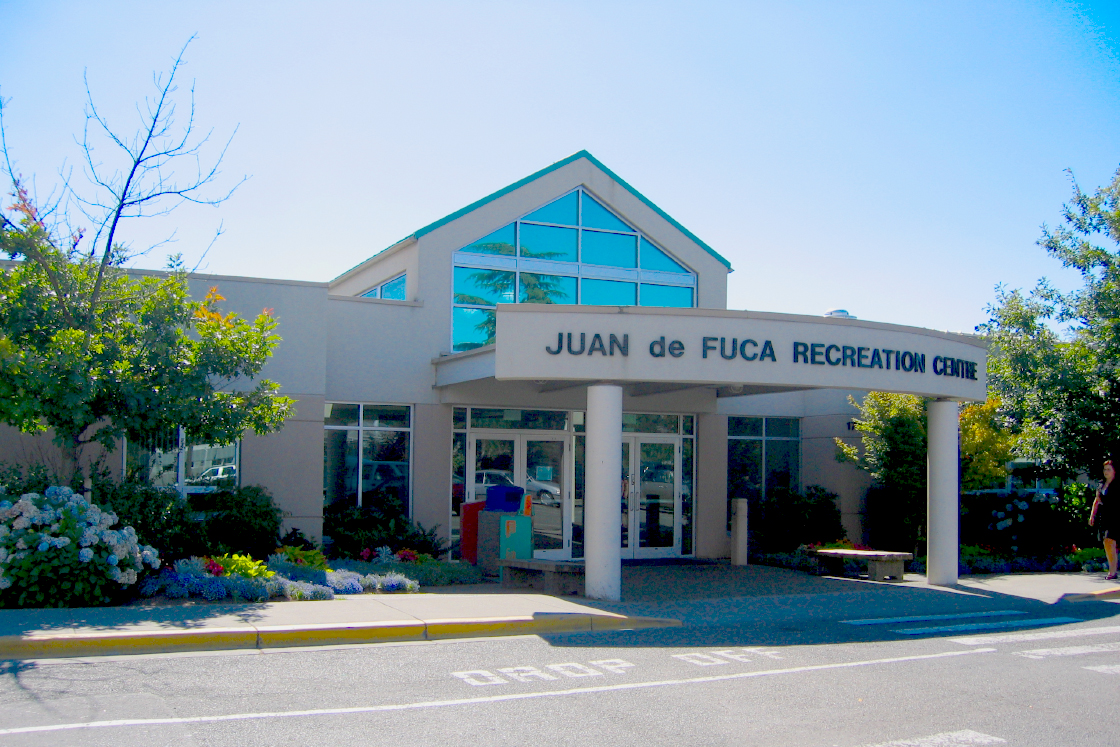
The Juan de Fuca Recreation Center (JDF) in Colwood, British Columbia is a 85,000-square foot facility containing an ice arena, pool, weight room, indoor sports complex and play area. Heating and cooling the facility with its existing gas-fired boilers required high energy usage and resulted in high levels of carbon emissions that they were looking to reduce in order to meet the sustainability goals set by the municipality; in early 2020, the town of Colwood and the province of British Columbia mandated buildings reduce their carbon emissions to achieve ambitious climate goals by 2050. The Center was also looking to reduce operating costs so they could reduce the costs of the activities offered to the community.
Additional challenges loomed in 2020; the COVID-19 pandemic resulted in greater operating expenses in order to comply with safety protocols plus an increase in the costs of labor and construction materials. JDF was searching for a cost-effective option for upgrading its HVACR system. They turned to Victoria, BC-based Polar Engineering, an engineering consulting firm specializing in industrial refrigeration and energy recovery systems. After assessing JDF’s needs and existing system, Polar proposed a custom heat pump solution with a heat recovery system that would integrate with the existing boiler. While the upgrades were expensive, Polar assisted JDF in securing federal and provincial funds available for energy efficiency retrofits in existing buildings.
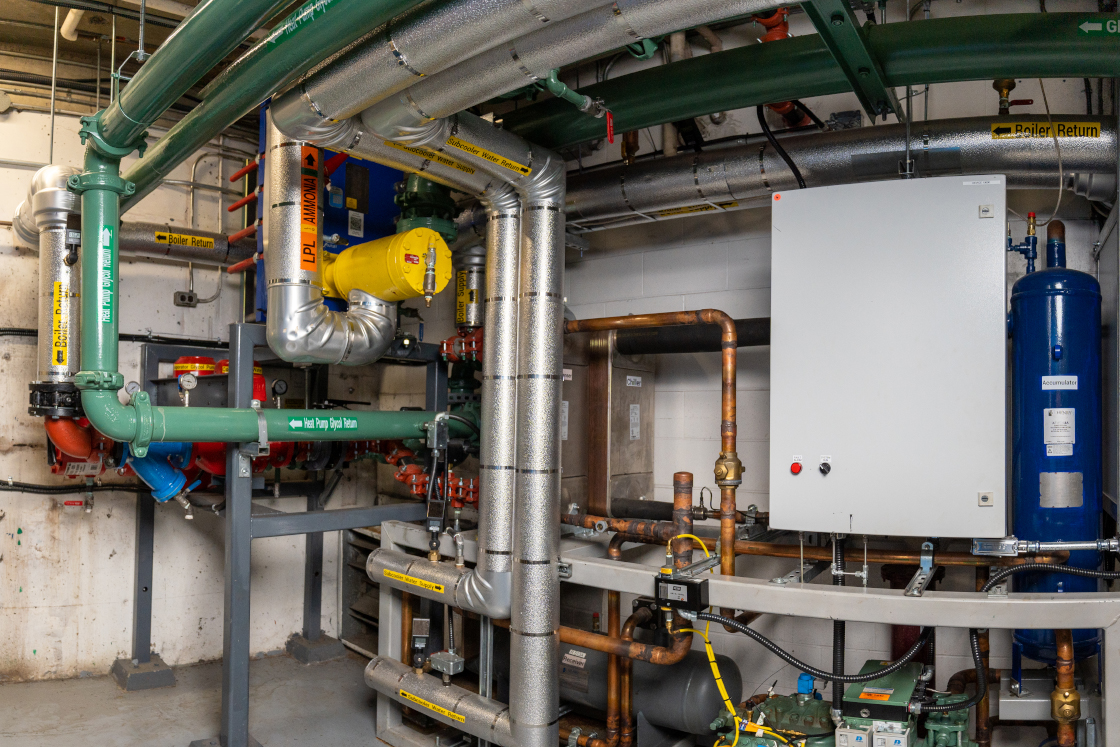
Engineering the Retrofit
Polar faced the challenge of designing a heat pump that would be effective in cold temperatures, work with a boiler, and be able to adjust to varying load requirements. In order to minimize carbon emissions and meet the requirements of the Kigali Amendment, the heat pump needed to use low-GWP refrigerants. While the boiler would provide backup on very cold days, the goal was to run the boiler as little as possible and lower natural gas usage for building and domestic hot water heating by 90%.
Polar had an established partnership with Danfoss and knew that its industrial line components and valves – solenoid, isolation, electric expansion (EEV) – would be able to provide flexibility and handle a range of operating loads and conditions. The solenoid and isolation valves provide a unique modular solution that allows flexibility in installation and repair; the bonnet can be easily switched out for another to change the functionality of the valve if needs warrant. The isolation valve, part of the SVL product line, can operate in temperatures as low as -76 to 302 degrees Fahrenheit and has a maximum working pressure of 943 psig. The Colibri EEV, a Danfoss commercial product line component, offers precise control in about one-fifth the number of steps required to travel from full open to full close, compared to other stepper valves on the market.
The result is quicker response times to the dynamic conditions often seen in heating and cooling applications. Even on the coldest days, the Danfoss components were able to effectively control the flow of refrigerant inside the heat pump, the first in Canada to use refrigerant R513.
Built by Fraser Valley Refrigeration, the heat pump was installed in late 2021. It forms a closed loop with the facility’s boiler system, with 100% redundancy. The heat pump heats the water flowing into the loop and supplies heat and hot water to the building, reaching water temperatures as high as 180 degrees Fahrenheit. Recognizing the need to be space and cost-conscious, Polar designed the heat pump to be about 50% of the size of the boiler; however, due to its superior efficiency, its output is about 80% of what the boiler can produce.
“We try to balance cost and performance; our goal is to be cost-effective while providing the best performance possible,” explained Ian Welle, Polar’s CEO. Polar also installed a subcooler that works in parallel with a reciprocating compressor to pre-heat the water in the loop via a braze-plate heat exchanger, increasing the efficiency of the heat pump by 25%. The heat pump is able to capture the rejected heat from the building’s refrigeration system and reuse that heat for the building or the hot water supply, saving even more energy and costs.
To ensure compressor longevity, Polar trusted Danfoss’ Colibri EEV to maintain a large turndown ratio and suction gas superheat. This is very important, due to a reduction in oil viscosity at high evaporating temperatures. The EEV allows the compressor to vary its speeds and modulate the capacity of the heat pump from 30-100% to match the building’s load requirements.
Reaching a Cleaner Future
The heat pump has helped JDF achieve its goals of saving energy and emissions reduction. Welle reports that the heat pump is operating well and meeting all expectations. “Even on the coldest days, the boiler is barely running,” he said. It has reduced the natural gas consumption of the facility to near-zero, reducing carbon emissions by 284 tons per year and resulting in a savings of $22,000 annually in energy costs.
Tristan Webb, maintenance supervisor at JDF, affirmed, “The project surpassed my expectations, and effectively reduced our natural gas emissions and costs to zero.”
Since the JDF installation, Polar has engineered similar heat pumps, with four already installed and three more planned in the coming months, using R515 refrigerant. They estimate a total carbon emissions reduction of 3000 tons per year. With Danfoss components becoming a standard element in their heat pump design, Welle spoke enthusiastically of the support Polar received in the development process. “The technical support and engineering expertise Danfoss provided were key to allowing us to push the envelope on energy efficiency and heat recovery. The components were critical to the success of the first low-GWP heat pump in Canada.”
“As greener solutions are being legislated and decarbonization becomes an industry driver, we are now seeing a growing focus on heat pump systems in the North American market,” said Adam Anderson, regional sales manager for industrial refrigeration at Danfoss. “At Danfoss, we take pride in global, cross-functional collaboration on applications designed to reduce global energy use and carbon emissions.”