Ammonia in industrial refrigeration
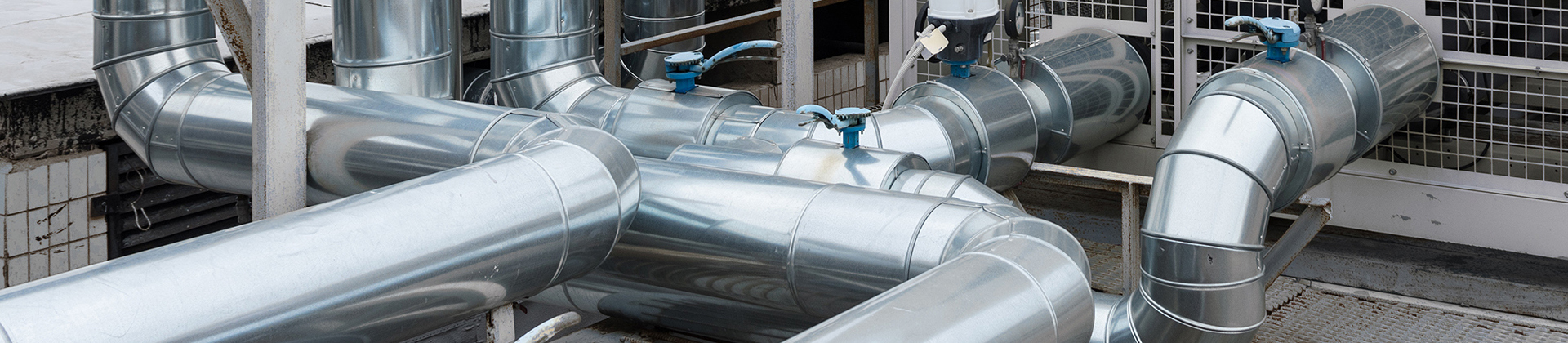
State-of-the-art components for ammonia refrigeration
Ammonia is the most trusted refrigerant right from the 19th century. All those who are involved in food preservation and industrial process plants know ammonia as refrigerant of choice due to its unmatched thermodynamic properties. You can read more about this and the many other benefits when using ammonia via the link "Why ammonia in industrial refrigeration".
While ammonia is not a universal refrigerant—mainly suitable for industrial and heavy commercial applications—and its toxicity, flammability, and material compatibility must be taken into account during system design, there is a huge global population of ammonia systems where those challenges have successfully been dealt with.
Ammonia offers a wealth of benefits for industrial refrigeration
With CFCs and other synthetic phased-out, many in the HVACR industry have looked back to natural refrigerants, including ammonia, as replacements. Ammonia has a number of benefits, which have been proven the past hundred-plus years.
Why ammonia in industrial refrigeration?
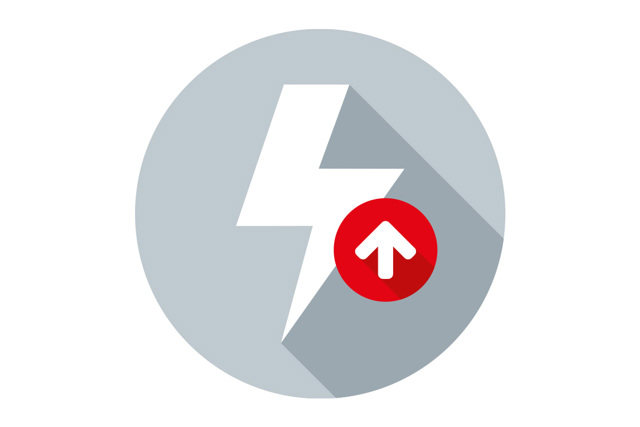
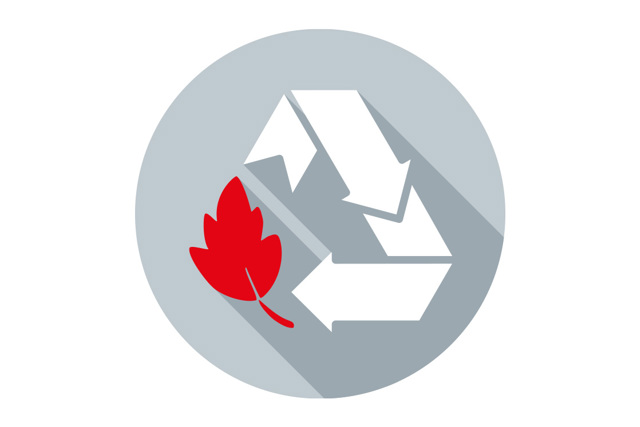
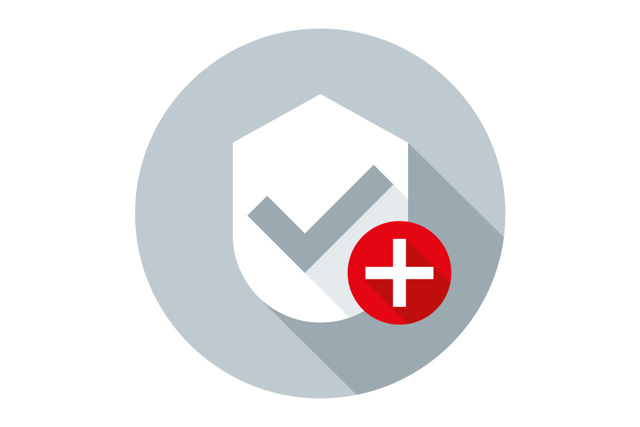
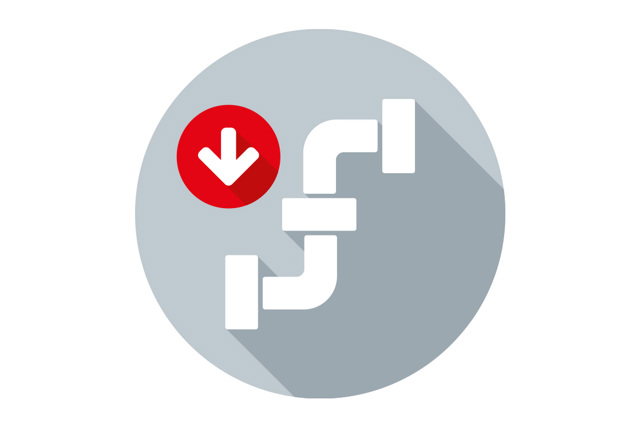
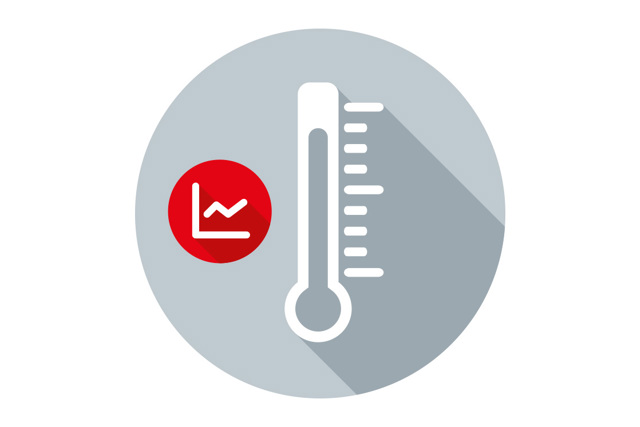
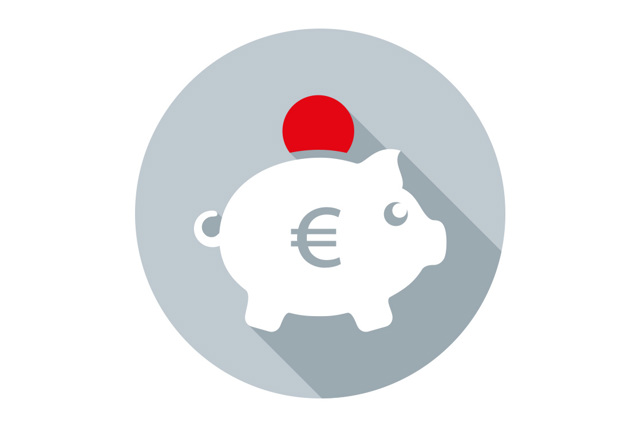
Products for ammonia
See all our products developed for industrial refrigeration and ammonia.
-
if (isSmallPicture) {
; } else if (isBigColumns) { } else { }SVL Flexline™SVL Flexline™ product platform targeted to meet industrial refrigeration requirements. The range cover five different functions with just two valve models.
-
if (isSmallPicture) {
; } else if (isBigColumns) { } else { }ICF Flexline™ valve stationUnmatched freedom is the keyword of ICF Flexline™ valve stations. As part of the Flexline™ platform, these valve stations are based on a unique modular concept.
-
if (isSmallPicture) {
; } else if (isBigColumns) { } else { }Flexline™ platformThe Flexline™ platform is synonymous with flexibility within industrial refrigeration. Based on a modular design concept, you will experience that each product features a variety of benefits, including easy selection, installation and maintenance.
-
if (isSmallPicture) {
; } else if (isBigColumns) { } else { }SVL-140B Parts programSVL Flexline™ platform is now expanding to 140 bar MWP to meet an increasing demand of large manual valves in industrial design for large scale R744 transcritical CO2 systems.
-
if (isSmallPicture) {
; } else if (isBigColumns) { } else { }ICV Flexline™ control valvesDanfoss ICV Flexline™ guarantees you a reliable, safe and green solution - both now and in the future. The product family consists of an ICS pilot operated control, ICM motor operated control and ICLX 2-step solenoid valve.
Case studies
-
if (isSmallPicture) {
; } else if (isBigColumns) { } else { }Ammonia conversion for cold storage facility is simple with ICV Flexline™Consumer retail stores are looking for tried-and-true ideas to thrive in turbulent economic times That’s why a major 190-store retail chain based in the Midwest switched to a proven refrigeration solution for one of its distribution centers - an environmentally friendly ammonia system that uses Danfoss ICV Flexline valve stations
History of Ammonia as a Refrigerant
Ammonia was first used as a refrigerant in 1876 in a vapor compression machine built by Carl Von Linde. Other refrigerants like carbon dioxide (CO2) and sulfur dioxide (SO2) were also commonly used until the 1920s.
Chlorofluorocarbons (CFCs) hit the US in the 1920s, swinging the pendulum in favor of synthetic refrigerants; compared to other refrigerants used at the time, CFCs were considered harmless and extremely stable. CFC refrigerants were promoted as safety refrigerants, resulting in high demand. Due to the success of CFCs, ammonia was looked upon less favorably, though it was still used, especially in food preservation and large industrial installations.
In the 1980s, the harmful effects of CFC refrigerants became apparent and it became generally accepted that CFCs were contributing to global warming and the depletion of the ozone layer. The result was the Montreal Protocol (1987), where nearly all countries agreed to phaseout CFCs in a timely manner. Later revisions to the Montreal Protocol and the later adoption of the Kyoto Protocol accelerated the phaseout schedule.
Today, with CFCs and many other synthetic refrigerants being no longer viable options, ammonia's popularity is growing. Once seen as a less desirable, potentially dangerous choice, today's ammonia refrigeration systems are rigorously engineered to maintain high efficiency and maximum safety.