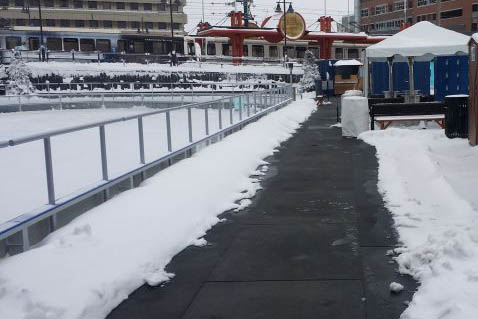
When it snows, this system melts...
According to the National Weather Service, a series of lake effect events and clipper-type systems dumped 112 inches of snow on Buffalo, New York, in the winter of 2014-15. In an area accustomed to harsh winters, this was still unusual—about 18 inches above normal. But even this impressive amount of snow was no match for the Danfoss snow melt system installed at Canalside, the heart of Buffalo’s waterfront revitalization.
For much of the 19th century, Buffalo’s Inner Harbor was one of the world’s most profitable business centers. The bustling port marked the western terminus of the Erie Canal and served as a gateway to the West. But all of this changed with the arrival of trains and automobiles in the early 20th century. Harbor activity sharply declined, and eventually, much of the site was filled in with stones and dirt to accommodate streets and parking.
In 1999, the Erie Canal Harbor Redevelopment Project outlined plans to reclaim the area for restoration. Sixteen years and more than $300 million later, the restored area encompasses Canalside, a mixed use district that reconnects downtown Buffalo to the harbor. The redeveloped center of activity includes shallow canals restored to their 1825 footprint and sidewalks where towpaths once accommodated mules that pulled barges along the canals. During the summer, residents and visitors can rent paddle boats and remote control sailboats for use on the replicated canals, while winter brings with it the opportunity to ice skate on these same waters.
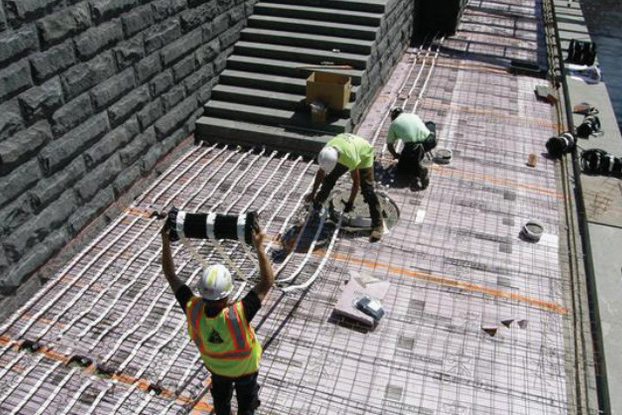
Snow melt system clears path to canals
Winter also brings snow and ice to the harbor. If the city hoped to offer ice skating on the canal, it needed to find a way to keep area sidewalks around the canals clear and dry to offer safe access to and from the skating area. That’s where the Danfoss snow melt system comes in.
Provided by Comfort Radiant Heating, LLC, Clifton, New York, and installed by O’Connell Electric Company, Inc., Victor, New York, the snow melt system uses 8,000 square feet of Danfoss GX mats and cables, 10 digital sensors and five GX 850 dual zone automatic control panels paired with five electric contactor and timer panels that control each of the system’s five zones. Danfoss provided the electrical contractor with diagrams indicating how the mats should be laid down and pairings of zones to controllers.
Because the Canalside project marked O’Connell Electric’s first experience with the snow melt system, the company hired Russ Hacker, owner of Comfort Radiant, as a consultant who could walk them through the installation process.
“We knew the first day we met Russ that this was the right product and he was the right person to help us install it properly,” said Joe Pellerite, executive vice president of operations at the electrical contracting firm. “He met with everyone involved in the project—the general contractor, masons and our electricians—to instill in them the importance of following the proper procedures during installation.”
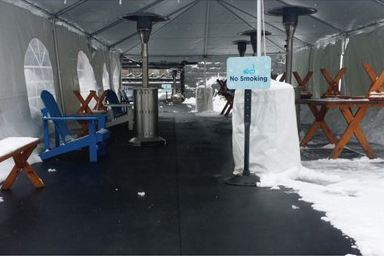
Mats and sensors embedded in concrete
Engineered for use in concrete, asphalt and under pavers, the Danfoss line voltage system consists of twin conductor heating cables and a single-point connection with a 20-foot cold lead. The system relies on digital sensors to provide precise feedback regarding precipitation and temperature and an automatic control panel that delivers total control of snow melting system set points.
The GX system is embedded during paving. Just before concrete is poured, electricians attach the mats to the reinforcement mesh that ends up in the middle of the pour. Sensors, too, are embedded in the poured concrete.
“The snow melt system was one of the highlights of the project,” said Tom Zielke, O’Connell Electric foreman. “The system was easy to install, from a product perspective. But, in order to ensure the warranty from Danfoss, testing was critical. The resistance tests alone required us to test the cables when we received them to make sure they weren’t damaged during shipment. Then, we tested them after we installed them, again as the concrete was poured and finally after the concrete was poured. In this project, the cables passed every test, which speaks to their durability and how well they are manufactured.”
Pellerite offered similar comments about the mats. “I think the beauty of the mats is how well they’re manufactured. Everything is laid out in a system and designed to meet a particular application. We were able to match up the sidewalk lengths with longer leads that we needed to hit the sensors. Danfoss provided the extra length the project required, and the mats went down extremely well, which I attribute to foresight in product design and manufacturing.”
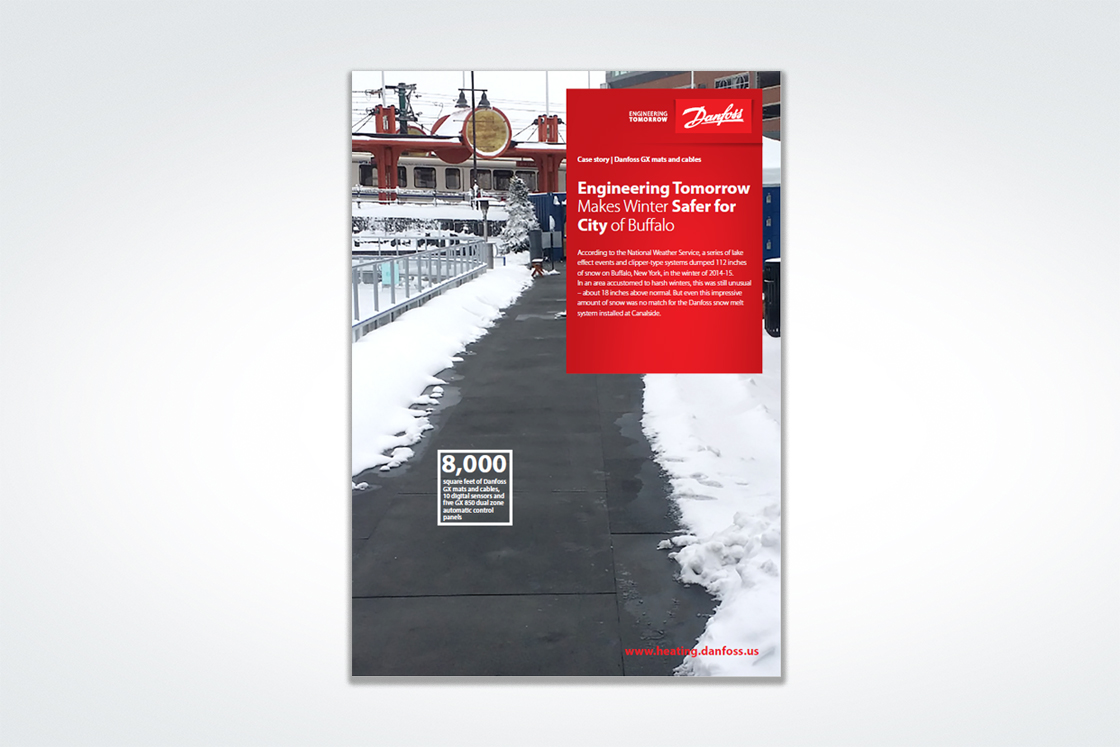