Functional safety is freedom from unacceptable risk of physical injury or of damage to the health of people. Today, people go to work expecting a safe working environment. No matter if they operate a crane to erect a new high-rise in the busy city center or pull tree trunks in the silence of the big woods, they know they have to watch out for safety issues themselves, but basically they expect a safe machine.
There is no such thing as a risk-free machine or application. Operators and bystanders working with heavy-duty and off-road machines in agriculture, construction or forestry know that they are exposed to some degree of hazard. And even when father and son stop at a road construction work to admire the excavators, they can be at risk if the machine suddenly tilts due to overload or failure of stabilizing legs or booms.
Functional safety is in the hands of machine producers, owners and operators, and even though risk cannot be eliminated, it can be brought to a tolerable level. The challenge is therefore to design a machine with a tolerable risk level.
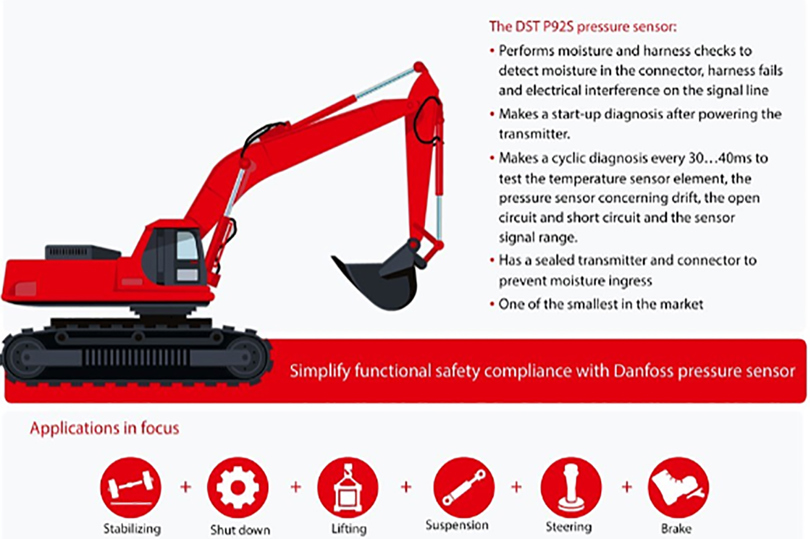
Functional Safety in machine design and building
Download and read the infographic