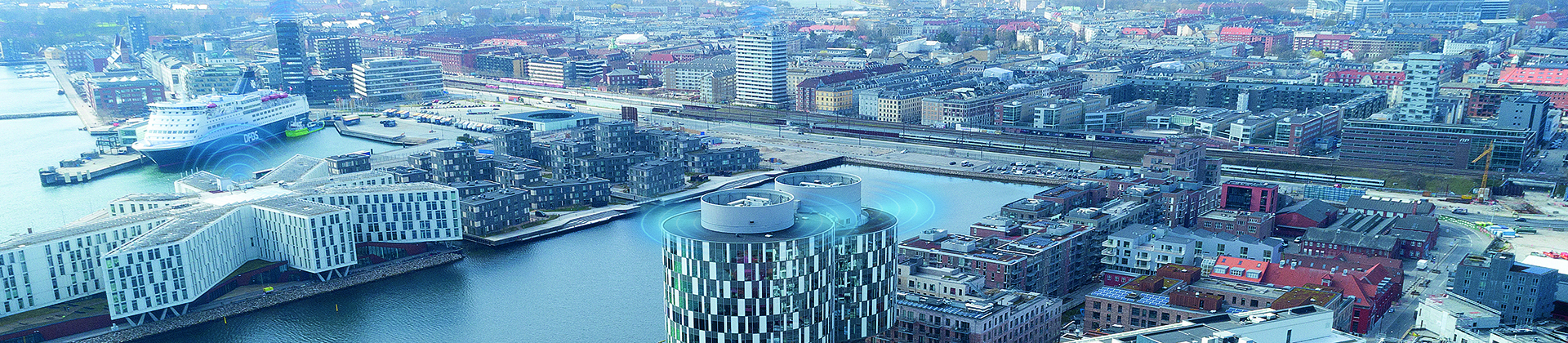
Umrichter sind mehr als einfache Drehzahlregler
Umrichter können als Sensoren und Sensor-Hubs Verbindungen herstellen, Daten verarbeiten, speichern und analysieren. Damit sind sie wichtige Bestandteile moderner Automatisierungs- und Gebäudemanagementsysteme (BMS). Dank der integrierten Condition Monitoring-Funktionen können Wartungsarbeiten wie die Condition Based Maintenance auf völlig neue Arten durchgeführt werden.
Die Entwicklung industrieller Automatisierungssysteme
Mit dem Übergang in das neue Jahrtausend haben wir einen tiefgreifenden technologischen Wandel erlebt, der letztlich zu einer völlig neuen Arbeitsweise in einer digitalen Welt führt.
Die vierte industrielle Revolution ist das Ergebnis einer Vernetzung von Computern, Menschen und Geräten, die durch Daten und maschinelles Lernen vorangetrieben wird. Obwohl der Begriff „Industrie 4.0“ recht vage ist, könnte eine mögliche Definition
Trends bei Automatisierungssystemen der Industrie 4.0
Industrie 4.0 wirkt sich auf Motorsysteme und Gebäudemanagementsysteme in Form einer Migration von der „Automatisierungspyramide“ hin zu „vernetzten Systemen“ aus. Das bedeutet, dass verschiedene Systemelemente
In einem Automatisierungsnetzwerk entstehen enorme Datenmengen. Da Daten vornehmlich von Sensoren erfasst werden, nimmt deren Zahl in modernen Automatisierungssystemen zu.
Moderne Frequenzumrichter eröffnen neue Möglichkeiten im Automatisierungsnetzwerk der Industrie 4.0 sowie in Gebäudemanagementsystemen. Üblicherweise galten Umrichter als Drehzahlregler zur Geschwindigkeitssteuerung bei Motoren, Lüftern, Transportbändern und/oder Pumpen. Heute
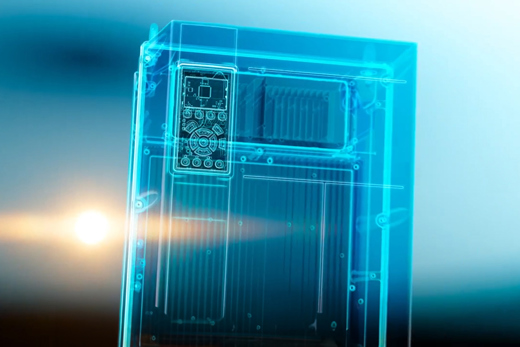
Was ist ein intelligenter Umrichter?
Im Netzwerk von Industrie 4.0 spielt der Umrichter eine wichtige Rolle und zeichnet sich durch einige Zusatzfunktionen aus:
Sichere Verbindung: Der Umrichter lässt sich sicher mit anderen Elementen verbinden. Andere Elemente im Netzwerk können Antriebe, Steuerungen, Sensoren oder eine Cloud sein. Der Umrichter funktioniert als Sensor: Der Frequenzumrichter analysiert die Motornennstrom- und -spannungscharakteristika, um die Motor- und Anwendungsleistung zu erfassen. Der Umrichter funktioniert als Sensor-Hub: Er erfasst Daten von externen Sensoren, die sich auf den vom Frequenzumrichter gesteuerten Prozess beziehen. Der Umrichter funktioniert als Regler: Der elektronische Drehzahlregler kann die SPS ersetzen, wenn die Anwendungsbeschränkungen dies zulassen. „Bring your own device“-Konzept: Kabellose Verbindung zu intelligenten Geräten (Smartphone, Tablet).
Die Informationen aus dem Umrichter können wie folgt definiert werden:
Sofortige Signale: Signale, die direkt vom Umrichter über eingebaute Sensoren gemessen werden. Daten wie Motornennstrom, -spannung, Antriebstemperatur und deren Ableitungen, beispielsweise Leistung als Multiplikation von Strom mit Spannung oder Motordrehmoment. Darüber hinaus kann man den Umrichter als Hub für den Anschluss externer Sensoren verwenden, die verzögerungsfreie Signale liefern. Verarbeitete Signale: Daten, die aus den verzögerungsfreien Signalen abgeleitet werden. Zum Beispiel die statistische Verteilung (Maximal-, Minimal-, Mittel- und Standardabweichungswerte), Frequenzbereichsanalysen oder Einsatzprofilindikatoren. Analysesignale: Signale, die Hinweise auf den Zustand von Umrichter, Motor und Anwendung geben. Die Signale werden verwendet, um Wartungsarbeiten zu veranlassen oder das Systemdesign zu optimieren.
Durch Analyse der Motornennstromsignatur kann der Umrichter den Zustand des Motors und der Anwendung überwachen. Externe Sensoren werden damit oft überflüssig. Fehlersignaturen können frühzeitig festgestellt und behoben werden. So können mit der Technologie Kavitationen und Wicklungsfehler bereits im Voraus sowie Exzentrizität mechanischer Lasten gefunden werden.
Das
Condition Based Maintenance und andere Wartungsstrategien
Es gibt folgende Wartungsstrategien:
Korrektive Wartung: Das Produkt wird nach einem Fehler ausgetauscht. Präventive Instandhaltung: Das Produkt wird vorsorglich auf Basis eines Wartungsplans ausgetauscht, obwohl es keine Hinweise auf einen bevorstehenden Fehler gibt. Contition Based Maintenance: Das Produkt gibt eine Warnmeldung aus, wenn die aktuelle Lebensdauer von der erwarteten Lebensdauer abweicht. Mögliche Ursachen werden dabei angegeben. Predictive Maintenance: Das Produkt warnt, bevor die geplanten Betriebsstunden erreicht sind, um eine Wartungsaktion zu initiieren.
Warum ist zustandsorientierte Wartung erforderlich?
Korrektive und präventive Instandhaltung hängen von Fehlern (Ereignissen) oder Zeit ab. Dabei erfolgen die Wartungsmaßnahmen im Falle von Fehlern (korrektiv) oder nach Ablauf vordefinierter Betriebsstunden (präventiv). Für diese Arten der Wartung wird kein Feedback aus der eigentlichen Anwendung herangezogen.
Dank der Einführung von Industrie 4.0 und der Verfügbarkeit von Sensordaten, ist nun bedingungsbasierte und
Überblick über Condition Based Maintenance und deren Vorteile
Condition Based Maintenance ist die einfachste und intuitivste Wartungstechnik. Sie basiert auf Daten aus der Anwendung selbst. Die erfassten Daten dienen zur Zustandsüberwachung der Anlagen. Zu diesem Zweck werden Schlüsselparameter als Indikatoren definiert. So ist es möglich, entstehende Fehler frühzeitig zu identifizieren. Der Zustand einer Baugruppe verschlechtert sich in der Regel mit der Zeit. Dies wird durch die P-F-Kurve veranschaulicht, die ein typisches Verfallsmuster zeigt. Erfüllt eine Anlage die vorgesehene Funktion nicht mehr, kommt es zu Ausfällen. Die Idee der Condition Based Maintenance besteht darin, den potenziellen Ausfall zu erkennen, bevor eine tatsächliche Fehlfunktion auftritt.
Vorteile der Planung von Wartungsaktionen
- Reduzierung der Ausfallzeiten
- Beseitigung unerwarteter Produktionsunterbrechungen
- Wartungsoptimierung
- Verkleinerung des Ersatzteillagers
Condition Monitoring-Funktionen für Antriebe mit variabler Drehzahl
Ein wesentlicher Teil der zustandsorientierten Wartung ist die Überwachung des Anlagenzustands. Bei Anwendungen mit variabler Drehzahl hängt der Zustand der Anwendung oft von der Geschwindigkeit ab. Zum Beispiel nimmt der Schwingungspegel bei höheren Geschwindigkeiten zu, wobei der Zusammenhang zwischen den beiden Werten nicht linear ist. Tatsächlich können bei bestimmten Geschwindigkeiten Resonanzen auftreten und wieder verschwinden, wenn die Geschwindigkeit erhöht wird.
Die Verwendung eines unabhängigen Systems zur Zustandsüberwachung einer Anwendung mit variabler Drehzahl ist schwierig, da die Drehzahl und der damit korrelierende Überwachungswert bekannt sein müssen.
Das Condition Monitoring folgt einem dreistufigen Verfahren:
Im CBM White Paper und im Video mehr erfahren
Umrichter sind heute mehr als nur einfache Drehzahlregler. Sie können als Sensoren und Sensoren-Hubs Verbindungen herstellen, Daten verarbeiten, speichern und analysieren und sind damit wichtige Elemente in Automatisierungssystemen.
Umrichter sind in vielen Automatisierungsanlagen bereits vorhanden und bieten eine gute Möglichkeit für ein Upgrade auf Industrie 4.0.
Dies ermöglicht neue Wege der Wartung, wie z. B. die zustandsorientierte Wartung. Die Funktionen
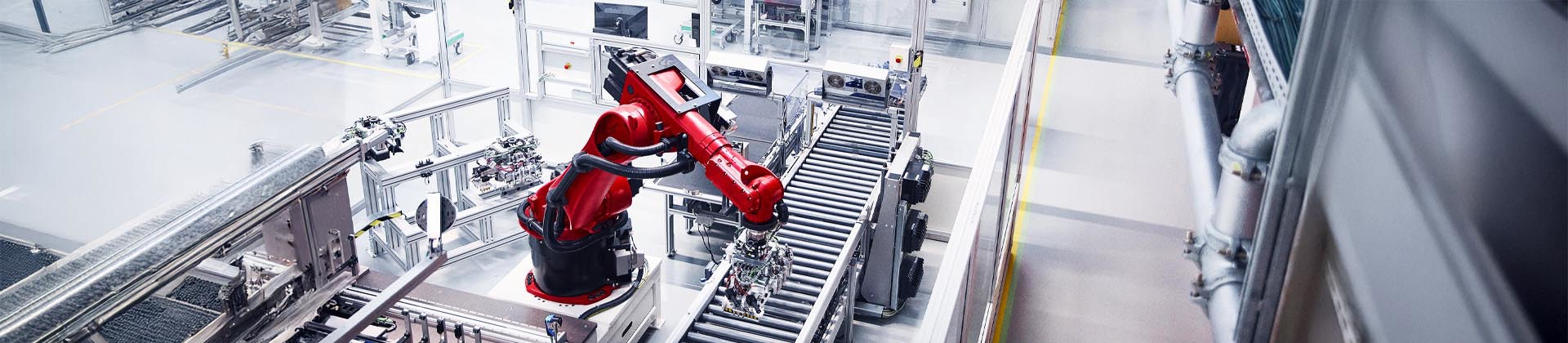
Erste Innovationen von Danfoss
CMB entstand aus einer Reihe von ersten Innovationen bei Danfoss. Danfoss strebt danach, sich von Mitbewerbern im Markt durch intelligten Funktionen im Umrichter zu unterscheiden, um die erforderlichen externen Komponenten zu reduzieren.
Treffen Sie uns auf der drinktec 2025
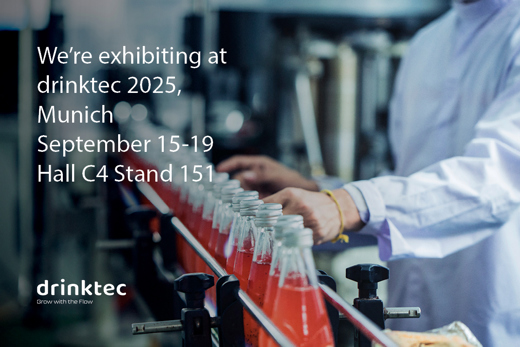
Die Zukunft der Getränkeproduktion gestalten – Gemeinsam auf der drinktec 2025
Nach drei Jahren versammelt sich die Getränkeindustrie wieder auf der drinktec in München. Besuchen Sie uns dort und sprechen Sie mit unseren Danfoss-Experten über unsere neuesten Lösungen für gesteigerte Produktivität und Nachhaltigkeit in Ihrer Anlage. Wir freuen uns, Sie vom 15. bis 19. September an unserem Stand C4.151 zu treffen!
Hervorgehobene Produkte
Danfoss Produkte mit Condition Monitoring
-
if (isSmallPicture) {
; } else if (isBigColumns) { } else { }VLT® AQUA Drive als netzrückwirkungsfreier Passive Low Harmonic DriveDie Wasserversorgung stellt besondere Anforderungen an die Antriebe. Danfoss Drives hat einen neuen passiven Low-Harmonic-Drive mit VLT® AUQA Drive, der nahezu netzneutral arbeitet.
-
if (isSmallPicture) {
; } else if (isBigColumns) { } else { }VACON® 100 FLOWDer VACON® 100 FLOW ist ein Frequenzumrichter, der in industriellen Pumpen- und Lüfteranwendungen die Durchflussregelung verbessert und Energie einspart. Zu seinen speziell angepassten Funktionen zählen Mehrpumpenlösungen.
-
if (isSmallPicture) {
; } else if (isBigColumns) { } else { }VACON® 100 INDUSTRIALDer VACON® 100 INDUSTRIAL enthält eine Vielzahl Funktionen und ist für eine große Bandbreite an Anwendungen mit konstanten Leistungs-/Drehmomentanforderungen geeignet. Die einfach zu bedienenden und robusten Motorsteuerungen erhöhen die Zuverlässigkeit und Effizienz
-
if (isSmallPicture) {
; } else if (isBigColumns) { } else { }VLT® HVAC Drive FC 102Der robuste und intelligente Frequenzumrichter FC102 optimiert Pumpen- und Lüfteranwendungen in Gebäudemanagementsystemen und lässt sich in den meisten Klimazonen im Freien einsetzen.