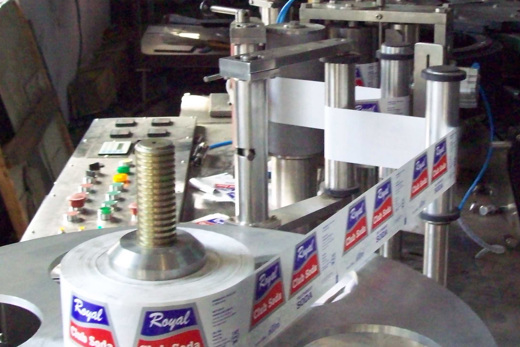
Hymech Engineers Ltd., Andheri, Mumbai, India has since 1975 provided equipment for the beverage industry. The company has since the year 2000 used Danfoss VLT® frequency converters in their machines – like in bottle fillers, hot melt machines, labelers etc.
In the labeler is used a 2.2 kW VLT® AutomationDrive to run a rotating cutter.
The cutter drive works as master drive. Incremental encoders with 2500 PPR are mounted directly on the cutter roller and on the feed roller, operated by a 1.5kW VLT® AutomationDrive with a VLT® Synchronising Controller MCO 305, so a gear ratio is calculated between the two.
Before: Fixed Label Length
Before Danfoss installed the VLT® solution, the labeller was operated with a servo installation. A PLC synchronized the machine through encoder signals and start stop signals to the servo drive. In that system, the labels were cut on the basis of inputs from print mark and zero mark feedback only. This way label length cannot be changed, and if marker signals were misaligned or the signal was lost, then the cutting length changed.
With the VLT® solution mechanical measurements of the roller diameter as well as mechanical deviations can then be removed. On the cutter roller a zero mark sensor is mounted, and on the feed roller a print marker sensor.
Free to Change Speed
The speed of the cutter is remotely controlled by a potentiometer from a remote station. The “follower” drive will adjust its speed to that of the cutter and have similar accelerations and decelerations.
The follower drive synchronizes with the master and then superimposed with zero mark and print mark sensor. This is done with external marker synchronization. Since not all labels have the same length, this variable should be adjusted from the LCP.
The calculations that adjust the synchronization ratio between roller and cutter are performed by the synchronization program in the VLT® Motion Control Option. Hence, follower speed will vary with the master speed as per label length.
Quick Syncronizing
Due to the external marker synchronisation, the follower should start when receiving the zero-signal from the master drive sensor and then catch the master speed as well as keep the print mark sensor, which is mounted on roller, aligned with the master sensor signals. Normally the system will pass two or three labels before it is synchronized.
Once the marker synchronization is done, operators are free to change machine speed without wasting labels. The machine can label 100 bottles per minute.
Saves Cost
The PLC and servo set up cost about 40% more than the VLT® AutomationDrive and Synchronising solution - and the cutting accuracy reached 1.0 mm to 1.5 mm throughout the machine speed.
Customer benefits:
- Better accuracy
- Higher speed
- Less cost