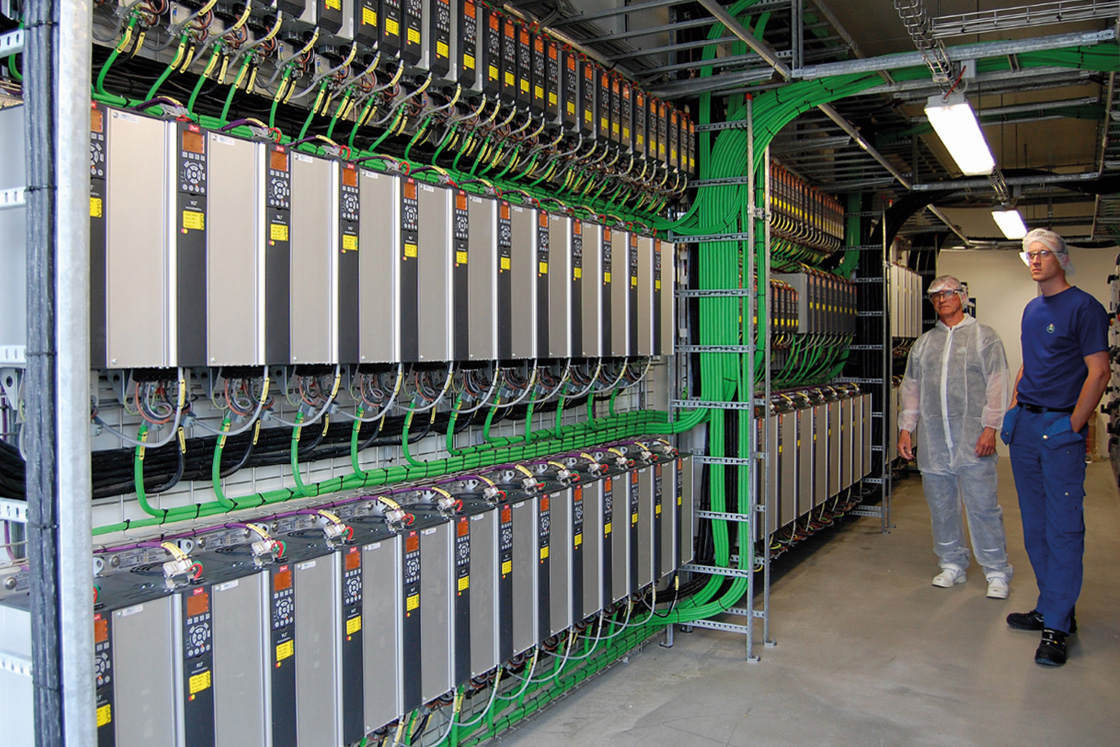
VLT®-Antriebe sorgen für maximale Verfügbarkeit, hohe Präzision und reduzieren den Energiebedarf von Arla – wovon auch Endkunden profitieren.
Bei Arla Foods Ingredients ist der Endverbraucher die kommende Generation; aber davor kommt erst noch der Hersteller von Babynahrung. Die neue Anlage, die für Säuglingsanfangsnahrung geeignetes Laktosepulver liefert, mit einem höheren Laktosegehalt als bisher möglich, erhöht die Laktoseproduktion im Arla Videbæk-Werk in Dänemark um das Vierfache, wobei dank VLT® AutomationDrive dennoch Energieeinsparungen erzielt werden können.
Energieverbrauch drastisch senken
Die neue Lactose-Fabrik von Arla Foods Ingredients mit einer Kapazität von 80.000 Tonnen pro Tag trägt dazu bei, den gesamten Kundenprozess umzubauen. Hochwertige Säuglingsanfangsnahrung kann damit sofort mit anderen Zutaten kombiniert werden. Um dies zu erreichen, garantiert Arla ein Höchstmaß an Qualität und Lebensmittelsicherheit, wobei ein straffer Prozess mit höchst präziser Kontrolle zum Einsatz kommt. Lebensmittelproduzenten erreichen enorme Energieeinsparungen, indem sie den gesamten Misch- und Verdunstungszyklus eliminieren, zum Beispiel bei der Herstellung von Babynahrung oder Energiegetränken.
Die Herausforderung für Arla besteht darin, in der Säuglingsnahrung-Laktoseanlage eine hohe Qualität und ein jährliches Volumen von 80.000 Tonnen zu erreichen, und gleichzeitig die immer ehrgeizigeren Ziele auf der Grundlage des CO2-Fußabdrucks zu erreichen, und zwar:
· Wasserverbrauch senken: weniger Liter pro kg erzeugtes Pulver
· Energieverbrauch reduzieren: weniger kWh pro kg erzeugtes Pulver
In der eigenen Fabrik reduziert Arla den Energieverbrauch um 5-15% durch den Einsatz von VLT®-Antrieben für jede Pumpe und jeden Lüfter im Vergleich zum DOL-Betrieb (Direct Online).
Motoren machen einen großen Teil des gesamten Energieverbrauchs in der Anlage aus. Daher liegt der Fokus auf der Effizienzklasse und die weitere Optimierung durch die Motorsteuerung über VLT®-Frequenzumrichter.
„Alle unsere Motoren sind asynchron. Wir beachten die Ökodesign-Richtlinie und spezifizieren IE3- oder IE4-Motoren. Wir wählen den besten Motor für die Aufgabe aus, um die Anforderungen zu erfüllen, aber nicht zu übertreffen. Wir haben im FC 302 mit der Funktion Advanced Energy Optimization (AEO) begonnen, um den Energieverbrauch zu optimieren, und messen den Verbrauch über PROFIBUS. Normalerweise müssen wir jedoch die Leistung der gesamten Anlage und nicht nur des Frequenzumrichters messen. Dies erreichen wir durch Energiemessung für jeden Kontrollraum. In Zukunft wird die neue aufkommende Carbon-Desktop-Plattform von Arla den gesamten Energieverbrauch auf Komponentenebene messen - einschließlich VLT®-Frequenzumrichter. "
Ein Antrieb in der gesamten Anlage
„Soweit möglich steuern VLT® AutomationDrive-Frequenzumrichter alle unsere Motoren. Es gibt einige sehr gute Gründe “, erklärt Knud Rahbek:
„Wir gewöhnen uns an diesen Frequenzumrichter und werden äußerst kompetent bei der Nutzung seiner Fähigkeiten. Wir glauben nicht, alle Funktionen des Frequenzumrichters nutzen zu können, wenn wir den Antrieb nicht sehr gut kennen. Infolgedessen sind einige unserer Elektriker unglaublich schlau geworden, die PROFIBUS-Kommunikation optimal zu nutzen. Unser Team hat keine Angst, den Frequenzumrichter zu parametrieren und zu optimieren. Er hat eine intuitive Benutzeroberfläche.“
„Zudem ist die Schulung neuer Mitarbeiter viel einfacher, wenn nur ein System erlernt werden muss. Neue Elektriker in unserem Team haben die Chance, anfangs einem Teammitglied zu folgen. Dann erhalten sie die Aufgabe, die Parameterliste für 15-20 Antriebe gleichzeitig unter Aufsicht zu erstellen. Dies ist eine echte Betriebssituation, es muss richtig funktionieren und der Druck ist vorhanden. Wenn der Elektriker einen Fehler macht, muss er ihn selbst finden,“ erläutert Knud Rahbek weiter.
Und Wartungsleiter Simon Arentoft ergänzt:
„Wir haben eine Anlaufstelle für Antriebe und wissen, wen wir in einer dringenden Situation anrufen müssen. Wir können uns darauf verlassen, dass Danfoss schnell reagiert, was bedeutet, dass wir schnell reagieren können, um Produktionsverzögerungen im Problemfall zu vermeiden. “
Effiziente Ersatzteilhaltung
Ein im gesamten Werk installierten Antriebstyp - dem FC 302 - reduziert die Ersatzteillogistik auf das absolute Minimum. Ein unglaublich schlanker Bestand von nur acht Einheiten, einer für jede Gerätegröße bis 90 kW, deckt die gesamte installierte Basis von 1400 Frequenzumrichtern ab. Verständlicherweise sind die Lagerkosten im Verhältnis zum installierten Volumen bemerkenswert niedrig. Der Lagerbestand reicht aus, um ein Laufwerk auszutauschen, die Reparatur vor Ort durchzuführen und in der Freizeit genau das richtige Ersatzlaufwerk zu bestellen.
Niemals aufhören!
Eine grundlegende Anforderung an den Betrieb von Arla ist die Vermeidung von Ausfallzeiten. Trotzdem ist der Austausch eines Frequenzumrichters mit niedriger bis mittlerer Leistung nicht durch Redundanz abgedeckt. Ein Laufwerkwechsel dauert 20 Minuten, während die Produktion mit einem geringfügig reduzierten Volumen fortgesetzt wird. Das ist dennoch deutlich kostengünstiger, als der Betrieb redundanter Einheiten.
Trotzdem ist der Produktionsstopp für den Austausch von Hochleistungsantrieben, wie zum Beispiel der Steuerung der großen Lüftungsturmventilatoren, unvermeidlich.
„Der Austausch von Einheiten, die größer als 90 kW sind, wird gemäß Servicevertrag von einem Techniker im 24-Stunden-Bereitschaftsdienst abgedeckt. In den letzten vier Jahren hatten wir jedoch keinen einzigen dringenden Service-Anruf “, schmunzelt Simon Arentoft.
Die bisherigen Erfahrungen zeigen, dass die anlagenweite Verfügbarkeit von FC 302-Antrieben aufgrund der Vorteile der Motorschutzfunktionen die Betriebszeit verbessert. Die Strategie der Installation von Antrieben in Kontrollräumen anstelle von Schaltschränken trägt auch zu einer zuverlässigen Betriebszeit bei und reduziert den Energieverbrauch. Bei der Montage in Kontrollräumen ist der FC 302 leicht zu lüften und hat eine längere Lebensdauer - und ist für Servicetechniker leicht zugänglich.
DrivePro®-Servicevertrag
Der interne Service wird von einem Team von 30 erfahrenen Technikern ausgeführt, die durch einen Danfoss-Servicevertrag ergänzt werden. Knud Rahbek betont, dass das 100% ige Vertrauen auf die schnelle Reaktion eines Servicetechnikers bei Problemen von entscheidender Bedeutung ist. Daher fordert und erhält Arla ein hohes Serviceniveau von Danfoss, das im gegenseitigen Servicevertrag niedergelegt ist.
Rahmendaten:
• Regelmäßige Serviceüberprüfung aller Frequenzumrichter einschließlich der Datenübertragung zum LCP
• Rabatt auf Danfoss-Schulungen für Arla-Mitarbeiter
• 24-Stunden-Bereitschaftstechniker für dringende Anfragen
• 24-Stunden-Lieferservice für Ersatzlaufwerke
Arla Foods Ingredients Group
Die Laktosefabrik in Videbæk, Dänemark, verbraucht jährlich 120 GWh Strom. Daher ist die jährliche Energieeinsparung von 15% bei den Energiekosten von großer Bedeutung.
Installiert sind 1400 Danfoss VLT® AutomationDrive FC 302-Einheiten mit einer Nennleistung von 0,37 bis 630 kW.
Höchste Qualität zahlt sich aus
Arla Premium-Laktose übertrifft sogar die strengsten internationalen Qualitätsstandards und gewährleistet jederzeit Lebensmittelsicherheit. Trockenmischungs-Laktose senkt die Produktionskosten für Endanwender effektiv und bietet gleichzeitig eine große Produktionsflexibilität, die die Endbenutzerkapazität um bis zu 25% erhöht. Durch die hocheffizienten Produktionsprozesse werden diese spürbaren Vorteile vollständig CO2-neutral erzielt.