Bryggeriet såg renoveringen av sitt 27 år gamla industriella kylsystem som en möjlighet att förenkla arbetet, förbättra säkerheten och minska CO₂-utsläppen. Men de stod inför en utmaning. Deras befintliga anläggning var fortsatt viktig för det dagliga arbetet, så att stänga ner i veckor eller månader var inget alternativ.
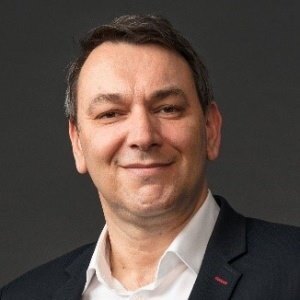
Gammal teknik innebär risker vi inte har råd med. Vi litar på att Danfoss levererar de innovativa lösningar av hög kvalitet som våra kunder efterfrågar.
Utmaningen: samtidig eftermontering och drift
Under dessa förhållanden vände sig bryggeriet till sin betrodda lokala entreprenör Frigotehnica Industrial, en del av VINCI Energies, för att få hjälp med konstruktionen. För det första var bryggeriet särskilt oroade över driftsäkerheten för sitt befintliga system. För det andra krävdes frekvent service av de omständliga ventilerna för ammoniakreglering. Slutligen försvårade nätverket av rör, som ursprungligen byggdes 1997 och delvis utvidgades 2007, underhållet ytterligare.
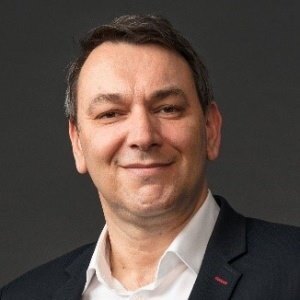
"Om man kräver stor rörlighet och inte har råd med misstag eller förseningar är ICF-ventilstationer oumbärliga. Vi ser enklare installationer, färre fel och lägre underhållskostnader. Kunderna uppskattar det minskade utrymmesbehovet och de operativa besparingarna från koldioxidavskiljning."
Lösningen: ICF-ventilstationer
För att ta itu med den unika projektsituationen föreslog Frigotehnicas konstruktionsexperter en enkel och effektiv lösning – nya ICF-ventilstationer från Danfoss. För att möta dessa behov installerade Frigotehnica den senaste tekniken från Danfoss – ICF-ventilstationer – kända för att möjliggöra snabb installation och enkel drift. Med denna omfattande uppgradering kunde kunden dra fördel av den senaste tekniken, utöka sin kylkapacitet och förbättra sitt CO₂-avtryck.
Resultatet: en betrodd lösning och implementering
Bryggeriets innovativa och miljövänliga tillämpning har tagits emot väl av medarbetarna. Det omdesignade systemet inkluderar en 120 ICF-ventilstation och minskar antalet lödsektioner från åtta till två. Dessutom finns det 73 % färre svetspunkter, från 1 164 till 308. Installationen utfördes under kalla förhållanden medan enheten förblev i drift, vilket orsakade minimala störningar i den dagliga verksamheten. Endast ett större stopp av kylanläggningen behövdes, så att bryggeriet kunde fortsätta sin normala verksamhet. Resultatet blev 30 % mindre stilleståndstid för bryggeriets eftermontering.