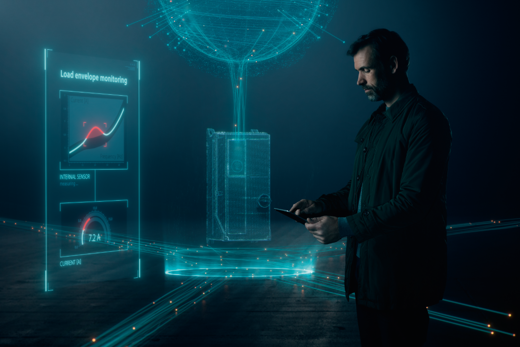
Corona-bedingt lassen viele Unternehmen in diesen Wochen ihre Produktionsanlagen warten und fit für den Neuanlauf machen. Hintergrund: In der Industrie sind nur wenige Antriebssysteme mit High-End-Condition-Monitoring-Software überwacht. Doch es gibt Alternativen, die dem Frequenzumrichter neue Aufgaben zuweisen und die Instandhalter unterstützen.
Es ist ruhig im Büro von Erwin Schroter. Das Kalenderblatt ist noch von April, die Büropflanze vereinsamt. Den Mundschutz nimmt er zur Begrüßung nicht ab, er muss ja gleich wieder raus. Seine Kontrollfahrt steht an. Er schwingt sich auf das Fahrrad und radelt durch die Fertigungshalle. Die Anlagen stehen nahezu still, die Kollegen von der Wartung geben jetzt den Takt in der Produktion vor. Werkzeugkisten stehen unter der Fördertechnik, nur die Beine des Mechanikers schauen unten raus. Schroter grüßt im Vorbeifahren. Seine Kolleginnen und Kollegen sind daheim – Überstunden abbauen, Urlaub und Kurzarbeit. Das Coronavirus zwingt die Industrie vielerorts zum Stoppen der Produktion. Nutznießer, wenn Schroter es so nennen darf, sind die Instandhalter. Von der Zwangspause profitieren die internen Teams – genau wie viele Dienstleister. Doch braucht es in Zukunft überhaupt noch ausgedehnte Wartungstermine? Corona sei eine Sondersituation, man nutze jetzt die Zeit, so Schroter, aber er wünsche sich schon einfachere Systeme zur Überwachung der Antriebe. Immerhin: Die Anbieter arbeiten seit Jahren an Condition Monitoring und Predictive-Maintenance-Anwendungen. Der Leiter der Instandhaltung hat die Begriffe schon viele Male auf Messen und Kongressen gehört und immer wieder neue Definitionen mitgenommen. Schlauer ist er nicht geworden. Er ist skeptisch.
Frequenzumrichter werden zu Datenplattform in der Fertigung
Hintergrund: In der Industrie sind nur wenige Antriebssysteme mit High-End-Condition-Monitoring-Software überwacht – weil sie oft zu teuer sind, so auch bei Schroter. Wenn so ein System eingesetzt wird, dann nur in kritischen Bereichen. Die Ingenieure Jörg Dannehl und Holger Schmidt von Danfoss wollen das ändern. Sie und ihre Kolleginnen und Kollegen haben eine Anwendung entwickelt, die sich anbahnende Fehler in den Antriebssystemen schnell und zuverlässig erkennt. Condition-based Monitoring heißt die Lösung – ein Mittelweg zwischen Monitoring und Predictive Maintenance würde es Schroter wohl nennen.
Die Idee: Der Frequenzumrichter wird durch Neuentwicklungen immer schlauer und regelt lange nicht mehr nur den Antrieb, sondern erkennt auch noch Fehler. Der Umrichter erlernt nach der Inbetriebnahme die typischen Muster der Anlage, definiert den Normalzustand und startet die Überwachung, wenn er mit ausreichend Daten trainiert wurde. Das System gleicht die Modelle aus der Lernphase dann mit dem realen Betrieb ab und gibt im Zweifel einen Alarm. Ein Ampelsystem warnt den Anwender vor auftretenden Fehlern in Echtzeit.
Der Frequenzumrichter wird zu einer Datenplattform in der Fertigung, denn in ihm sind viele Daten und Signale verfügbar. Gleichzeitig können externe Sensoren für die Vibrationsüberwachung installiert werden und durch die Rechen- und Speicherkapazität können die Daten analysiert und ausgewertet werden – direkt on the Edge.
„Sensoren liefern Rohdaten: Ströme, Spannungen und interne Temperaturen. Damit können wir den Fluss der Maschinen, das Drehmoment oder die Geschwindigkeit berechnen. Gleichzeitig regelt der Umrichter den Antrieb und wir sammeln Regelungssignale, die weitere Informationen zum Zustand der Maschine liefern,“ erklärt Jörg Dannehl. Der Entwickler spricht von Abtastraten im Millisekundenbereich. Das System kann dann aus den Daten Frequenzspektren, die Aussagen über den Zustand der Maschine zulassen, errechnen.
„On the Edge“ und in der Cloud
![]() |
„Über Remote Monitoring können wir auch eine Verbindung zur Cloud herstellen. Einige Kunden möchten, können oder dürfen wegen Datensicherheitsaspekten diesen Weg noch nicht gehen. Ich glaube aber an hybride Szenarien“, sagt Applikationsingenieur Holger Schmidt. |
Viele Anwender scheuen sich vor komplexen Installationen und Anlernphasen gepaart mit IT-Einsatz. Die Danfoss-Ingenieure beruhigen. Die Überwachung läuft auf dem Umrichter, embedded, und die Bedienung kann über das Display des Umrichters oder das Inbetriebnahme-Tool erfolgen. „Über Remote Monitoring können wir auch eine Verbindung zur Cloud herstellen. Einige Kunden möchten, können oder dürfen wegen Datensicherheitsaspekten diesen Weg noch nicht gehen. Ich glaube aber an hybride Szenarien“, berichtet Holger Schmidt. „Die Installation ist einfach“, versichert er. Abhängig von der Anwendung gibt es zwei Optionen, so der Applikationsingenieur. Im ersten Fall lernt der Umrichter über eine definierte Zeit automatisch und parallel zum Betrieb. Die zweite Option: Der Industrieanwender führt einen Identifizierungslauf durch. Das bedeutet, der Umrichter führt die Maschine durch den gesamten Drehzahlbereich und bildet dann ein Modell zur Überwachung. „Auch ältere Umrichter können fit gemacht werden,“ ergänzt Schmidt. Durch ein recht einfaches Upgrade können auch Bestandsanlagen überwacht werden.
Condition-based Monitoring vs. Predictive Maintenance
Für Schroter ist der Unterschied zwischen Predictive und Condition-based Monitoring noch nicht ganz klar. „Predictive arbeitet mit statistischen Lebensdauermodellen. Beim Monitoring werten wir Fehlersignaturen aus und überwachen den aktuellen Zustand“, fasst es Dannehl zusammen. Und Schmidt geht noch einen Schritt weiter: „Wir werden in Zukunft nicht mehr nur den Motor überwachen. Wir installieren zwei Schwingungssensoren und kommen so einer Systembetrachtung der Anlage näher.“
![]() |
„Predictive arbeitet mit statistischen Lebensdauermodellen. Beim Monitoring werten wir Fehlersignaturen aus und überwachen den aktuellen Zustand“, sagt Entwickler Jörg Dannehl. |
System? Das klingt für Schroter nach Wettbewerb zur SPS. „Es muss ein Zusammenspiel sein. Der Umrichter kann in einfachen Anlagen Funktionen der Steuerung übernehmen. Das kann auch dann Sinn machen, wenn dadurch eine SPS eingespart werden kann“, unterstreicht Dannehl. Schmidt ergänzt: „Wir machen mit unserem Umrichter eine dezentrale Voranalyse. Die Steuerung wird weiter ihre Daseinsberechtigung haben. Genauso wie die Instandhalter-Teams.“
Das hören die Kolleginnen und Kollegen in der Anlage sicher gerne. Drei Tage haben sich noch, dann soll die Produktion wieder voll starten. Schroter freut sich schon.
Den gesamten Podcast „Wie lernt ein Umrichter?“ können Sie hier anhören. Wir wünschen eine informative Zeit!