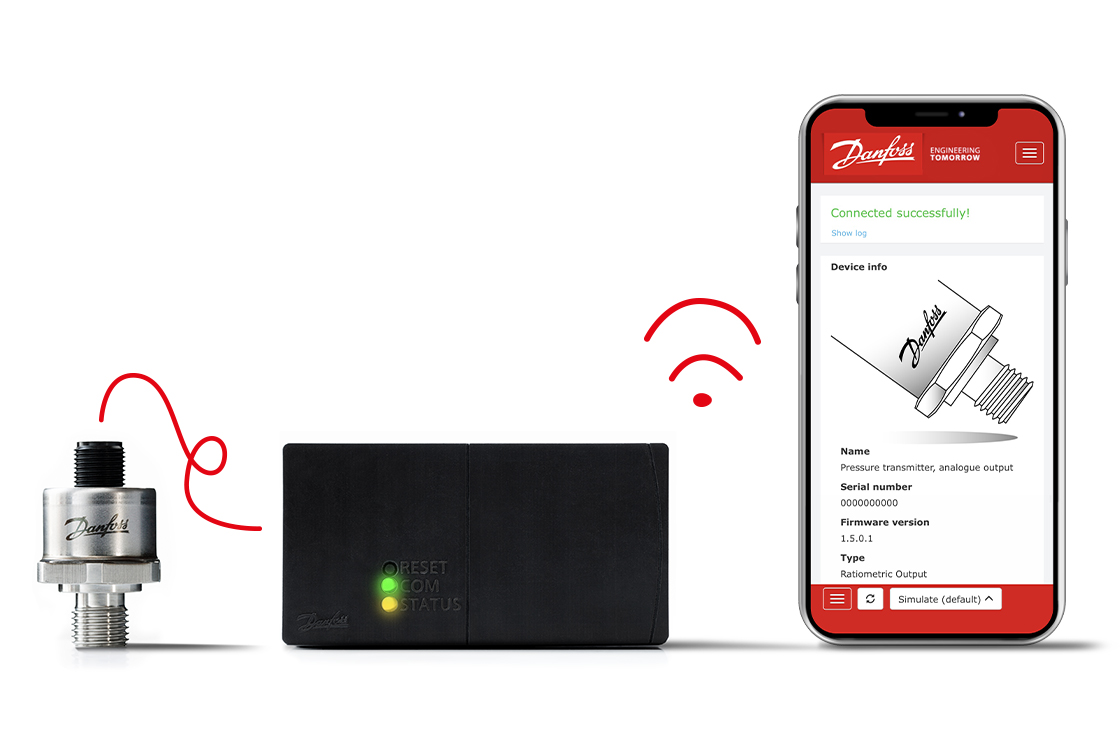
The pharmaceutical industry uses the cleanroom areas to carry out essential functions like vital manufacturing processes or other pharma sector applications. The core function of the cleanroom is to limit the flow of particulate matter in the clean spaces. These particulates can be moisture droplets or sub-micron particles, like dust, chemical vapors, and pathogens.
Maintaining the optimum differential pressure and temperature between the cleanrooms and their exterior area is the most crucial aspect of preserving their cleanliness. The differential pressure sensors and temperature sensors support this function by preserving the strict differential parameters central to preventing contamination in cleanrooms.
Furthermore, the long-term accuracy of these sensors also plays a vital role as the pressure, and temperature ranges are very narrow (pressure variations are about 0.02-0.05 w.c.). This means the sensors should have excellent stability. Hence, identifying the slightest leaks is crucial to guarantee a clean manufacturing environment and isolate the airborne contaminants.
Danfoss sensing solutions that drive efficiency to new heights
Danfoss's high-quality, best-in-class sensing solutions are driven by their industry specific applications, technologically advanced expertise, and decades of experience. Some of the Danfoss products in the category of pharmaceutical sensing solutions are:-
○ Thinfilm: Pressure transmitter with a compact design
○ MEMS Technology-based pressure transmitter
○ Heavy-duty temperature sensors
○ Temperature sensors equipped with integrated transmitter
● Temperature and pressure switches
○ Block pressure switches
○ Electronic pressure switches
Benefits of using Danfoss sensing solutions for the pharma industry:
1) The pressure sensors enhance safety and performance and are best suited for Safety Integrity Level 2 (SIL 2) environment in mobile hydraulic systems:
These pressure sensors are designed to match the performance requirement of mobile hydraulic systems in pharmaceutical material handling applications. The DST P92S pressure sensors are precisely designed to improve performance and reduce maintenance costs. The sensors also follow all the functional safety criteria and support fulfilling all the safety targets, thus keeping you a step ahead in the safety approval process.
Danfoss DST P92S pressure sensors also carry out harness & moisture checks to spot the moisture in the connector, detect failure conditions and electrical interference on the signal line. The cyclic diagnosis is carried out every 30 to 40 ms to assess the temperature sensor element, the pressure sensor drifts, and the sensor signal range. In case of any fault in the diagnosis, the system is moved to a safe state.
2) Danfoss has a wide range of reliable pressure switches and thermostats approved for tough working conditions:
The Danfoss pressure switches and thermostats are the most reliable solution for your cleanroom system. They are certified by 15 toughest International approvals that ensure the best in class functions. Danfoss’s robust switches provide seamless heavy-duty performance and are trusted as one of the most durable and reliable solutions for the challenging environments in the pharmaceutical industry.
The control solutions help prevent hazardous, time and cost-intensive failure conditions in trains and ships when fitted with Danfoss pressure switches. These switches help regulate the continuous flow and consistent pressure in water pumps and air compressors installed in the pharma industry.
3) The pressure transmitters are equipped with premium MEMS technology along with excellent vibration stability assisting noiseless clean-room applications:
These best-in-class pressure transmitters are ideal for industrial hydraulic, mobile hydraulic, and air compressor applications in the pharma industry. These transmitters feature exceptional long-term stability that too with zero drift. The wetted parts are generally fabricated using stainless steel and provide leakage-proof functions due to their completely welded design.
The pulse-snubber part of these Danfoss pressure transmitters shields the sensor element in case of cavitation, pressure peaks, and liquid hammer events, which occur due to the change in flow velocity in liquid-filled systems like fast valve closings. The media viscosity has very little effect on the response time of these transmitters since, at high viscosities of 100 cSt, the response time does not exceed 4 ms.
Conclusion
The cleanrooms in the pharmaceutical sector demand sensors that feature high stability enabling the cleanrooms to maintain the best safety and quality standards. If these sensors and transmitters have good stability and high accuracy features, they will help ensure safe levels for all cleanroom applications.
Danfoss sensing solutions feature the expertise and the most comprehensive product portfolio that improves the overall performance of the pharmaceutical set-ups. These pressure and temperature sensors have best-in-class quality and the lowest product life cycle costs compared with any industrial hydraulic application. Danfoss sensing solutions are known for their zero-defect policy, ensuring reliable and safe production methods. Danfoss switches, sensors, and valves are manufactured from the most durable materials and designed to endure vibrations, shocks, and allowable fluctuations in pressure and temperature during their operations.