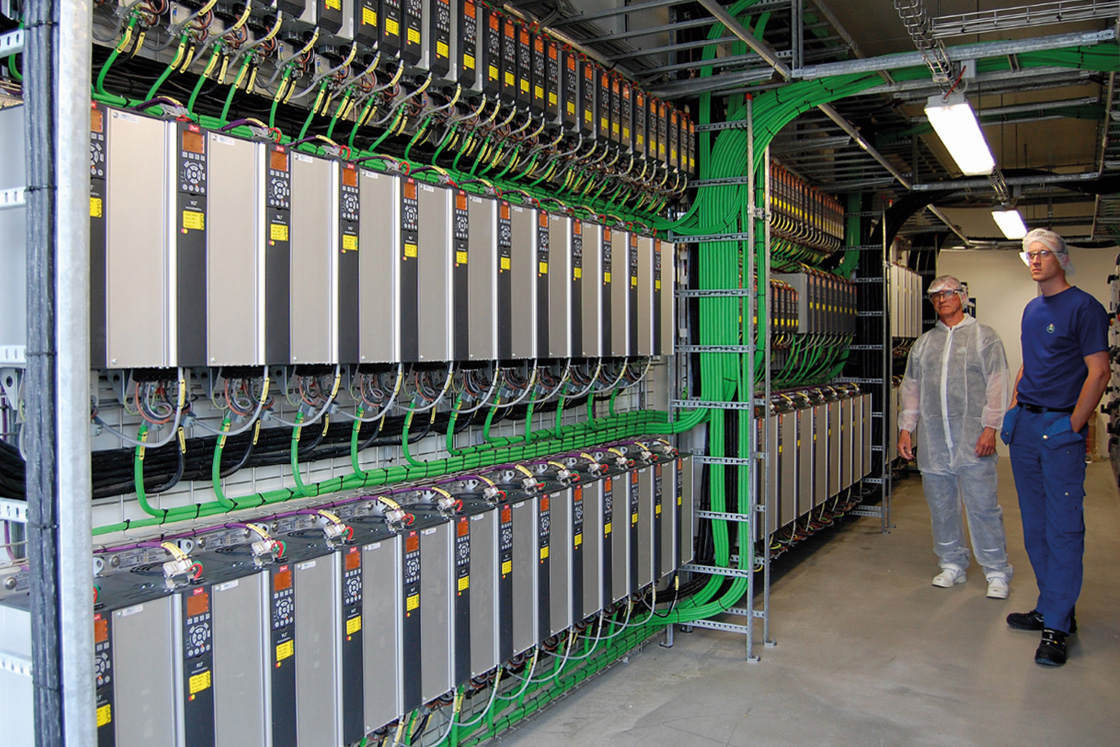
VLT® drives ensure maximum uptime, high precision, and cut Arla’s energy demand – also benefiting customers.
At Arla Foods Ingredients, the ultimate end user is the next generation – but before that comes the baby food manufacturer. The new plant delivering “infant formula” grade lactose powder, a higher grade of lactose than was previously possible, now increases lactose production four-fold at the Arla Videbæk facility in Denmark, with enviable energy savings thanks to VLT® AutomationDrive.
Cutting energy consumption downstream
The new 80,000 tpa lactose factory at Arla Foods Ingredients adds value to the extent of cutting out an entire customer process. High-quality infant formula is ready for instant combination with other ingredients, meaning food producers can save an entire energy-intensive cycle of mixing and evaporation. To achieve this, Arla guarantees extremely high levels of quality and food safety, using a taut process under precision control. Food producers win enormous energy savings by being able to cut out a whole mixing and evaporation cycle, for example in baby food or energy drink production.
The challenge for Arla is to maintain top quality and 80,000 t annual volume for the infant formula lactose plant, whilst staying ahead of ever more ambitious key performance indicators based on carbon footprint, including:
- Water consumption: litres per kg powder produced
- Energy consumed: kWh per kg powder produced
Winning the energy race
In its own factory Arla is also winning the energy race with 5-15% energy savings due to the VLT® drive control on each and every pump and fan motor – compared to direct on line (DOL) operation.
Motors account for a large portion of all energy consumption in the plant and therefore there is focus on efficiency class and further optimization using motor control via VLT® drives. “All our motors are asynchronous. We pay attention to the Ecodesign Directive, and specify IE3 or IE4 motors. We choose the best motor for the task, to fulfill but not exceed the requirements.”
“We have begun using the Advanced Energy Optimization (AEO) function in the FC 302, and measure energy consumption via PROFIBUS. However typically we need to measure the performance of the whole plant, not just the frequency converter, and we achieve that via energy metering for each control room. In the future, Arla’s new upcoming carbon desktop platform will measure all energy consumed at component level – including VLT® drives.”
One drive throughout the plant
“As far as possible, all our motors are controlled by VLT® AutomationDrive frequency converters. There are some very good reasons”, explains Knud Rahbek:
- We get accustomed to this frequency converter and become extremely expert in using the capabilities offered by this particular drive. We would not be confident to use the full range of functions offered by the drive if we didn’t know this drive well
- As a result, some of our electricians have become incredibly clever at getting the optimal performance out of the PROFIBUS communication
- Our team is not afraid to touch the drive. It has an intuitive interface.
- Training of new staff is much easier when there is only one system to learn. New electricians on our team get the chance to follow a team member in the beginning. Then they get the task of setting up the parameter list for 15-20 drives at a time, still under supervision. This is a real operating situation, it has to work right and the pressure is on. If the electrician makes a mistake, he has to find it himself.
Maintenance manager Simon Arentoft:
“We have one point of contact for drives and we know who to call in an urgent situation. We can rely on Danfoss to respond fast, and this means we can react fast to avoid delays in production, in the event of a problem”.
Lean warehousing
With one drive type installed throughout the plant – FC 302 – the spare parts logistics are reduced to the absolute bare minimum. An unbelievably lean stock of 8 units, one for each enclosure size up to 90 kW, serves the entire installed base of 1400 frequency converters. Understandably, warehouse costs are remarkably low in relation to the volume installed. The level of stock is still adequate to exchange a drive, make the repair on site and order precisely the correct replacement drive at leisure.
Never stop!
A fundamental requirement of the Arla operations is zero downtime. Even so, replacement of a low to medium power drive is not catered for by redundancy. A drive replacement takes 20 minutes, during which production continues at a slightly reduced volume, which is more cost-effective than operating redundant units.
Nonetheless, for changeout of high power drives, such as those controlling the huge ventilation tower fans, production stop is unavoidable.
“Replacement of units rated larger than 90 kW is covered by a 24-hour standby technician according to the service agreement. However over the last four years we have not had a single urgent service call”, smiles Simon Arentoft.
Previous experience shows that plant-wide reliance on FC 302 drives improves uptime, due to the benefits of motor protection functions. The strategy of installing drives in control rooms rather than cabinets also supports reliable uptime as well reducing energy consumption. When mounted in control rooms the FC 302 is easy to ventilate and has a longer lifetime – as well as being easily accessible for service technicians.
DrivePro® service agreement
Internal service is performed by a team of 30 expert technicians, supplemented by a Danfoss service agreement. Knud Rahbek emphasises that 100% reliance on fast response by a service technician is vital, when a problem arises. Therefore Arla demands – and receives - a high level of service form Danfoss, spelled out in the mutual service agreement.
Highlights
- Regular service check of all frequency converters including data transfer to the LCP
- Discount on Danfoss training courses for Arla staff
- 24-hour standby technician for urgent requests
- 24-hour delivery service for replacement drives
Arla Foods Ingredients Group
The lactose factory in Videbæk, Denmark consumes 120 GWh of electricity annually. Therefore the 15% annual energy saving in energy costs is of huge importance.
1400 Danfoss VLT® AutomationDrive FC 302 units are installed, rated 0.37 kW – 630 kW.
The highest quality pays off
Arla premium quality lactose exceeds even the strictest international quality standards, ensuring food safety at all times. Dry blend lactose effectively reduces end-user production costs, while offering great production flexibility that will increase end-user capacity by up to 25%. Due to the highly efficient production processes, these tangible benefits are achieved completely CO2 neutrally.