In case of limited access to the basement or heating system, the electronic controller (ELC) can be supplemented with a remote control unit, ECA 30/31, which can be placed at any desired location in the building.
This enables room temperature monitoring and control, easy interfacing, and remote access for overriding all the functions of the ECL Comfort controller.
The remote control units ECA 30 and 31 are used for room temperature control and override of the ECL Comfort 210 and 310 controllers.
The remote control units are connected to the ECL Comfort controllers by means of x2 twisted pair cables for communication and power supply (ECL 485 communication bus).
The remote control unit ECA 61 is used for room temperature control and override of the ECL Comfort 110 controller. The DLG is a gateway used for linking ECL Comfort 110 with Danfoss Living™ radiator thermostats.
Features and benefits
Can be placed at any desired location in the building
Enables monitoring, control and easy interfacing of the ECL Comfort controller
11 - 15%, or more, savings on your energy consumption in the building, as well as reduced CO2 emissions.
Tools and apps
Software tools
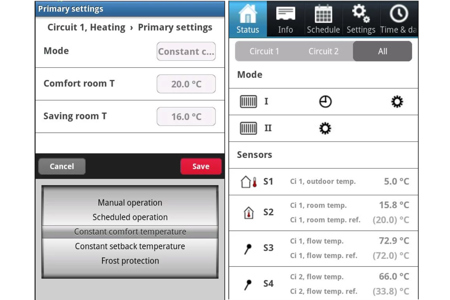
FAQ
Case studies
-
if (isSmallPicture) {
; } else if (isBigColumns) { } else { }Danfoss partners with the city of Banja Luka to decarbonize district energyThe Challenge: Renovate 34 of the city’s largest heating substations
The Solution: Danfoss Leanheat® Monitor enables full substation digitalization
The Results: reduced heat consumption by 10% -
if (isSmallPicture) {
; } else if (isBigColumns) { } else { }Successful transition from oil boilers to a local heating network in EurasburgIn the Wittelsbacher Land near Augsburg the local network in Eurasburg supplies heat to 80 buildings using a wood chip heating system. Danfoss’ substations ensure efficient heating in all building types, and its modern SCADA solution enables remote system monitoring and management.Â
-
if (isSmallPicture) {
; } else if (isBigColumns) { } else { }Intelligent optimisation of district energy in new residential apartmentsTwo new build apartments in Docklands, London and Newbury Racecourse, Berkshire have been equipped with intelligent Danfoss solutions, bringing increased control and stability as well as greater than 20% peak energy reduction.
-
if (isSmallPicture) {
; } else if (isBigColumns) { } else { }Leanheat makes buildings smartIn Europe, 30 percent of all energy consumption goes to heat or cool buildings. Danfoss has the solution to lower energy usage and improve indoor climate by adding a digital element: Leanheat software.
-
if (isSmallPicture) {
; } else if (isBigColumns) { } else { }MS Cinderella saves more than 1000 tpa marine diesel with new ventilation controlAboard the Viking Lines cruise ship M/S Cinderella, Danfoss AC variable speed drives are delivering fuel savings so large that the cost of installing the drives will be fully recovered in less than eighteen months.
-
if (isSmallPicture) {
; } else if (isBigColumns) { } else { }A cost-effective solution: district cooling in central CopenhagenEnergy efficiency was a major consideration in the design of Copenhagen’s district cooling project, where VLT® drives contribute to reducing CO2 emissions by more than 3000 t annually.