Match your capacity to heat load and process demands
One of the largest cost factors in the refrigeration system lifecycle is energy. In many refrigeration applications, capacity exceeds heat load due to seasonal variations, product loading, occupancy variations, and electrical appliances that cause power loss. Modern, dedicated AC drives, such as Danfoss Drives’ range of VLT® drives, provide the ideal means to continually adjust the equipment capacity to the actual heat load and process needs. The benefits are significantly lower energy consumption and lower operation and maintenance costs.
Intelligent compressor and condenser/evaporator fan control are essential in any optimized refrigeration system. You can typically achieve 10–25% savings on energy consumption by applying Danfoss AC drives to optimize the capacity control of refrigeration compressors, condensers and evaporators. By creating stability while balancing the capacity to the actual load, the system-wide coefficient of performance (COP) improves providing significant energy savings.
Cascade control optimizes energy savings and reduces lifecycle costs
Cascade configuration produces the optimal interaction between an application and an AC drive under partial loading. The base load is handled by a single application, such as a compressor, controlled by a drive. When heat load rises, the drive starts up additional compressors one at a time. This ensures the applications work at their optimum efficiency point, and the drive maintains maximum energy efficiency throughout the system.
Well-planned cascade control also ensures minimal wear on the individual applications. By rotating mains-powered compressors, for example, maintenance managers can ensure each ends up with a similar number of operating hours and an equal wear level. This increases the lifetime of the applications and extends service intervals reducing lifecycle costs.
Danfoss Drives’ advanced Multi-zone pack controller ensures effective cascading and controls of up to six compressor packs. This minimizes energy consumption, avoids too frequent staging and de-staging, stabilizes pressures and temperatures, and reduces compressor wear and tear. Similarly, the Pump Cascade Controller distributes running hours evenly across all pumps to keep wear and tear on individual pumps to a minimum.
Fast commissioning
Commissioning is fast and easy utilizing the Danfoss Drives display panel that uses common refrigeration terms rather than computer language. The wizard guides the user through the necessary settings. Ease of programming makes installers and service technicians more comfortable and confident, makes their jobs easier and quicker, reduces human errors and improves employee productivity.
Thermodynamic efficiency in commercial refrigeration
The commercial refrigeration sector includes food retail establishments such as supermarkets, hypermarkets and convenience stores. It also includes precision air conditioning in data centers.
Typical applications include racks and packs, condensers, evaporators and pumps.
Reliability and thermodynamic efficiency are the key factors in any commercial refrigeration system efficiency and effectiveness. A range of functionalities tailored to refrigeration applications ensures versatile compatibility, stable performance, system reliability and optimal energy efficiency.
Improved control in industrial refrigeration
The industrial refrigeration sector includes cold stores and cold rooms, meat, seafood and other food and beverage processing units, bio-pharmaceutical, chemical and textile plants. Typical applications include process chillers, condensers and evaporators/air-handling units and pumps.
For fresh fruit and vegetables, the initial cooling, processing and cold storage are amongst the most energy-intensive processes in the food industry. Faster refrigeration is needed in the beginning to cool down fresh fruit and vegetables to slow down their spoilage and maintain pre-harvest freshness and the flavour of fruit and vegetables. Danfoss AC drives provide fast cooling and freezing when necessary. They also maintain uniform temperature, humidity, air circulation and fresh air supply for cold storage maintaining food in marketable condition for a period of months and consuming less electricity than conventional installations.
Temperature-controlled logistics in the cold chain
Temperature-controlled logistics are important to ensure the preservation and safe transfer of food, beverages and medicine to consumers from the harvesting or production stages. Typical applications include racks, packs, process chillers, condensers and evaporators/air-handling units and pumps. The reliability and thermodynamic efficiency of Danfoss AC drives ensure a hygienic and controlled environment in your cold stores, food processing plants, food retail outlets and throughout the entire cold chain.
Chillers
Variable speed control of a chiller allows you to provide optimum process temperature, while matching the capacity to the actual need based on measurements in the system. Speed control is beneficial when a compressor runs for long periods at partial load. Reduce operational costs by running applications at a lower speed which saves energy consumption. And reduce installation costs by optimizing the system and the compressor itself.
Danfoss AC drives ensure fewer starts and stops which reduces mechanical wear. And dedicated features such as oil return management, high pressure / low pressure safeties and skip resonance frequencies ensure safe operation of the chillers.
Products for compressors include soft starters, high-power drives, AHF harmonic filters with a built-in cascade controller option, DC coils and PID controllers.
Start-up and peak load strategies
Start-up is the critical phase of compressor operation. The VLT Refrigeration Drive minimizes the number of starts required by varying the compressor speed to tune capacity during operation. The maximum number of start/stop cycles in a given period is configurable using the control panel.
The VLT Refrigeration Drive delivers 135% of the rated starting torque for a short duration. During normal operation, 110% of the rated torque is available for 60 seconds.
To extend the drive lifetime, a pressure relief valve can be opened to allow the compressor to start up quickly with no load.
Smaller compressors with the same peak load
Brief peak loads can be handled by configuring the system with a smaller compressor, which the drive runs at up to 90 Hz. In this way, a larger compressor just to cope with peak loads is not necessarily required.
The VLT Refrigeration Drive continues to control fixed-speed compressors in situations where the variable-speed compressor fails. For a fail situation, the neutral zone is set by a special parameter "Fixed speed neutral zone", which enables fewer starts by expanding the neutral zone.
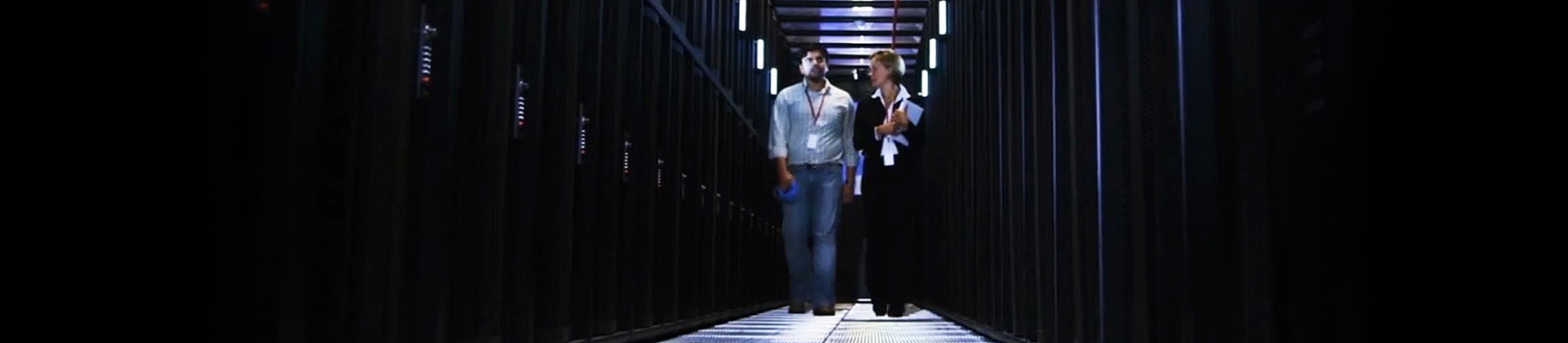
Danfoss and Inertech change the future of data center cooling
New solution enables expansion without compromising security, consumes less energy and water, and costs less than a traditional chiller plant.
Contact us
For further information please contact us
Case studies
-
if (isSmallPicture) {
; } else if (isBigColumns) { } else { }Danfoss and Inertech change future of data center coolingNew solution enables expansion without compromising security, consumes less energy and water, and costs less than traditional chiller plant.
-
if (isSmallPicture) {
; } else if (isBigColumns) { } else { }20% lower electricity costs for Olympia Sports and Event Centre InnsbruckVLT® HVAC Drives guarantee energy-efficient operation of fans, centrifugal pumps and compressors at the bobsleigh, luge and skeleton track.
-
if (isSmallPicture) {
; } else if (isBigColumns) { } else { }85% startup energy reduction for Reindl KältetechnikVLT® Refrigeration Drive provides optimal control of the dehumidifier in the hay drying process.
-
if (isSmallPicture) {
; } else if (isBigColumns) { } else { }Annual energy savings of 800,000 kWh for Aarhus HospitalVLT® Drives control the speed of heat pumps and chillers in the new cooling plant to optimize performance and annually save 800,000 kWh of energy.
Products
-
if (isSmallPicture) {
; } else if (isBigColumns) { } else { }VLT® Soft Starter MCD 500A comprehensive solution for soft starting and stopping of three-phase asynchronous motors.
-
if (isSmallPicture) {
; } else if (isBigColumns) { } else { }VACON® NXP Liquid CooledWell-suited to applications where air quality is critical, space is limited and efficient heat transfer is required. Active Front-end (NXA), Non-regenerative Front-end (NXN), Brake Chopper (NXB) and Inverter (NXI) configurations are available.
-
if (isSmallPicture) {
; } else if (isBigColumns) { } else { }VLT® Soft Start Controller MCD 100An extremely cost-effective and compact soft starter that provides basic soft start and stop functionality and easy DIN rail mounting.
-
if (isSmallPicture) {
; } else if (isBigColumns) { } else { }VLT® Compact Starter MCD 201 and MCD 202Two families of soft starters that provide a total motor starting solution for motors up to 110 kW.
-
if (isSmallPicture) {
; } else if (isBigColumns) { } else { }VACON® 100 INDUSTRIALDrive modules and enclosed drives that are easily integrated into all major control systems.