Electric traction inverter for HEVs and EVs
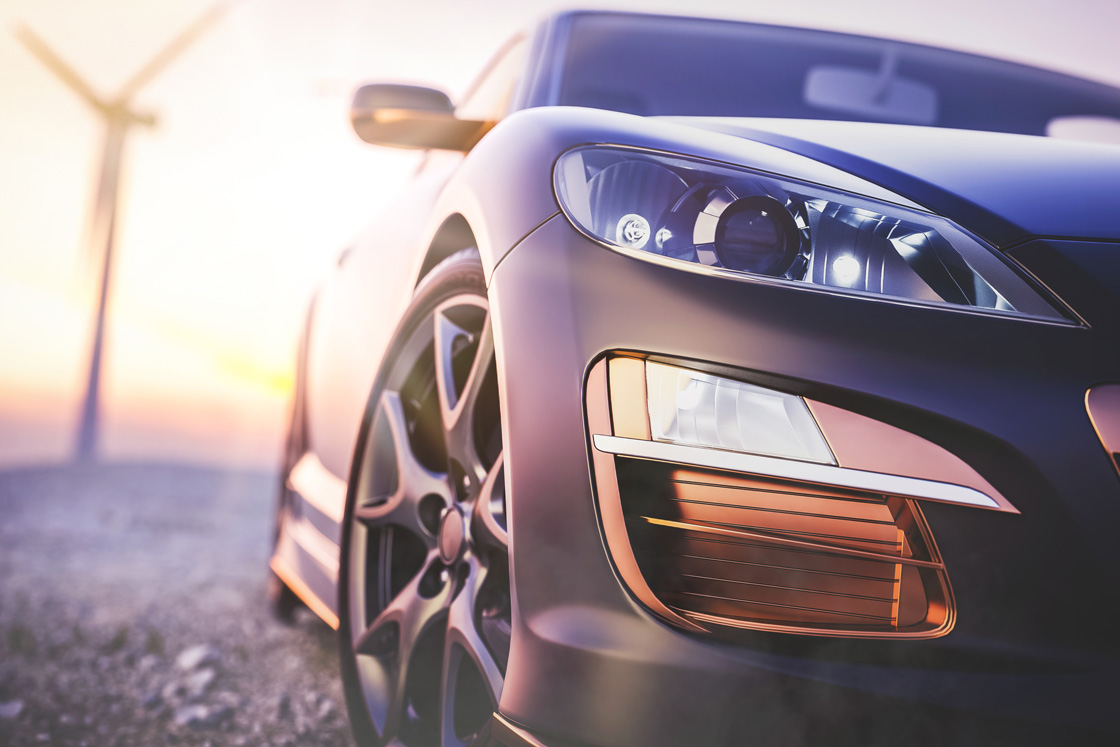
Drivers of hybrid electric vehicles (HEV) and electric vehicles (EV) rely on automotive manufacturers and system suppliers to deliver a safe, reliable and comfortable driving experience. The main traction inverter, a critical component in the electrified drive-train, has a direct influence on the driving experience, the battery range and the overall safety of the vehicle.
The purpose of the traction inverter is to convert the DC current from the electric vehicle’s battery to AC current to be used in the electric motor to drive the vehicle’s propulsion system. It plays a significant role in capturing energy from regenerative braking and feeding it back to the battery.
High integration level and increased power density
There are two different traction inverter design philosophies. The first is separate packaged ‘box-type’ inverters commonly used by many automotive manufacturers and system suppliers. These inverters combine ease of assembly with a modular design approach and comprise of frame-based, silicone-gel-filled power modules in six-pack or customized configurations, sometimes even including charger or booster topologies.
The second applies an integrated inverter design, where small and fully encapsulated components are placed within the mechanical compartment of the drive-train. Here, even permanent-magnet synchronous machines (PMSM) are often designed as part of the transmission system integrating the power inverter into the same housing.
The demand for higher levels of integration is growing. The concept of an electrical machine including all the power electronics needed for a frequency inverter, matching requirements for cooling, vibration and robustness, is very attractive when it comes to the sensitive discussion of volume or weight restrictions and overall system cost.
Reap the benefits of proven technology
Most electrified powertrain traction inverters contain a multichip-semiconductor power module. It can comprise of IGBTs, diodes or MOSFET dies, and the typical circuit topologies are half-bridge or six-pack.
The ongoing trend towards mechatronic integration of power electronic components and mechanical assemblies requires more compact and mechanically robust power modules. Design of the power modules becomes a core element in achieving higher levels of power density and fulfilling increasingly stringent requirements. Moulded packaging technology is a solution, but integration and compact designs challenge the thermal management of the components. Therefore, a high-performance but compact and cost-competitive liquid-cooling system is required.
Danfoss has developed a second-to-none portfolio of technologies, addressing all the aspects mentioned above. Well-known examples are the Danfoss Bond Buffer® (DBB®) that combines sintered die attach and copper wire bonding for outstanding reliability, transfer moulding processes for robust packages, and the ShowerPower® and SP3D® liquid-cooling technologies for optimal thermal management.
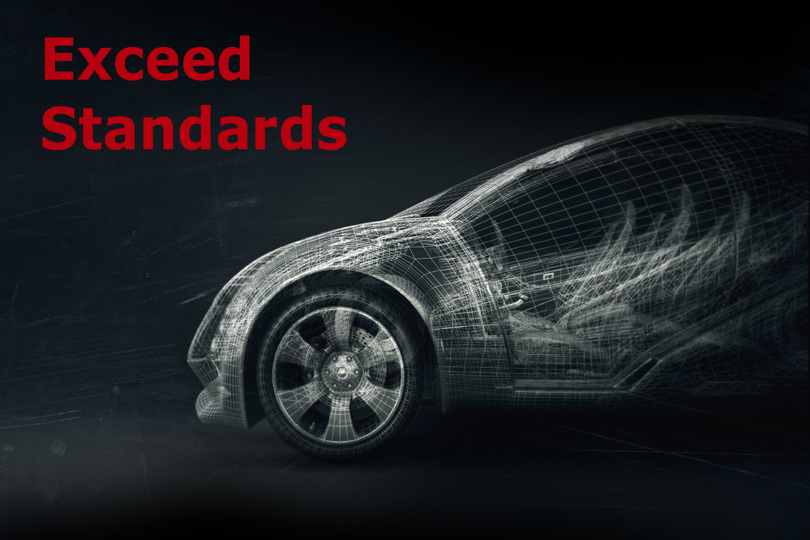
New DCM™ technology platform for automotive traction
The next generation power module technology platform for automotive traction inverters
Related solutions
-
if (isSmallPicture) {
; } else if (isBigColumns) { } else { }Automotive power electronicsDanfoss actively supports the automotive industry with electronic components, helping to power up future electric drive train applications and achieving the challenging emission goals.
Downloads
Type | Name | Language | Valid for | Updated | Download | File type |
---|