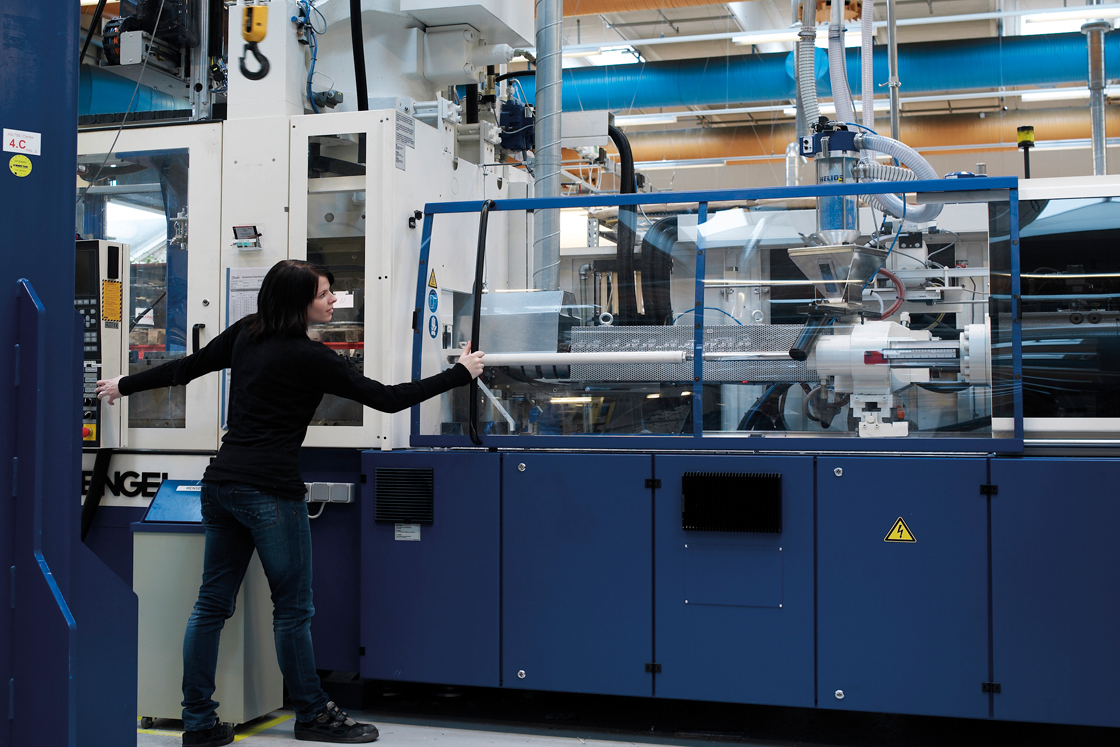
Electric noise caused by Variable Frequency Drives (VFD) and other direct-coupled electrical fast transients from valves and relays is a serious challenge in the plastics industry causing lost production hours, material waste and ultimately expensive damage and repair of machinery.
In light of the problem with electric noise, Danfoss set out to invent a new pressure transmitter optimized for the specific conditions of the plastics industry. The result is the new MBS 1600 that offers electric protection even under the toughest conditions.
“We worked closely with the plastics industry and machine builders to deal with the problem of VFD-induced electric noise and other direct-coupled electrical fast transients from valves and relays once and for all. We know how important it is that the lines are running without interruption and that our customers products live up to quality specifications”, says Product manager Lars Baunsgaard.
The new MBS 1600 is mainly used to control all hydraulic processes, including injection pressure, clamping force and servo pump.
Ensures efficiency and high uptime
The time constant of the new MBS 1600 allows extremely fast response time to support high productivity. The fully welded design of the transmitter ensures robustness and operational reliability even in the harshest environments.
MBS 1600 is built to withstand hydraulic system failures caused by pressure peaks, liquid hammer, cavitation, vibration and other mechanical impact.
“Our expertise in plastics processing allows us to offer a unique product portfolio customized to the industry’s needs. The new MBS 1600 is an addition to our existing product range that helps enhance performance and lower life-cycle costs in the plastics industry”, says Product Manager Lars Baunsgaard.
Facts about MBS 1600/1650
• Comes in two versions: MBS 1600 (without pulse-snubber) and MBS 1650 (with pulse snubber)
• Full immunity to electric interference caused by VFD or other direct-coupled electrical fast transients
• High burst and overpressure capabilities due to fully welded design
• Protected against cavitation and liquid hammering
• Fast time constant to support industry requirement (< 1 m sec 10 to 90% step response)
• Wide operating temperature range (-40 to 125 °C)
• Vibration and shock stability
• Zero drift due to excellent long term stability
• Wide range of electrical and pressure connections
Related product
-
if (isSmallPicture) {
; } else if (isBigColumns) { } else { }MBS 1600, pressure transmitters for plastic processingMBS 1600/1650 pressure transmitter is tailored to the specific requirements of the plastics industry. MBS 1600 is a high-quality and EMC-immune pressure transmitter.