The cooling water system is one of the most important auxiliary systems to ensure reliable performance, high energy efficiency and prolonged lifetime of the ship engine.
We will take a closer look at the general function of sensors and transmitters to help optimize the operation of the highly critical cooling water system.
Digitalization and sustainability are key drivers of development in the marine industry. In a series of articles, Danfoss marine experts explore and explain how advanced monitoring and optimization of essential engine systems contribute to enhanced energy efficiency, safety and profitability.
With a limited number of new builds, the primary focus of the industry is on refurbishment of existing assets to ensure that the opportunities delivered by digitalization are fully utilized in order to boost performance and live up to new demands for sustainable shipping.
In this article, we take a closer look at the general function of sensors and transmitters to help optimize engine sub-systems, and more specifically opportunities for improving the operation of the highly critical cooling water system.
The diesel engine is a complex machine consisting of several sub-systems which needs constant monitoring and control to ensure optimum performance of the engine. The basic principle of the compression ignition engine have remained unchanged over the past 120 years, but the technology for monitoring, control and optimization of the main engine processes have advanced dramatically.
Next generation shipping takes maximum advantage of the new technology, and today, temperature sensors and pressure transmitters are an integrated part of the engine control and alarm systems. Precise and reliable sensors and transmitters provide essential input to the engine control system that in turn optimizes engine performance and energy efficiency even under the most difficult operating conditions.
Furthermore, the sensors and transmitters collect data that can be used to benchmark engine performance and give early warning to initiate preventive maintenance measures.
Fig. 1 Optimum operation of engine sub-systems for cooling water, lubrication oil, exhaust gas, fuel and engine air are essential for efficient and safe operation of the engine
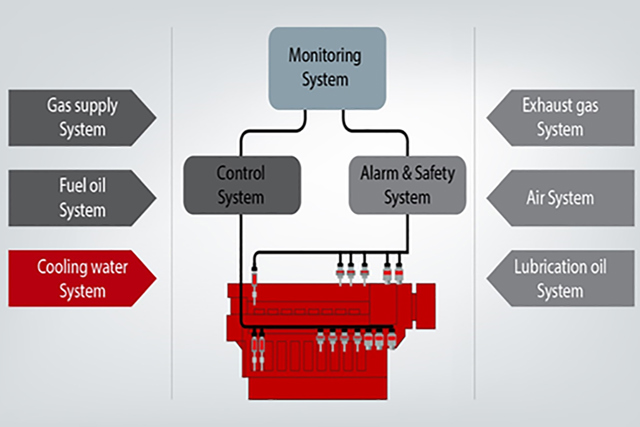
The engine is equipped with redundant sensors for the alarm and safety system that immediately detects irregularities in temperature, pressure or flow that might cause permanent harm to the engine.
Computer controlled safety and protection systems rely on input from precise sensors and transmitters to trigger the alarm and locate the problem. If no intervention is performed, the control system prompts automatic slow-down of the engine and, if necessary, safety shut-down of the engine to avoid havoc.
A number of alarms related to pressure and temperature are critical and likely to cause safety shut-down, e.g. high crankshaft bearing temperature, low lubrication oil pressure, high jacket water temperature, low jacket water pressure, and high exhaust gas temperature.
The cooling water system is one of the most important auxiliary systems to ensure reliable performance, high energy efficiency and prolonged lifetime of the engine.
The cooling water system is a closed loop system circulating freshwater that has been treated with PH-controlling additives to reduce the risk of internal corrosion and fouling of engine and heat exchangers.
The primary cooling loop consists of a high temperature circuit for the main engine and a low temperature circuit for the auxiliary engines, gear, oil cooler etc. The secondary circuit cools the primary cooling circuits by exchanging heat with the seawater. Use of this system prevents leakages or spills of lubricating oil into the sea, because seawater does not become contaminated with the oil.
Without adequate cooling, certain parts of the engine that are exposed to very high temperatures would soon fail. Effective cooling of the main engine is achieved by circulating freshwater around internal parts of the engine. The primary cooling water absorbs the combustion and friction heat generated by the main engine and is cooled by the sea water supplied in the secondary cooling water loop. Temperature sensors constantly monitor fluctuations in temperature and report back to the control system if more/less cooling is needed or give alarm if the temperature is measured to be outside the permitted range.
Fig. 2 Schematic illustration of primary (red/yellow) cooling loop and secondary (blue) cooling loop of main engine and auxiliary engine systems
In the low temperature cooling circuit, freshwater is circulated around the auxiliary engines, lubricating oil cooler, injection nozzle cooler, diesel cooler and other sub-system heat exchangers in order to ensure that all parts of the engine is kept within the optimum operation boundaries.
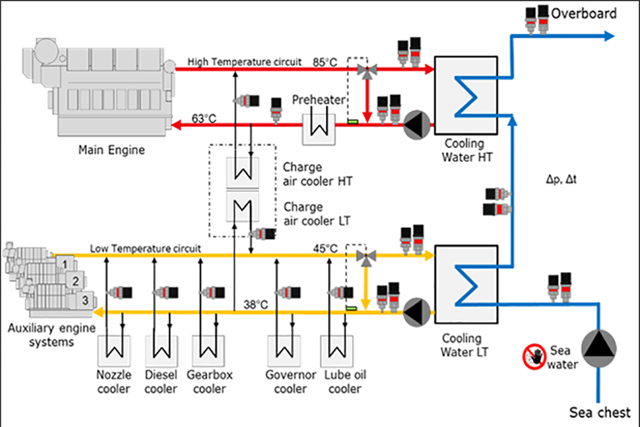
A common reason for performance decline is fouling of the heat exchangers. Fouling is a buildup of an insulation layer between the flowing media and the heat exchanger causing a reduced heat transfer and an increased pressure drop which has a negative impact on the engine performance and fuel efficiency. Temperature sensors and pressure transmitters can reveal fouling of the heat exchangers so that inspection and maintenance can be carried out before the performance of the system declines. In this way, short term actions like increasing the mass flow delivered by the pump and increased fuel consumption can be avoided.
A large number of sensors and switches are available for marine engine applications. Danfoss marine experts are ready to help you select the right components for your next new build or refurbishment project. With in-depth knowledge of marine engines and sub-systems, we can help you configure the right solution depending on your requirements.
Danfoss offers a wide range of marine approved temperature sensors, transmitters and switches for the engine cooling system.
Temperature plays a vital role in marine processes. Accurate temperature control allows safe operation and high performance, whereas overheating by just a few degrees can have severe consequences for equipment and personnel.
Danfoss offers a comprehensive range of temperature sensors and switches optimized for cooling water applications:
http://marinecontrols.danfoss.com/products/temperature-sensors/#/
http://marinecontrols.danfoss.com/products/switches/#/
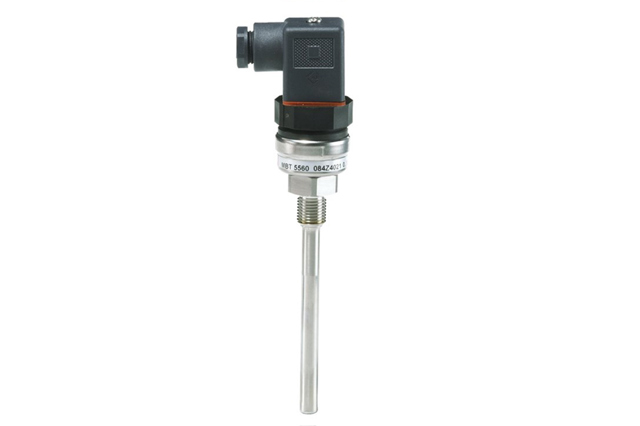
Precise pressure measurement and control of a large number of parameters is crucial to ensure a long service life and efficient operation of marine engines and support systems.
Danfoss offers a comprehensive range of pressure transmitters and pressure switches optimized for cooling water applications:
http://marinecontrols.danfoss.com/products/switches/#/
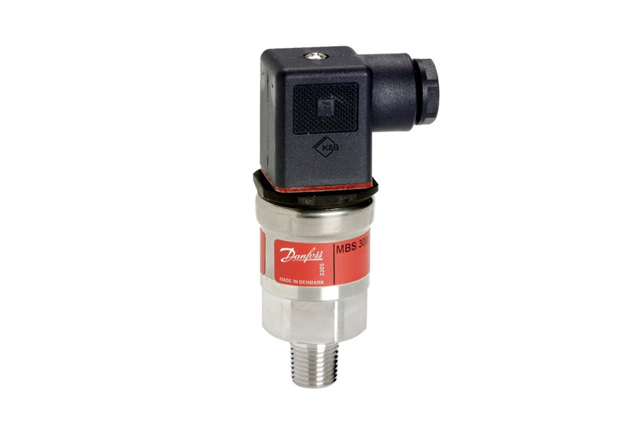