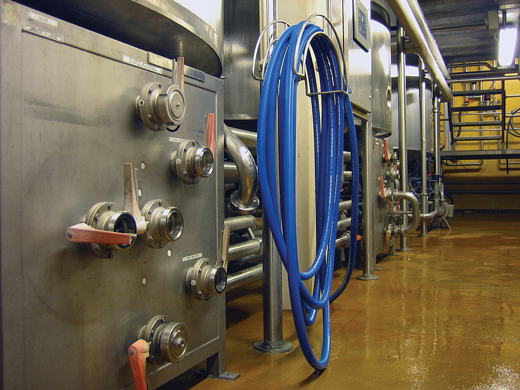
Introduction
With the advancement in technology, India has gone from a country with severe milk shortage to the world’s foremost milk producer. The increase in the demand is driven by the growth in the population, which is expected to be 180 million tons by the year 2022 as per the estimates of the National Dairy Development Board (NDDB). Notwithstanding the tremendous growth of the dairy industry, India is still facing multiple challenges related to quality, low efficiency, lack of infrastructure, and technological advancement.
Danfoss is the world leader in variable speed technology; along with energy-saving, enhanced safety, and upgraded productivity, there are several other benefits driven by their variable frequency drives (VFDs) in the dairy industry. Let's look at how the Danfoss’ drives address the various challenges of the dairy industry.
Here’s how variable speed technology can help achieve process precision in these six dairy plant applications:
1) Mixers & Separators
The industrial mixers used in dairy plants require a high starting torque, and a constantly varying speed of the mixers equipment for precise regulation to guarantee the best quality products.
To overcome these challenges, the drives employed should provide safe torque switching, direct torque control, and precise speed regulation so that the system performs with the variable loads.
Danfoss variable frequency drives (VFDs) enhance operational safety and improve the production speed and the overall process cycle time.
• Reduce energy consumption at lower speeds
• Reduced mechanical stress
2) Compressors
Compressors are one of the highest energy consumers; hence the dairy industry depends on energy-efficient technologies to safeguard the utmost reliability of compressor operations. Continuous usage and harmonics cause interruptions, resulting in the overall system's interference and downtime.
Therefore, the dairy industry requires energy-efficient drives that extend the compressors' speed range and are fitted with built-in harmonic-mitigation systems that support the compressors to operate at full speed.
Danfoss variable speed technology reduces harmonics by 97% and ensures the system up-time by reducing the wear and tear of mechanical parts. Danfoss VFDs reduce the energy wasted due to overheating and help achieve an energy efficiency of 20% to 60% across different speed ranges.
3) Centrifugal separators
The centrifugal separators in dairy processing face difficulty controlling the high torque during starting and maintaining the centrifuge speed without creating vibrations. These separators should start along with the spinning process.
The drives require an automatic switching system to change the maximum torque above a predefined frequency, regenerative braking systems with direct torque control functions to reduce these challenges.
Danfoss VFDs boost system efficiency by providing speed controls without over dimensioning; the energy required for braking is fed back into the mains, reducing energy consumption and saving time and equipment wear-outs.
• Controlled ramp up to nominal speed
• Fast speed control in nominal speed during load chokes (discharging process)
• Catching the motor after a mains disruption, in a controlled manner
• OVC (overvoltage control) to ramp down the bowl without brake resistor or AFE
• Constant torque mode
4) Cooling towers
The industrial cooling towers of the dairy plants are driven using belts; hence they are costly to maintain due to mechanical part wear-outs.
Danfoss Variable Speed Control technology offers fewer parts for the cooling tower systems, which reject the current start-up peaks, improve safety, and reduce the noise levels. Thus ultimately reducing the total cost of ownership.
5) Pumps
Pumps used in dairy systems are high-energy equipment that faces issues with the change in liquid pressure that impedes the reliability of pump seals and impellers. The pumps need to minimize water usage during the process and cleaning of the pipes. Furthermore, the shrouded pump motors pose difficulty in cleaning and, at times, do not fulfil the hygiene requirements.
To comply with these issues, the pumps should have a motor drive fitted with anti-cavitation software, which measures the motor torque and the speed to determine the development of cavitation. The drives used with the pumps should have the pump control software that provides the exact pressure and flow rate for the pipe cleaning and filling functions. The motor drives should work at only 1/8th of the power at half speed for better power efficiency.
Danfoss' variable frequency drives (VFDs) protect the pumps from cavitation that damages the fat globules. These drives expand the product quality and impeller life cycle time and aid in achieving 20 to 60% energy efficiency across various speed ranges.
6) Conveyors
The conveyor systems in the dairy industry face problems related to smooth, precise, and reliable control and harmonization of conveyor speeds to provide reliability, so the production process is never halted.
To overcome these challenges, the drives need to be fitted with a brake chopper that provides precise control to the conveyor deceleration rate without any external hardware. The motor drives should provide continuous, intermittent, or variable speed operation and safe torque off features to prevent unexpected conveyor movements.
The Danfoss VFDs function to adjust the conveyor speed separately, in synchronization to guarantee the material flow between the different process stages. Using Danfoss’ drives the conveyor systems require less maintenance and the process uptime is increased. Furthermore, maintenance costs are reduced due to the reduced mechanical stress on belts and gears.
• Controlling speed, position and synchronization
• Precise speed control and positioning, high control dynamics, absolutely uniform product transport
• Reduced risk of product fall-over
• Smooth acceleration and deceleration of products
• Optimal synchronization of inlet and outlet conveyors for the individual machines
• High starting torque and smooth transition to partial load operation
Conclusion
Danfoss offers an incomparable competitive edge through its quality, enhanced applications that target the dairy industry's requirements, and an all-inclusive range of product lifecycle services. You can rely on us for all the technological solutions required for the dairy plant with enhanced performance. To know more, write to danfoss.india@danfoss.com