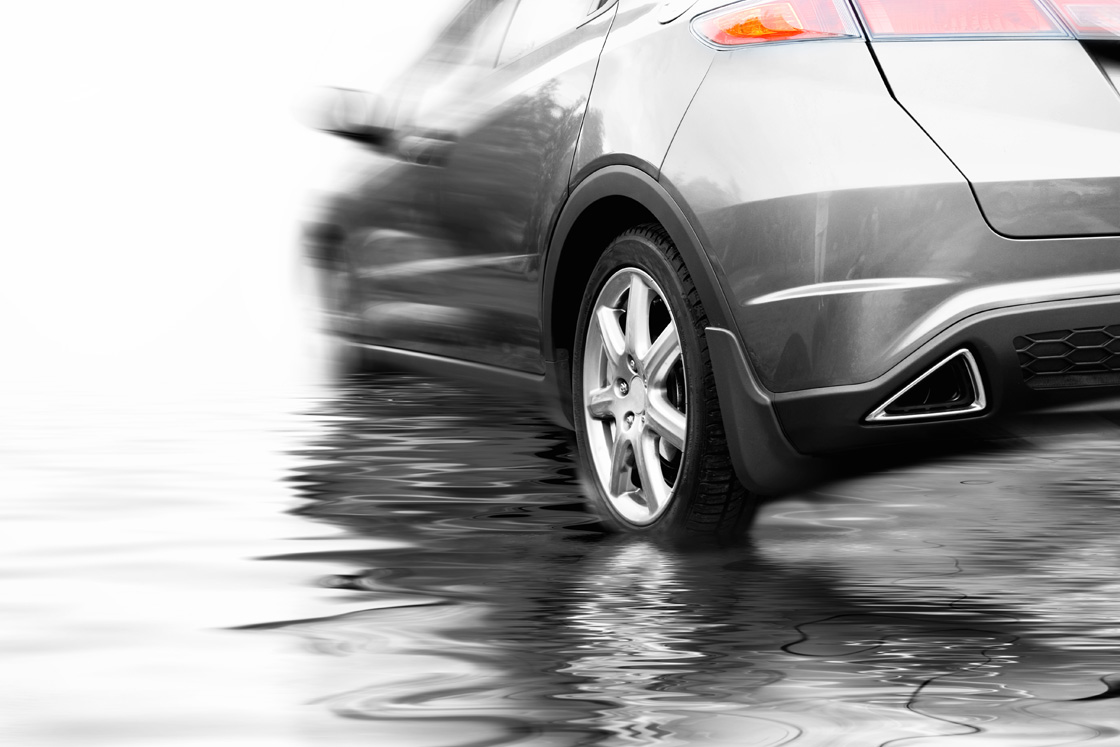
Known worldwide for the fiery motoring competitions that take place here, the Enzo and Dino Ferrari International Racetrack at Imola (Italy) has blazed the way in the sporting, historical, cultural and economic arenas for more than fifty years, not only within its home region, but across the country as a whole. It reached new peaks of excellence in 1981, when the race track hosted the San Marino Formula 1 Grand Prix for the first time.
Over the years, the Paddock, an essential area through which drivers and teams must pass in order to access the track, has undergone a number of resurfacing and maintenance initiatives. The Paddock comprises two main parts: Paddock 1 is located behind the boxes, and accommodates lorries, cars and motorbikes. Paddock 2 is located near the Rivazza Bend and is used as an extension to Paddock 1 on race days, as well as a test area for cars and motorbikes.
The hydro system was constructed in the summer of 2013, allowing certain areas of Paddock 2 to be flooded for the purpose of aquaplaning tests.
The machinery consists of a submerged pump which draws water from an underground collection tank, located next to the service area, and three series of nozzles, which are conveniently positioned underneath the road surface.
The system is completely automated, and is controlled by means of a control panel with two control modes:
- local controls, located on the front of the panel
- remote controls, operated via a remote push-button, which allows the co-driver to activate the valves during testing.
The high reaction speed of the system is the key to the performance of the equipment. Unreliable signalling is eliminated, guaranteeing immediate, real-time readings.
- Outstanding PI optimisation thanks to the oscilloscope function during the test phase.
- The IP66 protection level enables notable financial savings.
- Sleep Mode function. This function drastically reduces pump wear and power consumption, by pausing the unit at defined setpoints, ensuring minimised power consumption. The frequency converter re-starts the pump as soon as the pressure falls below the programmed value.
IP66 ingress protection
The 37 kW output, IP66 protection class VLT® AQUA Drive FC 202 controls the pressure in the pipes via a feedback signal (4-20 mA) issued directly from a pressure transducer. The IP66 protection class enables installation immediately adjacent to the tank, thus reducing the length of the pump feed to a minimum.
Programmed in “Closed Loop” mode and with conveniently calculated PI values, the frequency converter allows the system to operate highly dynamically by reducing reaction times to a minimum. This means that, starting from a closed pump, the 3 bar target pressure can be reached in 2 seconds. After all, speed is at home here!
Performance and key factors
This truly exceptional performance is obtained thanks to a number of VLT® AQUA Drive special features:
- Several different phases of ramping allow the flexible adaptation of the acceleration and deceleration ramps to meet the needs of the application. The Initial Ramp enables the limitation of the time needed for the pump to reach a pump specific minimum speed. This can be essential in submerged pump applications, when it is necessary to exit the low speed state as quickly as possible in order to prevent damage to the pump. The Final Ramp parameter enables the same feature when stopping the pump.
- PI start speed. This parameter ensures the PI controller is activated only once the pump has reached full pressure speed, thus further accelerating the system.
- Time filter on feedback signal. The rapid fluctuations of water inside the tubes generate turbulence, which is recorded by the pressure transducer. In this case, the filtered feedback signal can be used.