The Danfoss electrical actuators for combination with our control vales provide a new level of convenience through excellent control performance and quality features. The actuators provide risk reduction trough improved overload protection, which ensures trouble-free operation of the actuator inside the system.
The motorized control valves ensure stable and accurate control of water. This in turn improves temperature control, leading to enhanced comfort for the end-user. Good control ratios and rapid response times to changes in domestic hot water supply requirements are just some of the features needed to ensure optimum control performance.
Actuator features:
- Anti-oscillation
- Control ratio
- Stroke limitation
- Split characteristics
- Modification of controls characteristic (65X actuators)
Features and benefits
Easy selection, installation, commissioning and maintenance mean less time, money and effort
Built-in thermic and overload protection of the electromotor
External LED visualization and signaling save time and effort during installation and commissioning of MCVs
Tools and apps
Application guide
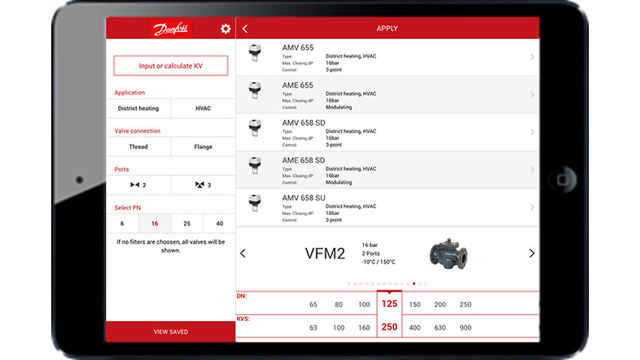
FAQ
Case studies
-
if (isSmallPicture) {
; } else if (isBigColumns) { } else { }Successful transition from oil boilers to a local heating network in EurasburgIn the Wittelsbacher Land near Augsburg the local network in Eurasburg supplies heat to 80 buildings using a wood chip heating system. Danfoss’ substations ensure efficient heating in all building types, and its modern SCADA solution enables remote system monitoring and management.Â
-
if (isSmallPicture) {
; } else if (isBigColumns) { } else { }DrivePro® Lifecycle Services secure maximum uptime for Rothes CoRDeSCOTLAND: The Rothes CoRDe plant, a biomass-fired combined heat and power (CHP) plant, ensured maximum uptime thanks to several DrivePro® Lifecycle Services.
-
if (isSmallPicture) {
; } else if (isBigColumns) { } else { }Intelligent optimisation of district energy in new residential apartmentsTwo new build apartments in Docklands, London and Newbury Racecourse, Berkshire have been equipped with intelligent Danfoss solutions, bringing increased control and stability as well as greater than 20% peak energy reduction.
-
if (isSmallPicture) {
; } else if (isBigColumns) { } else { }Leanheat makes buildings smartIn Europe, 30 percent of all energy consumption goes to heat or cool buildings. Danfoss has the solution to lower energy usage and improve indoor climate by adding a digital element: Leanheat software.
-
if (isSmallPicture) {
; } else if (isBigColumns) { } else { }MS Cinderella saves more than 1000 tpa marine diesel with new ventilation controlAboard the Viking Lines cruise ship M/S Cinderella, Danfoss AC variable speed drives are delivering fuel savings so large that the cost of installing the drives will be fully recovered in less than eighteen months.
-
if (isSmallPicture) {
; } else if (isBigColumns) { } else { }Solar heating plant reduces CO2 emissions by 15,700 tonnes annuallyThe world’s largest solar heating plant in Silkeborg, Denmark harnesses energy to heat the homes and workplaces of 40,000 citizens. It supplies 18-20% of the annual heat consumption in the city of Silkeborg, Denmark, which has an ambitious target of CO2 neutrality in heat production by the year 2030.