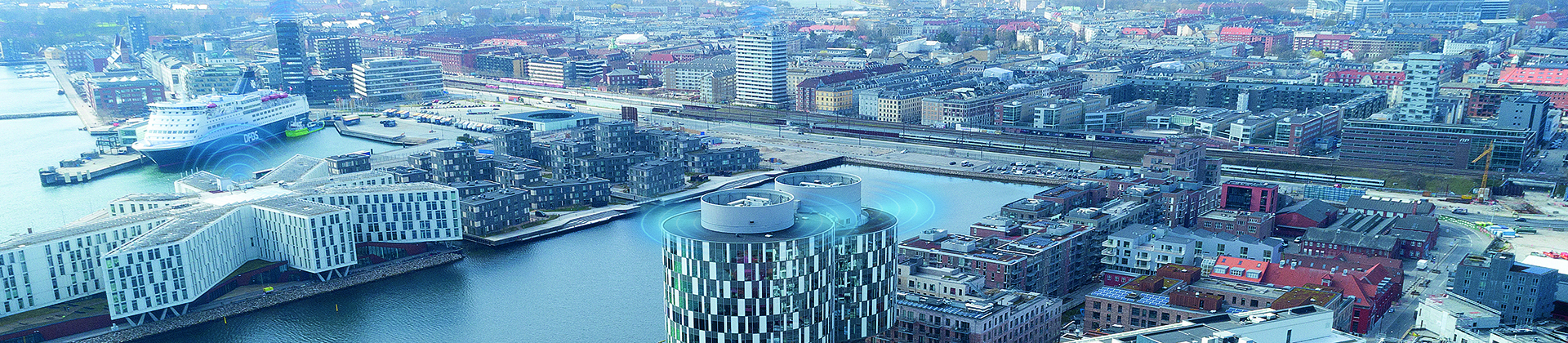
Napędy są czymś więcej niż tylko procesorami mocy
Dzięki możliwości łączenia się z innymi urządzeniami i pełnienia funkcji czujników oraz koncentratorów czujników w celu przetwarzania i analizowania danych napędy są istotnymi elementami nowoczesnych systemów automatyzacji i systemów zarządzania budynkiem. Zintegrowana funkcja monitorowania stanu układu napędowego umożliwia nowe metody wykonywania konserwacji, takie jak konserwacja zależna od stanu układu.
Ewolucja przemysłowych systemów automatyki
Na początku tego tysiąclecia byliśmy świadkami głębokiej zmiany w technologii, która zapoczątkowała zupełnie nowy sposób pracy w świecie cyfrowym.
Czwarta rewolucja przemysłowa nastała w wyniku połączenia komputerów, ludzi i urządzeń z siecią w celu umożliwienia wymiany danych i uczenia maszynowego. Chociaż termin „Przemysł 4.0” jest dość niejasny, jedna z definicji
Trendy w systemach automatyki Przemysłu 4.0
Wpływ Przemysłu 4.0 na systemy napędowe i systemy zarządzania budynkiem to migracja z „piramidy automatyzacji” do „systemów sieciowych”. Oznacza to, że różne elementy
Sieć automatyki obejmuje ogromną ilość danych. Ponieważ dane pochodzą głównie z czujników, liczba czujników w nowoczesnych systemach automatyki nieustannie rośnie.
Nowoczesne napędy o zmiennej prędkości otwierają nowe możliwości w sieciach automatyki Przemysłu 4.0 i systemach zarządzania budynkiem. Tradycyjnie napędy były uważane za procesory mocy przeznaczone do sterowania prędkością silnika, wentylatora, przenośnika i/lub pompy. Obecnie
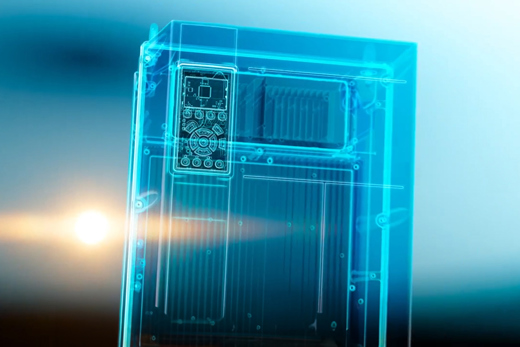
Co to jest inteligentny napęd?
W sieci Przemysł 4.0 napęd odgrywa ważną rolę i pozwala na stosowanie następujących funkcji:
Bezpieczna łączność: Napęd może się łączyć z innymi elementami w bezpieczny sposób. Inne elementy w sieci mogą obejmować napędy, sterowniki PLC, czujniki i chmurę. Napęd pełni funkcję czujnika: Napęd wykorzystuje prąd silnika i analizę sygnatury napięcia w celu wykrycia silnika i wydajności aplikacji. Napęd pełni funkcję koncentratora czujników: Napęd pobiera dane z czujników zewnętrznych powiązanych z procesem, który jest przez niego kontrolowany. Napęd pełni funkcję sterownika: Napęd może zastąpić sterownik PLC, jeśli pozwalają na to ograniczenia aplikacji. Koncepcja „przynieś własne urządzenie”: Bezpośrednia łączność z urządzeniami przenośnymi (smartfon, tablet).
Informacje z napędu można zidentyfikować w następujący sposób:
Sygnały natychmiastowe: Sygnały, które są mierzone bezpośrednio przez napęd za pomocą wbudowanych czujników. Dane takie jak prąd silnika, napięcie, temperatura napędu i ich pochodne, takie jak moc uzyskana poprzez pomnożenie prądu przez napięcie lub moment obrotowy silnika. Co więcej napęd ten może pełnić rolę koncentratora, do którego można podłączyć czujniki zewnętrzne dostarczające sygnały chwilowe. Przetworzone sygnały: Sygnały, które są wyliczane na podstawie sygnałów chwilowych. Na przykład rozkład statystyczny (wartość maksymalna, minimalna, średnia i odchylenie standardowe), analiza domeny częstotliwościowej lub wskaźniki profilu misji. Sygnały analityczne: Sygnały, które dostarczają wskaźniki dotyczące stanu napędu, silnika i aplikacji. Sygnały te służą do inicjowania konserwacji lub prowadzą do usprawnień projektowych systemu.
Techniki analizy sygnatury prądu silnika pozwalają napędowi monitorować stan silnika i aplikacji. Technika ta pozwala na potencjalne wyeliminowanie czujników fizycznych lub pozyskanie wczesnych sygnatur usterki, których wykrycie mogło być niemożliwe. Dzięki zastosowaniu tej techniki możliwe jest na przykład wcześniejsze wykrycie kawitacji, usterek uzwojenia lub mimośrodowości obciążenia mechanicznego.
Napęd
Konserwacja zależna od stanu układu napędowego i inne strategie konserwacji
Poniżej przedstawiono różne rodzaje strategii konserwacji:
Konserwacja korekcyjna: produkt jest wymieniany po usterce. Konserwacja zapobiegawcza: produkt jest wymieniany przed wystąpieniem usterki, ale żadne powiadomienia nie są odbierane z produktu. Konserwacja zależna od stanu układu napędowego: produkt przesyła ostrzeżenie, gdy aktualny czas użytkowania produktu różni się od oczekiwanego czasu użytkowania i zidentyfikowano możliwe przyczyny źródłowe. Konserwacja predykcyjna: produkt przesyła ostrzeżenie zanim osiągnie zaplanowaną liczbę godzin pracy, aby zainicjować serwisowanie.
Dlaczego potrzebna jest konserwacja zależna od stanu układu napędowego?
Konserwacja korygująca i zapobiegawcza są oparte na usterce (zdarzeniu) lub czasie. Z tego względu konserwacja jest wykonywana w razie usterki (korygująca) lub po upływie ustalonej liczby godzin pracy (zapobiegawcza). Te rodzaje konserwacji nie korzystają z żadnej informacji zwrotnej z rzeczywistej aplikacji.
Dzięki wprowadzeniu Przemysłu 4.0 i dostępności danych z czujników możliwa jest konserwacja zależna od stanu układu napędowego i
Przegląd i korzyści konserwacji zależnej od stanu układu napędowego
Konserwacja zależna od stanu układu napędowego to najłatwiejsza i najbardziej intuicyjna technika konserwacji w oparciu o dane z rzeczywistej aplikacji. Pozyskane dane są używane do monitorowania stanu sprzętu będącego w eksploatacji. Do tego celu wybierane są kluczowe parametry, które pełnią rolę wskaźników pozwalających identyfikować powstające usterki. Stan sprzętu na ogół degraduje się wraz z upływem czasu. Jest to zilustrowane na wykresie P-f, który pokazuje typowy wzorzec degradacji. Awaria funkcjonalna ma miejsce, gdy sprzęt nie jest w stanie wykonać funkcji, do której jest przeznaczony. Ideą konserwacji zależnej od stanu układu napędowego jest wykrywanie potencjalnej usterki zanim ona nastąpi.
Korzyści planowania działań konserwacyjnych
- Ograniczenie czasu przestojów
- Eliminacje nieoczekiwanych przestojów produkcji
- Optymalizacja konserwacji
- Zmniejszenie zapasów części zamiennych
Funkcje monitorowania stanu dla napędów o zmiennej prędkości
Integralną częścią konserwacji zależnej od stanu układu napędowego jest monitoring stanu sprzętu. W aplikacjach o zmiennej prędkości stan aplikacji często zależy od prędkości. Na przykład poziomy wibracji są wyższe przy większych prędkościach, jednak ta zależność nie jest liniowa. Co więcej, przy pewnych prędkościach mogą wystąpić drgania rezonansowe, które zanikają po zwiększeniu prędkości.
Użycie niezależnego systemu do monitorowana stanu aplikacji o zmiennej prędkości jest skomplikowane, ponieważ wymaga znajomości prędkości i zestawienia wartości monitorowanej z prędkością.
Monitorowanie stanu wykorzystuje procedurę składającą się z trzech kroków:
Dowiedz się więcej, zapoznając się z raportem i filmem o monitorowaniu stanu układu napędowego
Obecnie napędy są więcej niż tylko prostym procesorem mocy. Dzięki możliwości pracy w roli czujników i koncentratorów czujników w celu przetwarzania, magazynowania i analizowania danych oraz możliwości komunikacji napędy są kluczowym elementem nowoczesnych systemów automatyki.
Napędy często są już obecne w instalacjach automatyki i z tego powodu stanowią doskonałą możliwość modernizacji do Przemysłu 4.0.
Pozwala to na nowe sposoby realizowania konserwacji, takie jak konserwacja zależna od stanu układu napędowego. Funkcje te
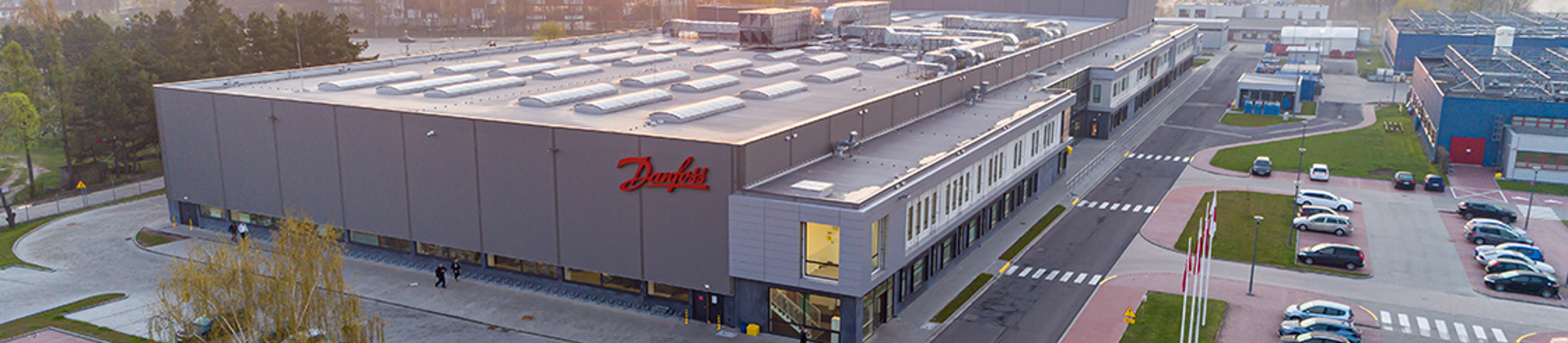
Condition Based Monitoring i Remote Monitoring w zielonej fabryce
Proekologiczne obiekty przemysłowe bazują na zaawansowanych rozwiązaniach, zapewniających maksymalną efektywność energetyczną oraz skuteczne gospodarowanie zasobami. Istotną częścią nowoczesnej infrastruktury są narzędzia umożliwiające zdalne monitorowanie poszczególnych elementów instalacji oraz całych układów. Ich znaczenie widać doskonale na przykładzie zielonej fabryki Danfoss w Grodzisku Mazowieckim.
Wyróżnione produkty
Produkty Danfoss wykorzystujące monitorowanie stanu układu napędowego
-
if (isSmallPicture) {
; } else if (isBigColumns) { } else { }VLT® Refrigeration Drive FC 103Przetwornica FC 103 jest przeznaczona do sterowania sprężarkami, pompami oraz wentylatorami w celu uzyskania dużych oszczędności energii w aplikacjach chłodniczych.
-
if (isSmallPicture) {
; } else if (isBigColumns) { } else { }VLT® AQUA Drive FC 202Przetwornica VLT® AQUA Drive FC 202 steruje wszystkimi typami pomp i jest wyposażona w sterownik kaskadowy.
-
if (isSmallPicture) {
; } else if (isBigColumns) { } else { }VLT® AutomationDrive FC 301 / FC 302Przetwornica częstotliwości VLT® AutomationDrive FC 301/FC 302 przeznaczona jest do regulacji prędkości wszystkich silników asynchronicznych oraz silników z magnesami trwałymi. Występuje w wersji standardowej (FC 301) oraz zaawansowanej wersji (FC 302) z dodatkowymi funkcjami.
-
if (isSmallPicture) {
; } else if (isBigColumns) { } else { }VLT® HVAC Drive FC 102Ta wytrzymała i niezawodna przetwornica FC102 usprawnia pracę pomp i wentylatorów w systemach zarządzania budynkiem (BMS) i może być instalowana poza szafą w większości warunków klimatycznych.
-
if (isSmallPicture) {
; } else if (isBigColumns) { } else { }VACON® NXP Common DC BusUmożliwia integratorom systemów, konstruktorom maszyn oraz producentom OEM tworzyć wydajne przemysłowe systemy przetwornic. Konfiguracja Active Front-end (NXA), Non-regenerative Front-end (NXN), Brake Chopper (NXB) oraz Inverter (NXI) jest już dostępna.
-
if (isSmallPicture) {
; } else if (isBigColumns) { } else { }VACON® NXP DC/DC ConverterMaksymalizuje wydajność energetyczną w rozwiązaniach hybrydowych i ułatwia poprawę wydajności dzięki zbliżeniu poziomu dostawy energii do poziomu zużycia.
-
if (isSmallPicture) {
; } else if (isBigColumns) { } else { }VACON® NXP Liquid Cooled Common DC BusUmożliwia czerpanie korzyści z chłodzenia cieczą w systemach ze wspólną magistralą DC w wymagających sytuacjach. Konfiguracja Active Front-end (NXA), Non-regenerative Front-end (NXN), Brake Chopper (NXB) oraz Inverter (NXI) jest już dostępna.
-
if (isSmallPicture) {
; } else if (isBigColumns) { } else { }VACON® NXP Liquid CooledDoskonale nadający się do zastosowań, w których kluczowe znaczenie ma jakość powietrza, gdzie przestrzeń jest ograniczona i konieczny jest skuteczny i sprawny transfer ciepła. Konfiguracja Active Front-end (NXA), Non-regenerative Front-end (NXN), Brake Chopper (NXB) oraz Inverter (NXI) jest już dostępna.
-
if (isSmallPicture) {
; } else if (isBigColumns) { } else { }VACON® NXP Grid ConverterPrzetwornice chłodzone powietrzem i cieczą specjalnie zaprojektowane z myślą o magazynowaniu energii oraz zarządzania energią w aplikacjach morskich.
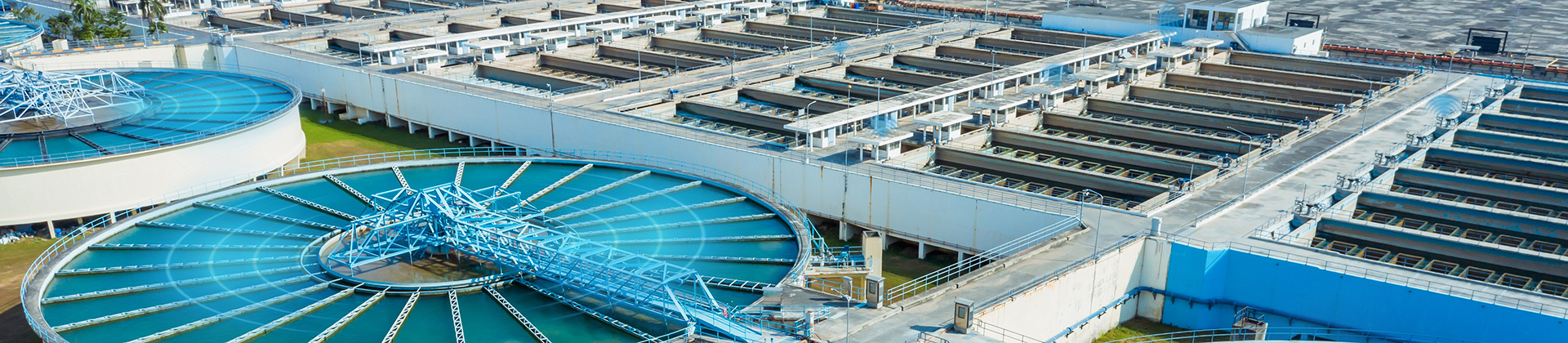
Pierwsze innowacje Danfoss
Monitorowanie stanu układu napędowego powstało w wyniku wieloletniego doświadczenia Danfoss w zakresie innowacji. Napędy Danfoss wyróżniają się na rynku dzięki inteligentnym wbudowanym funkcjom, które pozwalają ograniczyć liczbę wymaganych podzespołów zewnętrznych.
Studium przypadku
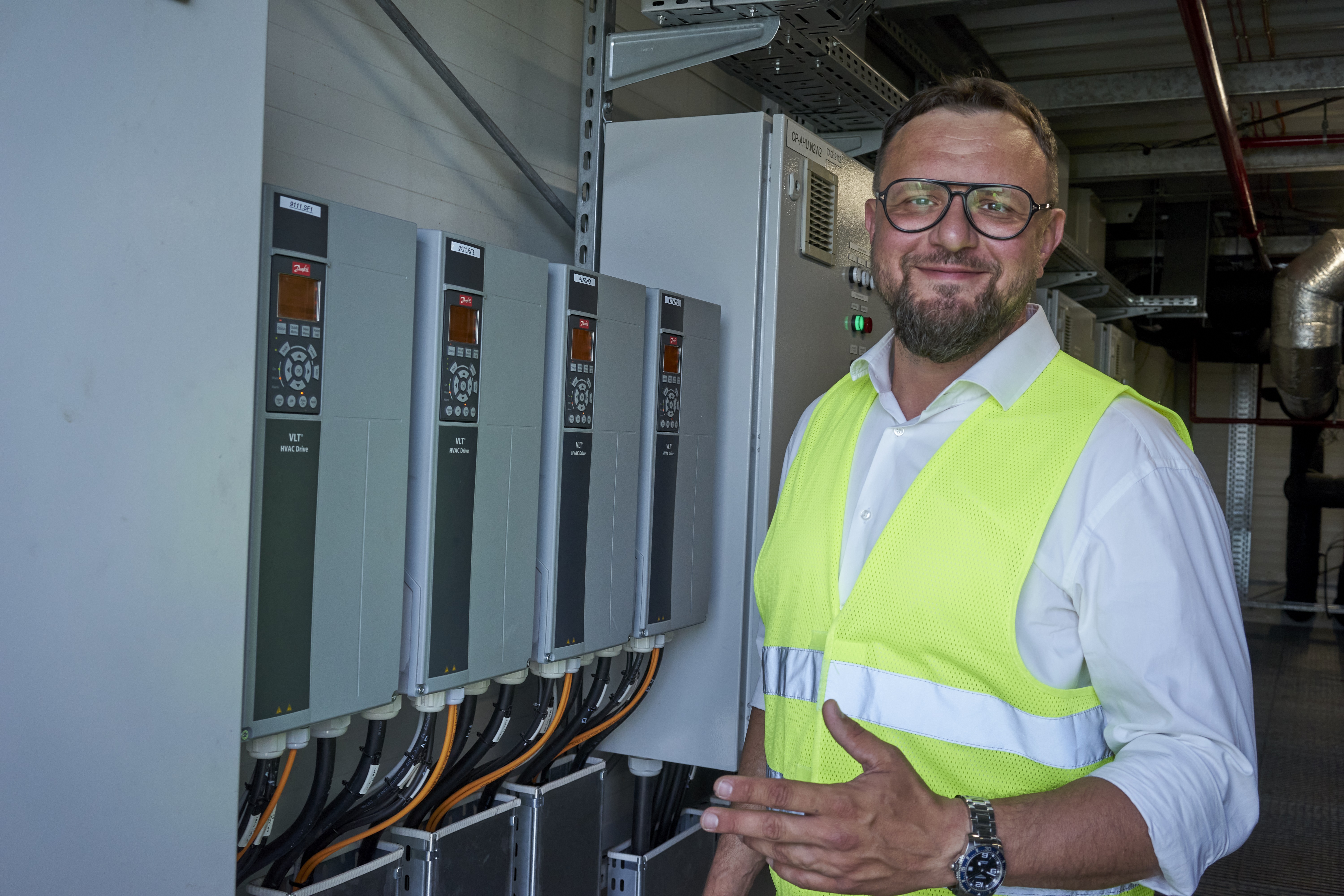
Czas na zmianę w podejściu do konserwacji instalacji w zakładzie. Skontaktuj się z Krzysztofem Kubickim - naszym ekspertem w zakresie konserwacji predykcyjnej, oszczędź pieniądze i uniknij nieplanowanych przestojów.